Indra Srl is involved in many large-scale LNG projects such as Arctic LNG.
This year, Indra Srl celebrates its 35-year anniversary. Established in 1987, the Italian manufacturer is at the forefront in the designing and manufacturing of ball and needle valves. The company designs and manufactures this equipment for various sectors, including LNG and hydrogen applications. Indra’s focus has been motivated due expected to a higher demand in these areas.
By Lucien Joppen
Indra states that its main characteristics are Made in Italy and a tailor made approach, qualities that represent the trademark. “The mission is to satisfy our customers’ needs by developing customized solutions. Safety, efficiency and reliability are pillars of the corporate culture, which is directed at the future by making choices of innovation and continuous improvement.” Quality starts at the source, with the selection and procurement of raw materials. “The raw material is carefully selected, as it is a fundamental and decisive requirement for the final choice by customers. The excellent quality is deemed a ‘must’ and the selection becomes then an essential starting point because a good product performance depends on that. To guarantee the high-quality standards of our products, the contributing elements are: the use of raw material of mainly Italian origin (also European, USA, South Korean and Japanese), the product monitoring from engineering to production, and the wide range of tests carried out. All the production steps are carried out in-house: RFQ/PO; engineering; purchasing manufacturing; testing; and shipping. Each process is performed according to existing procedures and monitored in-house, which ensures that product parts and the final product are tracked product during all its development phases”, the company states.
Modern machinery
It will come to no surprise that Indra prides itself on its ability to machine the raw materials into valve parts for the most stringent operating conditions. All the products are machined from the most standard materials, but also from ‘exotic’ materials used for critical applications (Inconel 625, Incoloy 825, Duplex and Super Duplex, Hastelloy-C, Monel etc.). Today, the company has modern machinery for very precise mechanical processing, with testing phases of the single items during the production process.
“We have invested and will continue to invest in state-of-art machining equipment. We strive to increase to produce a 100 per cent in-house. In 2020, for example, we acquired a brand-new machine: the DGM MORI machining center, a 5-axis milling machine that can work on several faces at the same time, thus optimizing production times and costs, and reducing waste material.”
Continuous improvement
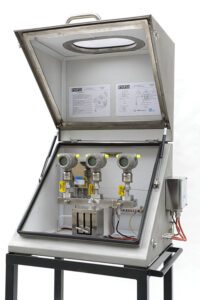
Testament to Indra’s quality promise are its ISO certifications (9001, 14001 and 45001 certified). The company states that it works according to growth targets and continuously improving its processes, which enables the company to meet specific technical requirements and high performances. “The certifications play a fundamental role to guarantee the quality of our products. Indispensable are those of the product achieved according to the regulations in force in the EEC countries and / or outside the EEC area.”
Apart from designing, manufacturing and delivering high-performance ball and needle valves, Indra stresses the importance of doing business in a correct manner.
“We have always paid great attention to the ethical aspects of our company and consider legality and correctness as essential condi-tions for conducting business. Therefore, we have established an Ethical Code which forms an integral part of our organization and management structure. For Indra, it is not only about the right products and services, but also about doing things the right way.”
About Indra Srl
Headquarters: Magenta, Italy
Founded: 1987
Production: 3,000 sqm (total sur-face area 4,000 sqm
Employees: 63 people
Key proudcts:
• Ball and needle valves in various configurations and diameters
• Integral and split body double block & bleed (DBB) valves
• Manifolds for instrumentation
• Interlocking manifolds for HIPPS systems
Website: indra.it/en
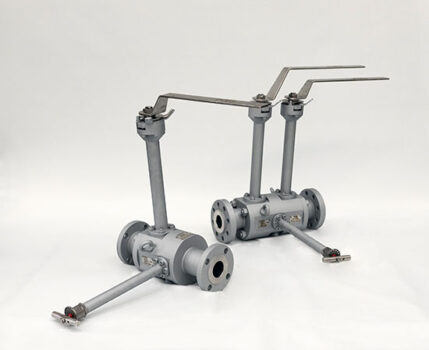
Geographical reach
As is the case for many of its Italian competitors, Indra relies a great deal on the export market. Roughly 60 per cent of its turnover is generated through export.
Indra has always considered its foreign presence important, for this reason the company has built its commercial network over the years in some strategic areas through carefully selected distributors and agents. “We have agents all over the world and this local presence allows us to directly manage some key activities for the development of the reference market and business. In addition, the following areas are very important to us: Saudi Arabia, Kazakhstan, Africa, Mexico, USA. Geographical expansion is planned with the development of new facilities in the Saudi Arabia area 4.”
Indra is also a regular exhibitor at the most important events in the oil & gas sector. “It is another aspect that underlines our will to affirm our role as a protagonist in both the domestic and foreign markets. As for our focus, we participate in sector-specific events and events that focus on valves, such as the Valve World events.”
Extensive track record
As mentioned before, Indra is specialized in product solutions for highly-demanding applications in various sectors, most notably in (offshore) oil & gas, LNG, hydrogen, offshore, chemical, petrochemical, energy. “We have increased our focus on LNG and hydrogen as these applications are very promising. The energy sector and the public sector are clearly investing in these energy sources as they provide a low(er) carbon foot-print and are less polluting than oil and coal.” As for LNG, Indra already has an extensive track record. For example, the company has supplied cryogenic valves (for liquefaction and gasification) for large scale LNG projects. The most relevant and representative supplied up to now are: Yamal LNG Project (2012), the Arctic LNG Project (2019), Stef (Sener EPC) and the LNG Coastal Depot in Ravenna, Italy (EPC Edison). “The quality and reliability of the products manufactured have kept active the request for support from Indra for the construction of new cryogenic valves designed for applications in these specific sectors.”
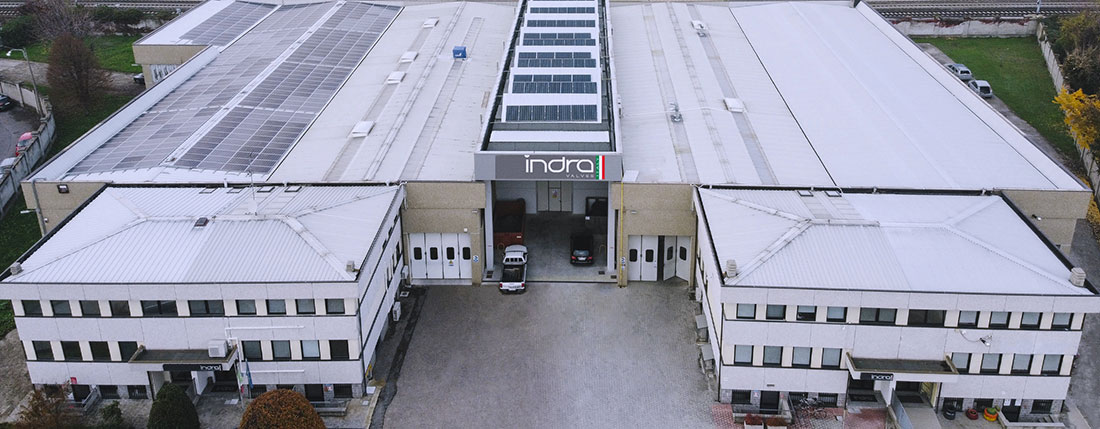
Hydrogen: high potential
Apart from LNG, hydrogen is an application of interest for Indra. The company has focused on this gas for a reason. With more and more countries aiming to reduce their CO2 emissions, decarbonized solutions are needed to provide affordable and available energy. Hydrogen has emerged as a game changer because of its multifaceted and versatile nature. It is already used as an industrial feedstock, but it can also be used in mobility (heavy-duty transport modes) or as an energy carrier to facilitate the decarbonization energy-intensive industrial sectors, such as steel or cement.
There is a lot of terrain to be won in hydrogen. Today, less than 2 per cent of Europe’s energy consumption comes from hydrogen (Source: EU), and this is mainly used for manufacturing chemical products like plastics and fertilizers. Moreover, almost all this hydrogen – 96 per cent – is produced from natural gas (grey hydrogen). The goal is now to decarbonize this production process, either by offsetting emissions through CCS (blue) or the use of renewable energy (green hydrogen).
“We have already supplied valves for hydrogen applications for some of our key customers. Depending on the application, hydrogen requires high levels of safety and reliability due to its flammability and volatility. Indra has proven that it is able to provide the necessary flow control equipment for these applications.”
Arctic LNG
As mentioned before, Indra has contributed to several major projects in the oil and gas and power sector. Below are listed more projects that are being developed around the globe, hence clearly signaling that Indra has the capacity and presence to serve both within and outside the EU-market.
The Yamal LNG and Arctic LNG projects are truly large scale. The Yamal and Gydan Peninsulas, containing enormous gas reserves, is already solidifying Russia’s position in the global oil and gas market. With the advance of the Arctic LNG-2 project, production is expected to increase in the coming years to serve Asian and European demand. With a production capacity of approximately 19.8 million tons per year (MT/year), or 535,000 barrels of oil equivalent per day (boe/d), Arctic LNG 2 will unlock more than 7 billion boe of hydrocarbons in the onshore Utrenneye gas and condensate field.
The project will involve the installation of three gravity-based structures in the Gulf of Ob on which will be installed the three liquefaction trains of 6.6 MT/year capacity each. The project is estimated to cost 20 to 21 billion US Dollar.
Other projects involved:
• Yamal LNG Project
• NASR Full Field Development Package II – Phase I and Phase II
• IGD E2 LG8
• Ruwais Refinery complex (Takreer)
• Al-Zour Refinery Project
• Coral South Development Project
• BAB Integrated Facilities Project
• FPSO Almirante Barroso Modec
Single valve body
Designing and manufacturing highly-de-manding product solutions requires an innovative approach, as mentioned earlier in this article. “We need to innovate to distinguish ourselves from the competition. Again, it is a matter of engineering expertise, manufacturing excellence, and quality control. However, it is first and foremost listening to our customers’ needs and requests to develop the best tailor-made/customized solution possible. To fully understand their needs, we also need to understand their processes and how our equipment can add value.”
Apart from bespoke product solutions, Indra has launched several innovative product lines, such as the Iblok Line. “We developed this product with a keen eye for environmental and human safety. It is the safety feature that was at the base of the development of the Iblock valve line. In the DBB version, we have incorporated multiple functions in a single valve body, thus replacing the traditional ‘Christmas Tree’-installation. All valves can be equipped with accessories such as blocking systems, electrical signals, actuators etc., improving their safety and efficiency requirements. With the Iblock, we have reduced complexity and installation and maintenance costs.”
SIL4 modular manifold
SIL4 modular manifold In recent years, Indra developed and intro-duced the SIL4 modular manifold, designed specifically for instrumental control applications. According to Indra, this product guarantees a high standard of safety, efficiency and quality in HIPPS systems. “The SIL4 modular manifold permanently guarantees the continuity of information between the process and the pressure sensors. Hereby we have eliminated human errors completely. Also, we have ensured that, in case of replacements or checks (for electrical or mechanical damage etc.), one or more sen-sors will always remain active through the various available configurations identified as 1oo1,1oo2, 2oo3,1oo4 mainly.”
The SIL4 modular manifold is equipped with extra safety features, such as the compulsory sequence of operations (never superimposable) and protection of the line from overpressure. “As for environment protection, the manifold reduces release of polluting emissions into the atmosphere due to high pressure lines.”
The standard construction of the SIL4 modular manifold does not accommodate the use of protective containers. However, in outdoor installations, it is recommended to use them to protect both the manifold and the instruments. For this purpose, Indra has designed and manufactured a stainless steel and polyester container as a safeguard.
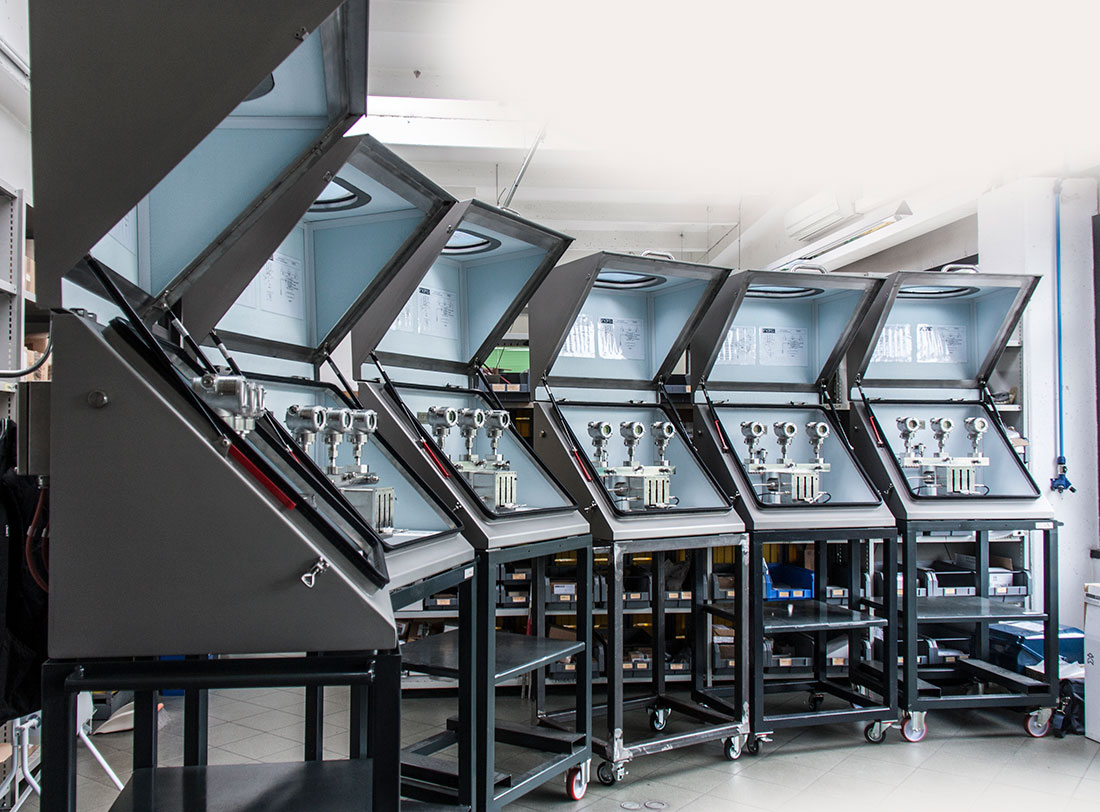
SIL4 modular manifold
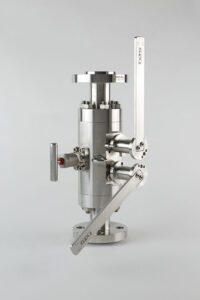
In recent years, Indra developed and introduced the SIL4 modular manifold, designed specifically for instrumental control applications. According to Indra, this product guarantees a high standard of safety, efficiency and quality in HIPPS systems. “The SIL4 modular manifold permanently guarantees the continuity of information between the process and the pressure sensors. Hereby we have eliminated human errors completely. Also, we have ensured that, in case of replacements or checks (for electrical or mechanical damage etc.), one or more sensors will always remain active through the various available configurations identified as 1oo1,1oo2, 2oo3,1oo4 mainly.”
The SIL4 modular manifold is equipped with extra safety features, such as the compulsory sequence of operations (never superimposable) and protection of the line from overpressure. “As for environment protection, the manifold reduces release of polluting emissions into the atmosphere due to high pressure lines.”
The standard construction of the SIL4 modular manifold does not accommodate the use of protective containers. However, in outdoor installations, it is recommended to use them to protect both the manifold and the instruments. For this purpose, Indra has designed and manufactured a stainless steel and polyester container as a safeguard.
DBB Twin pattern valve
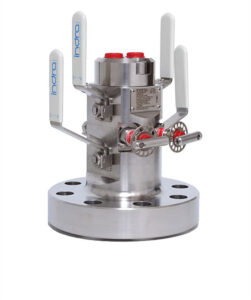
Another Indra-product is the DBB API 10000 twin pattern valve, made both in the ball and needle version. The valve is manufactured from a monobloc using the material suitable for the applications. A common alloy is AISI 316L, Indra states, but the company can also produce the DBB in more exotic materials.
“The extremely compact dimensions facilitate assembly in combination with the process variable control instrumentation (pressure transmitters, pressure switches, pressure gauges, etc.) in small spaces. The DBB twin valve has a single process connection and two separate outlet connections, each of which is made in the DBB configuration. The separation of the outgoing lines allows to control the process through one tool, while maintenance is being performed. This facilitates maintenance activities without compro-mising on safety and process continuity.”
The DBB twin valve can also be made with separate inlets, Indra states, to have two pressure lines completely independent of each other. With the twin valve, Indra claims it has developed a product that is “compact, realizes cost reductions and increases safety due to continuous monitoring of process pressure.”
DNA intact
To conclude, Indra has positioned itself for the near future, developing and manufacturing product solutions that are geared towards lower-carbon feedstocks/energy carriers such as LNG (natural gas) and hydrogen. Furthermore, it continues to serve the oil and gas sector supply chain as the global demand for fossil feedstocks is expected to rise, depending on the geography.
In terms of innovation, Indra sees further room for new product development in digitalization both for its products and product design and manufacturing processes. As for future growth, Indra eyes the export market. “The geographic expansion of our business includes the development of new production/distribution facilities in the area of Saudi Arabia in particular. Other areas of interest for business development are Kazakhstan, Africa, Mexico, USA.” Regardless of what might change in the (near) future, Indra pledges to keep its 35-year old DNA intact. “It is in our genes to satisfy customer’s needs by developing customized solutions ‘made in Italy’. Safety, efficiency and reliability are pillars of the corporate culture. We are confidently looking to the future!”
About this Featured Story
This Featured Story is an article from our Valve World Magazine March 2022 issue. To read other featured stories and many more articles, subscribe to our print magazine.
“Every week we share a new Featured Story with our Valve World community. Join us and let’s share your Featured Story on Valve World online and in print.”