Example of a Design Validation Test on a Triple Offset Butterfly valve.
Current valve standards cover design and material selection. However, only a few standards cover valve performance at the design conditions level. The new Type Testing Standard ISO 23632 enables any customer to order valves that have been prototyped and tested, improving long-term performance.
By Luc Vernhes and Colin Zegers
About the authors:
Luc Vernhes has been active in Product and Technology for Velan for the past 18 years. He is currently concentrating on business development for Severe-Service applications. Colin Zegers is Managing Director of ITIS, an independent company specialized in leak testing, valve testing, NDE and industrial inspections.
If not, some valves that comply with all existing standards, could fail prematurely when utilized within their pressure/temperature/cycles range. For example, without a DVT, the seat performance of a newly designed NPS 2 valve is only tested for 15 seconds during the final hydrotest, which is not enough to ensure the long-term performance of the valve.
Valve performance is typically measured during testing, either in production or in a laboratory setting.
ISO, API & EN are the three dominant standard organizations for industrial valves and provide procedures to assess performance during hydrotest, fire test and fugitive emission test. However, missing from these existing standards was the ability to gauge the durability of a valve, from shut-down to shut-down, or the total number of mechanical cycles the valves can perform for batch processes.
This is the reason why we have developed ISO 23632, a new standard to assess seat performances and torque requirements through mechanical and thermal cycles.
If not, some valves that comply with all existing standards, could fail prematurely when utilized within their pressure/temperature/cycles range. For example, without a DVT, the seat performance of a newly designed NPS 2 valve is only tested for 15 seconds during the final hydrotest, which is not enough to ensure the long-term performance of the valve.
Long-term performance
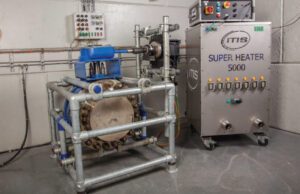
When buying a car, one has an expectation regarding the lifecycle of the car and maintenance period. This is often unknown for valves. How long does a valve last?
Has the valve ever been tested for durability? Has it ever been tested for design conditions?
Can it withstand operating conditions?Assessing the long-term performance of valves
is therefore critical to ensure we are delivering a robust product that will last. Therefore, major customers already require type tests to assess the following criteria.
For many years ITIS has tested valves according to DVT SPE 77/300 requirements (previously called Type Approval Testing or TAT) – ref. Figure 1. Even though these requirements were developed by Shell, they are also often requested by other end-users, highlighting the need for a new ISO standard.
Design flaws
Roughly 60 per cent of the valves do not comply with DVT requirements. Some valves fail under con-ditions (pressure, temperature, operational cycles) they will be exposed to in the field and therefore are not fit for their purpose. This is, of course, a major cause for concern.
As an example, during a DVT test it was observed that the required torque to open a 16” class 1500 valve at field conditions (60% rated pressure) was excessive. The test had to be stopped, and the valve was disassembled for investigation. It was observed that that stem failed due to design flaws (see Figure 2).
Obviously, this design does not meet DVT requirements and cannot go in the field. Such designs can lead to system failures and/or serious accidents!Other failure modes are also common such as 14-turn stems that plasticly deform (see Figure 3) – and soft materials that melt when exposed to maximum allowable temperature (see Figure 4).
One of the reasons for these design flaws may be because end-users, with good intention, tend to specify the most stringent standard requirements for Fugitive Emission or Seat leakage – i.e., Class.
A Fugitive Emission and Zero-seat leakage. Unintentionally, the method selected by the OEMs to achieve this stringent requirement could have a detrimental effect on the durability of the valves (i.e., narrower sealing surface, higher packing compression, etc.).
Design Validation Testing
The DVT in accordance with ISO is part of the solution. The new Type Testing Standard ISO 23632 enables any customer to order valves that have been prototyped and tested, improving safety and overall long-term performance. ISO 23632 specifies requirements and acceptance criteria for metallic butterfly and ball valves used for isolating services for all industrial applications and serves to validate the product design over 205 cycles at design conditions.
The test sequence is similar to ISO 15848-1 – ref. (see Figure 5). This helps leverage existing cycling stations that have been developed around the world for Fugitive Emission testing and that can provide both mechanical and thermal cycles.
The new standard assesses the following points:
• Torque measurement against DP shall not exceed published value.
• Seat leakage to meet targeted rate – ISO 5208 with air.
• Maximum allowable stem torque validations.
The purpose of this type test is to validate the seat performance within the manufacturer’s given pressure/temperature rating. This information is found in the manufacturer’s technical documentation of the product. This type test verifies torque requirements and maximum allowable stem torque (MAST), as given in the manufacturer’s technical documentation. This type test validates the durability of seat performance and operating torque through mechanical and thermal cycles. Importantly, ISO 23632 also provides rules to extend qualification to untested size and pressure designation of valves of the same product range.

Demand for additional information
After a DVT test, a valve is disassembled for inspection and investigation of all parts. For example, damages, wear, or tear, on the stem, during strip downs. As the DVT is limited to 205 operational cycles, there are limitations to the TAT, especially as the operational use
(intensity and frequency) is important in determining the life cycle of the valve in question. Whether it is acceptable, is up to the end user. The demand for DVT’s is constantly growing. More and more end users are demanding additional information regarding quality, reliability, and durability for the shut-off valves they procure.
There are discussions within the supply chain about DVT. Some suppliers are questioning these requirements. On the other hand, there are shut-off valves that leak at 50 per cent of the rated pressure. As mentioned earlier, more than half of the valves we type test are not delivering what they should. If we can bring this down, partially, by using ISO 23632 DVT, it would save some serious problems at the operational level!
Acknowledgment.
The project has been originally initiated and sponsored by Mirek Hubacek, who has been a very active contributor to Valve World and ISO for the past 20 years. Even though Mirek is now enjoying his retirement, we would like to thank him for his vision and support for this project.
We would also like to acknowledge the tremendous support we have received from ISO, in particular from Ms. Helene Cros, Committee manager of ISO/TC 153, and from Jacques Peterschmitt, former Chairman of ISO/TC 153.
Finally, thank you to all the ISO Experts from around the world that have contributed, in one way or another, to make this new standard a reality.
About this Featured Story
This Featured Story is an article from our Valve World Magazine October 2021 issue. To read other featured stories and many more articles, subscribe to our print magazine.
“Every week we share a new Featured Story with our Valve World community. Join us and let’s share your Featured Story on Valve World online and in print.”