Industrial gas generation is a strongly evolving market which has received an additional boost following the accelerated demand for oxygen following the global pandemic. In addition to oxygen, gases such as hydrogen and nitrogen are also expected to drive market growth. As for production, there is a trend towards on-site generation based on PSA technology. OMAL SpA has developed an axial valve – VIP and VIP EVO – whose features create additional benefits when used on PSA production skids.
By Lucien Joppen
There are several sources as regards data about the global market for industrial gases. Fortunately, the market research agencies involved report comparable numbers. Grandview Research states for example that the global industrial gases market totalled roughly USD 92m in 2020, and it is set to grow at a CAGR of 6 per cent during the forecast period of 2021-2028.
The agency says that this growth can be attributed to the diversified application of gases in industries, numerous government initiatives to shift toward alternative energy sources, and the development of the healthcare infrastructure. “Additionally, the prosperity of the food processing industry will contribute to future market growth.” Needless to say, the production of medical oxygen has received a big push as a result of COVID-19. Although the need for medical oxygen has become less pressing as a result of vaccinations and behavorial measures, there still is a structural supply-demand issue (see box text Structural shortage of medical oxygen).
Applications per sector
Besides oxygen in health care, industrial gases are used in various grades in an array of industries and sectors. As mentioned before, the food and beverage industry uses gases in the production of decaffeinated coffee and carbonating beer and soft drinks (CO2). Apart from the food processing sector, industrial gases are widely used in electronics, healthcare, chemicals, heavy metal, and petroleum.
For example, the heavy metal industry employs acetylene for the oxyacetylene flame to cut and weld metals.
Hydrogen is used in large volumes to manufacture chemicals (fertilizers etc.) and refine petroleum. The expansion in all these sectors is, therefore, expected to drive the industrial gases market growth. Nitrogen is used for example in blanketing LNG containers. Industrial oxygen is used for gas welding, metal manufacturing, and the production of glass and ceramics.
Trend towards local production
As for the production of these industrial gases, there is a trend towards localisation. There are various reasons to steer away (partly) from centralized production. For example, a centralized production of medical oxygen in developing countries could be hindered by poor infrastructure, hence the need for smaller scale production units.
“It makes sense”, says Giovanni Coombs, Export manager North-America at OMAL.
“This is not only the case in developing economies, there is also a solid business case for local production in developed nations.”
Centralized production involves additional environmental costs such as the need for road transport and inefficiencies related to the large size of the plants that are unable to be flexible in the face of fluctuating demand, Coombs explains. “When demand is low, large production facilities are generating less volumes which leads to higher operating costs. On the other hand, when demand is high – even exceeding supply – these plants are not scalable and therefore unable to produce what is required, leading to downtime for end-users.”
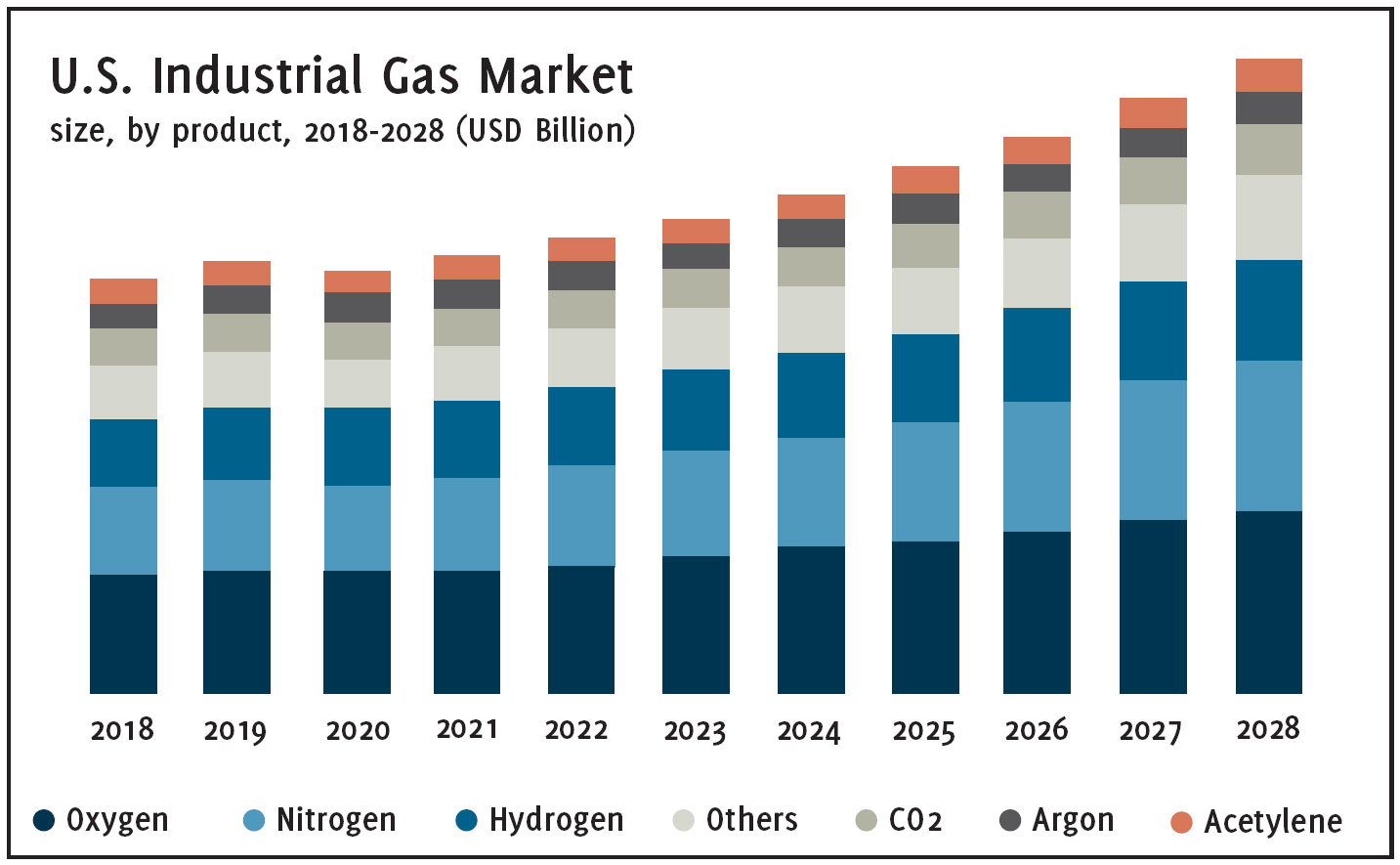
Tilting the playing field
There are also other advantages associated with localized production. According to industrial gas producer Atlas Copco, the price per litre is lower as supply and demand are the volumes with the specified purity levels. There is no need to pay extra for overspecified gas. Long-term and complex contracts are also not necessary. Furthermore, localized production eliminates to a large extent supply chain issues and CO2 emissions due to storage and transport. It also minimizes waste (leakages etc) which is more efficient and leads to less CO2 emissions. All and all, there is a lot in favour of local production.” It is fair to say that the pandemic has acted as a catalyst to push forward localized production. “On-site generation was already an option in the past”, Coombs says. “But as often happens, a crisis or a sense of urgency is needed to tilt the playing field.”
PSA as the preferred method
With the pendulum swinging towards localized production, Pressure Swing Adsorption (PSA) seems to be a preferred mode of production of industrial gases such oxygen or nitrogen, Coombs states.
Apart from PSA, there are other production modes, such as cryogenic technologies, electrolysis (hydrogen), syngas reforming (SMR plus PSA) for hydrogen and more bespoke technologies that are linked to the source and type of the industrial gas, for example hydrogen chloride which is produced by burning hydrogen in chlorine.
PSA is based on a physical binding of gas molecules to an adsorbent material. The respective force acting between the gas molecules and the adsorbent material depends on the gas component, type of adsorbent material, partial pressure of the gas component, and operating temperature.
The separation effect is based on differences in binding forces to the adsorbent material. Highly volatile components with low polarity, such as hydrogen, are practically non-adsorbable as opposed to molecules such as nitrogen, carbon monoxide, carbon dioxide, hydrocarbon derivatives, and water vapor. Consequently, these impurities can be adsorbed from a hydrogen-containing stream, and high-purity hydrogen is recovered.
Structural shortage of medical oxygen
Despite the use of oxygen medically for over 100 years and the World Health Organization (WHO) classifying it as an essential medicine in 2017, large population groups, especially in developing countries, do not have access to adequate supplies, states a McKinsey-article (COVID-19 exposes a critical shortage in developing countries, 2020).
The adverse impact of the shortage is most critically felt in neonatal care, with an estimated half a million newborns around the world dying annually from oxygen shortages. “As COVID-19 patient-care protocols have evolved, medical-grade oxygen is considered essential to treatments for critically ill patients, such as invasive ventilation and low- and high-flow oxygen therapies. In regions such as Africa and the Middle East, the surge in demand for medical oxygen to treat COVID-19 exacerbates pre-existing gaps in medical-oxygen supplies, leading to substantial supply shortages.”
With the emergence of COVID-19 and the need for medical oxygen, the World Health Organisation has focused on the production of this gas as it aims to ensure a steady and safe supply. The WHO has entered into the technical details, suggesting or validating specific equipment that could meet the need. For example, WHO has issued a Guidance Document for Pressure Swing Adsorption production units, providing technical specifications as the minimum requirements that these units must meet for use for the adminis-tration of medical-grade oxygen. “WHO already has validated a few manufacturers’ skids that meet specific requirements and initiated purchasing programs for oxygen generators in countries like India or South America to help local health agencies overwhelmed by the emergency”, Coombs says. “In this context, one of our axial valves has been vali-dated as an integral part of the system.”
Higher yields, low energy use
There are various advantages that have driven the acceptation of PSA technology in the production of industrial gases. First of all, the process works at a more or less constant temperature as pressurisation and depressurisation are used to perform adsorption and desorption.
“This technology is best suited given the technical requirements of smaller-scale units. Also, PSA is the most sustainable technology as heating or cooling are not required. The process also allows the generation of purer gas and therefore creates less waste. Often depending on the gas produced – the waste products of PSA-produced gas generation can be reused for other purposes in a kind of circular economy. In addition, it is easily scalable and modular to respond to peak demand. All and all, the combination of moderate energy usage and higher yields have made PSA into a winning technology.”
Better solution
It is for the PSA production process that OMAL has further optimized its axial valve to control the flow of industrial gases from one PSA unit to the other (pressurization and depressurization).
“To be fair”, Coombs states, “we have designed our coaxial valves more than 20 years ago to serve many types of applications, but in recent years they have found a perfect fit within PSA-units.” This market fit has stimulated OMAL to develop VIP EVO five years ago, which is a performance upgrade of the axial valve to meet the specific needs of this application, Coombs says.
“In most conventional units, either large or small-scale, ball or angle seat valves are used. Both solutions are commonly used but could be improved on in our opinion. Actuated ball valves have longer opening and closing times which leads to product loss and reduced purity of the gas generated. Angle seat valves result in larger configurations, making them less suitable for smaller-scale skids. Especially with these production units, scale and weight are more important as these units have to be transported and installed in locations (for example hospitals) where room is a critical factor.”
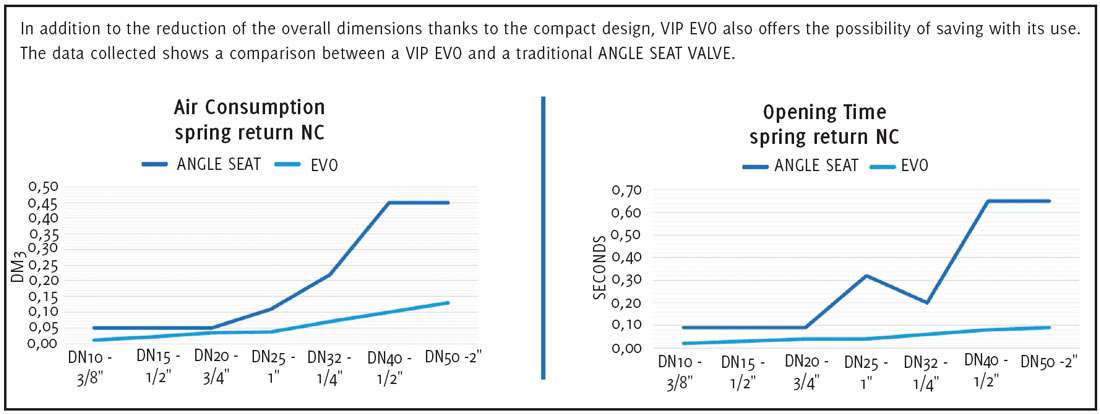
Competitive unit
As Coombs explains, OMAL’s coaxial valve is more compact as it incorporates all functions in a single device; both the opening and closing function of the ball itself with remote actuation typically relying on a pneumatic actuator.
“As I stated earlier, compact design is the way to go for small-scale production units. This way, skids can be designed to maximize production and yield by enlarging the generation tanks. Using axial valves also impacts the way the tubing system is designed as fewer components are needed, thereby saving on cost.
According to OMAL, there are more advantages, specifically for the operational point of view, from using an axial valve. First of all, the control aspect. “Axial valves are more accurate and have faster opening and closing times which results in less product loss and greater product purity. This seems like a small gain but valves in small-scale units have high-frequency cycle times
(600,000 cycles). Axial valves also need less torque to move which translates into down-sized equipment such as compressors and pumps. Therefore, both on CAPEX as well as on OPEX our VIP contributes to a more competitive unit.”
Given the advantages of the axial valves, the market reception was very positive, Coombs states. “We increased our overall sales in 2021 by 30 per cent compared with 2020. The sales of axial valves have hugely contributed to this sales increase. A majority of VIP sales were installed in brand-new gas generation units. Having said this, older units can be retrofitted with this valve too although this operation would also suggest an adjustment of the original equipment such as tubing, pumps and compressors.”
Sustainable mission
Finally, VIP EVO is also a perfect example of how OMAL’s strategy is reflected into the company’s R&D and new product development. “From the early beginnings, we have incorporated sustainability, guiding our way of doing business and creating value for our stakeholders”, the company states.
“Our aspiration is to increasingly and gradually integrate sustainability into everyone’s daily actions to obtain consistent operations in line with the most virtuous companies in the field of corporate social responsibility.” OMAL says that it is already reducing the environmental impact generated by production activities to prevent pollution of the area in which it operates and that resulting from the use and disposal of its products. OMAL is also certified according to the most important and advanced Italian and international social, ethical and environmental standards.
Società Benefit
In its effort to continually improve its standards, OMAL became a ‘Società Benefit’ in 2021. Companies that achieve this status, ‘combine the goal of profit with the purpose of creating a positive impact for society and the environment and operate in a transparent, responsible and sustainable way.’
“Being a Società Benefit allows us and our employees, to be part of a network of companies pioneering a change in the very concept of business, restoring value to humanity and the environment by developing markets and exhibiting those set to be the best and most profitable companies of the future”, the company states.
In terms of product development, it means that OMAL strives to reduce the environmental impact of its products and increase worker safety, both through product characteristics and production methodology.
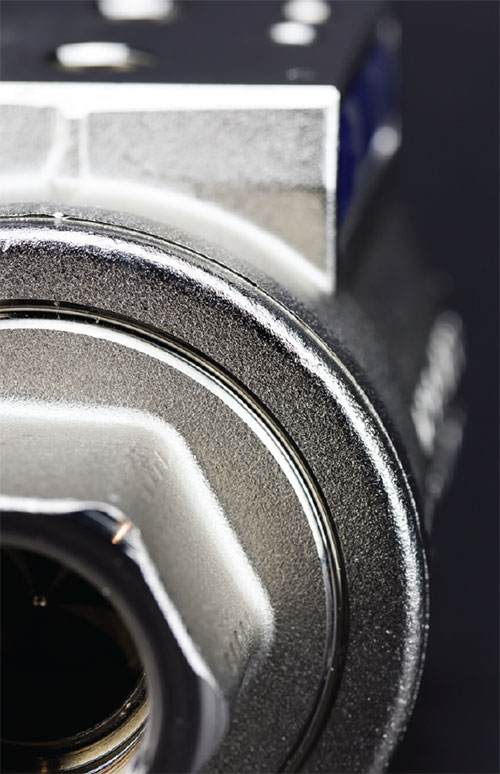
VIP EVO
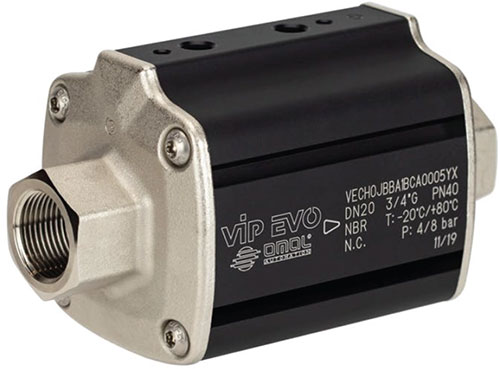
VIP valve
The pneumatic coaxial valve VIP EVO is the evolution of the OMAL’s VIP valve. The EVO is an interception valve (between pipe IN-OUT) with built-in control system. It works thanks to the internal movement of a piston supplied with air. At the end of its stroke (VIP EVO valve is an ON/OFF valve), the piston presses on the seat seal, stopping the fluid from flowing, or moves away from the seal, allowing intercepted fluid to flow.
As the seat is perfectly tight and the intercepted fluid pressures discharge on it, the pressure necessary to move the piston is hardly affected by the fluid pressure. Internal fluid-dynamics has been designed to reduce turbulence and pressure loss.
• Maximum compatibility with different types of fluids depending on the seals used (EPDM, NBR, FKM). No risk of injury due to moving parts. Easy mounting. Lifetime up to 10 times longer than a ball valve with reduced maintenance costs.
• 70 per cent less air consumption compared with an actuated valve with SR pneumatic actuator therefore less load on the compressor as well as the possibility of using a smaller sized compressor.
Source: OMAL.com
End of life
OMAL states that a longer life span is not only more cost-friendly for end users but also reduces waste throughout the supply chain and improves the CO2 footprint of its equipment. “We work on technical solutions to reduce the deterioration of moving parts to improve product functionality, reduce the torque and subsequently reduce the energy needed for activation and guarantee the maintainability of the product”, Coombs says.
End of life is an important factor in OMAL’s product development. The company states that it designs products in such a way that they can be completely dismantled, separating the different materials for correct disposal. The company instructs its clients by providing a blue-print listing all materials and the way these should be disposed.
“We want to make the world a more sustainable place which involves designing and manufacturing products that help our clients be more sustainable and more competitive. This also rings true for VIP EVO and industrial gas production.”
About this Featured Story
This Featured Story is an article from our Valve World Magazine April 2022 issue. To read other featured stories and many more articles, subscribe to our print magazine.
“Every week we share a new Featured Story with our Valve World community. Join us and let’s share your Featured Story on Valve World online and in print.”