^ The Tata Steel plant on the industrial estate in Jamshedpur.
Article by John Butterfield
___
In recent years Tata Steel has committed itself to becoming a leader in water conservation and in significantly reducing its impact on water as a company. At a time when global climate change is having a significant impact on all our lives, the company has committed itself to enhance policies that improve water sustainability.
As such, it has won the prestigious Global Water Intelligence Award 2019 for ‘an Industrial Water Project’ by reclaiming effluent. This was done by having the impressive tertiary Bara wastewater treatment plant built in its home city of Jamshedpur in the state of Jharkhand, north-east of India.
Project
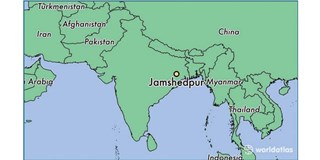
The Tata Group is located at the industrial heart of Jamshedpur, a city which contains one of the most populous urban agglomerates in the Indian state of Jharkhand. One of the company’s major ambitions for Jamshedpur is to see it become the first zero liquid discharge city In India. This project has therefore marked a huge step towards fulfilling this goal.
He added: “Tata Steel and Jusco are proud of the fact that the benefits of this project will also be shared with other industrial units in the city. We further thank Global Water Intelligence and the honorable jury and voters from various countries for selecting this project out of a strong group of international projects with a similar intention.”
The importance of what Tata Steel is doing
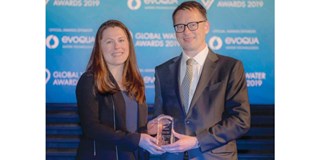
The World Economic Forum report identifies the shortage of freshwater as one the greatest risks for mankind during the coming years. In India, water availability per capita, for example, has declined by more than 60% over the past fifty years (from 3000 cubic meters to 1123). Putting this in perspective, the global average is around 6,000 cubic meters per capita.
Wastewater valves
Tata Steel uses their 4R methodologies to reduce, reuse, recycle and charge their water supply. To reduce fresh water consumption, they comply with a water audit and have real-time, online monitoring. By reusing drain water for low-end applications such as coke quenching, blast furnace quenching, dust control, tire cleaning, and pellet and sinter cooling, they significantly reduce their fresh water consumption. Recycling takes place in the central wastewater treatment plant and the output is purified water. Charging is done through aggressive rainwater harvesting measures, allowing rainwater to do what nature designed it to do! In fact, Tata Steel had commissioned the construction of Dimna Lake in Jamshedpur as a catchment area in the rainy season. Today it has the capacity of 6,292 million gallons of water. A store big enough to supply 14% of Jamshedpur’s annual water demand!
In short, the 4R methodology has helped Tata Steel to reduce total freshwater consumption by almost 35% over the past five years! The flagship steel mill in Jamshedpur consumes as much water as it did when it had only half the steel production capacity compared to today. It will be interesting to see what other benchmarks Tata Steel can set in the coming years.