As the focus of global energy provision moves away from fossil fuels towards renewable energy, it is important for the entire energy supply chain to play a role. Hydrogen production is increasingly relevant to this as it offers a versatile fuel source and feedstock that is carbon free when burnt, releasing no emissions. Its production can be decarbonised through the creation of green hydrogen.
By Andy Filkins, Head of Strategy at Rotork CPI (Chemical, Process & Industrial)
The Paris Agreement (the international treaty addressing climate change) lays out a goal of limiting global warming to between 1.5 and 2 °C compared to pre-industrial levels. A reduction of greenhouse gas emissions is essential in achieving this goal, for example by addressing CO2 emissions in hard-to-abate sectors such as the production of steel and fertilisers. Hydrogen is viewed by many governments and private companies as an indispensable piece in solving the low-carbon energy puzzle.
The International Energy Agency (IEA), in their report The Future of Hydrogen, state: “Hydrogen can help tackle various critical energy challenges. It offers ways to decarbonise a range of sectors – including long-haul transport, chemicals, and iron and steel – where it is proving difficult to meaningfully reduce emissions. It can also help improve air quality and strengthen energy security.” 1
A focus on the importance of hydrogen for the future has been clearly stated by global governments and leaders in recent years. It is estimated that demand for hydrogen could grow eight-fold by 2050. 2 Given this, it is important to understand both the different types of hydrogen (plus their production processes) and how the equipment involved in that production must provide high degrees of reliability and efficiency, ensuring a safe environment.
In Net Zero by 2050: A Roadmap for the Global Energy Sector report, the IEA say (referring to oil and gas) that: “while traditional supply activities decline, the expertise of the oil and natural gas industry fits well with technologies such as hydrogen (and) CCUS”.3 Those currently involved within these industries are therefore ideally positioned to take advantage of the benefits that the emerging market of hydrogen offers.
What is hydrogen and how is it produced?

Hydrogen is found in a huge number of natural resources. Supply is plentiful but it requires separation from the element it is joined to (for example, water is comprised of hydrogen and oxygen). Most of the world’s hydrogen is currently produced using fossil fuels such as coal and natural gas as a heat source, but it can also be made with renewable energy sources.
Traditionally, hydrogen is created by a reaction with either steam (“steam reforming” or “steam methane reforming”), oxygen (“partial oxidation”), or both in sequence (“autothermal reforming”). Steam reforming methods are the most common and result in carbon dioxide emissions. Hydrogen produced from this process is known as “grey hydrogen”.
Carbon emissions can be captured and stored (often buried in the ground). The hydrogen produced is known as “blue hydrogen” and the process is known as Carbon Capture and Underground Storage (CCUS). Carbon dioxide is produced but captured and not released into the atmosphere.
Clean and stable energy source
The production of hydrogen without the use of fossil fuels is the necessary future for the hydrogen industry, if it is to continue working towards targets that vastly reduce greenhouse emissions and contribute to a carbon-neutral future.
“Green hydrogen” is created by using nuclear or renewable energy (such as solar and wind) as the feedstock. If the fuel used and processes undertaken do not involve the creation of carbon emissions, this hydrogen can truly be considered as carbon neutral. It is a clean, stable energy carrier for the renewable energy that creates it, capable of being stored under high pressure or as a liquid. It can be transported in tanks or through pipelines and then used when required, through combustion or used in fuel cells.
Green hydrogen answers concerns about the carbon emissions which can result from the creation of heat needed within traditional hydrogen production. An emerging technology within green hydrogen is the use of electrolysis to create hydrogen; an electric current is applied to water, splitting it into hydrogen and oxygen. The energy used in this process is usually a surplus from renewable sources.
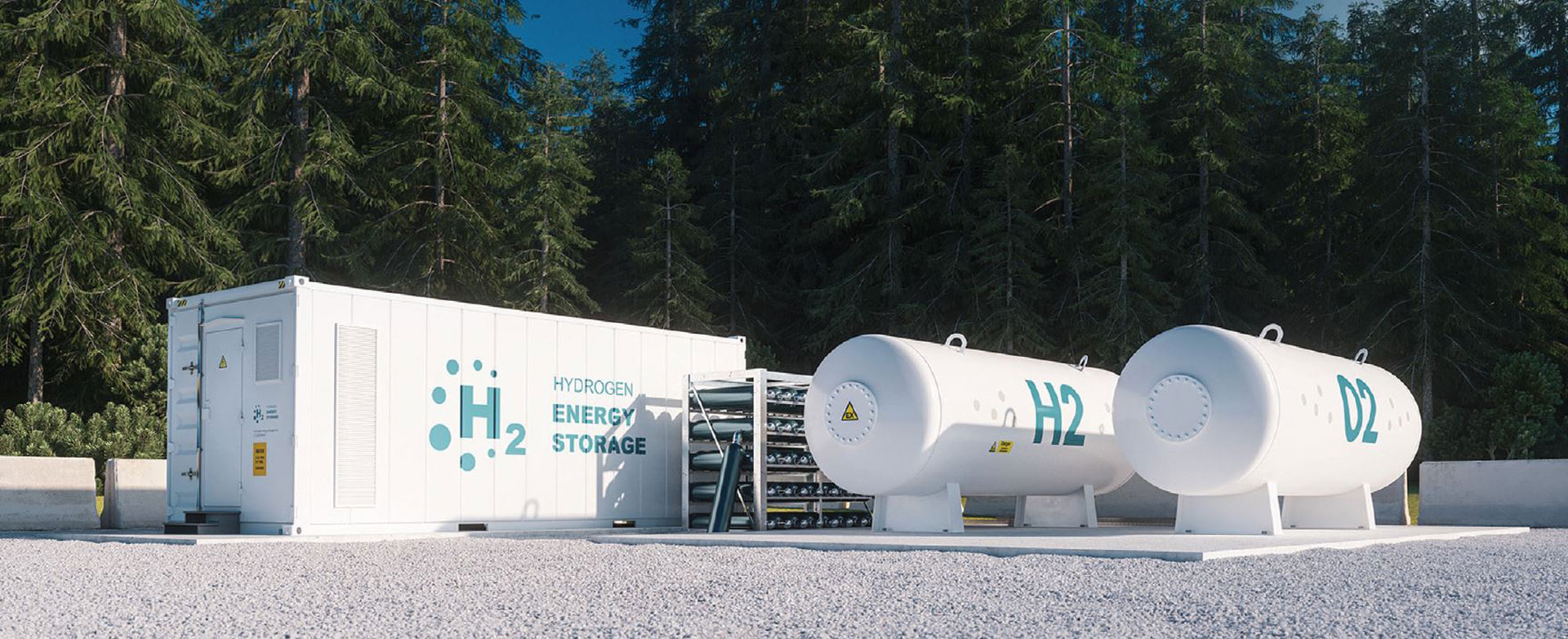
The role of flow control
Flow control products can be found in almost every process control application throughout the green hydrogen industry, from renewable power generation to hydrogen production, storage, distribution and consumer delivery. Products such as actuators are especially necessary in controlling the water at the heart of the electrolysis process.
Many different technologies are used to produce hydrogen, including flow control such as valves and actuators, at all stages of production, storage, transportation and utilisation.
The production process of hydrogen presents challenges that can be managed through the effective planning, control and use of specialist products that offer the appropriate regulation. Valve actuators remotely control valves and the flow of various liquids within hydrogen production, including water, natural gas and hydrogen. Additionally, auxiliary equipment such as sensors, regulators, flow meters and solenoids are required. The most common actuators are electric, that offer modulating or on/off control and fail-safe capabilities.
Efficiency key
New energy hydrogen applications, including electrolysers, fuel cells and refuelling stations are in their infancy but have significant potential for the flow control market, as amounts of produced hydrogen is set to grow in the coming years.
Hydrogen can be costly to produce. It is therefore essential that the production process is as smoothly and efficiently run as possible. Flow control products can contribute to this.
The automation of the flow of water, hydrogen and any associated hydrocarbons via actuators and related instrumentation ensures efficiency and peak performance. There is no possibility of human error and levels of accuracy and precision are increased.
Hydrogen can be dangerous (it is colourless and odourless, as well as highly flammable) so explosion-proof products (with appropriate approvals such as ATEX, CSA, IECEx) must be used in its production. Use of Rotork products within hydrogen production processes guarantees an accurate, reliable, efficient and above all safe operation.
Industrial environments can be tough places and all flow equipment must be durable and reliable. One of the great benefits of actuators is the precision control they offer, which is essential in the production of hydrogen. If the actuators are electric, emissions are not released during use (such as in the production of renewable energy and the subsequent creation of green hydrogen). Explosion-proof actuators, in a hazardous environment, ensure safety. Fail-safe flow control solutions are usually specified on safety critical systems such as hydrogen storage tanks, transport and distribution networks. Distribution stations demand the highest levels of safety, provided by actuators and flow control.
To conclude this article, as energy providers adapt to a world that is being shaped by emission reduction responsibilities, the role played by hydrogen increases in importance. The move from fossil fuels towards renewable and environmentally friendly sources of energy means that green hydrogen is an exciting option. The safe and reliable production of green hydrogen requires flow control equipment at every stage.
References:
1: The Future of Hydrogen (windows.net), 2019, page 13.
2: Hydrogen – Energy Transition Institute – Kearney (energy-transition-institute.com)
3: Net Zero by 2050: A Roadmap for the Global Energy Sector, 2021, page 23.
For further information please contact:
Sarah Kellett
Group Marketing Communications Manager Telephone: +44 (0) 1225 733492
Email: Sarah.Kellett@rotork.com
About Rotork:
Rotork is a market-leading global provider of mission-critical flow control and instrumentation solutions for oil and gas, water and wastewater, power, chemical process and industrial applications. We help customers around the world to improve efficiency, reduce emissions, minimise their environmental impact and assure safety.
Rorork PLC
Brassmill Lane, Bath, BA1 3JQ – UK
About this Featured Story
This Featured Story is an article from our Valve World Magazine October 2021 issue. To read other featured stories and many more articles, subscribe to our print magazine.
“Every week we share a new Featured Story with our Valve World community. Join us and let’s share your Featured Story on Valve World online and in print.”