This article discusses the importance of hydrogen, followed by the challenges of sealing hydrogen and comparing the leakage performance of fiber-based gasket materials between hydrogen and helium.
By Anna Berger, Frenzelit
The current search for alternative sustainable energy sources that generate significantly lower CO2-emissions has led to an increased interest in hydrogen in recent years.
At the moment, most hydrogen which is used in industrial applications is so-called “grey hydrogen”, which is produced in a steam reforming process, where fossil energy (e.g. natural gas) is used, and the greenhouse gas CO2 is released in the atmosphere as a byproduct. Grey hydrogen is therefore not climate-neutral.
However, hydrogen has many properties, which make it interesting as a possible alternative to fossil fuels. The main reason is that it can be generated in a climate neutral process via electrolysis using only water and renewable energy. Hydrogen which is produced with this process is referred to as “green hydrogen”.
Another important advantage of hydrogen is the high versatility it provides. It has a high energy density and can therefore be used as an energy source, for example as a direct replacement for natural gas in combustion processes, or by transferring it into electric energy in a fuel cell. Alternatively, hydrogen can also be used as a starting material for various power-to-X processes. This means that hydrogen is converted to other substances that are easier to store and transport than hydrogen and can either also be used as fuels or as starting materials for further processing (e.g. ammonia, methane or methanol).
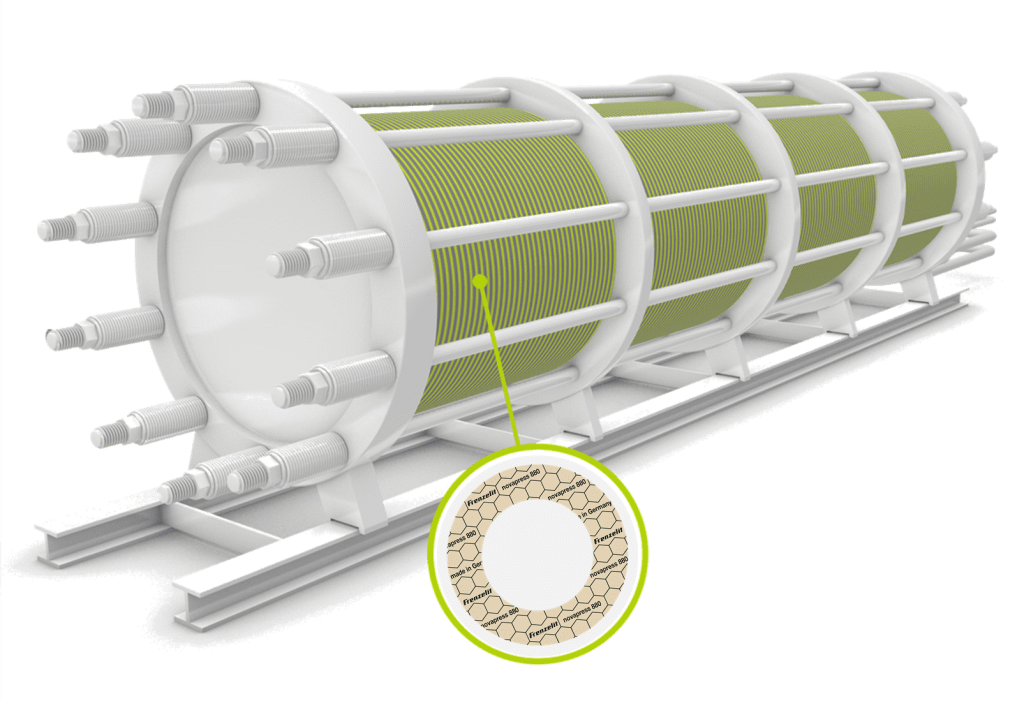
Gaskets in hydrogen applications
For every hydrogen application, there is a need for efficient and well-performing gaskets to prevent hydrogen-leakage. The requirements for gaskets in these applications are as diverse as the hydrogen applications themselves and can be quite challenging in some cases. Some hydrogen applications require extreme temperatures, ranging from cryogenic applications with liquid hydrogen at very low temperatures (- 253 °C), to temperatures up to 1000 °C in solid oxide fuel cells or high temperature electrolysers. Different processes also require chemical resistance against various different media, for example against oxygen in combination with potassium hydroxide in alkaline electrolysis. Apart from chemical resistance, gaskets which are used as stack gaskets in electrolysis (figure 1) and fuel cell applications usually also have to be electrically insulating, have a high mechanical stability and a defined relaxation behaviour.
Challenges of sealing hydrogen
However, no matter how different the requirements for gaskets in hydrogen applications are, all of them have one common task, which is that they have to seal the challenging medium hydrogen as well as possible.
The leakage performance of flat gaskets is usually determined in tests using nitrogen or helium as a test gas. For the gasket characteristics according to the European standard EN 13555, which are the basis for flange calculations according to leakage data, is measured using helium as a test gas. Helium has the advantage that it is an inert gas which in not reactive and does not burn and can therefore be handled without safety concerns. Helium was also chosen as an ideal gas for leakage tests due to its small atom-size, low density and high volatility. Due to these properties, helium is more challenging to seal compared to most other gases. So, the general assumption
is that if a gasket material shows a good sealing performance in a helium leak test, it will show at least a similar or even better leakage performance for other, less challenging media like nitrogen or natural gas. However, for hydrogen this assumption might not be true, as hydrogen is extremely challenging to seal due to its low density and small molecule size. Furthermore, hydrogen can be a safety hazard, as it is a very reactive gas which can burn easily and is potentially explosive. Therefore, it is even more important to minimise the emissions as much as possible by using high performance sealing materials.
The aim of this report was to investigate if the leakage performance of fiber-based gaskets is comparable when hydrogen and helium are used as test gases, or if hydrogen is noticeably more challenging to seal.
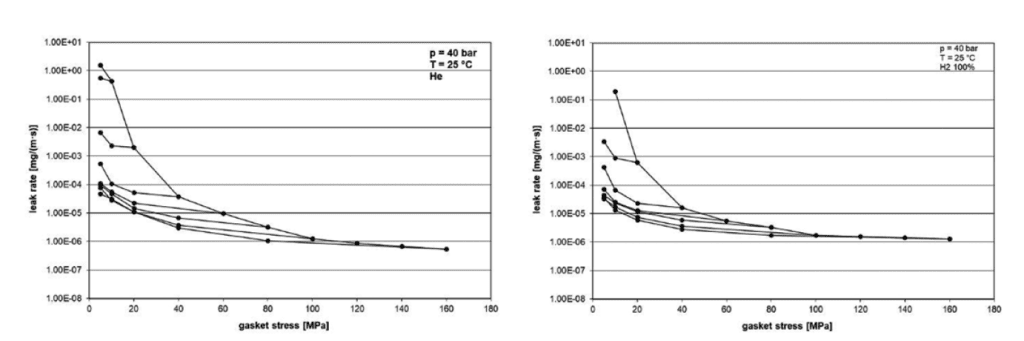
Fiber reinforced gasket materials
There are many different groups of flat gaskets which are suitable for different application conditions. For example, gaskets based on expanded graphite are suited exceptionally well for challenging applications at elevated temperatures up to 550 °C and high pressures, while PTFE-gaskets are ideally suited for applications that are chemically very challenging. These materials have already been investigated regarding their sealing performance in hydrogen applications in previous articles.
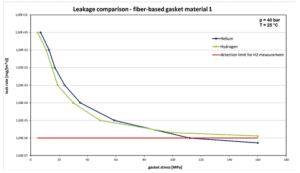
For this report, we focused on our fiber-based gasket materials. Fiber-based gaskets are composite materials which are comprised of an elastomer binder, often NBR, reinforcing fibers (mainly aramid-fibers) and inorganic functional fillers. These gaskets can typically be used for temperature ranges from -100 to +200 °C, are suitable for a wide range of different media and can cover most conventional applications. For this report, we investigated the hydrogen leakage rates of two fiber-based gasket materials. These materials represent the newest generation of NBR-bonded fiber-based gaskets and are characterised by their exceptional adaptability and their extremely good leakage performance in standard helium leakage tests. The aim of this investigation is to evaluate if the leakage behaviour for these materials is comparable when hydrogen is used as a test gas instead of helium.
Comparison of hydrogen and helium leakage tests
For this investigation, the leakage rates of two fiber-based gasket materials were determined according to DIN 13555 using helium and hydrogen as test gases (material 1 and material 2). All tests were performed on an TEMESfl.ai1 test device with mass spectrometric detection at room temperature with a test pressure of 40 bar of either hydrogen or helium using gasket specimens in the dimension DN40/PN40 (outer diameter: 92 mm, inner diameter: 49 mm) in a thickness of 2 mm. For the leakage tests, a surface pressure range of 5 MPa to 160 MPa has been applied in cyclic loading and unloading steps, with a leakage measurement after every loading or unloading step. The resulting leakage diagrams with loading- and unloading-curves for the hydrogen and helium measurements of both materials are depicted in figure 2 and figure 4. For a better comparability, the loading curves of the helium and hydrogen measurements are shown in a simplified diagram in figure 3 (material 1) and figure 5 (material 2).
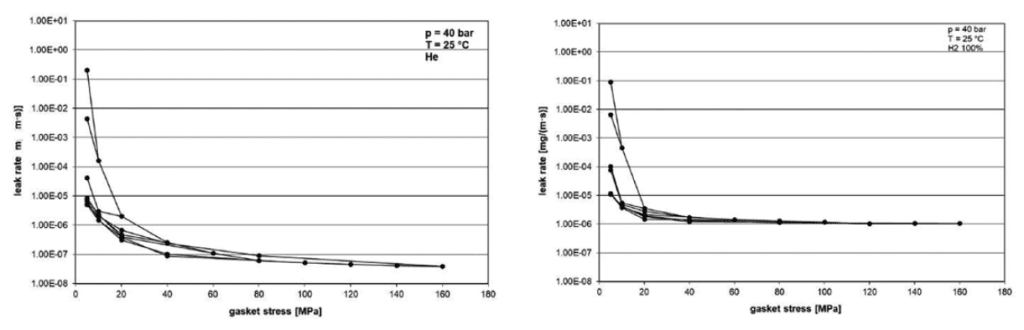
The first material tested is a gasket-material with a high compressibility of 18 % according to ASTM F 36 J, which leads to an excellent adaptability to the flange surface, and therefore a good leakage performance. For the fiber-based gasket material 1, the leakage value for the hydrogen measurements is slightly lower than for the helium measurements when the gasket stress is below 60 MPa. The leakage class L0,01, which is the limit value of the German TA-Luft regulation, is reached at a gasket stress of 17 MPa for helium, and 15 MPa for hydrogen. For gasket stress levels higher than 60 MPa, the leakage value for helium is slightly lower compared to hydrogen. However, the general trend of the leakage values for the loading and unloading curves are very similar to each other, which indicates that it is not significantly more challenging to seal hydrogen, compared to helium.
The second fiber-based gasket material which was tested for this report (material 2) is a gasket material which is exceptionally soft and has an excellent adaptability to the flange surface (compression according to ASTM F 36 J:39 %). This material has been designed specifically for reaching extremely low leakage values even at low gasket stress. So compared to material 1, material 2 shows an even better leakage performance in the standard helium leakage test according to EN 13555. The tests in this report show that this behaviour also remains valid for leakage tests with hydrogen.
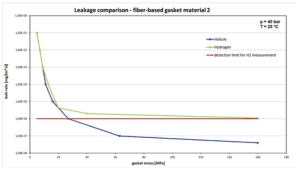
For material 2, the leakage class L0,01 is already reached at 7 MPa for hydrogen and helium. The leakage curves for the hydrogen and helium measurements are almost identical for low gasket stress until 20 MPa. The leakage rate 10-6 mg/(m*s) is reached at an assembly stress of 27 MPa for the helium measurement. For hydrogen measurements with the standard test procedure, 10-6 mg/(m*s) is the detection limit of the mass spectrometer, which is used as a detector in the test apparatus. This explains the increasing difference of the measurements with hydrogen and helium for higher assembly pressures. The leakage rate of the helium measurements is constantly decreasing with higher gasket stress, while the hydrogen measurement cannot fall below the value of 10-6 mg/(m*s) due to the detection limit of the hydrogen mass spectrometer. However, the fact that the results for low gasket stress are identical for hydrogen and helium indicates that in this case, the sealing behaviour is also very similar for hydrogen and helium.
Summary
The results of these investigations show that the leakage data measured with helium and hydrogen according to EN 13555 are very similar to each other. These results are also in line with previous reports for graphite and PTFE gaskets that have been published in previous issues of this magazine. Of course, there are many different fiber-based materials with different properties and different leakage performances, so this report cannot fully prove that hydrogen and helium show a similar behaviour in leakage tests for all materials. However, due to the similar composition of fiber-based materials and the results of the materials that have been tested so far, one can assume that the well-established helium leakage tests according to EN 13555 can also be used as a basis for calculation for most hydrogen applications.
About the author
Anna Berger is a chemist and joined the R&D department of Frenzelit five years ago, after finishing her PhD in Organic Chemistry. She now works as an application engineer for the Industry Division of Frenzelit GmbH and is a member of the ESA Flange Gasket Division.
About this Technical Story
This Technical Story is an article from our Valve World Magazine, February 2025 issue. To read other featured stories and many more articles, subscribe to our print magazine. Available in both print and digital formats. DIGITAL MAGAZINE SUBSCRIPTIONS ARE NOW FREE.
“Every week we share a new Technical Story with our Valve World community. Join us and let’s share your Featured Story on Valve World online and in print.”