Testing of Flange Insulation Kit
Corrosion is of great concern because it can lead to health and safety issues beyond economic loss and unwanted downtime; for this reason, experts make special efforts to control or avoid its occurrence.
By Francesca Torriani, General Packing Italy SpA
Corrosion is a phenomenon defined as the degradation of a material, typically a metal, caused by a chemical or electrochemical reaction with its environment.
There are several forms of corrosion and the different combination of materials and conditions in a system usually causes more than one form of attack. The Association for Materials Protection and Performance (AMPP) divides the different forms of corrosion into three groups:
Group 1 – Corrosion readily identifiable by ordinary visual examination
Group 2 – Corrosion requiring supplementary means of examination
Group 3 – Corrosion requiring verification by microscopy.
For more details on various forms of corrosion please refer to the AMPP, The World Corrosion Organisation (WCO) and Gesellschaft für Chemische Technik und Biotechnologie e.V (DECHEMA) websites.
Forms of corrosion that can occur in a pipeline are not limited to Group 1. The corrosion prevention strategy discussed below is used to prevent galvanic corrosion. Galvanic corrosion, which is also called “dissimilar metal corrosion”, arises when two dissimilar metals are coupled in the presence of an electrolyte. More details on galvanic corrosion and pipe corrosion prevention strategies can be found in the article “Corrosion and corrosion protection for flange connections in pipelines” by Dick Pronk.
The main and least expensive strategy to prevent galvanic corrosion in a bolted flange connection is to isolate electrically the different metallic components; for this purpose, a flange isolation kit is typically installed. A flange isolation kit consists of:
1. Isolating gasket,
2. Isolating bolt sleeves,
3. Isolating bolt washers,
4. Steel washers.
For the correct selection of the isolation kit, the following information is a minimum requirement: Pipe nominal diameter, pipe material, pressure class, flange dimension, flange type, flange schedule, operating temperature, operating pressure, media and test requirements.
Isolating gaskets
Isolating gaskets can be full face or flat ring. The first type is a gasket with bolt holes and with an outer diameter equal or even larger than flange outer diameter. The latter is designed so that the outer gasket diameter fits inside the bolt circle. The inside diameter of the gasket is usually optimized to fit the bore pipe diameter, in order to avoid an area where debris could accumulate and lead to erosion or where other forms of corrosion could occur.
The manufacture and design of isolating gaskets depend on producers and applications; in fact, a large variety of types can be found on the market: from a soft material gasket to a gasket with an energized sealing system included in its core, to a gasket constituted by multiple components and multiple sealing systems. Materials that are used for the production of these gaskets should have at least the following characteristics: to be isolators, to have low cold-flow, to have low water-absorption and high compressive strength.
Historically, the first materials chosen for isolating gasket manufacture was phenolics around 1934. It was only in 1968 that glass-reinforced epoxy (GRE) was adopted for such applications. GRE has higher electrical and mechanical properties compared to phenolics, and for this reason, it is one of the most commonly utilized materials for isolation kits nowadays. Although GRE has excellent mechanical and isolating performance even when exposed to moisture, it can have permeation issues when exposed to certain media and/or to particular conditions.
For this reason, different combinations of proprietary materials and designs have been introduced and adopted over the last few years.
Isolating bolt sleeves
Isolating bolt sleeves are mostly designed for standard bolting and with a length that should be adequate to extend halfway inside the steel washer. As before, the material of these components should have at least: low water absorption, high dielectric strength and low cold-flow properties. As for isolating gasket, the preferred material is glass-reinforced epoxy. Naturally, other materials are available for specific media, particular conditions or high-temperature applications.
Isolating bolt washers
Isolating bolt washers must also be manufactured from materials that ensure low water absorption, high dielectric strength, low cold-flow properties and high compressive strength. Typically, these components are sized so that their internal diameter fits with the isolating bolt sleeve while the outer diameter fits inside the flange spot facing.
Steel washers
Steel washers are installed between isolating bolt washers and nuts to avoid unwanted mechanical failures of isolating washers during the installation. For this reason, steel washers have the same dimensions as the bolt isolation washers and are specially treated to prevent corrosion.
In general, all bolted flange connections must be properly assembled to avoid undesired leakages. In addition to that, when dealing with galvanic corrosion issues electrical isolation shall be assured; this is the reason why isolation kit installation is a crucial point to successfully reach both targets.
Isolation kit installation
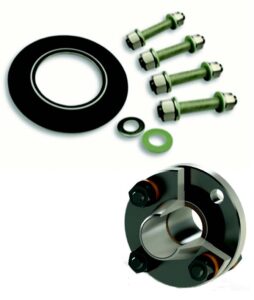
Ideally, isolation kit installation requires a clean and dry environment. Flange surfaces need to be clean, free from burrs or other superficial defects and correctly aligned. Flange misalignment could cause possible damage to the isolating sleeves.
The isolating gasket must be aligned correctly between flange surfaces to obtain a homogeneous gasket compression during bolt tightening. Alignment pins will facilitate bolted flange connection positioning. Subsequently, isolating sleeves are installed in the correctly aligned holes making sure that their length is correct. This will avoid possible rupture during mounting of the nuts if they are too long, or lack of isolation if they are too short.
After installation of the isolating sleeves, bolts with corresponding isolation and steel washers are inserted. During this phase, care must be taken to ensure that the isolation washers are positioned adjacent to the flange surfaces while the steel washers are placed between isolating washers and nut. It must be stressed that the bolt lubricant used during isolation kit installation should not be a metallic-based one.
After the majority of components have been positioned and the bolts tightened by hand using a cross pattern, alignment pins can be removed, and the tightening procedure can start. Bolted flange connection tightening must be performed in multiple steps using a cross pattern until the final step. Typically, these steps are divided as follows: 30% of the target torque, 60% of the target torque, 100% of the target torque and a final step during which 100% of the required torque is applied in a clockwise pattern.
After installation, a test must be performed to ensure the effectiveness of the isolation. Several types of tests can be performed to control the electrical isolation of the bolted flange connection so normally, the final customer should specify which test procedure should be used.
Additional measures can be adopted to protect isolating components from water absorption, which reduces their electrical resistance. Components that are outdoors and/or exposed to uncontrolled environments should be periodically inspected to check for the absence of unwanted debris. These pollutants could create undesired conductive bridges that could jeopardize the electrical isolation. In addition, during the periodical inspection, the integrity of protective barrier coatings can also be checked and remedied if damaged.
References
Images provided by Flexitallic and GPT Industries |
About the author
|
About this Featured Story
This Featured Story is an article from our Valve World Magazine December 2022 issue. To read other featured stories and many more articles, subscribe to our print magazine. Available in both print and digital formats. DIGITAL MAGAZINE SUBSCRIPTIONS ARE NOW FREE.
“Every week we share a new Featured Story with our Valve World community. Join us and let’s share your Featured Story on Valve World online and in print.”