Valve grinding technology has come a long way over the years. We have gone from large, cumbersome machines that could be used in the field only with great difficulty, to small lightweight equipment that produces excellent results despite its compact size. The goal is still the same – a perfectly flat valve seat and a tight seal.
By Björn Carlsson, R&D Manager, LarsLap International
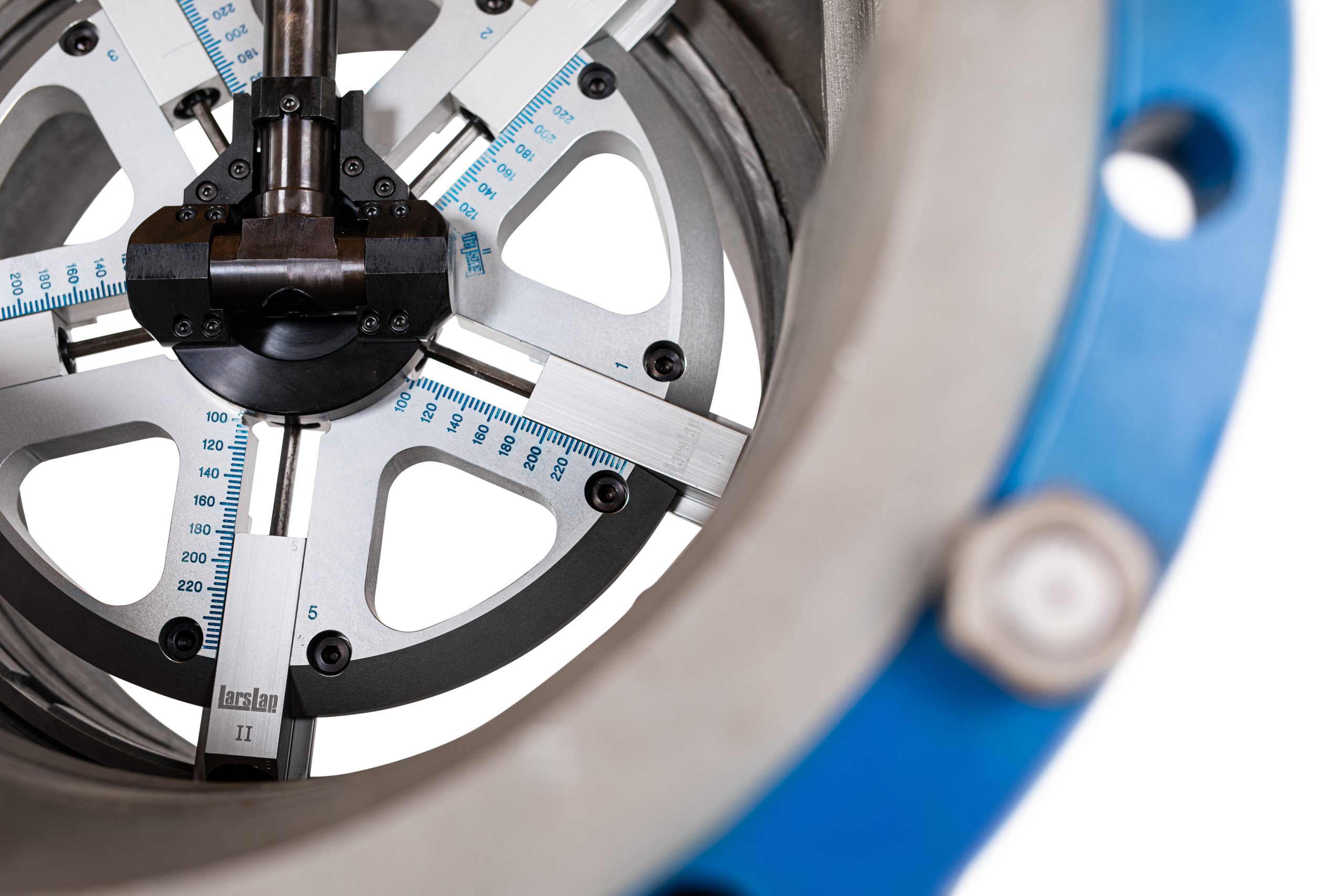
A tight seal is necessary for process valves to function properly. Leaking valves are annoying, compromise the performance of the process plant and can, in the worst case, be a hazard to health and safety and to the environment. Leakage of product and process medium also represents money that disappears down the drain.
Most valves in the process industry are hard sealing, metal to metal. To provide an effective seal, the surfaces need to be perfectly flat, finished to a high standard and, in many cases, polished to a mirror finish.
But over time, the sealing surface finish gets worn. In addition, particles might get caught between the disc and the valve seat, scratching the seat surface as the valve closes. There are many ways in which the valve seat can become damaged and stop performing.
If this happens to a critical valve, you may have an emergency situation where the valve needs to be repaired or replaced without delay to prevent costly downtime. But perhaps the most common scenario is that the valve is repaired during planned shutdown of the plant and the work is scheduled in advance. Preventing failure is far more economical than dealing with emergency repair or replacement.
Workshop or in-situ repairs
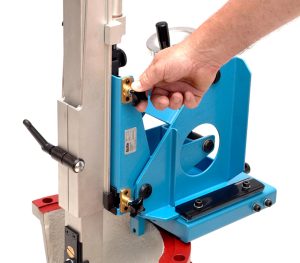
Valves can either be removed from the pipeline and overhauled in the workshop or repaired in-situ. The latter is almost always more efficient. The exception is if the valve is to undergo a major rebuild, for instance if a new seat needs welding into place.
In-situ maintenance is performed directly on the valve within the piping system, eliminating the need to re-install the valve.
The valve grinding equipment used in such situations needs to be portable, easy to use and be able to get into the small spaces inside the valve body. It must be easy to attach to the pipework and able to produce a flat surface regardless of the angle of the machine relative to the pipeline. Plus, it must produce an excellent result.
Early equipment for field use was heavy and cumbersome. Some still is. But over the years, designs have, in general, significantly improved, to the point where some users even prefer to use their portable equipment in the workshop as well.
Different machine designs
Grinding a valve seat can take a while and it is best to be patient. Pushing the machine down with great force will not speed up the grinding process, it will only build up heat and wear down the abrasive material quicker. It is the cutting action of the grains in the abrasive material that do the work, not the weight or pressure applied of the machine. So, it is best to leave the machine to do its work.
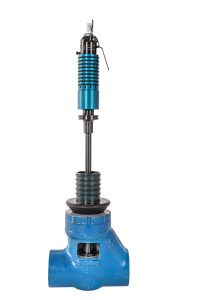
Material needs to be removed evenly from the valve seat. Sometimes, a solid flat disc is applied across the entire seat. This will remove more material from the outside of the seat, as a solid plate has a higher speed the further out on the diameter you are, making the seat slightly convex. It can also cause longitudinal scratches that result in inaccurate flatness across the entire seat.
To avoid this scenario, many machines have hubs with several individual, smaller grinding heads, each one of them grinding across the entire surface of the seat in a uniform manner.
A gear driven system uses a planetary gear in the hub that transfers mechanical power to the grinding heads using small diameter shafts. With this design, the centre of each grinding head is placed centrally over the valve seat.
The alternative is to use friction driven grinding heads. These have the centre of the grinding head on the inside of the valve seat, with only a small portion of its surface in contact with the seat. There are no shafts connecting the hub with the grinding heads. When the hub turns, the friction between the grinding head and the valve seat causes the grinding head to spin.
The shaft driven design tends to be more reliable. Friction drive can only transfer a limited amount of torque, which can cause individual grinding heads to slow down or stop altogether, resulting in inaccurate flatness of the valve seat.
Effective cross-hatch pattern
Placing the grinding heads centrally over the valve seat also produces a more effective cross-hatch pattern. This is the pattern caused by the abrasion, which should be criss-crossing itself, rather than run longitudinally along the seat. Even if the seat is lapped to a mirror finish, this pattern is always there, even though it may only be visible with a microscope.
The cross-hatch pattern breaks up the capillary paths of the fluid and helps produce a better seal. When the grinding head is placed centrally above the valve seat, the desired geometry of the cross-hatch pattern is easier to achieve.
Having successfully ground the valve seat this way, the user ends up with a perfectly flat seat with a fine surface structure, achieved far quicker than any other method can provide.
Preparing the job
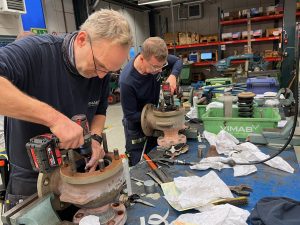
To ensure that dust can leave the work area, it is best to select a slightly oversized grinding tool. Any build up of dust will increase the temperature through increased friction. For instance, If the seat is 25mm (1”) wide, a Ø50mm (2”) grinding tool or larger could be used, providing the design of the valve body allows this.
Before starting grinding, the valve seat should be examined for damage. Start with a medium to fine paper, just to clean the surface prior to examination. Do not use a coarse paper at this stage. If the valve seat damage is only slight, coarse paper will not be needed and you will only have made more work for yourself. Also, there is only a finite amount of material in the valve seat, so using a fine paper at this stage prolongs the life of the valve.
If the seat damage turns out to be severe, proceed with coarse paper. Otherwise, continue with fine or medium paper. Use progressively finer papers, moving into micron sizes. When the valve seat is completely smooth, finish off with fine abrasive, diamond paste or slurry, depending on the surface finish that is needed. For a gate valve, this may be a smooth, dull gray finish, whereas for safety valves and valves handling gas, a mirror finish is frequently required.
Selecting the abrasive
When selecting the grade of grinding paper, it is important to note that grit and micron paper are graded according to different scales. For grit paper, the number on the back indicates the number of grains within a certain area. A low number means a small number of large grains and a coarse abrasive. With micron paper, the number refers to the size of the individual grain. A low number indicates that the particles are small and that we have a fine abrasive.
This means that the scales indicating the grade of the abrasive operate in opposite ways for grit and micron paper. 100 grit and 100 micron provide roughly the same rate of abrasion. But beyond that, the two scales work in opposite directions.
Grit paper is generally used to make the surface perfectly flat and micron paper to work up a smooth surface. The finest grades of micron paper can produce very smooth surfaces.
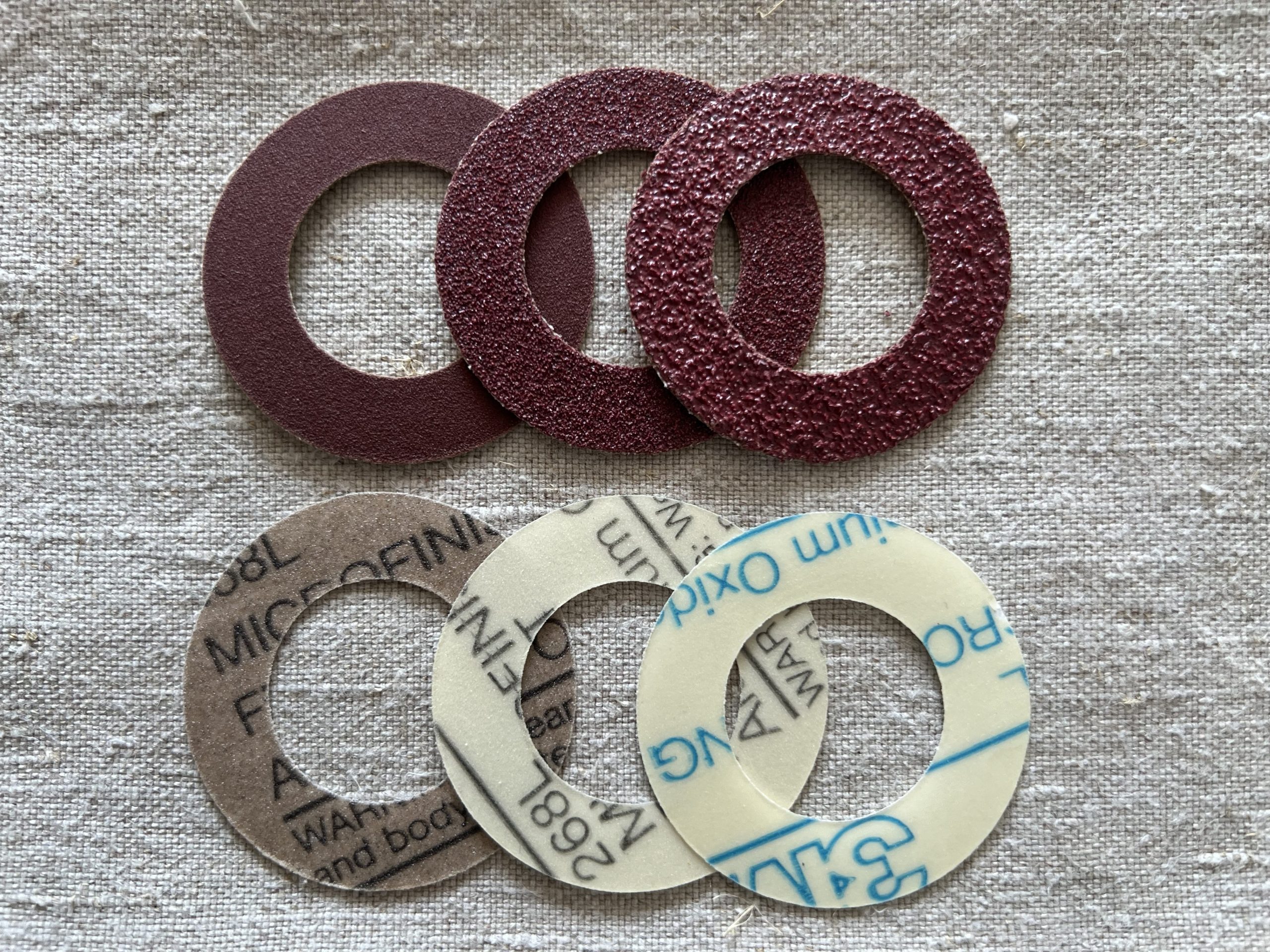
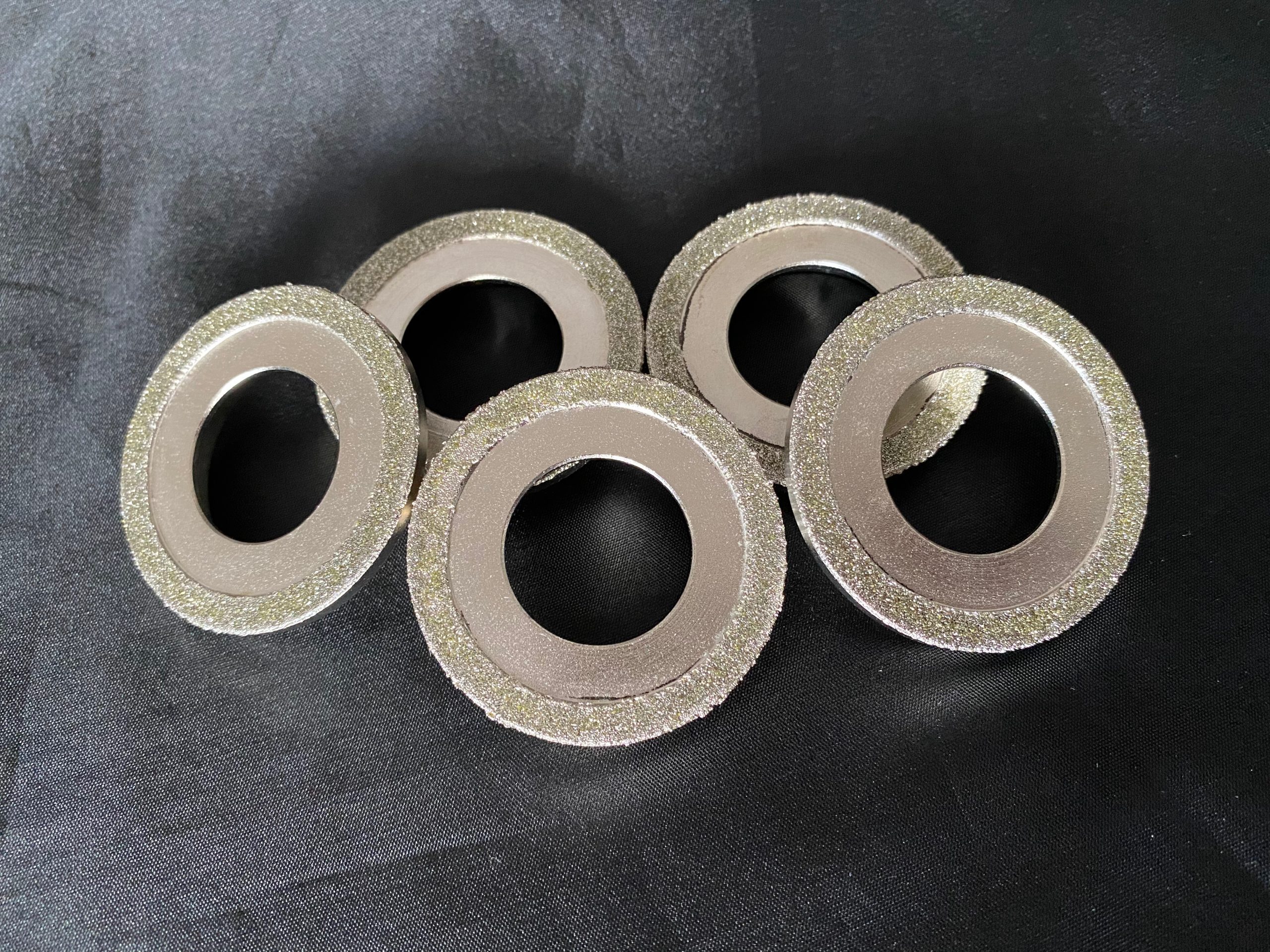
Alternatives to abrasive paper
If the seat material is very hard, diamond abrasive can be the solution. This is available as metal grinding heads with the diamond abrasive permanently attached. Because the diamond abrasive is very hard, there is no need to replace the grinding material. The same grinding heads are just used over and over again.
Another alternative is cubic boron nitride (CBN). This can be tried if even diamond fails to make an impact. Both diamond and CBN are extremely hard materials. They have the same structure, but diamond is made up of pure carbon, while CBN consists of boron and nitrogen.
CBN is often the better choice when working with steel, as steel has a high affinity to carbon. The steel can absorb carbon atoms from the diamond and erode the grit. CBN, on the other hand, does not contain any carbon.
Light machines make light work
“I have used both the modern, lightweight type of valve grinding machines and more sturdy, traditional designs and the difference is like night and day. The newer designs are far easier to work with,” says Rickard Nyberg, technical support manager at Vimab, Sweden’s largest valve service company.
“Traditionally designed machines are heavy and cumbersome and can be extremely difficult to get into tight spaces. The modern machines I work with now, by contrast, are lightweight, easy to handle and simple to set up. With their multiple grinding heads they achieve very effective abrasion.
“They also have nifty little features that make the work easier. For instance, there is no need to remove the whole rigging to grind the reverse side of the wedge in a gate valve – you can just raise the machine, flip the it over 180° and start again on the other side. You can also grind gate valves and globe valves with the same machine, which is a great advantage.”
Improved efficiency
With a light weight machine, you can today achieve the same surface finish with an in-situ repair as you would from a workshop repair using much heavier equipment. The explanation is the circle of individual grinding heads powered by shafts from a central grinding head. This provides accurate, controlled grinding action. Combined with appropriately selected abrasive materials, this will give excellent results in a short space of thim, ideal for improving the efficiency of valve service jobs in any application.
About the company
LarsLap International is a manufacturer of valve grinding machines with individually driven grinding heads. The company, based in Sweden, provides machines, abrasives and systems to service a wide range of valves for users all around the world.
About this Technical Story
This Technical Story is an article from our Valve World Magazine, June 2024 issue. To read other featured stories and many more articles, subscribe to our print magazine. Available in both print and digital formats. DIGITAL MAGAZINE SUBSCRIPTIONS ARE NOW FREE.
“Every week we share a new Technical Story with our Valve World community. Join us and let’s share your Technical Story on Valve World online and in print.”