Control valves had their heydays in the 1960s. Valve types designed in this decade account for around 80 per cent of all control valves sold today. There has been a noticeable lack of basic research, R&D and new product development within the industry. Yet, control valves play a vital role in automated process control and as such deserve more attention.
By Hans D. Baumann
However, there is a silver lining to every cloud. There are two areas of important advancements concerning control valves to upgrade such public understanding and, at the same time, improve the economic outlook of this industry.
First of all, there is the issue of improved valve selection. One can add value by informing a prospective valve customer in addition to proper sizing the expected sound and vibration levels under diverse operating conditions, and predicting the chances of cavitation1 in order to reduce future maintenance problems.
Also, tell the customer the expected gain of valve and positioner under various flow rates in order to help stabilize control loops. The estimating methods to predict sound level2, vibration3, and gain4 are known and published. All this information can be integrated in an advanced software package.
More efficient process
Secondly, there is the issue of saving energy, thereby reducing the carbon footprint of manufacturing processes. Saving pump horse power and compressor energy should be commendable efforts in this age of “green” living.
Bear in mind that all control functions of valves are essentially to modulate fluid flow. By utilizing the phenomena of pressure recovery, much potential energy (pressure) is saved from converting pressure drop, via turbulence, into heat. The big advantage of high recovery valves are, once choked flow is reached, then with a constant inlet pressure and a given valve travel, the flowing quantity remains constant regardless of down-stream pressure variations. This inherently makes for a constant flow regulator. Choked flow occurs if a pressure drop of (P1-Pv) x FL2 for liquids, and P1 x 0.5 x FL2 for gases is reached.
On an author designed HRV (see photo above), tests at the flow laboratories of the University of Utah confirmed that once low-pressure drop initiates choked flow, the flowing quantities of water remained exactly identical despite outlet pressures varying from 84 per cent of P1 down to atmospheric pressure. These results were also obtained at all different travel positions. During all tests, no cavitation noise was observed.
Limitations
This last requirement calls for the development of new types of control valves. The idea of utilizing pressure recovery is not new. It is practiced by controlling the flow of fuel gas in major gas turbine generators in power plants, saving up to 60 per cent of the pressure, which saves the equivalent BTU content and thus increases turbine efficiency.5 Special control valves used for this service are rather complicated and expensive. What is needed are more rugged valve types suitable for general industrial applications. Eccentric rotary ball valves have high recovery features, in and near wide open, capable of recovering up to 77 per cent of the pressure differential (FL = 0.48). Yet, they lose this advantage at lower travel positions where recovery rates are reduced to as low as 21 per cent (FL = 0.89). This limits their range of applications.
Typical application
To understand the advantages of such high-pressure recovery valves, here is a typical application for such a valve, called an HRV type. A centrifugal pump requires a constant liquid flow rate at a given head pressure to maintain its efficiency. Employing an ERV valve at the outlet of the pump can handle such needs.
Assuming again that such a valve has an FL factor of 0.48, all that is needed to provide a constant liquid flow from the pump is FL2 x P1 = 23 per cent of the absolute pump head pressure (psia).
It is thus apparent that the controlled flow rate is proportional to the pump head (pump outlet pressure). This relationship matches closely to the efficiency curve of a centrifugal pump (in itself an energy saver). Again, in comparison, using a conventional control valve having an FL factor of 0.75 would require a choking pressure drop across the valve of 56 per cent of the absolute pump head.
Severe cavitation
Such a high-pressure drop could cause severe cavitation. The ERV valve, in contrast, is immune from cavitation. In this case, the absence of pressure spikes, due to streamlined fluid flow, prevent implosions of vapor bubbles. The only external sound created is from turbulent flow inside the valve.
Again, using an ESV valve implies an energy saving of 59 per cent (23 per cent versus 59 per cent) compared to state-of-the-art valves.
The potential of energy savings by controlling the pressure of pumps is enormous. In a typical chemical plant, there are about 20,000 pumps, each consuming typically 3 kWh, making a yearly electric power consumption of 525 million kWh. Using the new valve concept offers an energy savings potential of up to 250 million kWh a year.
In an era, in which energy saving and equipment (pump!) protection have the potential to improve manufacturing processes and reduce energy consumption, control valves should get the attention they deserve.
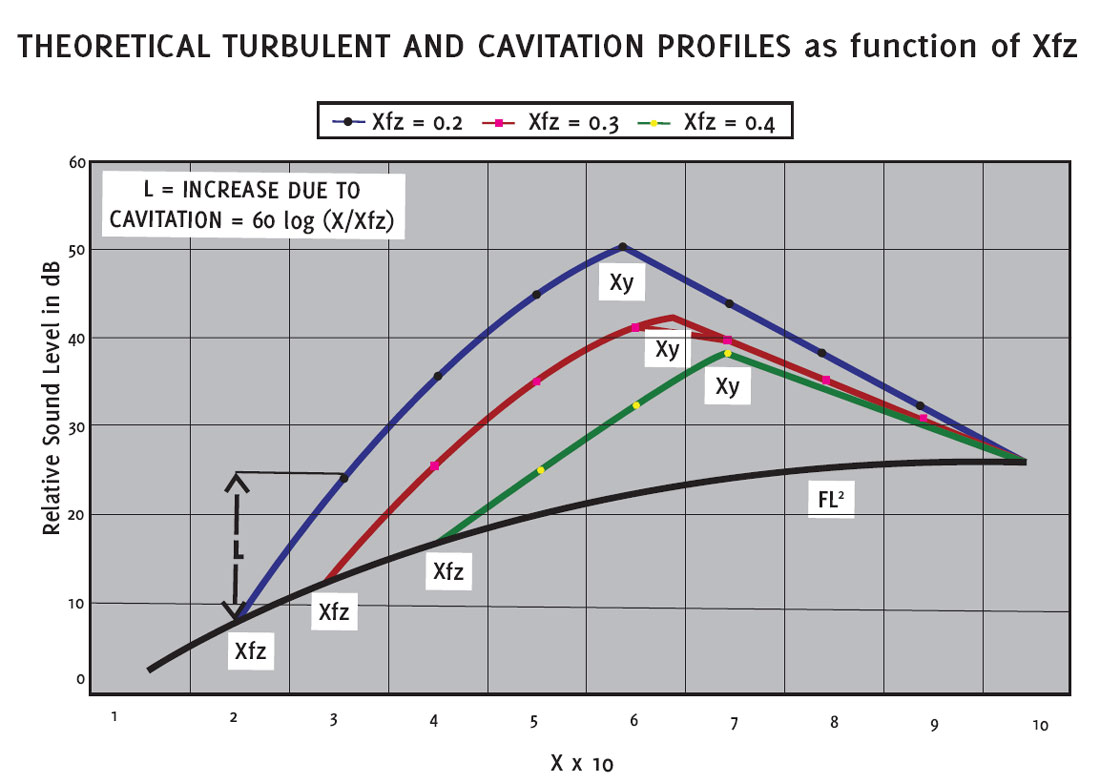
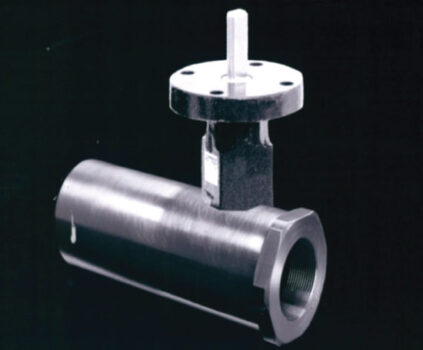
Additional note:
Choked flow occurs with gases once the orificial velocity reaches the speed of sound. Choked flow for liquids occurs when the orificial pressure caused partial evaporation of the liquids (without cavitation, vapor bubbles harmlessly dissolve further downstream).
About the Author
Dr. Baumann, a former VP of Masoneilan and Fisher Controls, is now an international consultant. He is credited with 106 US patents and has authored 140 publications and seven books, including the Control Valve Primer now in the fourth edition. Dr. Baumann is an Honorary Member of ISA and a Fellow Member of ASME. He can be reached at hdbaumann@phbinc.net
References:
1. Baumann, H.D. Control valve Noise estimating methods made easy, INTECH magazine July/August 2018, p. 43.
2. Baumann, H.D. Can sound damage pipes? Valve World magazine, Pp.74-75
3. Jon Monsen, Baumann, H.D. Stop cavitation from destroying your control valve trim Valve World magazine, December, 2019, Pp 61-63.
4. Jon Monsen, Calculating the installed flow and gain of a control valve, Plant Process Instrumentation, March 22, PP.26-30.
5. Baumann H. D. More efficient gas tur-bines: a role for high recovery valves. Valve World magazine April, 2021
About this Featured Story
This Featured Story is an article from our Valve World Magazine March 2022 issue. To read other featured stories and many more articles, subscribe to our print magazine.
“Every week we share a new Featured Story with our Valve World community. Join us and let’s share your Featured Story on Valve World online and in print.”