Matching materials to applications is critical for o-ring performance. Evaluating chemical resistance through immersion testing ensures fluid compatibility and proper seal material selection.
By Seema Gangatirkar, Greene Tweed
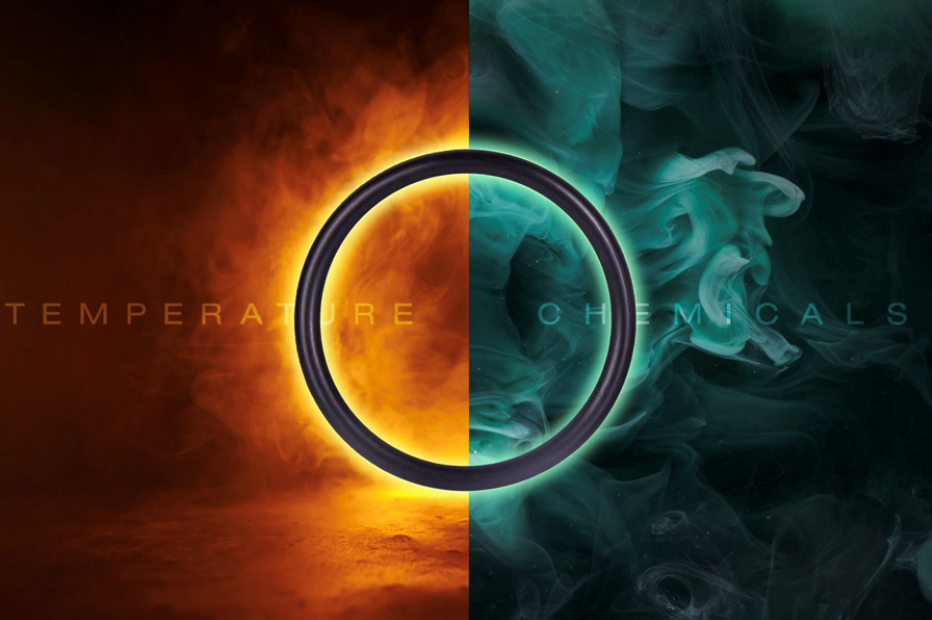
Matching the right elastomer to an application is key to ensuring an o-ring’s optimal performance and mitigating premature failure.
One critical factor to consider is resistance to process fluids. Different types of elastomers have differing resistance to various fluids, making material selection crucial to seal design. If the seal material is incompatible with a particular media, a seal could swell or experience other effects such as a change in hardness or deterioration of physical properties such as tensile strength and elongation, which could lead to a premature failure of the seal. Temperature also impacts the ability of an elastomer to resist chemical attack. As temperatures rise, it’s possible that an elastomer’s ability to maintain its properties within a process fluid may deteriorate. An elastomer that may exhibit excellent chemical resistance at a lower temperature may not perform as well at a higher temperature. So, it’s important to consider the effect of temperature when selecting a material to ensure that it can maintain its properties within the fluid.
Immersion tests
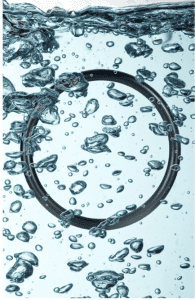
Immersion tests at specific temperatures and durations are used to evaluate how resistant a particular material is to a family of fluids.
An example test procedure to understand how a particular material performs in a hot water environment could be as follows:
Take the physical properties of a -214 o-ring and immerse it in distilled water at 250° F for three days. After retrieving from the vessel, o-ring measurements are taken to understand how the material has changed during its exposure to hot water. The change in the following properties is generally measured:
- Hardness
- Tensile strength
- Elongation
- Volume change
Assessing the chemical resistance
One convention of assessing the chemical resistance of an elastomer is to determine the percent volume change and then assign a rating based on that change. In this methodology, if the volume change is measured at 10 percent or less after exposure, the material is considered suitable for use in that fluid at that temperature. Volume swell measuring between 10 to 20 percent is generally suitable. A material measuring between 20 to 40 percent may still be suitable in certain situations but it is better to discuss with an applications engineer before selecting a material. An elastomer swelling of 40 percent or more would not be considered a good material candidate in that fluid Another method of determining chemical resistance takes the change in tensile strength into consideration in addition to volume swell.
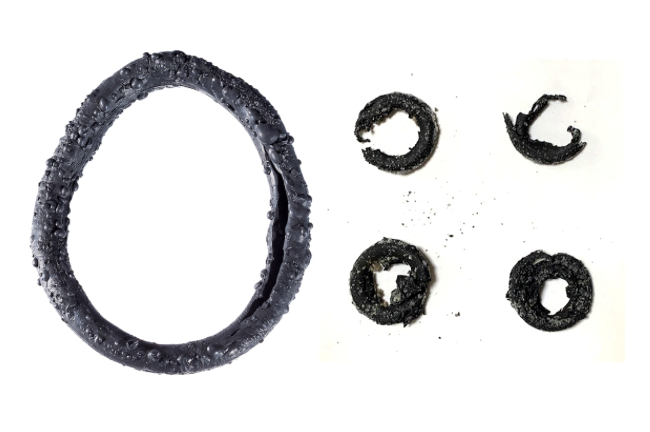
In this case, an elastomer with less than 15 percent volume swell and 15 percent change in tensile strength would be judged to have excellent compatibility with the fluid in which it was tested. Between 15 percent and 30 percent change in volume and tensile strength would indicate that the elastomer has experienced mild chemical reactivity with immersion fluid. Greater than 30 percent change in either volume or tensile would indicate that moderate chemical attack has occurred.
By reviewing the change in physical properties of an elastomer in specific process fluids, including the effect of temperatures, the right material can be recommended to ensure optimal seal performance.
About the author
Seema Gangatirkar manages Greene Tweed’s portfolio of FFKM sealing solutions built to outperform in the harshest environments in energy, chemical processing, life sciences, and aerospace industries. Leveraging her two decades of experience spanning product management, marketing, and market research, she has been instrumental in shaping product roadmaps driven by the voice of the customer.
About this Technical Story
This Technical Story is an article from our Valve World Magazine, May 2024 issue. To read other featured stories and many more articles, subscribe to our print magazine. Available in both print and digital formats. DIGITAL MAGAZINE SUBSCRIPTIONS ARE NOW FREE.
“Every week we share a new Technical Story with our Valve World community. Join us and let’s share your Technical Story on Valve World online and in print.”