Valve packing solutions have their drawbacks, like a low recovery rate. ProPack proposes new options to solve those problems.
Text and images by Propack
Today, valve packing is made primarily from PTFE- or expanded graphite yarn. PTFE packing is either braided from sintered sPTFE tape, which is mechanically combed to increase the surface area, or as well from expanded ePTFE yarns. Both materials are characterised by high sealing performance, exceptional chemical resistance and low coefficients of friction. However, its disadvantages are also well-known: low recovery rate and strong tendency to gap extrusion. Equally negative is a multiple thermal expansion value in relation to the body, stem and bolt materials of the valve. When the temperature fluctuates in the stuffing box, it changes the applied compression of the packing through the gland follower. It results in an overload on heating cycle, which can lead to extrusion, and to a decrease in compression on a cooling cycle, which can lead to leakage. Whereas the first phenomenon is irreversible, because the packing, once extruded, will not return to the stuffing box. Leakage can increase in cold applications. If the packing expands again when warmed up, it can be sealing again at room temperature.
Graphite rings
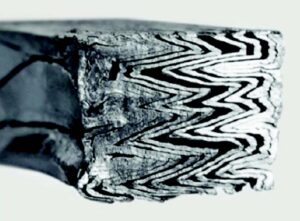
Expanded graphite is also frequently used to seal valves. For this purpose, a graphite foil is produced from graphite flakes in a calandering process. In a next step, this foil is cut into strips of a specific width and length, wound axially and compressed into rings in a compression mold. The delivery form is an endless ring, which must be assembled directly over the valve stem.
Since there are usually no reinforcements built into the cross-section, the graphite ring is largely unprotected against extrusion and blowout and requires minimum gap widths and precise gland surfaces. The sealability is low, which is illustrated at the cross-section picture. Dismantling of the soft material is difficult because, as mentioned, the ring is typically manufactured with no integrated reinforcement and it is also very brittle in its structure.
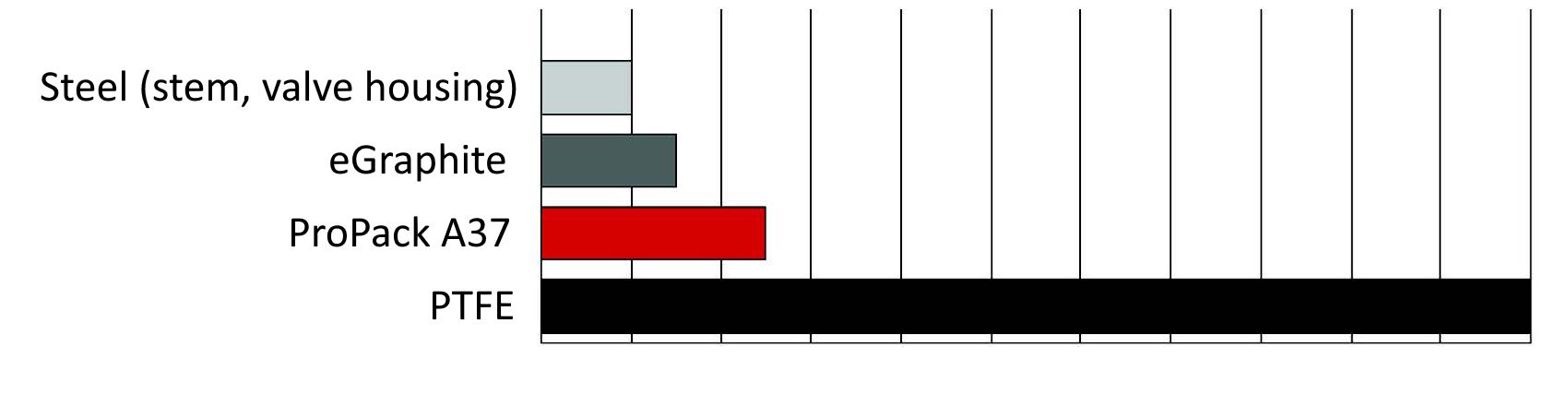
Braided packing
Expanded graphite is also processed into a yarn for braided packing. The yarn must have reinforcing threads of cotton, glass, carbon fibers or thin Inconel wires. Packing is produced from these graphite yarns in common cross-sections and sold as coil or spool. It is also supplied pre-compressed, as a ready-to-install packing ring, with a skive cut for easier assembly.
Expanded graphite has a coefficient of thermal expansion close to that of stuffing box materials. The material has almost similar chemical resistance to PTFE. The elasticity and resilience of this material is excellent.
The extrusion strength of braided eGraphite packing depends on the reinforcing material. Cotton reinforcement for example on the graphite tape makes the yarn processible on the braiding machines. The cotton is eliminated with a considerable loss of volume when the packing is installed and subjected to thermal or chemical stress. The most suitable material for extrusion protection and blow out is a fine Inconel wire matrix, which closely surrounds the expanded graphite yarn and embeds itself in the soft graphite.
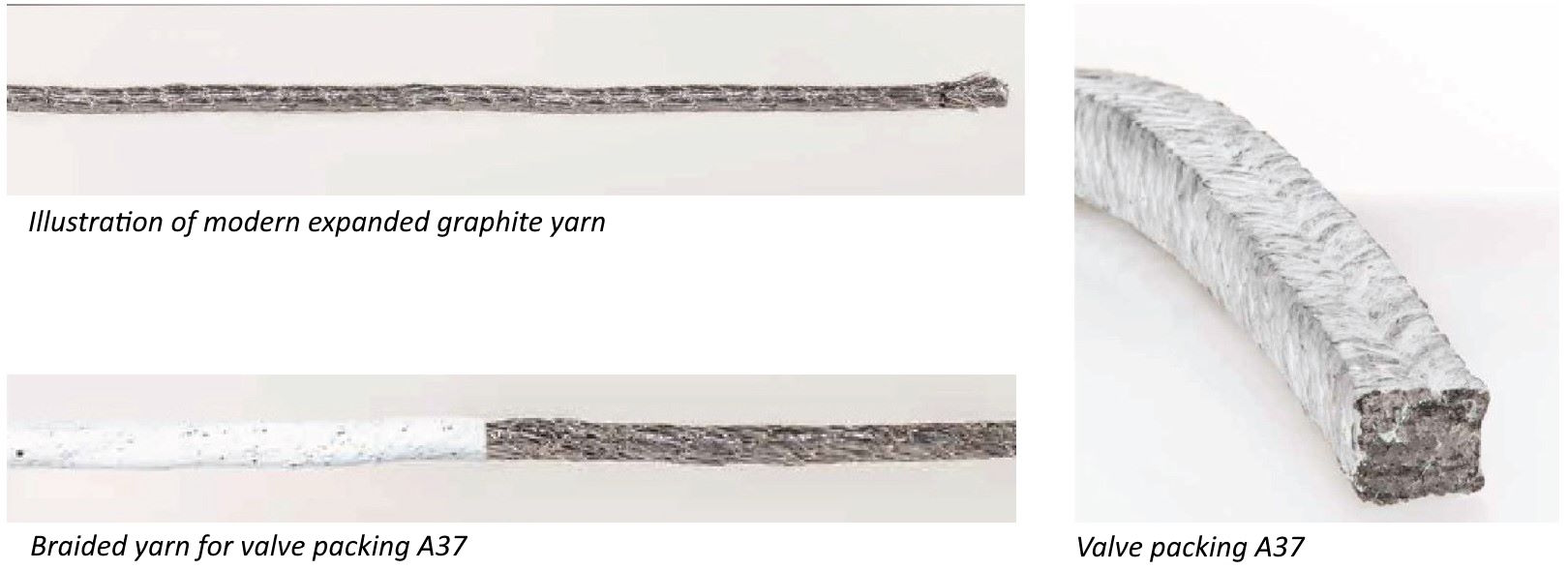
Benefits
Packing type A37 combines the advantages of both materials. The basis for the braided yarn is a thin, round-shaped, expanded graphite strand, extrusion-protected by an Inconel matrix. PTFE impregnation and additional PTFE film wrap around the yarn increase the sealability and reduce the coefficient of friction.
The combination of both materials results in a packing that seals excellently in cryogenic temperatures as well as temperatures at the limit of PTFE. Emission tests according to VDI 2440 and under temperature cycles according to EN15848 have confirmed this. The PTFE content reduces the friction coefficient of graphite, prevents the undesirable slip-stick effect and increases sealability. A high graphite content contributes to neutral thermal behavior. Likewise, graphite remains flexible and does not harden. As a result, the packing remains adjustable with low gland force over its service life.