Hydrogen pipeline.
Discover how innovative valve technologies are revolutionizing the hydrogen economy, enabling the safe and efficient transportation, storage, and utilization of this clean energy carrier. Learn how these cutting-edge solutions are playing a crucial role in reducing emissions.
By Melonie Dodaro, Valve World
Hydrogen, boasting zero carbon emissions at the point of use and a high energy density by weight, has positioned itself as a leading contender in the pursuit of clean energy solutions. Its diverse applications range across various sectors, including fuel cells for transportation, electricity generation, and industrial processes.
However, realizing the full potential of hydrogen necessitates the development of a robust infrastructure for its production, transportation, and utilization. This network relies on a crucial component: valves. These seemingly simple devices play an essential role in ensuring controlled flow and preventing fugitive emissions, acting as the gatekeepers of the hydrogen economy.
This article explores the technical considerations surrounding valves in hydrogen applications. We will examine the unique challenges they face, including susceptibility to hydrogen embrittlement and the paramount importance of leak prevention. Furthermore, we will examine the cutting-edge advancements in valve technology specifically designed to address the demands of hydrogen applications. By critically evaluating both the obstacles and the opportunities, we can ensure that valves continue to play their vital role in facilitating a clean energy future powered by hydrogen.
Hydrogen: A clean energy carrier
Hydrogen is rapidly gaining traction as a clean energy carrier due to its inherent properties. Unlike fossil fuels, hydrogen combusts cleanly, producing only water vapor as a byproduct. This translates to zero carbon emissions at the point of use, making it a highly attractive option in the fight against climate change. Furthermore, hydrogen boasts a remarkable energy density by weight, surpassing even gasoline. While its volumetric energy density is lower, advancements in storage technologies are continuously mitigating this limitation.
- Advantages and limitations of production methods: There are several established methods for hydrogen production, each with its own advantages and drawbacks. One prominent method is electrolysis, where electrical current splits water molecules into hydrogen and oxygen. The cleanliness of this process hinges entirely on the source of the electricity. If generated from renewable sources like solar or wind, electrolysis becomes a truly sustainable option. Another established method is steam methane reforming (SMR), where natural gas reacts with high-temperature steam to produce hydrogen and carbon dioxide. SMR is a mature technology with a readily available feedstock (natural gas). However, the process itself generates Scope 2 greenhouse gas emissions, negating some of the environmental benefits of using hydrogen. Technological advancements like carbon capture and storage (CCS) can be integrated with SMR to mitigate these emissions, but this adds significant complexity and cost.
- Diverse applications: Beyond production, hydrogen offers a wide range of potential applications. In the transportation sector, hydrogen fuel cells are a promising alternative to internal combustion engines. Fuel cells combine hydrogen and oxygen to produce electricity, powering the vehicle with zero tailpipe emissions. Hydrogen can also be used in stationary applications for power generation, particularly when paired with renewable energy sources like solar or wind. Here, hydrogen acts as a form of energy storage, providing a buffer for times of low renewable energy production. Additionally, hydrogen has established applications in various industrial processes, such as steel production and ammonia synthesis. In these applications, hydrogen can help to decarbonize industries that are traditionally reliant on fossil fuels.
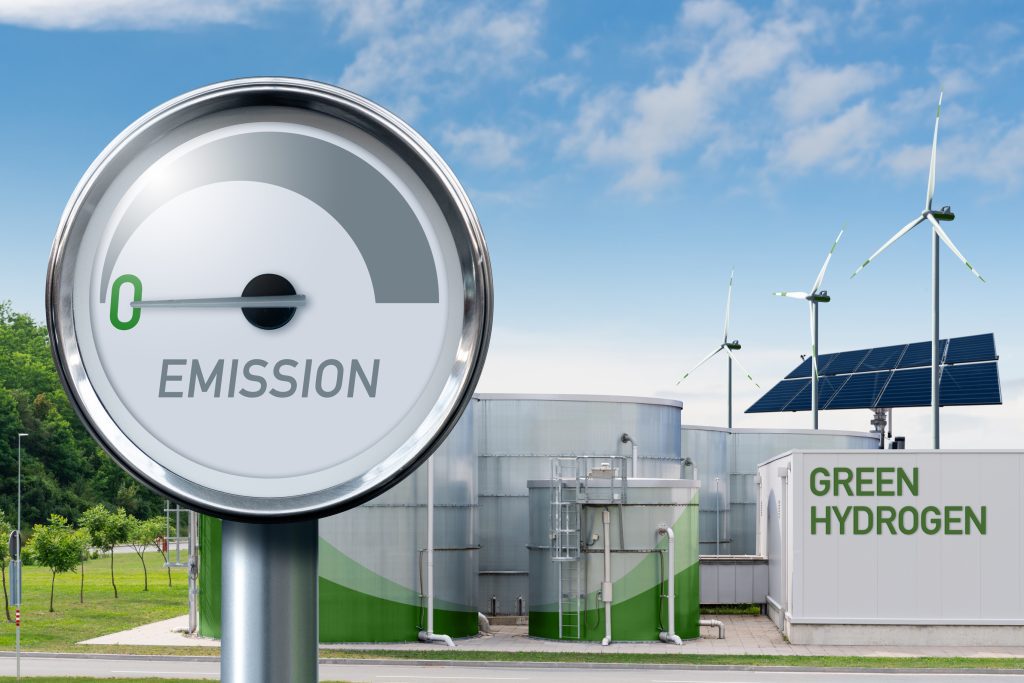
Unique challenges of hydrogen for valves
While hydrogen offers a promising path towards a clean energy future, it presents unique challenges for valves compared to traditional fluids, necessitating careful consideration of material selection, design features, and operational practices.
- Hydrogen embrittlement: One of the most significant concerns is hydrogen embrittlement. This phenomenon occurs when atomic hydrogen diffuses into the metal lattice of a valve component, weakening the material and increasing its susceptibility to cracks and fractures. Over time, this can lead to catastrophic valve failure, resulting in loss of containment and release of hydrogen under pressure. The risk of embrittlement varies depending on the specific material, its microstructure, and the pressure and temperature of the hydrogen gas being contained in the valve/pipeline. Stainless steels, a common choice for valves in many applications, are particularly susceptible to hydrogen embrittlement. To mitigate this risk, valve manufacturers are exploring alternative materials like nickel alloys (e.g., Monel, Inconel) and special high-purity steels with enhanced resistance to hydrogen diffusion.
- Minimizing leakage: Another critical challenge is the minimization of fugitive emissions. Due to its small molecular size and high diffusivity, hydrogen gas can readily leak through even the smallest clearances. These leaks not only represent a loss of valuable energy but also pose a potentially major safety hazard. To combat this, valve designs for hydrogen applications often incorporate features like metal bellows or diaphragm seals, which minimize the potential leakage paths. Furthermore, advanced gland packing materials specifically designed for hydrogen compatibility, such as graphite-based or PTFE-based materials, are being developed to optimize leak tightness. Leak detection methods are crucial in hydrogen applications. Traditional methods like soap bubble testing are ineffective with hydrogen due to its low viscosity. Alternative methods, such as acoustic emission testing and tracer gas surveys, are becoming increasingly important for identifying and quantifying leaks in hydrogen valve systems.
-
Designing for a flammable gas: Hydrogen gas is highly flammable and explosive when mixed with air in specific concentrations. This necessitates a rigorous approach to safety considerations in valve design, material selection, and operation. Valves for hydrogen applications are often designed to minimize potential ignition sources by employing features like spark-resistant materials (e.g., beryllium copper, aluminum bronze) and avoiding components and materials which are prone to frictional heating.
- Material selection: Choosing the right material for hydrogen valves requires a balance of several key properties. Resistance to hydrogen embrittlement is paramount, as discussed earlier. However, the material must also possess adequate strength and mechanical properties to handle the pressures and stresses encountered in different hydrogen applications. For instance, valves used in high-pressure hydrogen storage require materials with exceptional strength and fatigue resistance, such as high-strength stainless steels (e.g., 316L, 347), nickel alloys (e.g., Monel, Inconel), or titanium alloys. Furthermore, special considerations need to be taken for sealing mechanisms at high pressures. Traditional packing materials may not be suitable due to increased wear and tear. Alternative sealing technologies, such as metal-to-metal seals or self-energizing designs, are being explored to meet the demands of high-pressure hydrogen applications. Corrosion resistance is another important consideration. The specific choice of material may depend on the presence of impurities or contaminants within the hydrogen stream, as these can accelerate corrosion. For example, in applications where hydrogen is produced from steam methane reforming, the presence of sulfur compounds may necessitate the use of more corrosion-resistant materials like stainless steels or nickel alloys. The operating temperature can influence material selection, as some materials exhibit superior properties at specific temperature ranges.
- High-pressure hydrogen: The trend towards utilizing high-pressure hydrogen for transportation and storage presents additional challenges for valves. High-pressure operation necessitates robust valve designs that can withstand significant forces without compromising leak tightness. Valve bodies and components require careful engineering to ensure they possess the necessary strength and dimensional stability under high-pressure conditions.
Innovative valve technologies for hydrogen applications
As the hydrogen economy grows, valve manufacturers are developing innovative technologies specifically designed to address the unique requirements of hydrogen applications. These advancements mitigate the risks associated with hydrogen’s properties while enhancing operational efficiency, safety, and reliability.
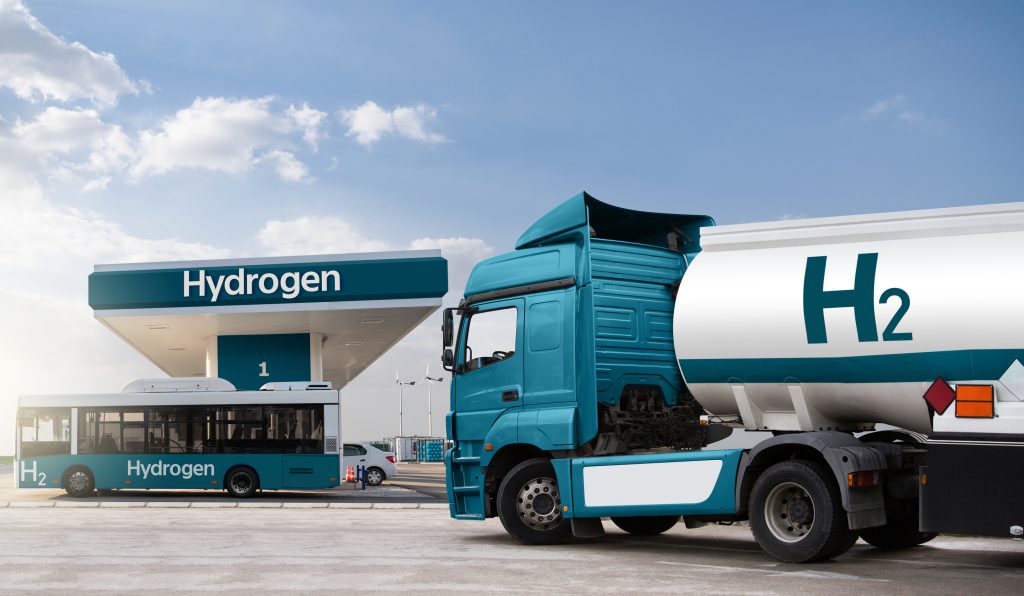
Metal bellows valves: Metal bellows valves are emerging as a preferred choice for hydrogen applications due to their inherent resistance to hydrogen embrittlement. The bellows, a flexible, corrugated metallic element, isolates the valve stem from the hydrogen stream, eliminating a potential pathway for hydrogen diffusion into critical valve components. This significantly reduces the risk of embrittlement and ensures long-term valve integrity.
Metal bellows valves also excel in minimizing leakage potential. The bellows design inherently provides a leak-tight seal, further enhanced by welding the bellows directly to the valve body. This eliminates the need for traditional packing materials, which can be prone to wear and leakage over time. Examples of metal bellows valves are being employed in various hydrogen applications, including hydrogen fueling stations and high-pressure hydrogen pipelines.
Diaphragm valves: Diaphragm valves offer another compelling solution for hydrogen applications. These valves utilize a flexible diaphragm to isolate the process fluid from the valve bonnet. This inherent design feature minimizes potential leakage paths and makes diaphragm valves well-suited for applications demanding high leak tightness. Furthermore, the diaphragm material can be specifically selected for hydrogen compatibility, ensuring long-term performance.
Diaphragm valves are finding application in various segments of the hydrogen economy. They are a popular choice for isolating hydrogen purification units and for controlling hydrogen flow in fuel cell systems. Their inherent fluid containment design makes them ideal for applications where fugitive emissions are a critical concern.
Specialty coatings & materials: Material science advancements are playing a crucial role in developing valves for hydrogen applications. Specialty coatings, applied to valve components, can significantly enhance resistance to hydrogen embrittlement. These coatings can be engineered to create a barrier that hinders hydrogen diffusion into the base metal, thereby preserving valve integrity. Material innovation is also at the forefront. New high-strength alloys and special grades of stainless steel are being developed specifically for hydrogen compatibility. These materials offer superior resistance to embrittlement while maintaining the necessary mechanical properties for demanding hydrogen applications.
Smart valve technologies: The integration of sensors and actuators into valves is ushering in an era of “smart” valve technology for hydrogen applications. These smart valves can collect real-time data on operating parameters like pressure, temperature, and flow rate. This data can be leveraged in several ways to enhance efficiency and safety:
- Predictive maintenance: By continuously monitoring and analyzing valve performance data, operators can identify potential issues before they lead to in-service failures. This data can be used to guide proactive maintenance, leading to reduced downtime and valve life extension. For example, changes in valve signature (e.g., increased vibration or changes in opening/closing times) can indicate component or seal wear or a developing failure mechanism, allowing for a timely and focused maintenance intervention.
- Leak detection: Smart valves equipped with acoustic emission sensors or other leak detection technologies can quickly identify and localize leaks. This early detection capability is crucial in hydrogen applications, where leaks pose significantly higher safety risks. By pinpointing the exact source of a leak, operators can take swift corrective action, minimizing potential hazards and potentially reducing maintenance costs.
- Performance optimization: The real-time data collected by smart valves enables operators to optimize system performance continuously. For instance, by monitoring flow rates and pressures, operators can adjust valve settings to maintain optimal operating conditions, improving efficiency and reducing energy consumption. This data-driven approach to valve control can yield significant benefits in large-scale hydrogen production and distribution networks.
Smart valve technology represents a significant step towards enhanced safety, operational efficiency, and overall system reliability in hydrogen applications. As the hydrogen economy expands, the adoption of smart valves is expected to grow, driving further innovation in this field.
Case studies: Valve technology in action
To better understand the practical applications of valve technology in the hydrogen economy, let’s explore real-world case studies that showcase the implementation of various valve solutions across the hydrogen value chain.
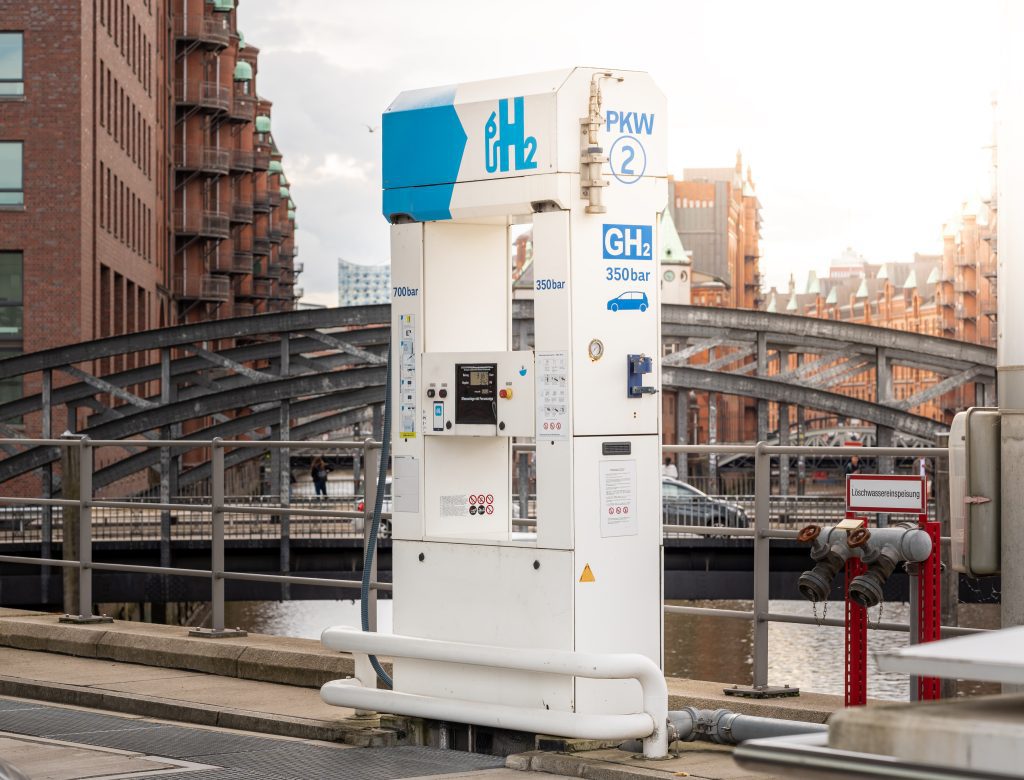
1. Hydrogen fueling stations: Ensuring safe and efficient refueling
Hydrogen fueling stations are critical infrastructure components that enable the widespread adoption of fuel cell vehicles. These stations rely on high-performance valves to ensure safe and efficient hydrogen dispensing. One notable example is the use of metal bellows valves in the high-pressure hydrogen storage and dispensing systems.
At a hydrogen fueling station in California, metal bellows valves were installed in the high-pressure storage tanks and dispensing lines. These valves, designed specifically for hydrogen service, provided leak-tight sealing and superior resistance to hydrogen embrittlement. The metal bellows design eliminated the need for traditional packing materials, reducing maintenance requirements and ensuring long-term performance. The use of metal bellows valves in this fueling station demonstrated their effectiveness in ensuring safe and reliable hydrogen dispensing. The valves performed flawlessly, with no reported leaks or failures, contributing to the station’s overall operational efficiency and customer satisfaction.
2. Hydrogen pipelines: Enabling long-distance transportation
Hydrogen pipelines are essential for transporting large volumes of hydrogen over long distances. These pipelines require valves that can handle high pressures and ensure leak-tight operation. A recent project in Europe showcased the application of specialty coated valves in a newly constructed hydrogen pipeline.
The pipeline, spanning over 100 kilometers, connected a large-scale hydrogen production facility to industrial end-users. The valves used in this pipeline were coated with a proprietary material that provided enhanced resistance to hydrogen embrittlement. The coating acted as a barrier, preventing hydrogen diffusion into the valve body and components. The coated valves performed exceptionally well throughout the pipeline’s operation. Regular inspections and maintenance checks revealed no signs of embrittlement or degradation, validating the effectiveness of the specialty coating. The leak-tight performance of the valves ensured the safe and efficient transportation of hydrogen, with minimal losses and no safety incidents.
3. Fuel cell power systems: Reliable flow control
Fuel cell power systems, used in stationary and mobile applications, rely on valves to control the flow of hydrogen and other gases. In a recent project, a fuel cell manufacturer integrated smart valve technology into their power systems to optimize performance and enhance safety.
The smart valves, equipped with sensors and actuators, provided real-time monitoring of flow rates, pressures, and temperatures. This data was used to continuously adjust valve settings, ensuring optimal operating conditions for the fuel cell stacks. The smart valves also incorporated leak detection capabilities, enabling quick identification and localization of any potential leaks.
The integration of smart valves in the fuel cell power systems yielded significant benefits. The real-time monitoring and control capabilities allowed for improved efficiency and extended fuel cell life. The leak detection features enhanced safety, minimizing the risk of hydrogen leaks and associated hazards. Overall, the smart valve technology demonstrated its value in ensuring reliable and efficient operation of fuel cell power systems.
Conclusion
The rise of hydrogen as a clean energy carrier presents both challenges and opportunities for valve technology. Hydrogen’s unique properties, such as low molecular size and susceptibility to embrittlement, necessitate careful consideration of material selection, design features, and operational practices, with leakage prevention and safety being paramount.
However, these challenges are being met head-on with the development of innovative valve technologies. Metal bellows valves, diaphragm valves, and specialty coatings are pushing the boundaries of performance and reliability in hydrogen applications. The integration of sensors and actuators into “smart” valves is further enhancing safety, efficiency, and predictive maintenance capabilities.
References
- White & Case LLP article: https://www.whitecase.com/insight-alert/hydrogen-economy-case-study
- Sheffield Hallam University report: https://www.shu.ac.uk/-/media/home/research/cresr/reports/u/uk-hydrogen-economy.pdf
- Senior Metal Bellows case studies: https://www.metalbellows.com/case-studies/
- MDPI article on hydrogen economy research: https://www.mdpi.com/2076-3298/10/1/11
About this Featured Story
This Featured Story is an article from our Valve World Magazine, June 2024 issue. To read other featured stories and many more articles, subscribe to our print magazine. Available in both print and digital formats. DIGITAL MAGAZINE SUBSCRIPTIONS ARE NOW FREE.
“Every week we share a new Featured Story with our Valve World community. Join us and let’s share your Featured Story on Valve World online and in print.”