Storage and transportation of hydrogen in liquid state offers several advantages. Liquid hydrogen (LH₂) has a higher density and requires a lower storage pressure compared to gaseous hydrogen. However, hydrogen turns into liquid at -253°C, which brings its own challenges. The very low temperature as well as the risk of flammability make it a challenging medium. Stringent safety measures and reliability are thus a must when designing valves for this application.
By Fadila Khelfaoui and Frédéric Blanquet, Velan
LH₂ applications
Currently, LH₂ is being used and explored in various special applications. The aerospace industry uses it for rocket launching and transonic wind tunnels. Under the umbrella of big science, LH₂ is essential in superconductivity applications, particle accelerators and nuclear fusion.
Recently, with increasing demand for sustainability, LH₂ has become of interest as a source of fuel for heavier trucks and ships. Valves play an important role in the successful operation of these applications. Reliable and safe operation of valves that form part of the LH₂ supply chain ecosystem (production, transport, storage, and distribution) is a necessity.
Working with LH₂ is not easy. There are numerous challenges associated with it. Leveraging 30 years of field experience and technical expertise in supplying high performance valves down to -272°C, Velan has been involved in pioneering projects and is unequivocally well positioned to meet the LH₂ challenges.
Design challenges
Pressure, temperature, and hydrogen concentration are the primary factors when determining valve design risk assessment. For optimum valve performance, design features and material selection are of utmost importance. There are challenges to be overcome when handling LH₂.
One such challenge is the deleterious effect of hydrogen on metallic materials. Combined with the very low temperature, valve materials need not only to withstand the attack of hydrogen molecules (some degradation mechanisms are still a subject of debate in the scientific community) but must also be able to perform at that temperature for a long service life. The current knowledge of non-metallic material compatibility with hydrogen is still limited. This gap in knowledge must be taken into consideration when selecting sealing materials.
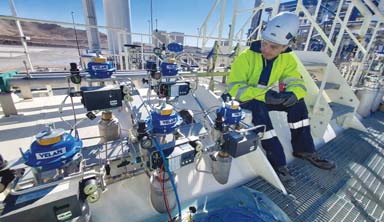
Tight sealing is another key design performance criterion. Under thermal gradients resulting from temperature differentials of up to 300°C between the LH₂ and the surrounding environment (at room temperature), different valve components expand and contract by varying amounts. This discrepancy can result in detrimental leakage of critical sealing surfaces. Sealing tightness at the stem is another design consideration. The transition from cold to warm generates a heat flow. Ice may form in the warmer section of the bonnet cavity, compromising the stem sealant and thus the operability of the valve.
The -253°C temperature demands optimal insulation technology for the valves to maintain LH₂ at this temperature and minimize hydrogen losses via boil-off. Any heat transfer to the liquid causes hydrogen to evaporate and leak. Furthermore, a break in the insulation causes oxygen condensation. Any contact between oxygen and hydrogen or other combustible material will increase the likelihood of fire hazard. Therefore, when considering the susceptibility of valves to the risk of fire, the valve design must be explosion-proof and include a fireproof actuator, instruments, and wiring, in conformance with the most stringent certifications. This will ensure that the valve will function safely during a fire.
Pressure buildup is another potential issue that may render the valve inoperable. The accumulation may occur when liquid is trapped in the valve cavity, and under certain conditions of heat transfer and vapor formation. In the case of high differential pressure, cavitation and/or noise can occur, which will damage the valve prematurely and result in unacceptable process failures.
By considering these aspects regardless of the process conditions, appropriate design features are integrated into the design process, thus providing a safe and reliable operation. Other key design challenges are related to environmental issues such as fugitive emissions. Hydrogen has unique characteristics: small molecular size being colorless, odorless, and explosive. These characteristics make zero leakage an absolute necessity.
Valve solutions
Regardless of their functionality or type, all valves in LH₂ service must meet certain common requirements. These include the use of appropriate construction materials that ensure structural integrity at very low temperatures, as well as materials that are inherently fire safe. Similarly, the sealing and packing materials used in these valves must also meet these basic requirements.
Austenitic stainless steel is a preferred material for LH₂ valves. It offers excellent impact strength, minimal heat loss, and can handle steep temperature gradients. Other materials are also available that are compatible with hydrogen but depend on the process conditions.
Besides the choice of materials, other design details such as extending the stem with a gas column protect the sealing packing from the effects of extremely low temperature. In addition, the stem extension can be supplemented with a thermal collar to avoid condensation in the insulated area. Unique features tailored to each valve design offer enhanced technical solutions to different challenges.
Butterfly valves
Velan provides two different designs of butterfly valve: double- and triple-offset metal seated valves. Both designs provide bi-directional flow capabilities. They are designed with disc rotation geometries to ensure tight shut-off sealing. Trapped cavities are eliminated. In the double offset, an exceptionally tight shut-off is achieved with eccentric disc rotation combined with a unique sealing system, VELFLEX. This patent technology overcomes even high temperature fluctuations.
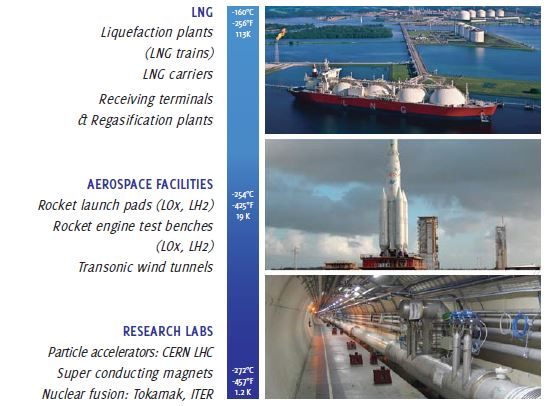
The triple-offset disc rotation geometry, TORQSEAL, ensures that the disc seal contacts the body seat only at the final shut-off position without rubbing or galling, providing a torque-generated resilient seat with sufficient wedging effect to ensure a uniform seal contact around the entire circumference of the valve seat when the valve is closed. The resiliency of the seal allows self-adjusting of the valve body and disc to prevent the risk of jamming during temperature transients.
A reinforced stainless-steel shaft is furnished for high cycles and smooth operation at very low temperature. The VELFLEX double offset valve design allows for easy and quick in-line maintenance. Thanks to the side cover, free access to the seat and disc for inspection or maintenance is possible without disassembly of actuators, and no special tools are required.
Control valves
Velan has a quite unique portfolio of control valves for low-temperature applications designed for temperatures down to -272°C and working pressures up to PN70. The valves used are bellows seal globe control valves, with angle and/or straight patterns. Proprietary design features and material are developed for reliable and safe operation. Valves can be fitted with a tight double shell or jacket enabling vacuum insulation. Valves are manually or pneumatically operated, depending on the on-site applications.
Safety relief valves
The safety relief valves are specially designed for overpressure protection of liquefied helium lines in superconductivity applications. This is achieved by a magnetic safety device developed specifically to protect containers and pressure shells against overpressure of compressed fluids at ambient temperature or during a very low temperature discharge. In the event of a local temperature increase, called ‘quench’, the valve opens in less than 80 ms. Initially supplied for liquefied helium, it can be adapted to hydrogen applications.
Qualification and approval
Tests are performed in accordance with the most stringent customer requirements. Protection against explosion is required in conformance with ATEX, KOSHA, NAMUR standards as per the applicable legislations. Some customers require local certifications, such as KGS in Korea, or NK in Japan. Today, there is still no specific standard for valves in hydrogen service. Working groups to define this standardization are being set up to accelerate the deployment of ‘green’ hydrogen on a commercial scale. TÜV has issued a standard, but no customer is implementing it yet.
Field experience
In the past, Velan has supplied control valves for hydrogen liquefaction plants in the USA (Westcoast project, North Las Vegas) and in South Korea (SK project, Ulsan) and is currently manufacturing valves for the Woodside project (Ardmore, Oklahoma). In the field of aerospace, Velan has supplied butterfly valves for the launch pad of Ariane rockets in Kourou (French Guiana) and control valves for the Indian space program.
Future of LH₂
Currently, LH₂ is gaining popularity as a clean fuel and a sustainable form of energy. Although it holds much promise, the deployment of LH₂ on a large scale worldwide is still a challenge. With proven engineering expertise and hydrogen field experience, Velan is ready to be a part of the solution.
About the author
Fadila Khelfaoui is a professional engineer with 25 years of combined experience in materials engineering and coatings. She joined Velan Canada in 2016 as Corporate Engineer, Metallurgy. She holds a Ph.D. degree in materials science and engineering and is a registered Professional Engineer in Quebec.
Frédéric Blanquet has 34 years of experience in the valve industry. He has been responsible for cryogenic market at Velan France for the past 19 years.