Design validation testing is a means to ensure that industrial valves perform within their design range. They are tested to see if they can withstand the pressure and temperature that they’re intended to endure. A specific standard that valves can be tested for is ISO 23632.
Luc Vernhes, Velan & Colin Zegers, ITIS
ISO 23632 is a standard first issued in 2021 that covers the design validation testing (DVT) of industrial valves. The purpose of these tests is to evaluate the valve’s operating and sealing performance within the design range determined by the full pressure/temperature envelope of the valve. Large oil and gas companies have been using DVT for a long time to limit the risk of field service issues caused by unproven products, and to improve overall plant performance and safety.
Surprisingly, approximately 60 percent of industrial valves, despite meeting conventional design standards, do not meet the requirements of DVT. As a result, some of these valves fail when exposed to field conditions, such as pressure, temperature, and operational cycles, rendering them unsuitable for their intended purpose. ISO 23632 provides a comprehensive framework for end users, manufacturers, and testing laboratories to perform DVT and ensure that industrial valves meet the necessary safety and performance requirements before reaching the field.
DVT is essential for ensuring that industrial valves are safe, reliable, and efficient in their operation. In this paper, we will present technical requirements of the ISO 23632 standard, where the industry stands with respect to adopting it, and finally, connecting the standard to a much larger initiative to limit environmental impact by key stakeholders.
Technical summary
ISO 23632 sets out the requirements and criteria for the use of metallic butterfly and ball valves in all industrial applications. The standard validates the design of the product by subjecting it to 205 cycles at the designated conditions. The test sequence is similar to ISO 15848-1, which enables the use of existing cycling stations developed globally for fugitive emission qualification and offers both mechanical and thermal cycles.
The new standard evaluates torque measurement against differential pressure to ensure it does not exceed the torque values published by the manufacturer, seat leakage to verify compliance with targeted leakage rate based on ISO 5208 with air, and maximum allowable stem torque validations. The purpose of the test is to confirm that the valve performs as expected when operated within the manufacturer’s designated pressure/temperature rating, as provided in the product’s technical documentation.
It verifies torque requirements and maximum allowable stem torque, and the durability of seat performance and operating torque through mechanical and thermal cycles. ISO 23632 also includes rules for extending qualification to untested size and pressure designation of valves within the same product range.
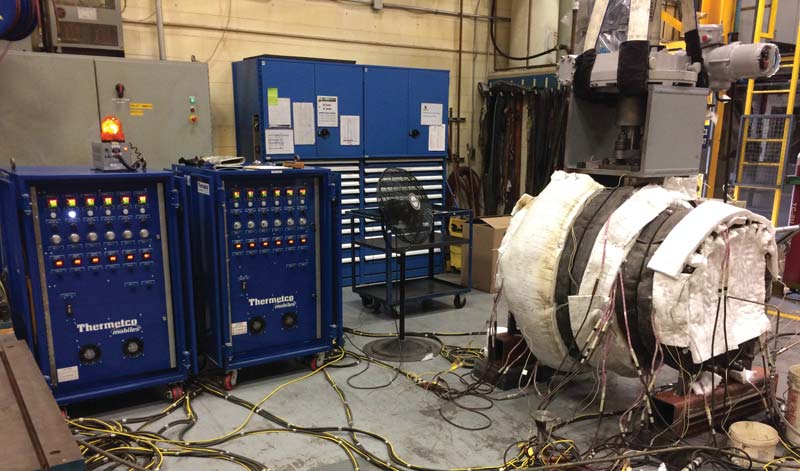
Adoption by the industry
Since ISO 23632 is a newly published standard, it has not been widely adopted by the industry at this time. However, based on past experience with ISO 15848, it is common for the implementation of new ISO standards to require a significant amount of time before widespread adoption. Despite this, the adoption of ISO 23632 is expected to bring benefits such as improved safety and performance, as well as reduced environmental impact, which will incentivise the industry to adopt the standard sooner rather than later.
The increased demand for severe service valves required to realise the full potential of alternative energy sources such as hydrogen, geothermal and thermal solar, or to improve overall efficiencies of conventional energy sources, drives the development of custom valve design, tailored for these new processes. These special valves are good candidates for DVT since they largely have not been field tested.
On the other hand, because there is an increasing demand on procurement to diversify sources due to the turbulence experienced in recent years, the need to qualify new suppliers can also serve as a driver for DVT. This is why one of the largest oil and gas companies now includes ISO 23632 in their specifications and has ordered ITIS to test several valves accordingly.
Shell DVT SPE 77/300
Shell has required DVT for a long time. According to their proprietary standard, a DVT should include a performance test at ambient, at maximum and at minimum design temperature at both a low and high pressure. The detailed test requirements and procedure are in accordance with SPE 77/300. This procedure only evaluates the manufacturing location or plant where the valves are made. Therefore, even if a manufacturer produces identical valves elsewhere, these other locations or plants will require independent qualification in accordance with this procedure.
Changes to any item will not void the qualification for which the DVT procedure was intended, provided that the manufacturer notifies Shell and complies with any additional requirements Shell may specify. Shell has the right to request a re-test when the qualification of valves has been voided. The re-test shall be subject to exactly the same requirements as specified. Unless agreed otherwise, the re-test shall take place at the same testing facility, where the previous test was carried out. Shell is now considering adopting the ISO 23632 standard, instead of their proprietary Shell DVT SPE 77/300, for its internationally recognised status and cost-effectiveness, as well as its auditable and standardised testing protocol, which aligns with industry best practices.
ITIS’ DVT experiences
For a DVT, the manufacturer is expected to have sufficient stock from which a random sampling of their valve products, and shell materials to be qualified, may be selected. After completion of all the tests, the valve shall be disassembled in a clean, dust-free environment. The valve body and all internals, specifically the stem, packing, seat(s), seals, bearings and obturator, shall be checked for (excessive) wear and damage. Post-test condition photographs are then made and included in the report.
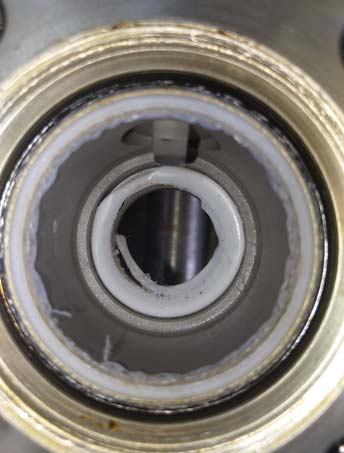
For about ten years, other major asset owners in the oil and gas industry have been requesting DVTs which are more or less the same requirements as SPE 77/300. During DVT testing performed at ITIS, we have even seen problems with valves tested at the same practical conditions for pressure and temperature. As already mentioned, over 60% of industrial valves fail the test for one of more reasons, despite conforming to conventional design standards.
For example, a class 1500 ball valve could be equipped with PTFE seats which can endure 200°C to 250°C, though only in combination with limited pressure. If the valves are exposed to a temperature this high as well as the highest possible pressure at which they should still be able to function, the seats could be damaged, which leads to seat leakages. Alternatively, a valve could function very well at room temperature, but for low-temperature or cryogenic tests, hardness of materials, moisture, tolerances and clearances play a major role. In such conditions, all valve features must be just right, or seat leakage can occur, as well as the valve only being able to open or close with immense strength.
As more and more end users and engineering companies started to demand DVT, it was time to launch an international standard: ISO 23632. Only seat and operational testing is described in this standard because fugitive emission testing is already covered by ISO 15848-1.
Environmental benefit
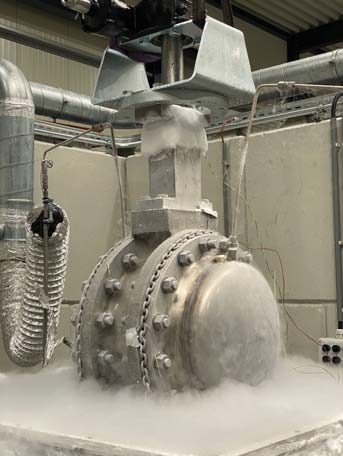
In addition of safety and reliability, ISO 23632 also offers an opportunity for the customer to help the environment by validating the durability of valves. By selecting a product that went through a series of qualifications, the customer opts for a product that will most likely last longer and that will, in the long run, consume less resources than an untested product that could fail prematurely and would have to be replaced.
ISO 23632 is one of the building blocks that ISO is developing to reduce the environmental impact of the valve industry. Ultimately, the customer will be interested in performing environmental life cycle assessment (LCA) of its valves. LCA is a method used to evaluate the environmental impact of products or services over their entire life cycle, from the extraction of raw materials to disposal or recycling. In order to perform such study, one has to assess how long a product will be able to stay in service. ISO 23632 is a valuable source of data for conducting an environmental life cycle assessment by providing intel on product durability.
However, to fully complete the assessment and enable accurate comparison between various valves, additional parameters such as a valve’s technical and economic reparability, environmental impact during manufacturing, and recyclability level will also be necessary. The development of new ISO standards will eventually allow for fair and accurate comparisons between products when conducting LCA. In conclusion, by following the guidelines outlined in ISO 23632, companies can improve a plant’s performance and safety, reduce their environmental footprint, and contribute to a more sustainable future.
About the authors
Colin Zegers is the founder and Managing Director of ITIS BV. He has been involved in leak testing, industrial product testing, valve testing, and inspections for 25 years. Colin is Team Leader of ISO/TC 153, WG5, CD-ISO 12101: Type Approval Testing of stem sealing for industrial valves.
Luc Vernhes joined Velan in 2003 and has held multiple positions. He now collaborates with clients to create innovative products and expand markets. Luc is the Chair of the Canadian Mirror Committee ISO/TC 153 and was the Convenor for ISO 23632. He holds a PhD in Engineering Physics and is a mechanical engineer.
About this Featured Story
This Featured Story is an article from our Valve World Magazine, June 2023 issue. To read other featured stories and many more articles, subscribe to our print magazine. Available in both print and digital formats. DIGITAL MAGAZINE SUBSCRIPTIONS ARE NOW FREE.
“Every week we share a new Featured Story with our Valve World community. Join us and let’s share your Featured Story on Valve World online and in print.”