A Rotork service engineer carrying out a health check
This article examines the crucial role of tailored maintenance for flow control actuators in high-risk environments, highlighting strategies to reduce downtime and ensure operational safety.
By Dave Godfrey, Rotork
When the UK’s Buncefield oil storage terminal exploded in 2005 it was said to be the biggest blast in Europe since the Second World War. The disaster was caused by faulty equipment used to monitor the flow of petrol entering a tank and is a stark reminder of the need for
a strict maintenance regime in severe service applications.
There is no single definition of a severe service application, but it can be thought of as any process where the consequences of a failure are likely to be severe. Among those processes may be any that involve hazardous chemicals, such as ammonia or caustic acid. So, the question operators must ask themselves is ‘what would the consequences be if a particular actuator failed?’
While monitoring and maintaining all flow control equipment properly is important, focusing the highest level of maintenance on the most critical actuators can prevent serious damage, expensive shutdowns, and protect lives.
Maintaining critical actuators
Effective aftermarket services address the need to monitor and maintain critical actuators that manage the flow in various sectors, including oil and gas, water, power, chemical, process, and industrial applications. These services provide lifetime management that proactively maintains critical equipment with the aim of avoiding failures. To determine the appropriate level of support for a site, experienced engineers work closely with companies to assess each unique situation. This collaborative approach ensures that maintenance strategies are tailored to the specific needs and risks associated with each installation, particularly in severe service applications where reliability is paramount.
Experienced maintenance engineers and plant managers aim to identify the most critical actuators in any facility. Their goal is to determine which actuators would cause the most significant problems, costliest downtime, or severe process interruptions if they were to fail. In a facility with 100 actuators, this assessment might highlight just 10 that require the highest level of maintenance, due to the severe impact their unavailability would have on operations.
Given that not every actuator failure would lead to a serious incident, tiered maintenance strategies have become common in the industry. These typically offer basic, standard, and premium levels of service. For severe service applications, the premium level is often the most appropriate. Companies can choose a premium package for actuators controlling their severe service processes and other levels for less critical situations.
The different tiers of maintenance vary in their scope and frequency of maintenance activities. While a basic package might involve periodic site visits for external inspections, a premium offering typically includes more frequent visits, thorough internal inspections, and proactive replacement of components such as seals, oil, and other parts as required.
These maintenance strategies can be enhanced with an intelligent asset management system, which collects data on various parameters such as vibration, temperature, torque, number of starts, and power status. This data is then analysed using advanced algorithms to assess the health of an actuator and generate recommendations for maintenance, helping to prevent failures and potential safety incidents or process shutdowns.
As industries increasingly move towards electrification, intelligent asset management is becoming more prevalent. Modern electric actuators often come equipped with data loggers to facilitate this approach.
While safety is paramount, the financial implications of actuator failure can also be significant. For instance, a company operating in Asia reported that a single critical actuator, if it were to fail, could cost $1 million a day in downtime. Such scenarios underscore the importance of appropriate service support, especially for critical equipment in severe service applications.
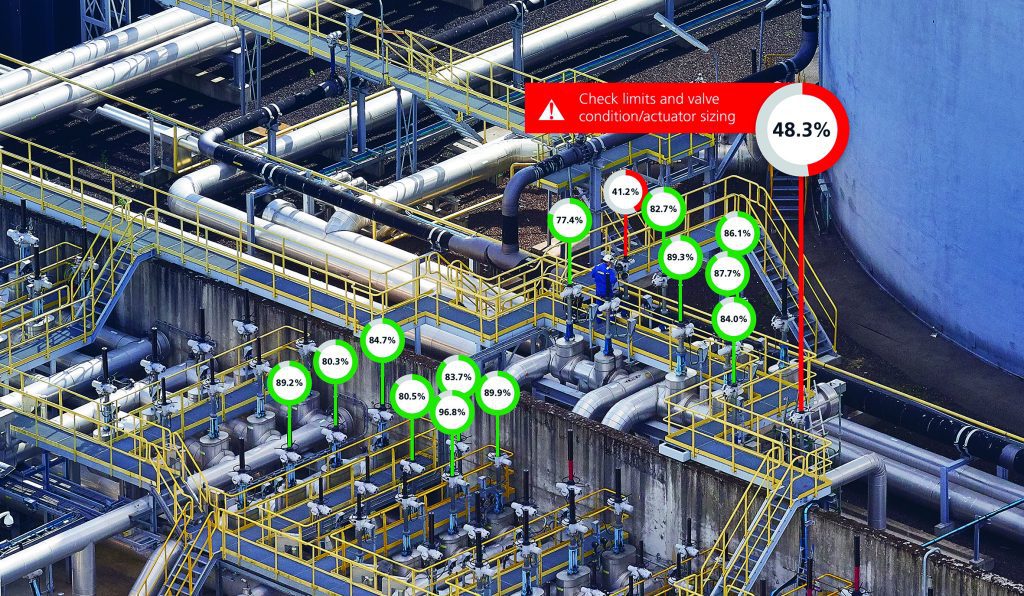
Lifecycle management and obsolescence
The rise of electric actuation delivers greater precision, efficiencies and environmental performance. Rotork takes a proactive approach to lifecycle management, monitoring and maintaining actuators as they age and helping customers plan years in advance for the cost of replacements.
At industrial sites, actuators are typically categorised into four lifecycle stages: preferred product, supported product, mature product, or obsolete product. For preferred products, spare parts are readily available, and service engineers have the knowledge and experience to repair and maintain them. However, managing older actuators through lifecycle management and obsolescence approaches is equally crucial.
For obsolete products, spares may not be available. This situation is comparable to attempting to repair a 1960s Ford Cortina today – repairs might be delayed, parts difficult to source, and some components may be entirely unavailable. The same principle applies to older actuators, where lack of spares might necessitate complete replacement if a failure occurs.
However, even if a site has 100 obsolete actuators, they may continue to function effectively for many years. The challenge arises when these units fail, as replacement costs can be significantly higher than repairs. If multiple units fail simultaneously, companies could face large, unexpected costs.
While obsolete actuators aren’t normally included in standard service contracts, many service providers, including Rotork, continue to support customers with all of their assets, aiming to remain trusted partners regardless of the asset’s age.
A recent obsolescence survey at one of the main fuel tanks at the UK’s Gatwick Airport exemplifies this approach. The survey identified obsolete actuators, leading the airport to replace 24 units and add the new ones to its maintenance contract.
This proactive strategy demonstrates how lifecycle management can be effectively implemented in critical infrastructure.
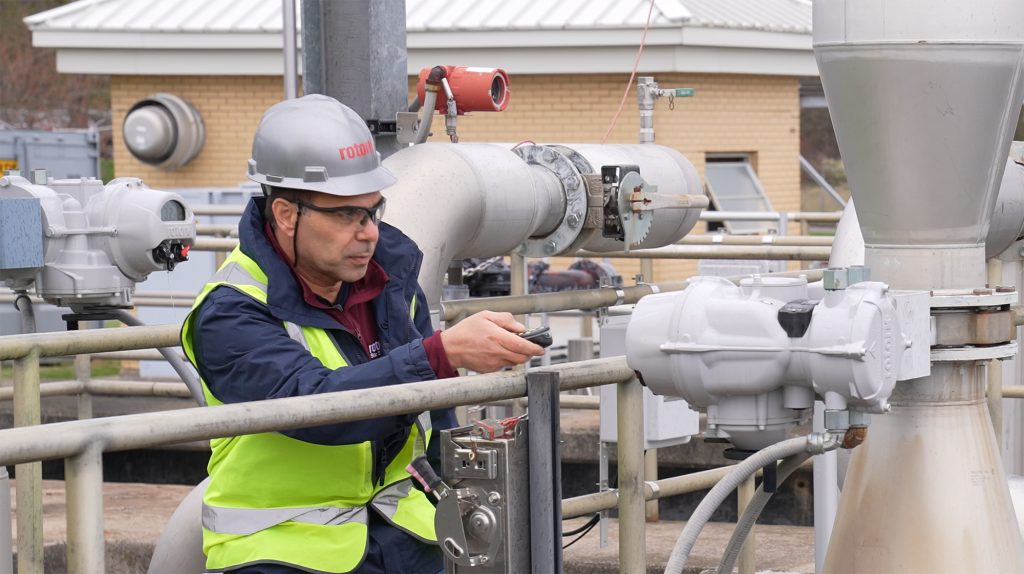
Advanced network protocols for actuator control
Specific technologies have been developed to control critical actuators effectively and efficiently. Advanced network protocols, such as Rotork’s PakscanTM, can manage numerous motorised valves, including those in severe service applications, or support the full automation of complex plants. These systems can lead to significant savings in both time and cost.
Such protocols continuously monitor actuators to ensure normal operation and allow operators to override automatic settings and control individual actuators. For instance, an operator could decide to open a specific valve by a precise percentage to relieve pressure build-up. These systems can provide crucial data such as valve position, flow rate, pressure, and temperature, which are standard feedback signals from a process valve.
PakscanTM has been installed in one of the largest offshore development projects in the Norwegian continental shelf, Johan Sverdrup, where it controls hundreds of actuators. Rotork Site Services is also providing ongoing asset management and condition-based maintenance.
PakscanTM is capable of linking up to 240 electric actuators on a single 20 km, two-wire loop. This capability enables remote control of actuators and valves, including built-in field network redundancy to maintain control even in the event of equipment or cable failure.
Aftermarket expertise and maintenance
Original equipment manufacturers (OEMs) of widely used actuation solutions, such as Rotork, can provide crucial ongoing maintenance. For example, after upgrading to intelligent IQ3 actuators at its aviation fuel station, India’s Netaji Subhas Chandra Bose International Airport signed a service plan as part of Rotork’s Reliability Services Programme.
Even without a formal maintenance contract, skilled engineers are often available to address issues. Rotork, for instance, employs over 300 engineers globally, ranging from apprentices to senior experts, all of whom undergo rigorous, internally developed training.
These engineers typically have access to advanced diagnostic tools and extensive engineering resources, including historical data. When assessing a product, they can draw upon their own knowledge and data, as well as leverage the support of their entire organisation.
Rotork offers workshop services where customers can send actuators for repair. Additional services include upgrades, where electric actuators and control systems are fitted within existing plants, as well as valve automation services. These services ensure that actuators and control systems remain up-to-date and efficient, even as technology and industry standards evolve.
Intelligent electric actuators can enhance safety, efficiency and environmental performance. While ongoing maintenance is essential for all such equipment, it becomes particularly critical when controlling the flow in severe service applications. The Buncefield incident demonstrated how poorly maintained equipment can have severe repercussions. It is crucial that operators today heed this lesson and take appropriate action to prevent similar occurrences.
Sources
1. Buncefield: Why did it happen? COMAH, 2011
About Rotork
Rotork is a market-leading global provider of mission-critical flow control and instrumentation solutions for oil and gas, water and wastewater, power, chemical process and industrial applications. They help customers around the world to improve efficiency, reduce emissions, minimise their environmental impact and assure safety.
Dive Deeper into Valve World
Enjoyed this featured article? There’s much more to discover! Subscribe to Valve World Magazine and gain access to:
- Advanced industry insights
- Expert analysis and case studies
- Exclusive interviews with valve innovators
Available in print and digital formats.
Breaking news: Digital subscriptions now FREE!
Join our thriving community of valve professionals. Have a story to share? Your expertise could be featured next – online and in print.
“Every week we share a new Featured Story with our Valve World community. Join us and let’s share your Featured Story on Valve World online and in print.”