“Over the years, Neles and its predecessors have developed capabilities that position us as a best-in-class player in our field. Now, we look forward to accelerating this agenda as part of Valmet. The key message to our customers is: our capabilities and know-how are even stronger. In fact, we are operating from a stronger base and with wider offering, covering more markets and leveraging our global reach in a more efficient manner.”
By Lucien Joppen
Neles merged with Valmet on April 1st of 2022 and became Valmet’s Flow Control Business Line. “This means that after the merger Valmet has become an even stronger, globally leading company with a unique and competitive offering to process industries”, Simo Sääskilahti says, former CFO and Interim CEO of Neles and current President of the Flow Control Business Line within Valmet.
“Valmet develops and supplies a unique combination of competitive and reliable process technologies, services and automation solutions globally and now the offering is complemented with flow control solutions. The automation solutions cover distributed control systems, quality management systems, analyzers and measurements, related services and Industrial Internet solutions.”
According to Mr. Sääskilahti, the heritage of reliable flow control solutions remains intact. The former Neles demerged from Metso in 2020 similarly as Valmet did seven years earlier.
“We can pride ourselves on over 65 years of experience in designing and manufacturing flow control solutions for various process sectors. Building on this foundation of knowledge, expertise and insights, we are ready for the 21st century with exciting developments in renewable energies and more mature sectors such as oil and gas, pulp and paper or mining.”
Positive market signs
The first signs for 2022 are also positive for Valmet’s flow control business, be it that the financial figures for Q1 of 2022 were still listed as Neles.
“The first quarter was strong”, Mr. Sääskilahti says. “Our business developed in a positive way despite current global market challenges. We had good business momentum across all geographies, in particular in North America. In terms of end user categories, pulp, paper and bioproducts projects orders remained at a good level. We also saw growth in chemicals and oil & gas project orders after a challenging 2021.” Services and MRO-driven businesses also developed well, according to the company. The above organic growth was further complemented by the acquisition of Flowrox’s valve and pump business (see text box Flowrox on page 10).
Mr. Sääskilahti says that the estimated short-term market outlook for Valmet’s flow control business is good. “All and all, I’m extremely proud of our experienced and capable global team which has been delivering reliable products and services to our customers in a challenging environment and working together in building the foundations for future growth.”
Valve automation
The previously mentioned Flowrox is of course not the only brand in the flow control business within Valmet. “The Flow Control business line will continue to offer the expertise and same extensive flow control portfolio as before: industry-leading valves, valve automation solutions and related services under the renowned Neles, Neles Easyflow, Jamesbury, Stonel, Valvcon and Flowrox product brands”, Mr. Sääskilahti explains.
“With our mission-critical flow control technologies and services we answer the continuously evolving needs of various process industries. In addition to our traditional strongholds (pulp and paper, gas processing and LNG, industrial gas, chemicals, energy, refining, etc.), we have also systematically expanded our footprint in strategic focus areas such as mining and metals, Power-to-X (see ‘Power-to-X’ box text) and renewable energy.” Talking about valve automation, the company has decades of experience in valve automation, not just Neles, Jamesbury and Flowrox valves, but any valve by any major manufacturer. “We offer complete range of solutions for valve automation needs for all industrial valves, providing the best possible flow control performance”, Mr. Sääskilahti says.
Focus on sustainability
Another aspect that has not changed due to the merger, is the focus on sustainability. As a result, Valmet’s Flow Control Business Line will continue on its path to reduce CO2 emissions for its own operations as well as for its customers.
“Being ready for what the future brings is not just about understanding and anticipating the changing needs of the industries and the specific processes and valve applications within”, says Jukka Borgman, Director of Technology Development, Valmet’s Flow Control Business Line.
“It also means designing and manufacturing product solutions and services that help reduce energy consumption and environmental impact today. In most cases, a more sustainable and environmentally friendly process is more efficient in terms of process performance and profitability, which reduces cost for our customers.”
According to Valmet, three key aspects related to valves stand out clearly in the forefront: reduction of emissions, internal tightness and a lifecycle view. In all three cases industry standards and regulations play an important role in driving development and ensuring the environmental performance of industrial processes.
Valmet: Facts & Figures
• Advanced technologies for pulp production
• Technologies for sustainable cardboard and paper production
• Flexible tissue-making technologies
• Resource-efficient energy and environmental solutions
• Innovative automation solutions
• Reliable flow control solutions
• Remote expert services through performance centers
• Advanced industrial internet solutions
• Virtual, augmented and mixed reality applications
• Services for reliability and performance
• 17,000 professionals
• Over 140 service centers globally
• 24 research and development centers
• Sales in 2021: EUR 4.5 billion
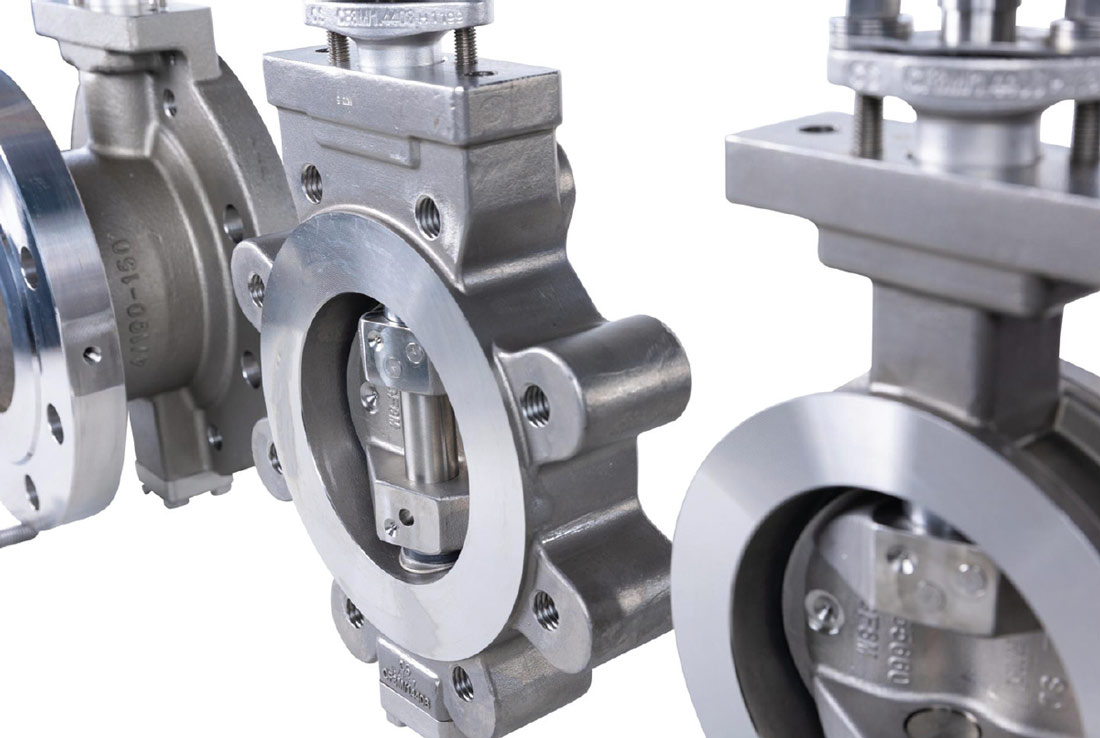
Lifecycle-focused viewy
“While regulations dictated by governing bodies continue to set strict parameters, there has been a strong shift towards end users setting tight demands on valves in industrial processes”, Mr. Borgman states. “The shift in emphasis has been from factory acceptance testing (FAT) towards type testing where valves similar in type to those ordered are put through rigorous testing, ensuring up to several hundreds of thousand cycles under simulated conditions. This is a testament to the third factor, which is a more lifecycle-focused view on sustainability. Products not only need to pass pressure testing prior to being installed, but the valve design and manufacturing quality must be proven to perform over time. There is also a clear trend, which shows that emission standards are required more and more often, even by customers in rapidly developing and industrializing countries. And more often the reason for modern emissions requirements can be found in environmental concerns rather than just the elimination of local risks and hazards.”
Flowrox: strong asset in mining and metals
With the acquisition of Flowrox (Q4 of 2021), Neles cemented its position in the mining and metals industry. These markets are expected to book strong short- and mid-term growth for the next decade. This growth is driven by the increasing demand for metals, ore depletion and underlying investments into more efficient processing, so the company says.
‘With good long-term fundamentals, service intensity and a different cyclical nature balancing out cycles of Neles’ more traditional core industries, mining and metals is an attractive industry for us. The acquisition enables us to better leverage growth opportunities in minerals processing applications and serve customers with expanded offering. Diversification of our customer industries is a key component of our growth strategy. Flowrox is an excellent fit for us since it is a well-known niche player in flow control within mining and metals, with the right offering and very strong competence and know-how.’ (Source: company website)
Long history in hydrogen valves
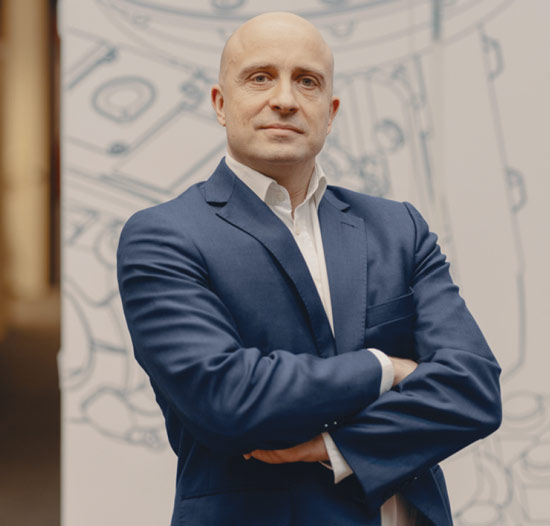
Apart from making existing processes more sustainable, Valmet also focusses on relatively new industrial processes that are designed to lower or offset CO2 emissions. These technologies include for example Carbon Capture Utilization & Storage (CCUS) or green hydrogen. Hydrogen is most often used for the production of fertilizers, as a feedstock for chemicals or for power generation.
“While hydrogen and oxygen might sound like something new and exciting, we actually have a long history of supplying valves to both”, says Ville Kähkönen, Head of Renewable Energy and Gases at Valmet’s Flow Control Business Line. “We have ample experience in designing and manufacturing valves for these applications.”
Oxygen is a very dangerous process medium and not all players are aware of the requirements for oxygen valves, Kähkönen states. “In some cases, special materials might be needed. Again, as with hydrogen valves, we have a long history in this product segment. Currently, we have a recorded installed base of approximately 30,000 valves in active oxygen service worldwide.”
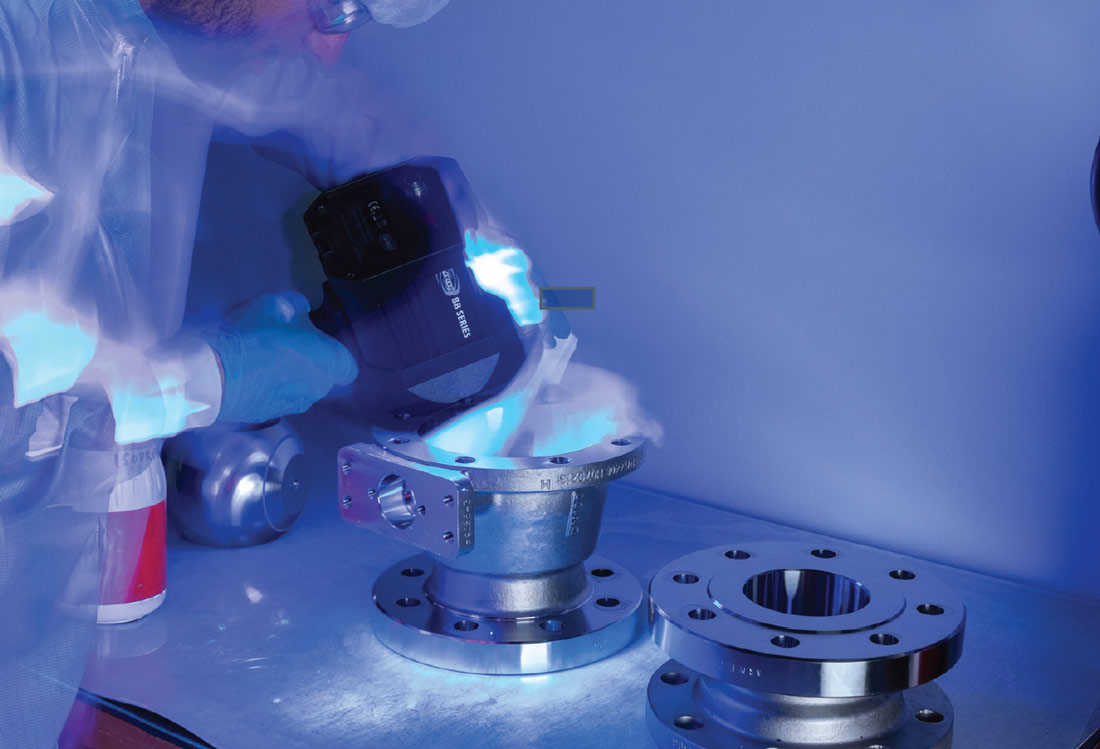
Power-to-X
Power-to-X refers to hydrogen technology to store or convert surplus electricity, generated preferably from renewable energy sources. PtX also covers the conversion of electric energy via hydrogen to hydrogen-based synthetic fuels and feedstock.
The process to produce hydrogen requires huge amounts of energy. Traditional production methods using fossil fuels emit a lot of CO2. Green hydrogen production, however, uses renewable energy, such as wind, hydro, or solar power. Green hydrogen is a great carrier of renewable energy and it also facilitates the production of green hydrocarbons and chemicals, such as eMethane or eMethanol. Burning green hydrocarbons emits greenhouse gases, but those are taken from the atmosphere during production, so the carbon emission balance is neutralized.
Oxygen valve service
It is also noteworthy to mention that Valmet operates specialized facilities to provide oxygen valve cleaning. When dealing with oxygen in industrial processes such as PtX, it is not just important to select the right valves for ensured performance, safety and long-lasting reliability, it is also vital that the valve degreasing and cleaning process adheres to the tightest of regulation-based international standards.
The regular cleaning and maintenance of valves in oxygen service is one of the most important factors that simply cannot be neglected, according to Mr. Sääskilahti. “Our special cleaning process is planned and implemented in accordance with our global procedures, which fully comply with the international oxygen cleaning standards. The safe and effective cleaning and degreasing of oxygen valves sets very specific demands on the equipment, space and facilities used for this important maintenance work. We have dedicated clean rooms permanently constructed in five different countries with a combined available space of more than 400m2.”
Next generation butterfly valves
Plants around the world are focusing increasingly on topics like the renewal of established technologies, better performing solutions and the use of (data) analytics. These, and the ever-present need to increase cost-efficiency – doing more with less – guide the company’s R&D activities.
In 2021, the company launched a new versatile butterfly valve range that was designed based on the above customer trends. “Safe and sustainable operations must adhere to today’s strict standards and regulations. This range ensures this adherence and facilitates extended process uptime, a performance that maximizes process efficiency, yield and simplicity. These characteristics make these valves an attractive option for a wide range of applications”, says Taija Hämäläinen, Head of Butterfly Valves at Valmet’s Flow Control Business Line.
The versatility of the above range is illustrated by its ability to combine various parameters, such as materials, sizes, pressure classes, etc. which allows customers to get the exact configuration for their application.
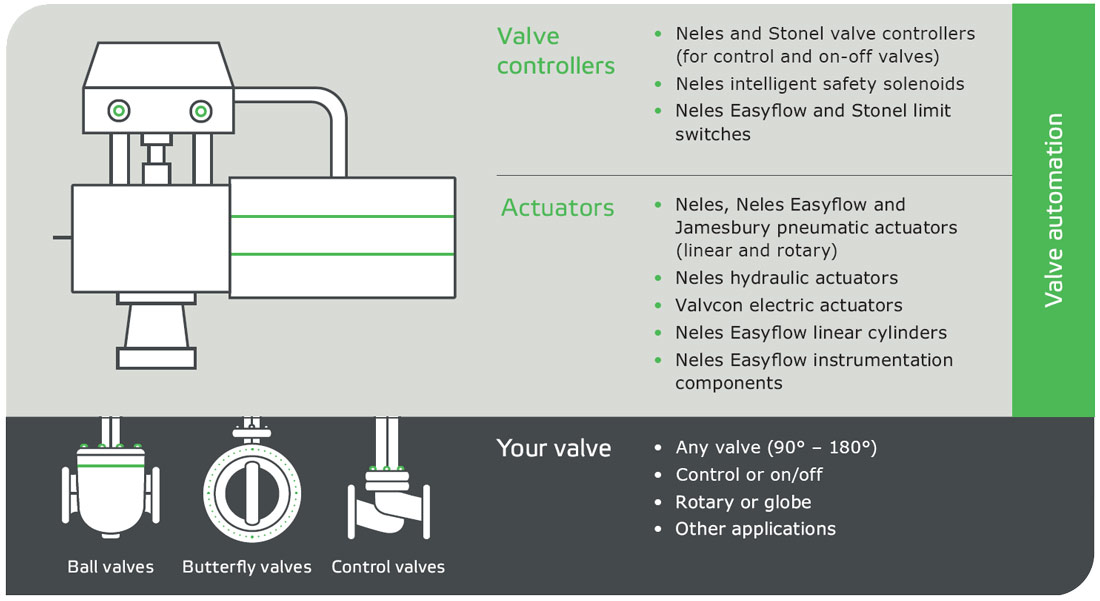
Positive feedback
‘The versatile butterfly valve platform offers reliable solutions for a wide range of applications including a high-cycling valve to handle high-purity gases and valves for abrasive service or corrosive media’, the company states. ‘The cross-compatible components and standardized parts make it easy to upgrade valve performance or to conduct maintenance without the need to replace or dismantle the entire valve.’
“Our goal was to simplify valve selection for all customers, irrespective of their industry or technical background”, Ms. Hämäläinen continues. “Customers have welcomed the new range which helps them easily select the features, functionalities, and materials they need to create a robust and reliable butterfly valve that meets their exact requirements. We have also received positive feedback about introducing a platform that helps them to streamline their spare part strategy and maintenance activities. A wide coverage of international standards and regulations has also been seen as a benefit of the introduced product range.”
Enabling technologies
Valmet’s flow control business has invested and continues to invest in enabling and supporting technology domains to stay ahead of the pack. “We are one of the front runners in 3D-manufacturing in the flow control business”, Mr. Borgman says. “In 2018, we delivered the first valves with 3D-printed valve parts. In some sectors, additive manufacturing (AM) is viewed as simply a handy tool for developing prototypes, but not for us. We see real opportunities with AM for less standardised parts. For example, their noise attenuation trims which with AM benefit from very complex internal flow paths. For customers, AM therefore means having access to a superior valve trim with a longer life span and more reliable performance. Besides, we are also playing an influential role in using AM in the production of pressure-retaining components.”
Fast delivery of valve automation components via Eurohub
‘Reliability and availability are two things that are extremely important to our customers’, the company says. ’We are continuously developing not only our products, but also the way we work with partners and customers around the world. In 2021, we have launched Eurohub, which ensures the availability and faster delivery of standard valve automation components across the continent. It is a logistics and warehousing concept that will reduce the need for our European channel partners to stock spare parts and replacement devices locally on site. The Eurohub is a concept that makes life easier, simpler and more economical for our channel partners in Europe, with delivery times ranging from same day delivery to a maximum of 1.5 weeks to the further reaches of Southern and Eastern Europe.’
(Source: company website)
Metal matrix composite materials
Another topical area within material science is the advance of metal matrix composite materials (MMC), as used the Neles Wear-blockTM. These hybrid materials combine the superior hardness of ceramics and the toughness of metals to offer the best possible reliability and performance to end-users.
More times than not, material wear is the root cause of failures. In MMC, the ceramic addition is embedded into metal, and contributes especially to the wear resistance, while the metal carries the mechanical load and improves impact resistance.
“We have built up expertise in technologies, such as advanced powder metallurgy, that are needed to integrate MMCs into products. These MMCs are then used as an inner layer in multi-material constructions where the outer layer is a standardized construction material. This combination ensures PED requirements for ductility are met. We have implemented various MMC-based solutions in the field for more than ten years”, Mr. Borgman states.
To recapitulate, Valmet’s Flow Control Business Line will continue on its path to develop reliable, safe and sustainable flow control solutions for various applications in a myriad of product segments. Simo Sääskilahti: “For our customers, we are there on the same road towards more sustainable and efficient process industries.”
About this Featured Story
This Featured Story is an article from our Valve World Magazine June 2022 issue. To read other featured stories and many more articles, subscribe to our print magazine.
“Every week we share a new Featured Story with our Valve World community. Join us and let’s share your Featured Story on Valve World online and in print.”