The Northern Lights Project doesn’t just stand out as the world’s first open-source CO2 transport and storage infrastructure, it also reaps praise from the entire CCUS community for freely sharing extensive project details. Taking advantage of Northern Lights’ open-door policy, VW’s editors enjoyed a guided visit around the receiving terminal currently under construction at Øygarden in Western Norway.
By David Sear, Valve World
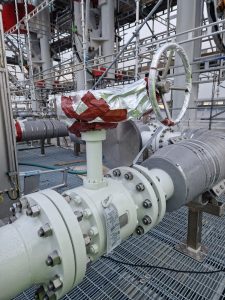
Weather and safety issues permitting, there isn’t a single area where visitors to the Northern Lights CO2 receiving terminal are unable to go. The logical point to start, however, is at the brand-new jetty. There, our gracious host Project Director Sverre Overå explained, “we designed the jetty to accommodate the specified tankers. These carry 7,500 m3 of liquified CO2. There are three unloading arms from Technip Energies in France. One is for offloading the CO2 whilst a second provides for vapor return. The third is a spare, which can fulfil both functions. The unloading arms are larger than might be expected as we had to take into account the effects of the local tides as well as the fact the ship will rise significantly during unloading.
Asked about the need for vapour return, Mr Overå said this concept may be unfamiliar to people used to the oil industry. “When transferring oil, all you need to consider is the necessary headspace. However, when pumping out a certain volume of liquefied carbon dioxide, you must ensure it is replaced with an equivalent volume of carbon dioxide vapour so this is a fairly complex system.”
Special alloys
Moving away from the jetty, Mr Overå first indicated the pipework required for unloading and vapour return before pointing to a third line. “This pipework is designed to allow for circulation, necessary to keep all pipes sufficiently cool. If liquified CO2 were to come into contact with a warm surface it could potentially flash.”
The next stop took in the twelve storage tanks built by IDESA in Spain. Together, the tanks can accommodate an entire shipload of liquefied CO2 plus a small margin. The storage tanks act as a buffer, allowing Northern Lights to balance incoming tanker deliveries with outgoing injection operations, all the while ensuring a reasonably stable injection flow rate. Incidentally, a further nine storage tanks have been ordered – a sign of Northern Lights’ confidence in the future of the CCS market.
Despite the sleek appearance, the tanks have been built without the need for costly, high-quality steel, said Mr Overå. “Corrosion is not a problem when working with pure carbon dioxide. This means that carbon steel is perfect for items like storage tanks, valves, pumps, piping, etc. Our contract with customers therefore stipulates purity requirements for the carbon dioxide and limits for selected contaminants. And yes we will be checking incoming cargoes for any undesirable contamination.”
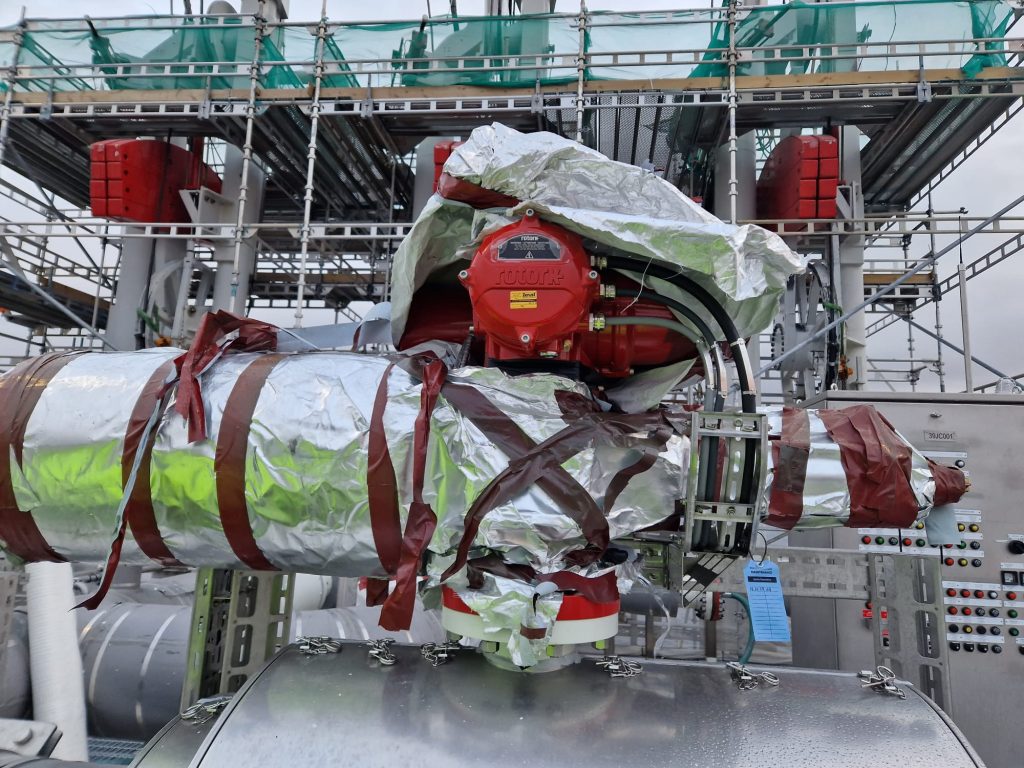
Flow control
A raised gangway provides access to the numerous pipes heading to and from the storage tanks. Here, multiple valves allow specific tanks to be filled or emptied. Sadly, there was insufficient time to inspect all equipment, but a significant number of valves were clearly delivered by Italian company LVF, with Rotork from the UK providing large numbers of actuators. Many valves had extended stems, to allow for thick layers of insulation along the pipework.
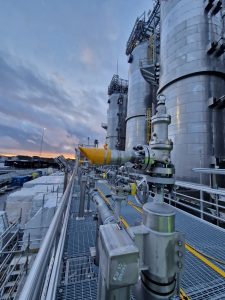
The outlets on the pressure relief valve also drew attention, as each is covered with what appeared to be yellow socks. Mr Overå explained: “here in Norway, we always have to consider the possible build-up of snow or ice. Therefore, we designed these ‘duck bill’ caps specifically to protect the safety relief valves. They will easily blow off if needed, even by a low over-pressure situation. The bright yellow colour gives an immediate visual confirmation that they are securely in place, protecting the valves and ensuring the safety of the entire plant.”
Further discussing flow control issues, Mr Overå indicated that valve selection engendered plenty of healthy discussion. “Working with subcooled fluids like liquefied CO2 means you have to consider what might happen if it were to evaporate and form a gas If such an overpressure situation is a possibility, then it is crucial to avoid cavities that can trap liquids in valves.”
Safety first
At the end of our pleasant visit, Mr Overå confirmed again that Northern Lights has been designed with safety as a top priority. “The receiving terminal has been engineered and built to the highest standards whilst the aquifer was selected based on extensive seismic surveys. Even if the unthinkable – a CO2 leak – were to occur, Mr Overå would remain pragmatic. “Carbon dioxide is not a flammable or toxic gas and any leaks at the terminal will simply flow downwards towards the sea and dissipate.
Having said that, I have full confidence in our engineering skills and fully believe that the Northern Lights Project offers permanent and safe storage. Ultimately, everyone here at Northern Lights sincerely hopes that by openly discussing our successes and set-backs, other companies will be inspired and encouraged to help develop a viable, full-scale CCS infrastructure.”
CCS in a nutshell
Carbon capture and storage (CCS) separates and captures carbon dioxide (CO2) from industrial sources to be transported and stored long-term, usually in underground geological formations. This aims to reduce greenhouse gas emissions and mitigate climate change.
CCS can capture over 90% of emissions directly from sources like power plants. Global CO2 storage capacity is estimated to be sufficient for centuries at current rates. However, risks of leakage remain a concern.
CCS is considered expensive, but higher carbon prices and utilization of CO2 to produce chemicals can improve economics. Supportive policies like tax credits and emission reduction requirements are emerging, though some criticize CCS as prolonging fossil fuel use versus transitioning to renewables.
About this Featured Story
This Featured Story is an article from our Valve World Magazine, April 2024 issue. To read other featured stories and many more articles, subscribe to our print magazine. Available in both print and digital formats. DIGITAL MAGAZINE SUBSCRIPTIONS ARE NOW FREE.
“Every week we share a new Featured Story with our Valve World community. Join us and let’s share your Featured Story on Valve World online and in print.”