Plant and personnel safety relies heavily on valve reliability and integrity.y Laura Wang, Valve World Asia
Mousa R. Al-Harbi is an Engineering Consultant and Valves Committee Chairman for Saudi Aramco. In this interview, he shares his experience of ongoing challenges and demands faced by end-users in valve applications.
By Laura Wang, Valve World Asia
Career journey in valve engineering at Saudi Aramco
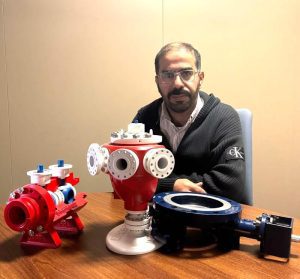
Although this is our first interview with Mr Mousa R. Al-Harbi, he is no stranger to Valve World as his team’s technical articles have been featured multiple times in Valve World’s global, Americas, and Asia publications. Since joining Saudi Aramco straight out of university, Mousa’s experience has encompassed mechanical engineering, plant operations in Gas Oil Separation Plants (GOSPs), upstream oil and gas processes, project management in facility construction, valve specialisation and standards development, among others.
Upon graduating with a degree in Mechanical Engineering at Milwaukee School of Engineering in the United States, he promptly joined Saudi Aramco as a Plant Engineer in several Gas Oil Separation Plants (GOSPs). His responsibilities encompassed a wide range of plant equipment, working closely with plant operators and gaining a deep understanding of the process side, which was crucial for equipment operation. As GOSPs are the first plants to handle upstream oil and gas fields, he was also responsible for well services and operations, giving him exposure to the entire upstream process, including valve operation and maintenance.
Three years later, he joined the project team to build a new facility, experiencing all design phases, from conceptual design to construction completion and commissioning. He also oversaw the field network, working extensively with various valve types. This diverse experience led him to focus more on valves. Subsequently, he moved to central engineering within the Consulting Services Department (CSD), as part of the valve team, serving the entire company and joint venture facilities. Their task involved developing and maintaining standard requirements, as well as supporting operations and projects. Given the rapid evolution of the valve industry, he underwent numerous developmental assignments.
Currently, Mousa is the chairman of the Valve Committee, which continuously reviews specifications and standards to ensure sound and practical governance.
Typical valve problems & solutions
The cost of valve failure can be enormous, given their critical role in diverting or isolating fluids and as essential safety components. Plant and personnel safety relies heavily on valve reliability and integrity, making any signs of failure a matter of immediate concern. For Mousa and the team, when a valve fails, the top priority is to conduct online troubleshooting to minimise plant or unit shutdowns to preserve operational continuity.
Mousa shared: “To address these issues effectively, we have established special guidelines for assessing valve failures and have developed customised procedures to tackle them. Our collaboration with field personnel involves the application of diverse technologies and methods aimed at ensuring operational safety. A common issue is a valve’s inability to internally isolate fluids when closed, often resulting from wear and tear on sealing surfaces over time and exposure to varying operating conditions.”
“To combat this, we impose stringent material requirements for valves intended for extended service lives and arduous applications. We also include supplementary specifications for online interventions, such as mandatory sealant injections and the use of drain and vent valves. Furthermore, we maintain close cooperation with our maintenance crew to adopt the latest technologies for valve cavity and seat flushing, as well as advanced sealants.”
“Our engagement with partners, particularly our valve suppliers and field operators, has reached new heights. We conducted a detailed and comprehensive failure assessment to study the trends in valve failures. This assessment allowed us to address these issues at a company level, shifting from a reactive approach to a proactive one, where we identify potential failures before they occur and enhance overall performance. The study revealed significant gaps and areas for improvement in various domains, including governance (by refining specifications and requirements) and the identification of new technologies for valve inspection and maintenance.
“Given the diverse classifications of valves, they are included in our overall periodic maintenance programs. These programs ensure that valves are regularly inspected and maintained, thereby continuously guaranteeing their integrity and reliability. Our proactive approach and close collaboration with partners have led to numerous success stories, underscoring our commitment to excellence in valve management.”
Valve supplier management and market trends
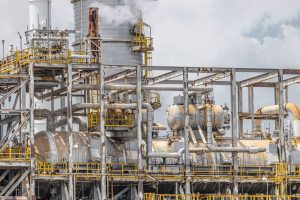
Different valve types are sourced from various suppliers, and Saudi Aramco categorises them using a unique numbering system, aligning with industry trends where no single supplier excels in all valve types. Specialisation exists within types, too, with some suppliers focusing on large sizes, high-pressure/upstream applications, or small sizes for clean/instrumentation uses.
Mousa explained: “We rigorously evaluate a supplier’s technical and quality performance before adding them to our Regulated Vendor List (RVL), assessing financial stability, technical capabilities, R&D, and quality systems to ensure consistent product quality. Products undergo varying levels of in-process and final inspection, tailored to application needs. We periodically review suppliers’ performances with different metrics, delisting some and limiting others’ scopes. Many suppliers have grown with Saudi Aramco, expanding product portfolios and approvals gradually.”
“The valve industry evolves with market trends, causing supplier performance and status to fluctuate. In market downturns, some suppliers scale back production, while in growth phases, key suppliers expand to meet demand and gain market share. Production philosophies have shifted from vertically integrated models, which ensure quality control but drive up costs, to relying on specialised subcontractors and sub-suppliers for cost-effective production. This trend has expanded internationally, optimising key processes and cutting costs, allowing suppliers to focus on design, partner assessment, and received goods inspection with final testing.”
Partnering with suppliers
“I find it interesting that although valve design and manufacturing know-how is a well-established field, R&D cannot stop, and those who invest in this thrive and can more easily adapt to changing industry conditions,” continues Mousa. “Rapid changes and advancements affect all factors, from materials used to manufacturing methods, valve design, and the supply chain. Therefore, for a supplier to be part of this development, they have to adapt how they do business, invest in development, and work as partners with their clients to form a cohesive team.”
One of the success stories that Mousa and his team are proud of is the level of engagement they have with their partners, both valve suppliers and field operators. The team conducted a detailed and comprehensive assessment to study the trend of failures and address these on a company level. The main goals were:
- to move from a reactive to a proactive response to failures,
- to identify failures before they occur,
- to improve performance.
The study identified major areas of improvement in areas such as governance (improving specifications and requirements), and enablers to identify new technologies for valve inspection and maintenance. Valves are now assigned different classifications and included in periodic maintenance programs, so they are inspected and maintained continuously to assure integrity and reliability.
Future trends in the oil & gas and valve industries
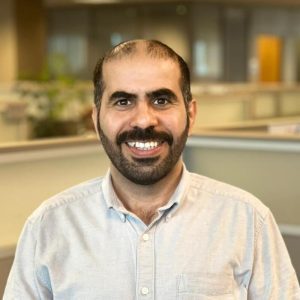
The valve industry is continuously evolving to meet new demands and energy trends within the oil & gas sector. Challenges related to industry regulations and standards are pushing valve manufacturers to innovate new designs and utilise advanced materials. For instance, the decarbonisation trend is prompting valve suppliers to adopt new types of seals and stem designs to reduce emissions. Additionally, stricter fugitive emissions regulations are leading to more rigorous testing of valves. Furthermore, the rise of hydrogen processing is necessitating valves with fewer joints and advanced materials to meet process requirements. Today, manufacturing methods are undergoing significant changes, requiring valve suppliers to adapt to advancements such as 3-D printing, robotics, and computerised machining. These technologies enable the creation of new shapes, designs, and improved welding and material treatments. Suppliers who fail to keep pace with these developments may fall behind and risk going out of business.
Moreover, Mousa believes that the industry is currently experiencing an AI-driven industrial revolution, making valves smarter. “Many valve suppliers are integrating intelligent features that allow for continuous and real-time monitoring of critical parameters such as cyclic loading, torque values, pressure changes, and temperature trends. Advanced analytics enable remote sensing, where data is transmitted to solution centres for thorough analysis and diagnosis. These analyses are accompanied by alert messages and embedded corrective measures, providing plant operators with the information needed to make informed decisions on valve maintenance and replacement.”
“In this context, predictive analysis and smarter valves are increasingly becoming the norm. The main challenge lies in how to effectively merge operational and manufacturing knowledge with these advanced and smart predictive solutions. However, with the proven utility of simulations in providing valuable insights, it is evident that this integration is already a feasible and practical reality in the valve industry.”
Meet Mousa at Valve World Southeast Asia 2025!
Mousa and his colleague from the Beijing office will give a presentation at Valve World Southeast Asia 2025 in Singapore in September, titled “Systematic Approach of Valve Casting Assessment.” This presentation will delve into various valve body casting defects, their corrections, and SOUTHEAST ASIA the methods and processes influenced by material selection, valve component size, type, and final shape. While casting defects like voids or inclusions are expected and often tolerable for certain applications, different industry methods assess their severity, with defect location being crucial. The paper will explore critical valve locations and services where defects are unacceptable, how they can escalate to severe consequences, and case studies of valve failures due to improper defect corrections, along with the corrective actions taken to mitigate these failures. For the upcoming Valve World Southeast Asia Expo & Conference, Mousa noted: “Our approach is to follow industry developments, assess advanced materials and technologies, and integrate R&D into our daily mindset. When challenges arise, we seek industry solutions or develop our own. We deeply evaluate technologies and ideas, pilot them safely, and analyse their success. We consider our company a pioneer in leading the industry, so we’re excited to showcase our innovations and meet peers, partners, and customers to share insights, learn, and explore collaboration. Together, we drive innovation and progress in the valve industry.”
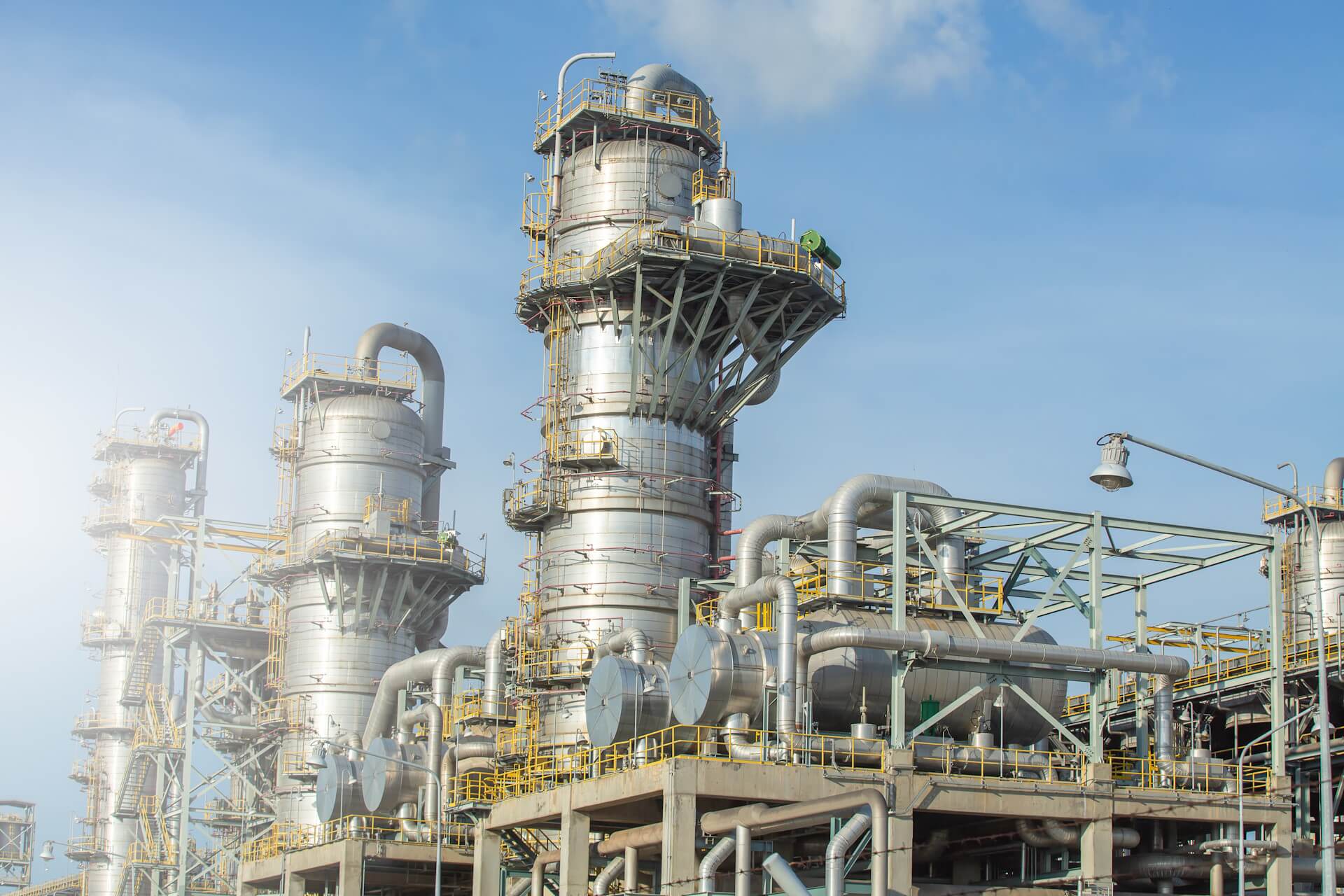
Dive Deeper into Valve World
Enjoyed this featured article from our June 2025 magazine? There’s much more to discover! Subscribe to Valve World Magazine and gain access to:
- Advanced industry insights
- Expert analysis and case studies
- Exclusive interviews with valve innovators
Available in print and digital formats.
Breaking news: Digital subscriptions now FREE!
Join our thriving community of valve professionals. Have a story to share? Your expertise could be featured next – online and in print.
“Every week we share a new Featured Story with our Valve World community. Join us and let’s share your Featured Story on Valve World online and in print.”