In this article we take a look at the effectiveness of the optimisation approach for the selection of pipeline ball valves. Field experience of end users and valve manufacturer knowhow in specific applications are also appointed as key factors.
By Bader Al-Jarallah, Saudi Aramco Central Engineering & Marco Sparisci, Dafram S.p.A.
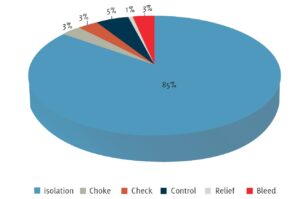
Valves are critical elements in pipeline operation. Valves are used mainly for isolation but they are also used for flow diversion, control and backflow prevention. Moreover valves are also installed for safety purposes as they are essential elements of the Pipeline Emergency Isolation Systems: a valve is the final element to respond in case of emergency to protect equipment, system, environment and personnel. Any disturbance of valve functionality will have a direct impact on facility overall operations.
To achieve the intended purpose of the valve and ensure that the valve is readily available once needed, each valve shall be properly selected for the application.
Gold plated valves that suit all applications could be very costly. A smarter approach is to optimise the selection of pipeline valves for the specifically required application. This requires clear understanding of the valve functionality and criticality to operation facilities.
Ball valves for pipeline applications
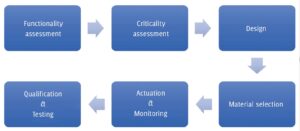
In oil & gas operation, upstream pipeline valves are considered a severe service as the valves are operated in a harsh uncontrolled environment, handling hazardous fluids including lethal, toxic, flammable gas mixtures that are often unclean due to the presence of debris and left-over materials. Ball valves are the preferred option in gas pipeline systems due to several advantages including their flow characteristics, quick opening, bidirectional functionality and compactness of actuator-valve assembly. Nevertheless, ball valves can be very costly hence an optimisation is required. In order to achieve this, designers need to have a clear understanding of the valve functionality and criticality to operation facilities. Based on assessment, four elements need to be considered, including design, material selection, actuation, and qualification.
Equipment criticality assessment
The Equipment Criticality Assessment process is a structured and systematic method of assessing the risk asset failures pose to a business. The method is used to rank the criticality of assets relative to each other. Four criticality criteria are considered in the assessment:
- Asset failure consequences
- Asset importance
- Asset reliability
- Asset capacity utilization
Based on the Equipment Criticality Assessment (ECA), pipeline valves are classified into three categories as described in Table 1.
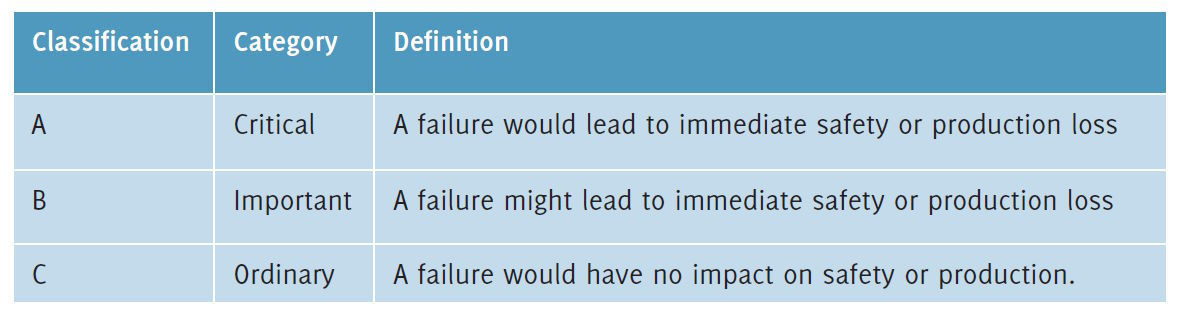
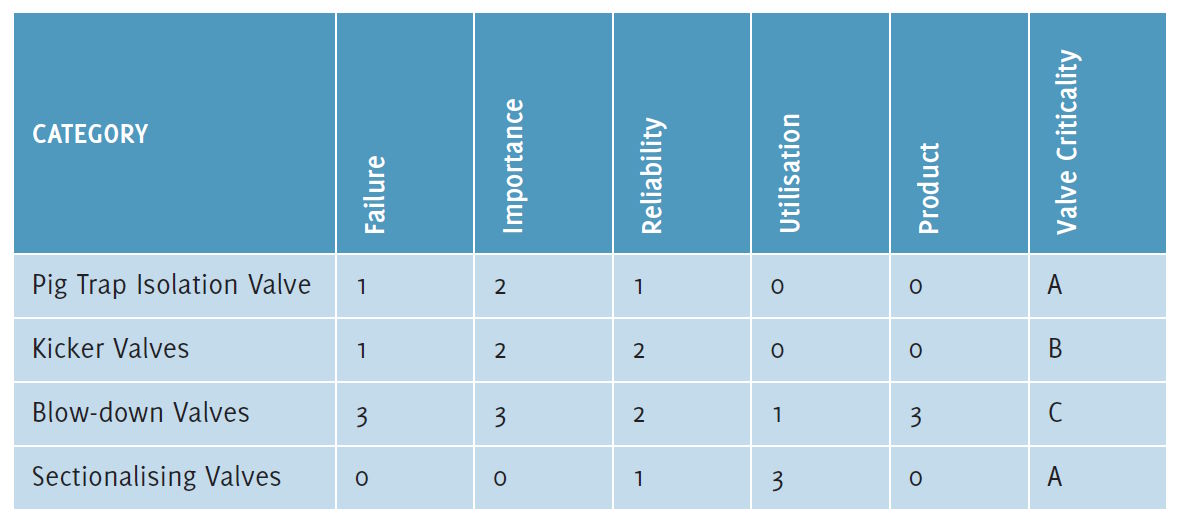
Functionality assessment
Understanding the intended function of the valve and the operational philosophy will help to develop the right specification for the valve. Table 2 is an example of the functionality assessment of sample Pipeline Valves.
Category | Function | Requirements | Recommendations |
Pig trap isolation valve |
|
|
|
Kicker valves |
|
|
|
Blow-down valves |
|
|
|
Sectionalising valves |
|
|
|
Table 2: Functionality assessment of sample pipeline valves
Design and material selection
Ball valve design and material selection are governed in several international standards such as API 6D, IOGP-S-562, API 608, DIN 3357, GB12237, ISO 7121, BS 4460, BS 5351, MSS SP-72, ASME B16.34 and NACE MR0175 etc. Nevertheless, there are still some features that are not governed and need to be defined in order to achieve the expected performance and get the full benefits from ball valve operating principle. In particular, guidelines shall include valve body design (top entry, side entry or welded body), seat design (metal vs. soft, single piston effect vs. double piston effect), trunnion design (trunnion vs. floating ball) and accessories (drain, vent, relief valve, Injection fittings). In addition, very important aspects are to be considered in the material selection of critical valve components in order to guarantee effectiveness and durability of valve performance.
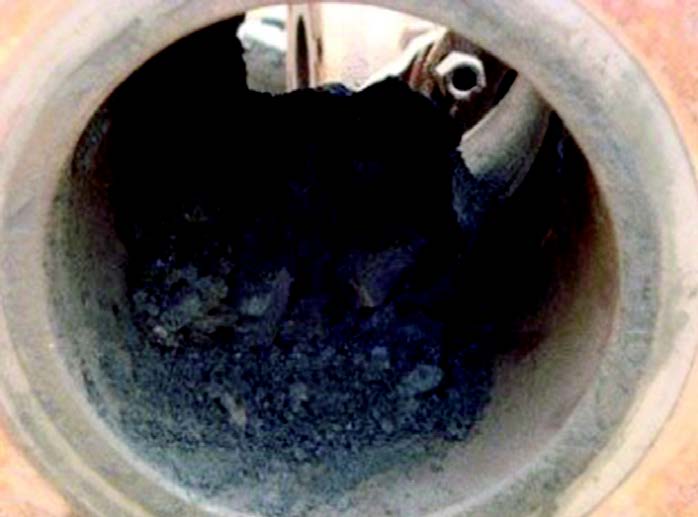
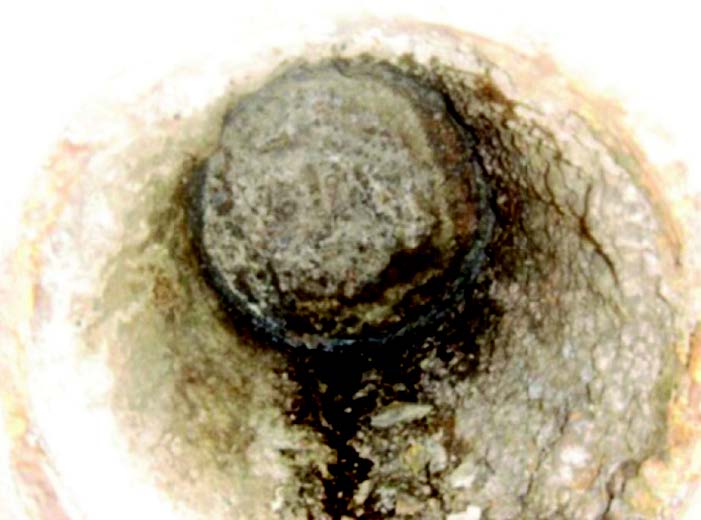
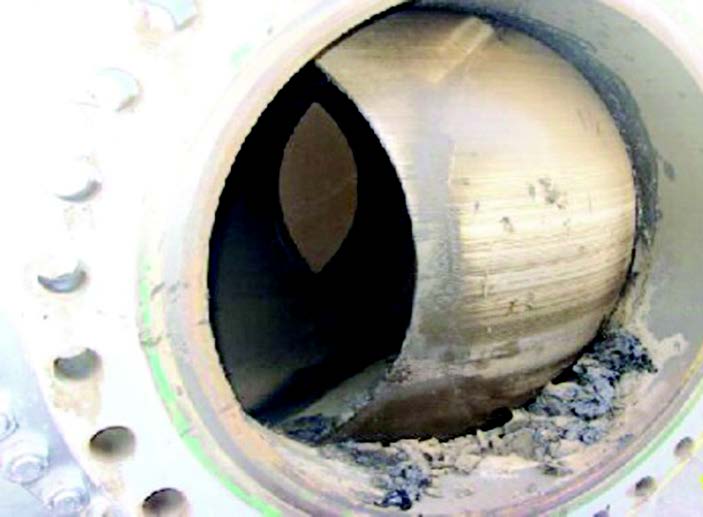
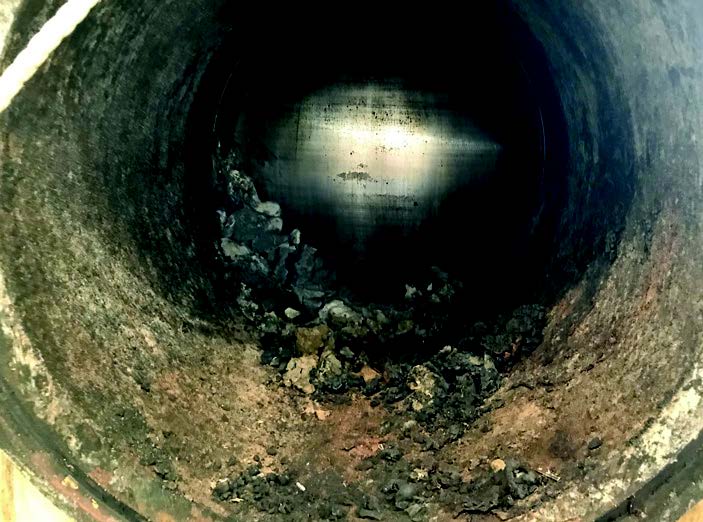
Actuation and control
Actuator sizing is an essential step in the development of pipeline valves. As a matter of fact, a failure of the actuator is a failure of the valve hence all related parameters need to be considered including process OIL & GAS conditions (all foreseen cases), aging and wear of materials, torque values for similar application by manufacturer database. Last but not least, specific safety factors for actuator sizing should be specified for the emergency stroke as minimum or better for each phase of the whole stroke (e.g. Break, Run and Re-seating).
Monitoring systems are to be considered for critical valves in order to have real time information of the obturator position and the valve seal integrity. Other parameters such as vibration, torque, pressure variations, emission measurements and actuator performance can be also considered as needed for the application. Moreover, the use of monitoring systems like DAFRAM Remote Valve Diagnosis (RVD) increase environmental and personnel safety as they enable plant prompt reaction in case of problems and at the same time they allow valve-actuator assembly to reach a higher level of functional safety (i.e. Safety Integrity Level).
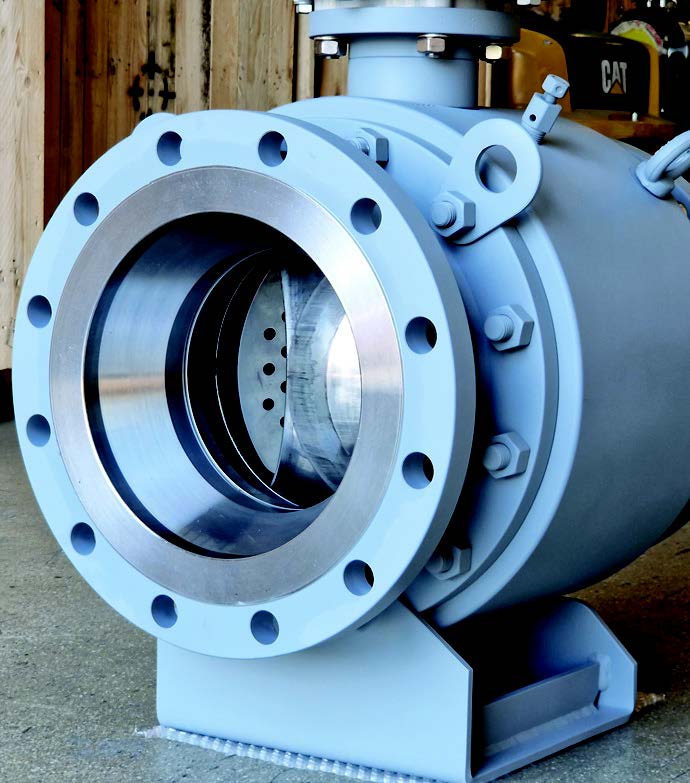
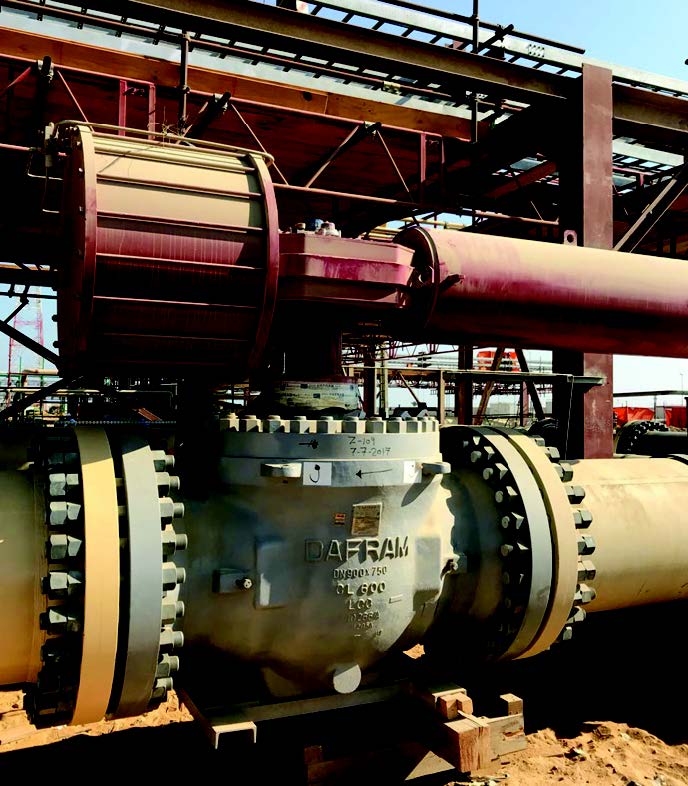
Qualification testing
A wide range of qualification test protocols is available including fire tests, fugitive emission tests, pipe loads test and validation tests with mechanical and thermal cycles to be performed. So, it is essential to define a proper set of qualification tests as well as the relevant acceptance criteria in consideration of the valve intended application as they will confirm the valve performance in those conditions similar to field ones. In addition to the above-mentioned tests, other tests may be added to qualify valve design and performance: destructive tests (run to failure), sandy tests or seismic tests.
Conclusion
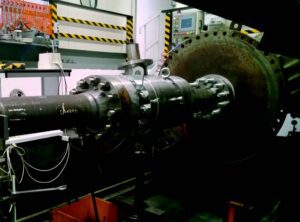
Photo© DAFRAM
Valves are critical elements in upstream pipeline systems, as any disturbance of valve functionality will have a direct impact on facility overall operations. Proper material selection, design based on field lessons learnt, innovative monitoring systems and qualification tests work all together to provide long lasting performance of valves.
Ball valves are the preferred option in gas pipeline systems, yet they should be properly selected for the application by means of criticality and functionality assessment, which are not only essential to confirm valve performance for the intended service, but also will lead to cost effectiveness and expenditure optimization. As a matter of fact, initial costs are focused and limited to the valve features required for the application and they are easily paid off with minimised maintenance or down time.
About the authors
Bader Al-Jarallah is a Valve Engineering Consultant at Saudi Aramco Central Engineering. He served as the Chairman of Valve Engineering Standards Committee as well as committee member of several engineering standards. He has dealt with various design, commissioning, operations, troubleshooting & maintenance issues.
Marco Sparisci is Technical Director at Dafram S.p.A. and he is responsible for development and design of severe service and critical valves. As R&D coordinator, he cooperates with international research institutes, universities, end users and EPCs technical experts to develop focused solutions for energy transition and innovative processes.
About this Featured Story
This Featured Story is an article from our Valve World Magazine, March 2023 issue. To read other featured stories and many more articles, subscribe to our print magazine. Available in both print and digital formats. DIGITAL MAGAZINE SUBSCRIPTIONS ARE NOW FREE.
“Every week we share a new Featured Story with our Valve World community. Join us and let’s share your Featured Story on Valve World online and in print.”