Application Engineer William Braule specialises in the selection and design of elastomer valve seals and packing for challenging applications.
By Joanne McIntyre, Valve World
William Braule is an Application Engineer working for DuPont, providing technical services for customers in energy and oil & gas applications in EMEA countries. Since joining DuPont in 2006, he has specialised in the application of Kalrez® elastomers. “Kalrez® is a perfluoroelastomer ideally suited to the manufacture of seals and packing for valves. At our facility in Switzerland, we develop and test O-rings, seals and packing to support customer projects.”
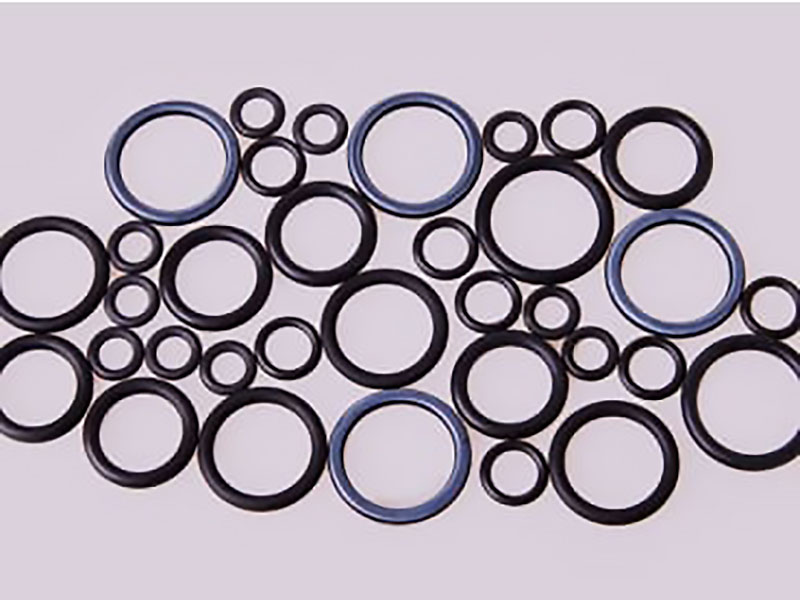
Kalrez® perfluoroelastomer
The DuPont chemical company invented Kalrez® perfluoroelastomer more than forty years ago and has worked on perfecting its application ever since. Today, key applications of the elastomer are valve seals and O-rings, but also sealing in pumps, mechanical seals, compressors and many other industrial equipment, where performance under the most stringent conditions of temperature and chemical resistance is crucial.
“Kalrez® has the broadest chemical and thermal resistance of any elastomer and is therefore ideally suited for demanding applications such as refineries, chemical plants and the Oil & Gas and Energy industries,” explains William.
“Its inert polymer structure can withstand more than 1,800 different chemicals. Secondly, it is the elastomer with the best resistance to high temperatures and can even be used at temperatures above 300 °C. These two properties make it unique.”
Kalrez® is a perfluoroelastomer suitable for valves operating in harsh environments that require specialty sealing for mission-critical applications. As oil production has been pushed into more extreme conditions and harsher environments, advanced sealing solutions are more in demand than ever.
The DuPont team has developed a new Kalrez® perfluoroelastomer product which was officially launched in November 2021 under the name of Kalrez® OG193. It can be used in a broad range of applications for the Energy industries and other high-pressure applications. The compound is particularly suitable for high rapid gas decompression (RGD) resistance in a broad range of temperatures and conditions.
DuPont Centre of Excellence
In recent years, DuPont has invested significantly in its R&D, laboratory equipment and people to better support the energy market. The company has two main centre of excellence locations in Wilmington, Delaware, USA, and Geneva, Switzerland. William is the Coordinator of DuPont’s Global Centre of Excellence for Energy in Geneva.
“The company created a global network of experts, with a presence in Houston, Texas, the Middle East, Singapore, China, Japan, and Europe to focus on the energy sector. Valve applications are an important market for us.” “At the Centre of Excellence here in Geneva, we carry out tests on O-rings and seals including high-pressure sealing tests at high and low temperature, rapid gas decompression tests and stem sealing tests on packing.
At the Centre of Excellence in Wilmington, we can conduct ageing tests in aggressive environments such as hydrogen, hydrogen sulfide, methane and others. Recently we tested Kalrez® seals at high pressure for hydrogen applications. We conducted these rapid gas decompression tests with hydrogen at 200 bar and 150 °C and the Kalrez® elastomer sustained its properties under those conditions.
Our Geneva and Wilmington laboratories have the full range of equipment to carry out high-pressure sealing tests for gases and liquids. Furthermore, our global Center of Excellence network exchanges technical studies, knowledge, and results on relevant topics to allow us to develop and keep pace with the evolving energy industry.”
Custom designs & co-development with customers
In addition to research and development on elastomer properties, William and his colleagues develop solutions and design parts to meet customer needs.
“Customers come to us when they have a tough application requiring custom valve parts. Our designers work on a project basis to conduct design and analysis, including small-scale prototyping. We also conduct sealing tests in conditions as close as possible to those of the customers’ application. Relevant details such as pressure, temperature, the type of media, service conditions and chemical conditions inform our choice of how to select a bespoke seal or part.”
“The first step is to select the best sealing elastomer for the environment.
We then recommend a design and carry out computer simulations to see how the product will behave under those specific conditions. If required, we will test the designed part in the laboratory to provide the client with some data to help him make the final selection before the final bench test. In most cases, the customer will also do a Factory Acceptance Test in their facility. As this is usually a requirement for large-size valves and equipment, our task is to work together with the customer to find the optimum sealing solution.”
Valve stem packing
Globally, the drive to reduce fugitive emissions has led to the development
of sealing and packing products that can handle the toughest conditions. DuPont developed KVSP™ (Kalrez Valve Stem Packing) to reduce emissions by providing better sealing and reducing fugitive emissions such as methane while lasting longer than other elastomers.
“It is ideal for packing the valve stem,” explains William. “Kalrez® KVSP™ helps reduce fugitive air emissions and valve leakage in chemical and petroleum manufacturing processes. The systems have been used successfully in hundreds of different chemicals, including benzene, vinyl chloride, chlorine, fluorine, steam, hot water and heat transfer fluids.”
BP Chemicals tries KVSP
BP Chemicals Ltd significantly reduced unscheduled reactor shutdowns and saved an estimated GBP 56,000 annually for each reactor control valve at its Hull, UK, plant by switching from PTFE packing to DuPont™ Kalrez® Valve Stem Packings (KVSP™). In addition to environmental and safety benefits due to improved leak prevention, the company reports much-improved valve hysterisis and control, less “stiction,” and longer service life for valve stem and bore parts.
The Kalrez® KVSP™ set operates in an aggressive process environment involving 60 percent pentane and 40 percent butane, hexane, acetone and water acid at –30 °C (-22 °F), at a specific pressure. These conditions caused annual attention to the previously fitted PTFE packings to prevent leakage, damage to valve parts and unscheduled reactor shutdowns.
“In the past, preventing product leakage from valve glands on the separator four levels at the company’s DF3 plant to avoid outages into the atmosphere and surrounding area was a major effort,” said Ken Foster, Line Manager of Maintenance Services, Control Valve Department, BP Chemicals, Hull.
“Also, valve stems were damaged beyond repair, necessitating costly replacement.”
Each time a valve has to be overhauled, whether scheduled or unscheduled, it is recorded on the valve history. The valves in question had been overhauled at least once per year over the past ten years. Previous attempts to remedy the problem with varying packing configurations and chromed stems were not successful. The solution was to fit a Kalrez® KVSP™ set supplied by James Walker & Co. Ltd, in conjunction with a ceramic coated stem.
About William Braule
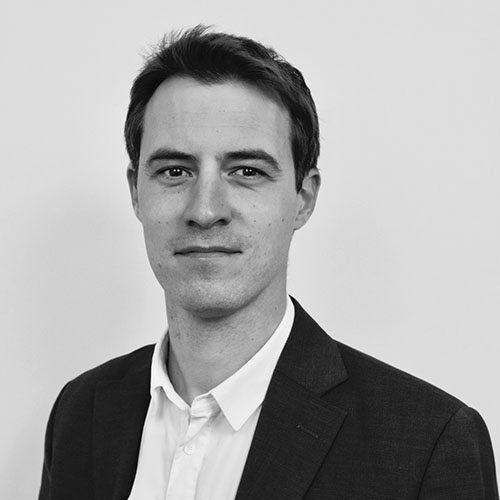
William joined the DuPont European Technical Centre in Geneva, Switzerland, in 2006, working in extrusion processing development for plastic polymers. He then spent seven years working with elastomers in technical support and formulation development for FKM and AEM elastomers.
This was followed by three years as a product specialist for Hytrel, a type of thermoplastic elastomer polymer (TPE), before joining the Kalrez® product team in 2019.