The petrochemical industry is struggling with the challenge of over-supply, but its long-term prospects are positive. The main driving factor is the shift towards sustainability, which carries costs but also creates opportunities.
By James Chater
Outlook
Growth has been slowing in the petrochemicals industry. The outlook is mixed, with the Chinese economy faltering, Europe heading for recession and the USA more buoyant. Higher oil prices and geopolitical instability have not helped.
Yet chemicals and petrochemicals are not going anywhere: they are an integral part of our lives, serving both end users in household goods and a wide range of businesses: auto, hydrogen, semiconductors etc. Demand in years to come is expected to grow. Petrochemicals are set to account for over a third of the growth in oil demand to 2030 and nearly half to 2050 (1).
According to the IMARC Group, the market is expected to grow 4.8% per year between 2024 and 2032 (2). Some of this growth will come from innovation as the industry shifts towards sustainability and takes measures to make more efficient use of resources. But regulation also drives up costs, and major producers have been complaining about stringent EU regulations.
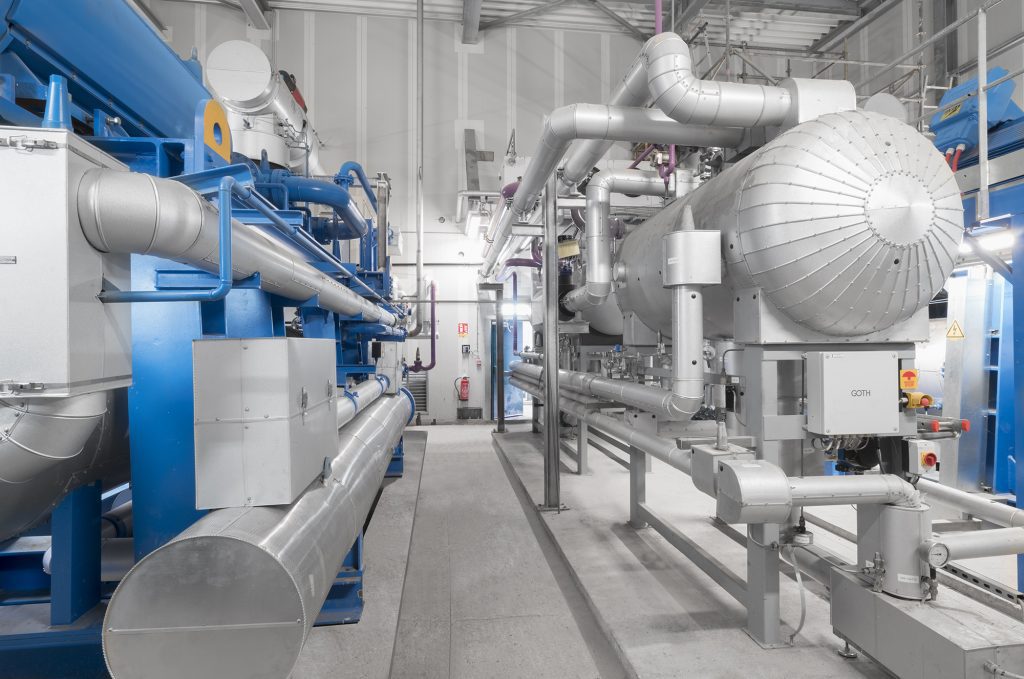
Despite China’s slow-down, several new plants have been finished or are being planned or built. BASF has broken ground on two plants in Zhanjiang and the joint Verbund site with Sinopec in Nanjing; it will build a further plant in Zhanjiang. The HAPCO plant is being built, and sites using LyondellBasell technology are being built in Lianyungang, Dongming, Shaanxi (coal-to-chemicals complex) and Inner Mongolia. Elsewhere in East Asia, Aramco and Greene Tweed are building plants in South Korea, while Indian Oil approved its large complex in Paradip and is building an HDPE plant in Panipat with technology from LyondellBasell. The Middle East continues the fast growth of previous years. Sinopec and Aramco are collaborating on YASREF in Yanbu, Aramco and TotalEnergies are building the Amiral complex in Jubail and financing has been arranged for Ras Laffan Petrochemicals, a joint venture of Chevron Phillips Chemical and QatarEnergy. The USA continues to cash in on its shale resources, with several start-ups and ongoing construction.
TotalEnergies and Borealis have doubled their PE capacity at Baystar, Texas; ExxonMobil has started up two new chemicals units in Baytown, Texas, and doubled polypropylene production at Baton Rouge, Louisiana. Chevron Phillips completed its 1-Hexene unit in Old Ocean, Texas; Dow started up units in Freeport and an HPPG plant it built with Evonik, and it will build a carbonate solvents facility on the Gulf Coast to support lithium-ion battery production.
Sustainability
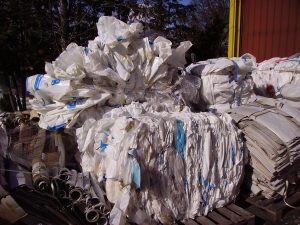
This word, already used twice in this survey, is on everyone’s lips in the process industries as they adapt to the new regulatory climate designed to combat global warming; and there is scarcely a manufacturer that has not created a page on “Sustainability” on its company website. However, it is more than a buzzword: substantial pressure is being exerted by both governments and customers, many of whom are themselves subject to stringent regulatory regimes. All the major petrochemical companies are organizing themselves to lower their carbon footprint by adopting the following strategies:
Recycling
This can take many forms, ranging from returning the plastic to its original use to the more sophisticated processes of breaking down plastics and transforming them into new products. An example of the investments many large companies are making can be seen in TotalEnergies.
The company is building a mechanical recycling unit for plastic waste at its Grandpuits site southeast of Paris. The unit will produce 30,000 tonnes a year of compounds containing up to 50% recycled plastics. Dow and Procter & Gamble are collaborating to develop technology to convert hard-to-recycle plastic packaging into recycled polyethylene with near-virgin quality and a low greenhouse gas emissions footprint. Sumitomo Chemical plans to recycle waste plastics collected from end-of-life automobiles, following the example set by Europe, where new cars are increasingly incorporating recycled materials. BASF and Sulzer Chemtech are collaborating on developing technologies to convert plastic waste into new products. ExxonMobil is operating a new facility in Baytown to break down hard-to-recycle plastics and transform them into raw materials for new products. At the SATORP refinery in Jubail, a consortium consisting of TotalEnergies, Aramco and SABIC is converting oil derived from plastic waste into polymers. In a new plant in Frankfurt-Höchst, Germany, Arcus Greencycling Technologies pyrolyzes plastic waste into a condensate that is used to produce new products.
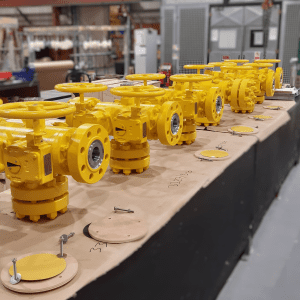
Bio-based plastics
This is an emerging industry, comprising only 1% of the plastics market. Despite concerns about competition for land use with agriculture, and the challenge of integrating them into waste management systems, there is great growth potential. Achievements so far include Coca-Cola’s bottle made of 100% plant-based plastic; Dow and New Energy Blue’s collaboration to develop bio-based ethylene from corn residue; and Sumitomo Chemical’s pilot facility (under construction) to produce propylene directly from ethanol.
Biodegradable plastic
Recycling, incineration or consigning waste to a landfill can be avoided if one makes plastics that can biodegrade or compost on its own. One of the leaders in this field is Danimer Scentific, which is collaborating with Chevron Phillips to make polyhydroxyalkanoate (PHA), synthesized from lactones produced using Danimer’s proprietary catalyst technology.
CCS / CCU
Carbon capture and storage (CCS) has become a well-established technique in several industries, ranging for steel making to oil & gas and petrochemicals. Carbon capture and utilization (CCU) is relatively new. Recycled CO2 has several uses: it can be converted into polyether used in mattresses, while researchers at the UK Centre have used CO2 to make nylon. Linde and Heidelberg Materials are using BASF technology to build a CCU facility. Most of the resulting liquid CO2 will be sold as a feedstock for the chemicals industry and into the food & drink markets. Messer has just announced a CO2 recovery plant that will cater for the food & drink industry.
Fossil-free energy
An important way to reduce carbon footprint is to use fossil-free energy such as renewables, hydrogen or nuclear power. Reliance has stated it will “use solar energy to decarbonise our O2C business and use green hydrogen generated from renewable sources – and CO2 as raw materials to develop a road map for new green chemicals, green fertiliser, and e-fuels.” TotalEnergies has announced it will generate electricity from green hydrogen with an electrolyzer built by VNG. Dow and X-energy are exploring the possible use of a nuclear SMR (Small Modular Reactor) as an energy source.
Valves in the petrochemical industry
Valves play a critical role in the petrochemical industry, regulating the flow of fluids and gases, and ensuring safe and efficient operations. They are used in a wide range of applications, from controlling the flow of raw materials to regulating the output of finished products.
In the petrochemical industry, valves must be able to withstand harsh conditions, including high temperatures, high pressures, and corrosive environments. Materials such as stainless steel, duplex stainless steel, and nickel alloys are commonly used in valve construction to ensure durability and reliability. One example of a valve designed specifically for the petrochemical industry is the thermal shutoff valve series developed by Assured Automation. These valves are critical components in refinery, terminal, and chemical piping systems, providing an additional layer of safety in the event of a fire or other emergency.
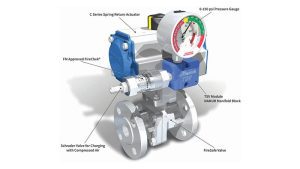
Another example is the Double Block and Bleed pipeline valves supplied by Oliver Twinsafe for use on monoethylene glycol (MEG) injection pump systems. These valves are made from A182 F55 super-duplex grade stainless steel, which offers excellent resistance to corrosion and high temperatures. They have been dynamically tested to meet the requirements of API 6A PSL level 3, ensuring their suitability for demanding petrochemical applications.
As the petrochemical industry continues to evolve and embrace sustainability, valve manufacturers are developing new technologies and materials to meet changing needs. Smart valves, equipped with sensors and connected to Industrial Internet of Things (IIoT) platforms, are becoming increasingly popular, allowing for real-time monitoring and predictive maintenance. Additionally, the use of 3D printing technology is enabling the production of complex valve components with improved performance and reduced lead times.
Recycling essentials (3)
Each UK household produces a tonne of waste per year. 80% of UK household waste is recyclable, but only 45% of household waste is in fact recycled.
Most commonly recycled plastics: PET (water bottles and plastic trays), HDPE (milk cartoons and shampoo bottles) and PP (margarine tubs and ready-meal trays). Harder to recycle: PVC (piping), LDPE (food bags) and PS (plastic cutlery).
Still harder to recycle: crisp packets, salad bags and plastic wrap.
Non-recyclable: bioplastics, composite plastic, plastic-coated wrapping paper, cling film and polycarbonate.
In general, the lower the resin count, the harder it is to recycle.
Petrochemicals and AI
Creating a sustainable petrochemical industry depends on being able to measure performance in precise terms. Aramco and IBM are setting up an innovation hub in Saudi Arabia that will address issues such as the circular economy, material discovery, sustainability, supply chain, digitalization and artificial intelligence, using technologies in hybrid cloud, AI and quantum computing.
About this Featured Story
This Featured Story is an article from our Valve World Magazine, June 2024 issue. To read other featured stories and many more articles, subscribe to our print magazine. Available in both print and digital formats. DIGITAL MAGAZINE SUBSCRIPTIONS ARE NOW FREE.
“Every week we share a new Featured Story with our Valve World community. Join us and let’s share your Featured Story on Valve World online and in print.”