INEOS Olefins & Polymers Europe has secured EUR 3.5 billion in financing to build the most environmentally sustainable cracker in Europe.
By Joanne McIntyre, Valve World
Project ONE is the largest investment in the European chemical sector for a generation. The new ethylene cracker, to be located in Antwerp, Belgium, will have the lowest carbon footprint of all European crackers, five times better than the worst in Europe and two times better than the best.
The plant will have the capability of operating entirely with low-carbon hydrogen, as well as room for a carbon capture facility and future electric furnaces. As soon as enough green hydrogen becomes available, the cracker will have a zero carbon footprint. Jason Meers, CFO INEOS Project ONE stated: “This is an incredibly important moment for INEOS. Our ethane cracker will set new environmental standards for Europe as well as help revitalise the whole of the European chemical industry.”
Largest investment for a generation
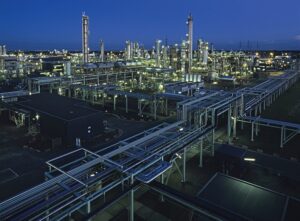
Project ONE is the largest investment in the European chemical sector for a generation. The plant will have the lowest carbon footprint in Europe, three times lower than the average European steam cracker, and less than half that of the 10% best performers in Europe.
“Project ONE is a game changer for Europe. It will bring new opportunities to the chemical cluster in Antwerp as well as strengthen the resilience of the whole of the European chemical sector,” explains Mr Meers.
Supported by 21 commercial banks, the deal validates the strong commercial rationale of the project and its leading environmental characteristics. The debt will be drawn in stages to support the spend profile of the project through to completion. It comprises EUR1.5 billion of uncovered debt, EUR 1.2 billion of covered facilities from export credit agencies UKEF, Cesce and SACE; and an EUR 800 million covered tranche of which up to EUR 500 million is guaranteed by Gigarant (a vehicle of the Flemish Government that provides loan guarantees).
Meers continued: “We are thrilled to reach this milestone and secure this funding. Bringing together such a large number of environmentally focused commercial banks alongside four governmental agencies demonstrates the huge importance of the project.”
Project ONE is part of a EUR 4 billion investment plan for the Port of Antwerp. The cracker will produce ethylene, a vital raw material for a wide range of products essential to our daily lives. These range from insulation to lightweight vehicles, plastics for medical, healthcare and food hygiene, as well as technology for renewable energy.
What is ethylene?
Ethylene is a basic building block in the chemical industry and a primary link between chemical companies and petroleum refiners. An ethylene or olefin plant will mostly produce ethylene, but also breaks the feedstock into other usable byproducts, such as propylene, butadiene and gasoline.
Crackers separate ethane from natural gas to produce ethylene, the building block of plastics and other industrial products. The plants use extreme heat to “crack” the molecular bonds in ethane to produce ethylene. Ethylene is further processed into a resin, which is used to produce plastic products.
About INEOS
INEOS is a global chemical company making the raw materials and energy used for everyday life. It comprise 36 businesses with 194 sites in 29 countries throughout the world.
Valves in ethane crackers
A range of valves is required to safely and efficiently operate crackers and to keep them running with a minimum of costly downtime.
Examples include
- Control valves handle the dilution steam injected into the furnace tubes to protect the pipes from fouling or forming coke
- As the feedstock may be either a liquid and/or a gas, the supply valve must be able to control this accurately, making it one of the most important control valves in the plant
- Controlling the dilution steam in cracker furnaces is a task for globe valves which are a tried and tested technology for this application
- Rotary valves may be employed to ensure reliability and cost optimisation
- Transfer lines and decoking typically use gate valves which can withstand dirty decoking effluent with coke accumulation, which may otherwise cause a valve to get stuck.
- Valves in the furnace section are critical in maximising ethylene production and throughput. Three critical control valve applications in the furnace area are dilution steam ratio control, feed gas control, and fuel gas control.