A thought-provoking article that challenges conventional valve testing methods and proposes a more efficient, cost-effective and informative protocol for manufacturers and end-users alike.
By Dr. S Vijayakrishnan
Every day, thousands of valves leave manufacturers’ facilities to end users after final inspection and testing. Typically, this involves conducting the following tests, which are often witnessed by customers and/or third-party inspectors:
1. A test on the valve’s capability to hold fluid under maximum rated pressure without structural damage or deformation.
2. A test on the valve’s capability to hold fluid under maximum rated pressure without leakage to the environment.
3. A test on the valve’s capability to hold the fluid at rated maximum pressure with specified maximum leakage past the closed valve to the downstream side.
In the case of control valves, the following additional test may also be done:
4. A test to confirm the rated capacity (Cv) of the valve and/or its flow characteristic.
Tests (1) and (2), often conducted as a single test, concern operational safety and are therefore necessary. These tests can detect serious defects that may pass undetected through the manufacturing process despite checks. However, test (4) is not conducted routinely but only at the request of the user, often for an additional fee. The discussion in this article focuses on test (3), the seat leakage test.
Seat leakage
What constitutes seat leakage? It is the passing of a fluid across a closed valve, which is not desirable.
What determines the seat leakage of a valve? Typically, the following factors influence the leakage capability of the valve: valve type, size/flow capacity of the valve, seating materials, manufacturing processes (particularly of the seating components), pressure across the closed valve, and age of the valve.
Tests can be conducted at the prototype stage to determine the seat leakage for a specific valve design. Further units of the valve manufactured under the same design and process are bound to conform to the same range of seat leakage, within a specified range.
Since the affecting parameters are defined and guaranteed by the manufacturer with their internal records, there is really no need to individually test each valve for seat leakage. However, there is another small chance that the valve may leak beyond the specified range. This occurs when the valve does not close fully mechanically. Despite the controlled materials and processes used, a minor defect that escaped detection may cause this to happen.
How are on-off valves used in service?
Valves used for on/off applications are typically kept fully open or fully closed. Well, when fully closed, do users need or expect the flow to completely stop?
Yes, in some locations. For example, drain valves, custody transfer valves, line isolation valves, and the like. Users would then specify valves with zero leak capability (typically soft-seated valves) or use devices like double block and bleed (in critical services).
In all other locations, what most users really need is for the flow to be “almost” stopped, not necessarily “completely” stopped.
This implies that the actual seat leakage of the valve is rarely important in most applications – if the valve stops the bulk of the flow, that is enough!
Another aspect is the disparity in conditions under which a new valve is tested for seat leakage and what the valve experiences in service. One of the most common differences is the way the valve is “fully” closed. While a factory test under controlled, ideal conditions would ensure proper closure, in actual use, the operator may hardly ever close a valve fully. Except in the case of quarter-turn valves, it may be difficult for the operator to gauge whether a valve is fully closed based solely on the tactile feedback of the operating torque they apply. To compound matters, in many services handling “not so clean” fluids, debris in the media settled at the seating area might obstruct full closure. Therefore, in actual usage, a “fully closed” valve may not be closed fully, which makes the factory seat test irrelevant in actual use.
A logical testing protocol
Considering the above, a more logical valve testing protocol may be followed. It may be divided into prototype tests (done on a set of samples) and production tests (done on each valve shipped to users).
Prototype tests
- Tests that establish the range of seat leakage for a valve design (for on-off valves; for control valves, seat leakage should, ideally, be irrelevant).
- Tests that establish flow capacity and characteristic (for control valves; for on-off valves, flow capacity is rarely important as “type and size” effectively define the ballpark range of capacity, which is almost always sufficient. A Cv test for on-off valves should be optional).
- Life tests to establish reasonable service life (number of operation cycles) during which the valve can be expected to retain all design parameters.
Typically, seat leakage tests are conducted using specified fluid, conditions, and test pressure. However, in practice, users operate on-off valves at any pressure from insignificant levels (say, as in gravity flow) to the rated maximum pressure of the valve. For most valves, the seat leakage will vary according to the differential pressure applied across the seat. Usually, leakage will increase with increasing differential pressure, but in some valve designs, it could decrease – as, for example, in pressure-assisted sealing valves such as unidirectional, metal-seated knife gate valves.
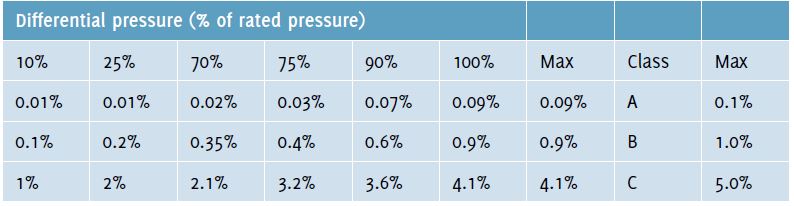
Therefore, seat leakage data at different test pressures, rather than at one test pressure, would be more logical. If these leakage flows are expressed as a percentage of the maximum flow that the valve will pass at the same differential pressure, the data would be more comprehensible to most users as well. Tests may be conducted on multiple samples of the same size and design, and the maximum leakage observed in any of the samples could be used to determine the conforming seat leakage class.
For example, a seat leakage test would involve obtaining the following data for the valve sample:
In the above example, the figures in italics are actual test data from three different valves, and the valve with data in the second row would have a seat leakage designation of Class B (seat leakage max 1%).
Another designation could be established for life tests, as per the example in the table below:
Life test qualification may then be indicated, for example, as N1, C2, etc. The N0 designation is included to be comprehensive and used for one-off special valves; they may, of course, be tested in a production test.
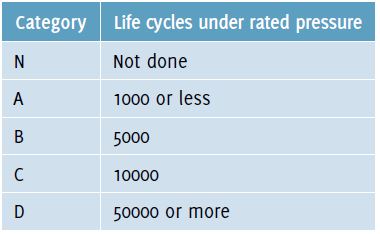
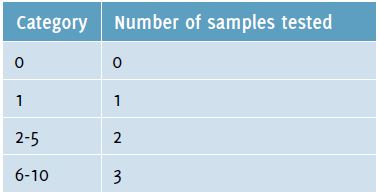
Production tests
- Test for body integrity for pressure containment.
- Test for body integrity for fluid containment.
- Test for operational fitness – to identify any rare manufacturing defects that may affect operation.
For (3), a test of, say, five on-off cycles could be set as the norm. The test would involve only operating the valve from open to close five times. This should detect any production defects affecting full closure, if any, that were not detected earlier.
Protype tests
Seat leakage: CLASS B
Life test: CLASS B2
Production tests Fluid pressure holding integrity at 15 bar: PASSED
Fluid containment integrity at 15 bar: PASSED
Operation test for FIVE cycles: PASSED
In conclusion, manufacturers could ship valves with a compliance certificate and valve tag plate stating, for example, the following:
In short, the proposed protocol removes seat leakage testing from production tests in the existing system and adds an operation test, while a life cycle test is added to the prototype testing. Prototype tests should ideally be conducted by the manufacturer with a third-party agency witness and certification for credibility. Production tests can be performed by the manufacturer and self-certified; witnessing by a user/third-party inspector can be optional.
If adopted, a protocol as described in this article would present the user with more useful and relevant data on the valve while also saving time, effort, and money currently spent on seat leakage testing.
About the author
S. Vijayakrishnan, Ph.D. in Chemical Engineering, is a retired valve industry veteran with a three decade career at DeZURIK, VAAS, Habonim and Bray. Post-retirement, he continues contributing to the industry as an author of internationally published articles on valves, particularly knife gate and slurry valves. He lives in Chennai, India and can be reached at vijykrishnan@gmail.com.
About this Technical Story
This Technical Story is an article from our Valve World Magazine, September 2024 issue. To read other featured stories and many more articles, subscribe to our print magazine. Available in both print and digital formats. DIGITAL MAGAZINE SUBSCRIPTIONS ARE NOW FREE.
“Every week we share a new Technical Story with our Valve World community. Join us and let’s share your Technical Story on Valve World online and in print.”