Brand new Houston satellite facility.
Actuators are not often thought of as a highly critical aspect of a process control system. However, without purpose-built actuators, the operation may cease to function as designed or at all. It is this driving sentiment that has led REXA Inc. to become globally recognized as a go-to source for actuator technology.
By Charlie Evans and Angelica Pajkovic, Valve World
Valve World had the pleasure of speaking with Geoffrey Hynes, President of REXA Inc., to discuss the importance of actuators in the marketplace, how its unique technologies can optimize valve packages, and how dedication to innovation and reliability will allow REXA to continue to devise new solutions.
Innovative beginnings
REXA Inc. was established in 1981, with a simple concept in mind: improve the actuator’s ability to perform positioning the valve or driven device. “The importance of an actuator is often overlooked in the process control system, and the idea was to change that,” said Hynes.
When Robert Glomeau, CEO of Dresser Masoneilan, first brought his concepts and perspective on process control improvement via, what would become, REXA technology, the listening board of directors decided against investing in his proposed product development. Knowing how significant the potential benefits could be, and tired of attempting to develop internal valve designs to compensate for inherent limitations in traditional actuator technology, Glomeau took matters into his own hands. He left Dresser Masoneilan and began developing his concepts out of a home garage.
Despite a slow start, industry professionals caught wind of the advancements of the new technology and the company was sold to Takashi “Ike” Ikegaya, President of Nihon Koso Co Ltd. “As products were beginning to enter the market but were still in development, customer acceptance was initially slow,” explained Hynes. “Ike’s belief in the concept had a resounding impact on its success. His decision to invest in the product was shortly followed by a significant order which effectively validated the technology.”
Deciding not to rely solely on business it received from the power market where it initially made its entrance, REXA expanded its capabilities into other areas. “We made inroads into the oil & gas market, and then made subsequent moves down the road into other markets such as metals and mining, and the water and wastewater industries.”
“To expand, more product development was crucial, and we have therefore invested significant time and energy into expanding the actuator’s capabilities and performance. Our company has been growing our capabilities and presence in those markets since that first significant order, and we do not intend to stop,” stated Hynes.
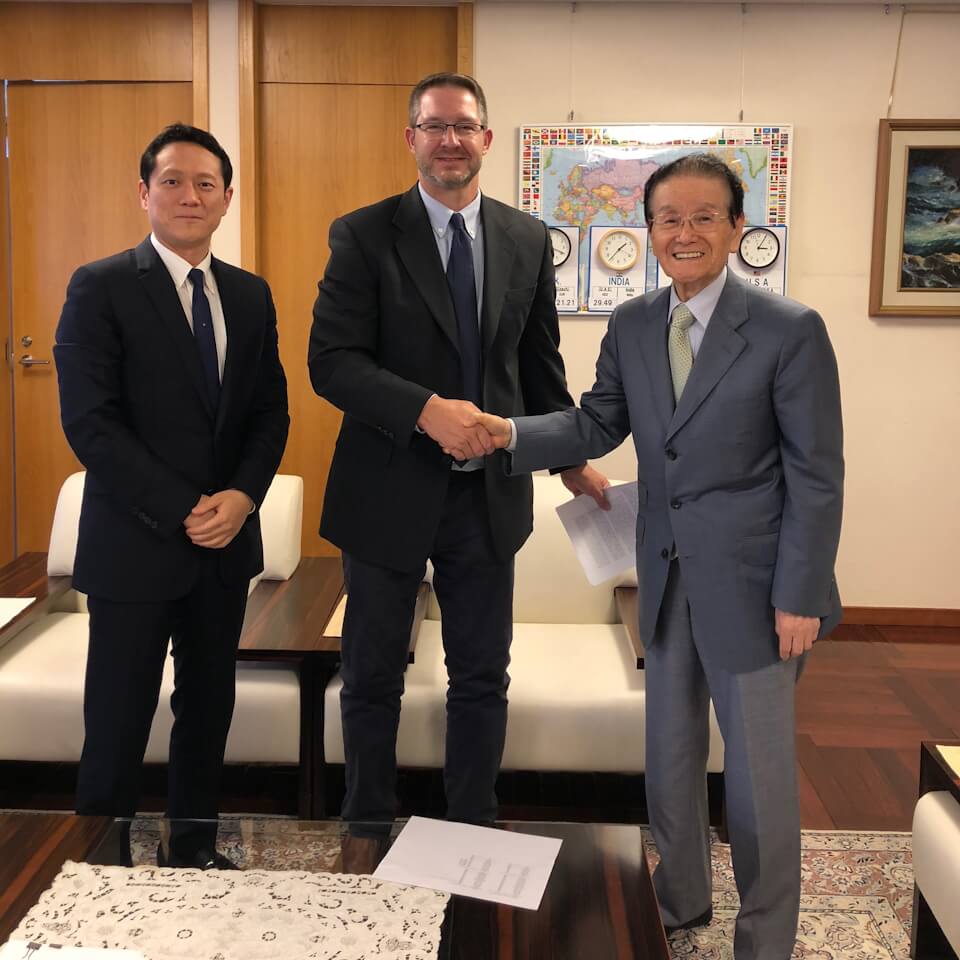
REXA owners Takashi Ikegaya (right) and Yuichi Ikegaya (left) and Geoff Hynes in the middle.
Elevating the market
Due to its longevity in the industry, REXA Inc. has gained credibility within its main market; the oil & gas industry. “Our primary target has always been oil & gas, with a heavy focus on the midstream liquid pipelines,” relayed Hynes. “However, over the past few years, there has been a more concerted and focused effort on growing our presence in the downstream market; namely the refineries and petrochemical plants.”
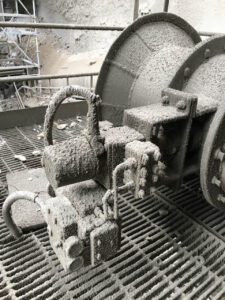
In addition to its focus on delivering packages for new control valves, much of its business pertains to retrofits and upgrades. If a plant has been in operation for some time, REXA seizes the opportunity to talk to the company about how to improve its process control systems by replacing the originally supplied actuator technology with its own. “A plant may have been initially designed to have X amount of output or X efficiency without much consideration for which actuator technologies to use in the applications that most affect those parameters. This can result in not hitting the desired targets,” said Hynes. “To address this, they often compromise on those performance targets at reduced efficiency to mitigate the risk of down time. This is not the best solution.”
REXA approaches the plant, no matter the industry, with the goal in mind to improve the performance of the process and remove all compromises, workarounds, or suboptimal ‘fixes’ put in place over years of operation. “It is crucial to us to help each company reach its optimal performance, whether that is the refining/petrochemical market, power, metals and mining – specifically, copper, nickel, and gold – or the water & wastewater industry.” “We are not a generic commodity type actuator for general service simple on off applications,” added Hynes. “We target modulating applications that have fast acting control loops, where if the actuator does not react instantaneously, it will cause instabilities, delays, or inefficiencies in the process.”
Unique actuator technology
“Actuators are often seen as less important than other parts of a process control loop, including the valve itself,” relayed Hynes,
“For us at REXA Inc., it is important to help our customers understand that actuators are just as important. We view valves as the accessory, and the actuator as the main component from a process control standpoint, as opposed to the other way around. Valves themselves are designed to handle process conditions. The valve is, simply, an adjustable orifice in a pipe. It does nothing to control without the actuator.”
Through its dedication to constant and ongoing innovation, REXA Inc. can provide actuators that exemplify this notion.
REXA’s most widely recognized innovation is the concept of Electraulic™ actuation. Electraulic™ combines the functions of a high-performance electromechanical actuator and a hydraulic actuator. Instead of driving internal gears for motion and force, the brushless motor drives a hydraulic pump in a closed loop hydraulic circuit moving a single volume of oil from one side of the piston to the other.
“It is hydraulic in the sense that it is using a hydraulic circuit internally, but electric in the sense that it is motor driven,” continued Hynes. “It is a discrete operation. The motor turns, instantaneously creating motion with the internal hydraulic ‘transmission’ until it reaches target position, and then the motor turns off, stopping the actuator. Hence the reason we have coined the term Electraulic™. One of the largest benefits of the Electraulic™ actuator technology, is that it does not require oil or filter maintenance.
“The system is not continuously circulating oil to/from a reservoir tank, it is discrete – meaning it only moves the motor/pump/oil when a position change is commanded, it only builds enough pressure to move the load it is driving, and it is always above atmospheric pressure. What this means is that, unlike conventional systems, it does not have oil heat rise associated with continuous circulation at high pressure nor does it have potential for ingress of foreign contamination or condensation into the oil. Essentially, all the factors that cause oil breakdown and regular required oil/filter maintenance (and condensation heaters) are eliminated by the inherent design. We have actuators operating in field in modulating applications for 25 years that have never had any mechanical maintenance performed,” Hynes continued.
“As the internal parts and seals are always bathed in a clean synthetic motor oil, they have unparalleled longevity. The system has 95% less oil volume than conventional systems and uses ‘off the shelf’ synthetic motor oil. There is less oil in them than there is grease in electromechanical actuators. The stable, repeatable, and non-degrading positioning performance extends valve packing and trim life. So, the end user, gets significant reduction in maintenance frequency in the valve/actuator and reliability is greatly improved. All of this is in addition to the major benefit of improved control and stability of the process that allows the user to optimize their process efficiency. They can tune their system how it was originally intended to perform on paper… without compromises.”
Optimizing turbomachinery
“Within all of the industries REXA provides solutions to, there is a very specific set of applications that we target where we know our technology provides significant value,” explained Hynes. Turbomachinery is one area that is common across all industries and therefore remains prevalent in each infiltrated market for REXA. “Steam and gas turbines typically use conventional/complex hydraulic systems to control valves and IGV’s. Those systems have all the problems described in the previous section and they are operating on the most critical equipment in the plant. It is a natural fit for REXA technology and has become one of our fastest growing application areas for upgrades & retrofits.”
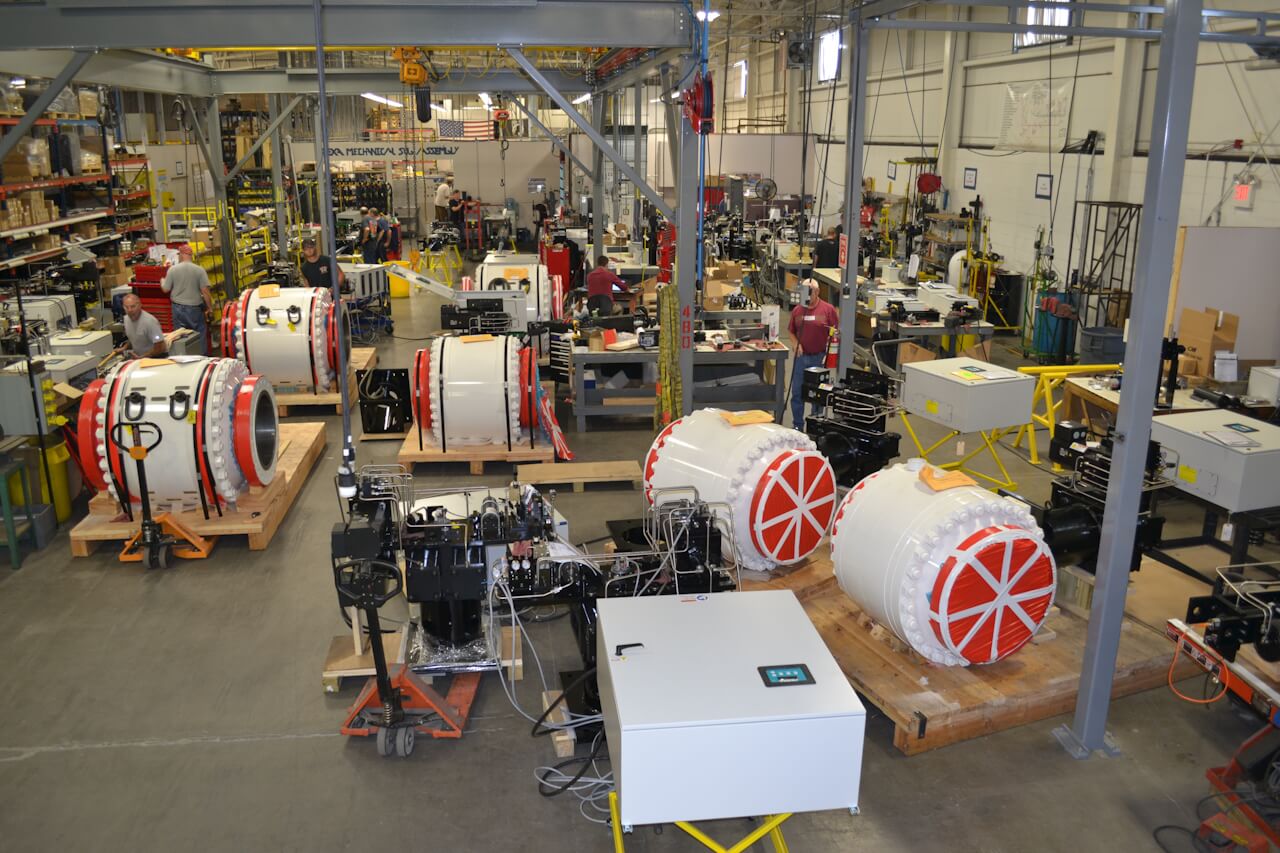
Main factory doing mount-cal-testing on large modulating ball valves.
Unique customer service contributes to reliability
The expertise and knowhow of its personnel, coupled with its dedication to continually provide reliable solutions, are just some of the many factors that elevate REXA above its competitors. The fact that many of the company’s personnel, including its sales team, are engineers, is an added benefit. As they have an intimate understanding of not only the product, but the technical details of the applications and processes that they support, they are better able to provide reliable solutions.
Rather than simply selling technology to a customer, REXA enjoys being a consultant and contributing to business issues with
its specialized experience. “We try to understand how each process works at a company, as specifically as possible, and then make recommendations on how to best address the issues. Our specialists previously worked in the plants and processes that we support. We have also established strategic relationships with companies who specialize in the processes that we serve. If we cannot help the end user with their process issue, then they can. Whether or not we supply an actuator to solve the issue is irrelevant if we are able to help the user solve their problem by bringing in the appropriate expertise,” explained Hynes.
“Our service team is also extremely responsive, and available 24 hours a day, 7 days a week. They will go to the customer site immediately and observe what is happening to help solve the problem and ensure that they remain operational. All companies have service issues, particularly when serving the most demanding applications in their field. We take those issues seriously for immediate rectification, root cause analysis, and permanent corrective action. If the root cause involves areas unrelated to the actuator performance, our specialists will keep digging with the end user to ensure that we help them find and correct the actual root cause, wherever it may be.”
If the order includes a new valve, the qualified team will proceed to mount, calibrate, and test it with the actuator before supplying the customer with the entire package. Whether it is a new valve or a retrofit to an existing valve, it is important to REXA that it install, or oversee the installation of, the actuator as well as do the final calibration. “We want to be there when plant operations begin, to observe that everything is in order. We make sure that we do not simply ship the product and walk away,” relayed Hynes.
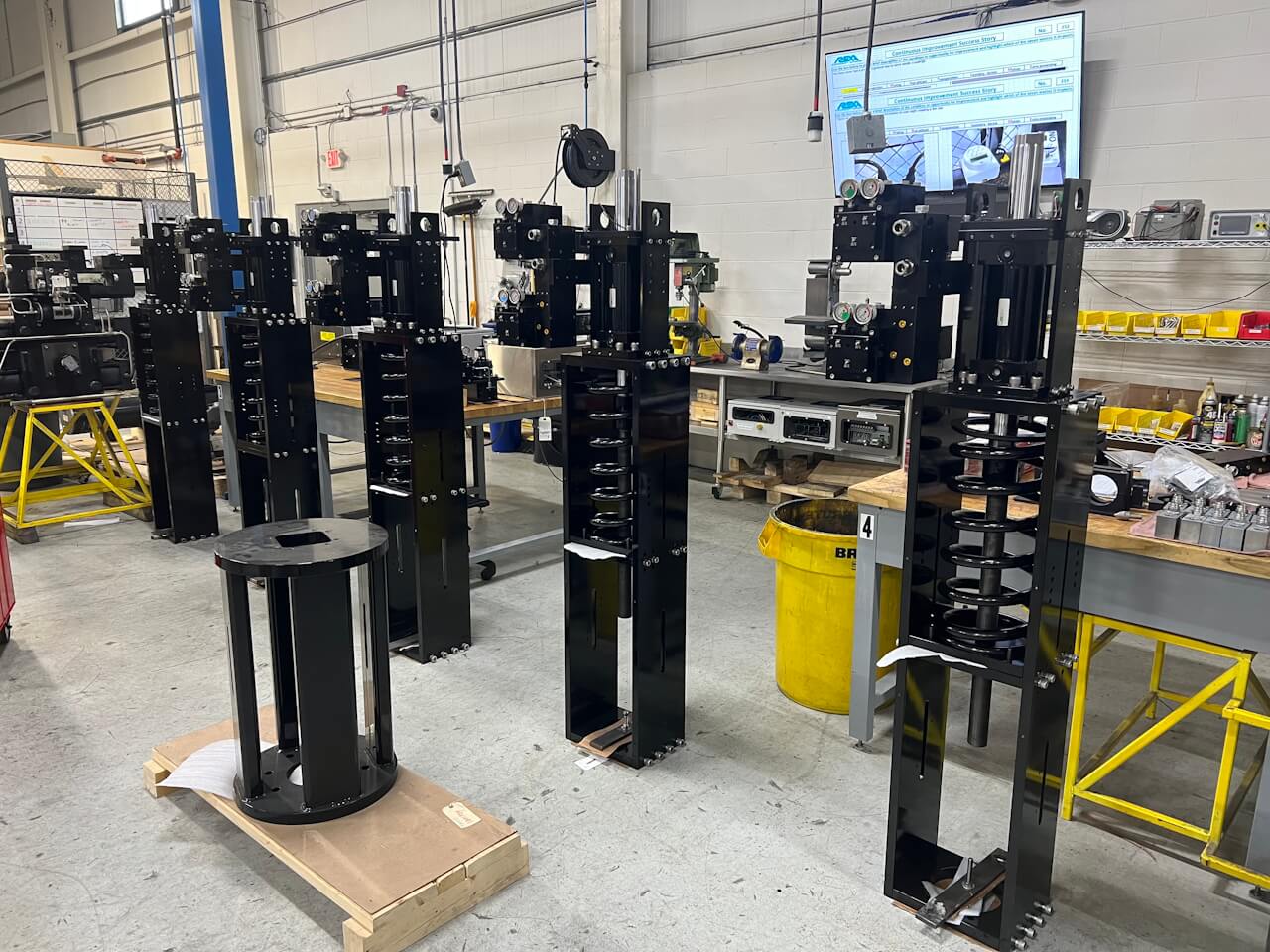
Compressor anti-surge actuators to replace pneumatics at a refinery in Saudi Arabia.
Looking forward
Although the company is not looking to broaden its focus to other non-complimentary assets, it will never cease to advance and innovate the actuator and process controls optimization skills. “We already know that building even more advanced diagnostics directly into a system is the next step for REXA,” expressed Hynes. “If we continue to enhance diagnostics that tell the customer what the actuator and valve are doing, based on historical and live time data, users will be able to pre-emptively address any issues before they become a real problem. They can also shift to more condition-based maintenance. Really, it is just asset management. It is crucial to understand and protect all the assets at a plant to avoid unnecessary risks.”
REXA has also recently expanded its capabilities with a new facility in Houston, Texas. This addition allows it to meet the needs of its North American market with faster services, response times, and valve automation services.
“It is moves like these that will continue to set a future path for REXA Inc. By anticipating the changing needs of the market and committing ourselves to delivering high quality and innovative solutions, REXA takes the opportunity to expand and thrive in each unique market where its technology can make a significant difference in process efficiency, environmental impact, safety, and reliability,” concluded Hynes.
About this Featured Story
This Featured Story is an article from our Valve World Magazine, June 2023 issue. To read other featured stories and many more articles, subscribe to our print magazine. Available in both print and digital formats. DIGITAL MAGAZINE SUBSCRIPTIONS ARE NOW FREE.
“Every week we share a new Featured Story with our Valve World community. Join us and let’s share your Featured Story on Valve World online and in print.”