This year, Score Group celebrates its 40-year anniversary. The Scottish company has a rich history of excellent technical expertise and customer care. Valve World spoke with Ian Davidson, Commercial Director; Trevor Fleming, Operations Manager; and Scott Wallis, Emissions Manager to learn more.
By Alexandra Kist, Valve World
Score specialises in valves, fuel systems and accessories, and component manufacture. It supports customers in markets such as energy, aerospace, defence, utilities and nuclear. Its services have expanded to include engineering design, repair and modification, supply, testing, diagnostics and specialist coatings.
Score is a proud provider of fast customer services thanks to its strong global presence, and its technical capabilities, such as the overhaul and testing of an existing critical valve and the supply from its stock of over EUR 190M of products, including valves and actuators. Score also offers onsite services, such as machining, mechanical joint integrity, shutdown management, testing and repair.
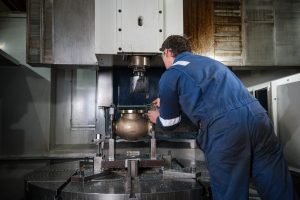
History and overview
Score was founded in 1982; just over forty years ago. “I have been with the company for 35 years now, so I have grown up with Score,” notes Ian Davidson, Commercial Director. “The company first offered repair and recertification services for valves. At the time, we served companies such as BP, Shell, ExxonMobil, and other major energy providers. Many of those have stayed with us since. Nowadays, we operate out of thirty locations across the globe, so the company has changed significantly since its inception. A major change happened in 1992, when we won a contract with a major customer to provide all valve services under one roof. This included all repairs, supply, engineering, materials management, and more. We still serve this customer under a revised contract to this day, which means we’ve got the right competencies and values.”
The business was founded by Charles Ritchie, who unfortunately passed away in 2017. Up until then, Score used to be a family-owned company. Three years after Charles’ passing, the business was sold to SCF Partners. SCF have invested in protecting the heritage and the worker mentality that comes along with having been family owned for almost 40 years. “The often-made statement is that we like what we bought and that’s a testament to all the people within the business,” Ian adds. “We are very proud of what Charles created and the way SCF has decided to stick with this company culture.”
Score was founded in Peterhead, in the north-east of Scotland, which is where its headquarters are located. Its other locations can be found across all other continents. “From these locations, and with the support from a robust supply chain we’ve collaborated with for 40 years, we offer all types of service regarding valve management, such as engineering, repairing machines, and welding tests. Our customers see us as a trusted contractor because of our one-stop-shop approach,” says Ian.
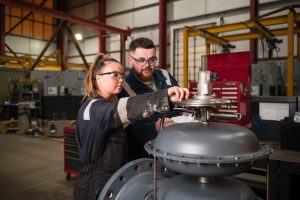
Apprenticeship programme
Score has had its impressive apprenticeship programme in place for over thirty years. “I’m actually a product of this award-winning apprenticeship scheme,” says Trevor Fleming, an Operations Manager. “In January, I will have been with the business for 27 years. A lot of our employees have come in through this programme and have stayed at Score for a long time, and I think our people are what sets us apart from the competition. They possess a high level of competency, great work ethic, profound knowledge, and vast experience. We don’t send anyone out to a customer site until they’ve completed the apprenticeship, which typically takes anywhere from five to six years.”
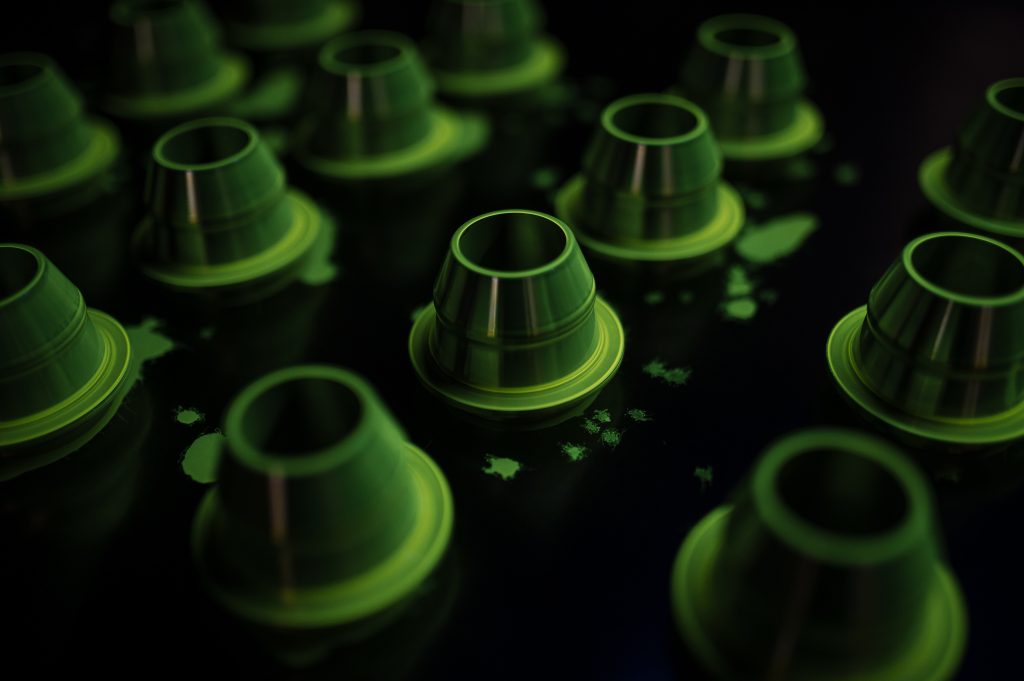
An apprenticeship at Score consists of a careful combination of academic and on-the-job training. The company allows their apprentices to travel the world and a share of their former trainees have gone on to lead the company. Score works closely with local schools on STEM (Science, Technology, Engineering and Mathematics) activities and provides advice on engineering careers.
“This year alone, we’ve received about 150 customer compliments, and I would say 95% of them pertain to the performance of our people,” Trevor notes. “We’re very proud of that as a business, and as an Operations Manager, it’s great to see frequent feedback saying the customer would love to have our technicians back on their assets.”
When enrolled in the apprenticeship programme, the technicians spend their first year forming a solid basis as engineers, whether that be in school or off the job. After that, an apprentice following the valve technician programme would move into core valve workshops. This is where they will start working in the workshop on product types, products on overhauls, modifications, and upgrades, and more. “We offer a broad variety of apprenticeships, but the vast majority of our apprentices are enrolled in our core valve business,” Trevor explains. “They will then rotate through the core departments of isolation valves, pressure safety valves, control valves, and the drawing office. They’ll be exposed to a bit of the customer interface, project management and a bit of the commercial side of the business. The apprentices spend four years moving around the various core departments and then specialise in one department.”
Globally, about 350 people are enrolled in Score’s apprenticeship programme. As the industry is dealing with a shortage of young people with technical knowledge, Score ensures that they have a large number of well-educated young staff. “There’s a large variety to the programme, and I think that shows in the number of contracts we’ve got globally. I believe we have about fifty valve management contracts, which is a great achievement,” Trevor says.
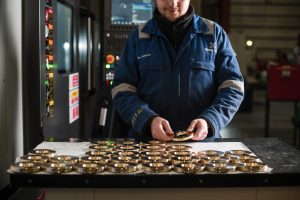
Emissions Eliminations Program
“Valves are one of the most common components in industry and the primary cause of fugitive emissions. Valve failures also significantly increase flare and vent emissions. We at Score are valve specialists and we support our customers on their sustainability journey,” notes Scott. “We’ve completed over half a million maintenance work scopes in the UK alone to date, mitigating emissions from valves and ancillary equipment. Good valve management will (by default) reduce your emissions footprint.”
“It is important to understand that there are many emission sources; you can visualise it like an iceberg. The area above the water is what everyone tends to focus on: the fugitive methane leakages to the atmosphere. Hidden under the surface however, you see
the bigger picture (or the rest of the iceberg), unnecessary (through valve) process losses to flares and vents significantly increase emissions, as do inefficiencies in other process systems (for example steam and compressed air) increasing your environmental footprint, as well as other types of process releases like internal corrosion cracking on pipework (known as non-fugitive emissions).”
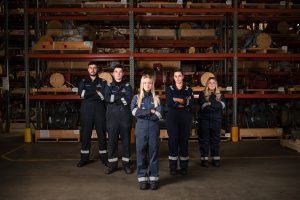
The Emission Eliminations Program (EEP) was developed to support operators in achieving their emission reduction goals in a manageable way. The programme consists of four steps: surveys (targeting potential emissions sources), analysis (interpreting data, quantifying leaks, and recommending repairs), mitigation (providing temporary and permanent maintenance solutions to eliminate emissions) and improvement (through engineering reviews, reliability enhancements and data analytics).
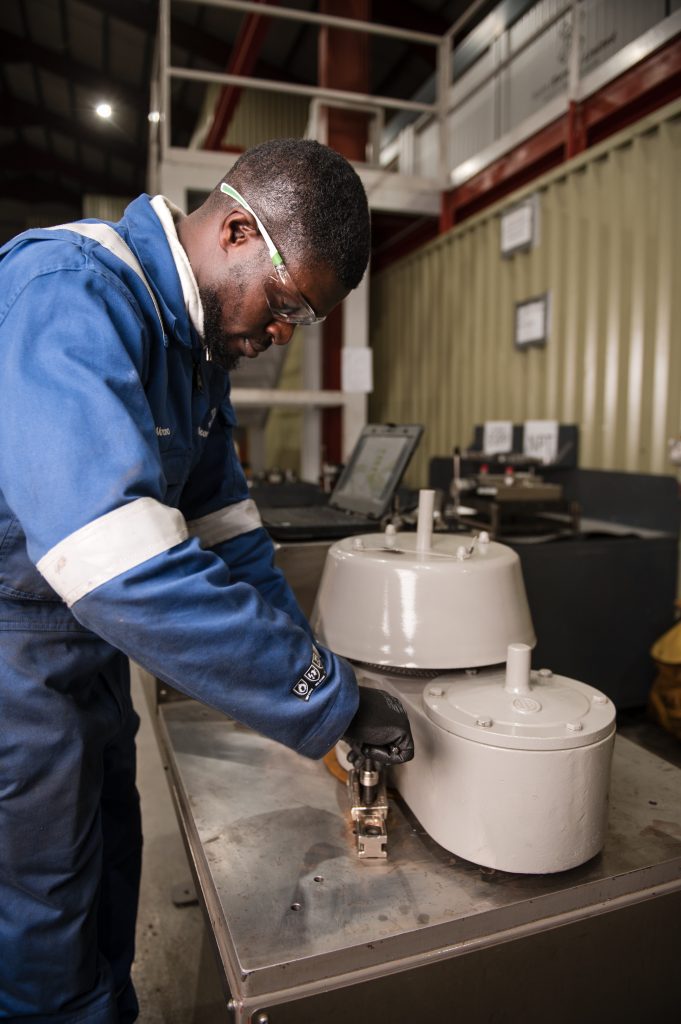
“Through the EEP, we utilise an array of different tools and technologies to identify and quantify emissions sources, for example OGI cameras, sniffing devices, high flow samplers and acoustic imaging,” explains Trevor. “Through valve emissions is a key area of focus for us (this is where process escapes internally through the valve seat, to the flare or vent). Over a decade ago, we developed our own technology to identify and quantify these emissions. The MIDAS® Meter is a handheld acoustic emissions device that detects and quantifies through valve leakages.
“We recently partnered with leading software developers asset55 to enhance our EEP solution further through data integration with their ‘Operate’ software platform. One of the key industry challenges is data management and this solution allows you to manage everything digitally, in one place.
You can monitor the environmental performance of your facility, track maintenance activities and execute work. The software offers customisable dashboards to provide valuable insights and data analytics to all stakeholders, as well as allowing the customer to report on the emission sources in a framework that suits the regulator in the required region. Work packs can be generated within the system to mitigate emission sources.”
An added value to Score’s existing customers is that Score will migrate the component databases it manages on behalf of their customers to the ‘Operate’ platform (the databases are currently hosted in asset55’s ‘Calculate’ software).
This will reduce the time it would take Score’s customers to adopt EEP and start reducing their emissions. “Say, we manage fifty different valve management contracts. We will be taking those valve contracts and migrating them over to the “Operate,” the platform that allows the customer to visualise their valve populations or their tag database in a 3D environment. That allows us to digitally plan, manage and execute emission surveys, identify the emissions leakage, identify the emission sources, report on them digitally and then the live environment shows the customer exactly where on their assets the leaks are.”
“We give our customers access to the exhaustive network we’ve developed over the last forty years,” Scott adds. “Our programme isn’t just about the leaks to the atmosphere, but it’s about capturing everything that causes emissions and mitigating the whole issue.”
Portfolio
Score identifies its core business to be the valve industry. “Our thirty locations worldwide enable us to respond quickly to our customers’ needs. We have a huge internal infrastructure, and we hold a huge amount of stock: about EUR 190M worth of products. And even then, if we don’t have a direct replacement for a faulty product in stock, we have the in-house capabilities to take that valve, shut it down, modify it to suit the customer specification and then return that valve to them,” Trevor explains.
“What’s interesting,” Ian notes, “is that the average age of a Score employee is 30-33 years old. We’re a very young organisation and that is partly because of our investment in the apprenticeship programme, I think that makes us one of the most progressive young organisations in our industry.”
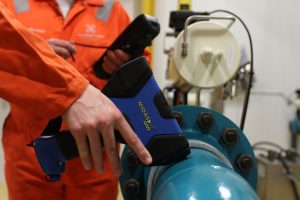
About this Featured Story
This Featured Story is an article from our Valve World Magazine, December 2023 issue. To read other featured stories and many more articles, subscribe to our print magazine. Available in both print and digital formats. DIGITAL MAGAZINE SUBSCRIPTIONS ARE NOW FREE.
“Every week we share a new Featured Story with our Valve World community. Join us and let’s share your Featured Story on Valve World online and in print.”