Article by Tony Majka, ValvTechnologies
___
Quarter turn and rising stem valves
Refer to Figure 1 for a pictorial demonstration of the quarter turn method of actuation and Figure 2 for the rising stem method of actuation.
The quarter turn method of actuation is often considered to be the more robust design for stem/shaft sealing because the stem is merely rotated about its axis in the stem seal area whereas the rising stem design is rotated about its axis and moved linearly through the sealing area. The linear movement of the rising stem allows for debris and shaft imperfections to generate leak paths as the stem pushes linearly through the seal from inside the pressure boundary to outside the pressure boundary. For this reason, ValvTechnologies utilizes quarter turn valve actuation in most severe service, high-cycling applications. This will be the basis of discussion moving forward.
Severe service stem sealing solutions
When chosen correctly, there are many stem sealing solutions in existence that can provide adequate external sealing based on a particular application. A combination of proper selection of seal material and geometry can last many years in service if the valve is appropriately designed. Some of the most common stem seals are made of elastomers (such as Buna, Viton® or Kalrez®), polymers (such as PTFE, PEEK, or special PTFE based blends) or flexible graphite derivatives (such as Grafoil® GTJ, GTK or braided rope). Each of the sealing materials have great properties in certain applications.
- Elastomer blends have great sealing characteristics and are particularly suited for high pressure, but have lower temperature limitations than graphite and blended polymers and are typically more susceptible to failure in abrasive applications such as catalyst and slurry feed.
- Polymer blends can withstand more abrasive applications and often have great chemical compatibility. At very high-temperature and pressure these often fall short of performance goals as PTFE really starts to lose its strength around 450°F (232°C) and cannot withstand a fire.
- Graphite derivatives are generally chemically inert and have very high temperature ranges. Unfortunately, graphite is porous allowing permeation in most emissions tests. Additionally, graphite tends to breakdown in high-cycle applications and extrude from the packing area if the valve is not properly designed. Although its nature does not promote longevity, it is common to find this material utilized in severe service applications due to the high temperature capability and its ability to withstand a fire.
- For high cycle applications, where stem sealing is crucial, it is common to utilize a mixture of several or all of these in a stem seal.
The details of each geometry present their own pro and con list, but the key to each of them is to turn the axial compression from packing fasteners into a radial load which seals on the stem without over compressing and wearing too quickly. A common problem with all compression seals is that an end user will observe a leak and attempt to tighten the packing fasteners to stop the leak and often over-compress the packing thus reducing its effective life.
Among other criteria, it really depends on the type of service, media flowing through the valve and size of pipeline to truly determine what really constitutes “high-cycle”. ValvTechnologies’ rule of thumb is about 30,000 cycles as this is the point when most stem seals fail. This varies a lot based on size, etc. but is a good starting point. Common considerations when working with a high-cycle application are:
- Mounting kit design: the stem MUST remain on-center when cycling.
- Clearance in the packing box: this must be kept to a minimum to prevent extrusion of the packing.
- Fire safe: does the valve need to pass a fire test such as API 608 or API 6FA? This would require a high-temperature material.
- Ability to adjust in service: valves are often in difficult-to-access areas which make adjustment difficult and dangerous.
- Pressure/temperature: this will dictate material selection as well as valve type.
- Fluid type: if the fluid is dry and/or abrasive it can cause issues.
- Thermal cycling: will the valve be subject to frequent thermal transients causing it to grow and shrink often?
- Speed of rotation: if the valve is fast-acting, see subsequent paragraph on fast-acting.
- The application was to “pulse” hot syngas (a flammable and lethal gas if inhaled). Atmospheric leaks are hazardous in multiple ways.
- The product operated at 1640 psig (113 barg) with temperatures of 475°F (246°C) while cycling from closed to open to closed in 0.45 seconds.
- The valve would dwell in the closed position for roughly 90 seconds then operate again.
- This continued for four months before any maintenance could be performed without the system running.
- There was no question that this was severe service.
After partnering with several vendors and running through many iterations of product design, the Special Projects team at ValvTechnologies came up a configuration which greatly exceeded the results we were seeking. Through painstaking efforts, the team was able to employ special materials, coating technology and a unique seal combination of filled PTFE, PEEK and graphite (known now as EcoPack®) to allow our customer to make it to an eight-month turn-around plan.
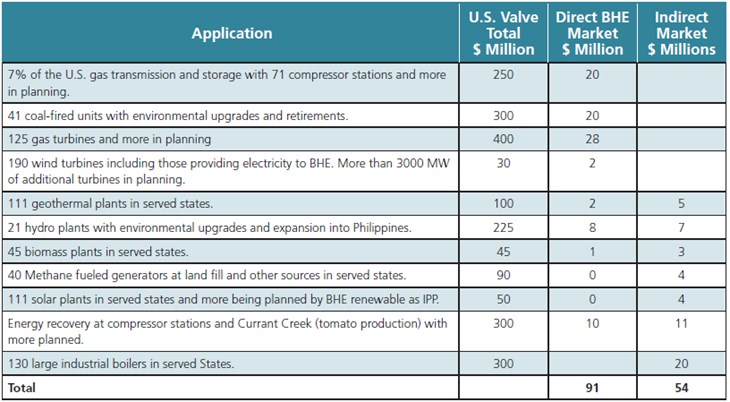
About the author
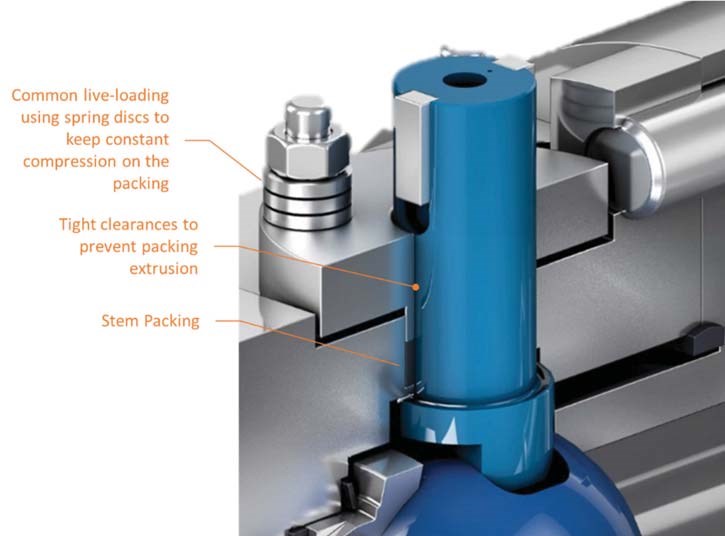