Unexpected problems in flow control equipment are the bane of all process engineers looking to start up projects on schedule. Valves are often (incorrectly) identified as being ‘bad actors’ as the root cause tends to lie elsewhere, is the experience of Valmet’s Mr Börjesson. Better on-site practices could be the solution, is his message.
By David Sear, Valve World
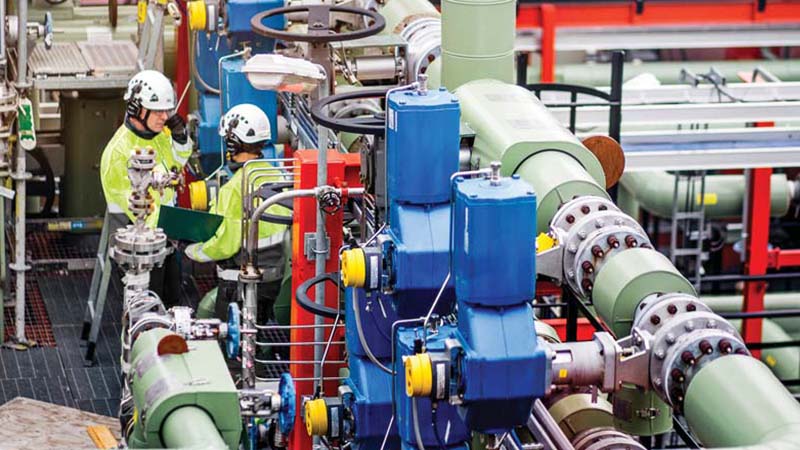
As Service Sales Project Manager in Valmet’s Flow Control business line, Peter Börjesson has been involved in numerous greenfield and brownfield projects. He has also witnessed many EPCs and end users allocate budget for the purchase of spare parts or even complete extra valves in advance, in a bid to ensure timely plant availability. After all, flow control problems are not uncommon during project commissioning and start-up.
Peter’s message, however, is that whilst such purchases may be well-intentioned, the EPCs and end users are in fact trying to anticipate valve problems which are easily preventable. A little forethought, he says, can avoid both financial costs and help keep projects on track. Moreover, he states, although the problems may manifest themselves in the valves, the root cause is often due to inadequate working practices elsewhere.
By way of example, Peter recalls discussions early in his career with a seasoned flow control engineer. “For want of a better description, he was a real old-timer. A man who let his hands do the talking. Thanks to thirty years travelling the world to provide assistance during the start-up of power plants, he had become a real expert as regards trouble-shooting. And here’s my point: although he had helped to resolve countless flow control issues, he categorically stated that valves from reputable sources were never the actual cause of problems during start-up. When I pushed him, he started to reel off a whole list of root causes, including the valve being installed the wrong way around or upside down, the valve having suffered damage during installation or whilst in on-site storage, broken limit switches due to careless handling, issues in the instrumentation system, ancillary devices which had been broken by someone stepping on them, actuated valves installed incorrectly leading to water flowing into instrumentation, valves left outside which had rusted after being left submerged after heavy rainfall… his list went on and on!”
Inspect before flushing
In the following years, Peter himself has witnessed numerous valve problems that were actually caused by shoddy on-site workmanship. “At Valmet, we take good care to properly package our valves. However, when goods like valves arrive on site, the packaging is often removed for inspection. That is fine, but if the valve is going to go into storage for another twelve months prior to installation, a responsible authority such as the project manager should ensure that the valve is then properly repacked. That isn’t rocket science, it is all down to good working practice. Note that this issue is not just restricted to some localities but occurs world-wide.”
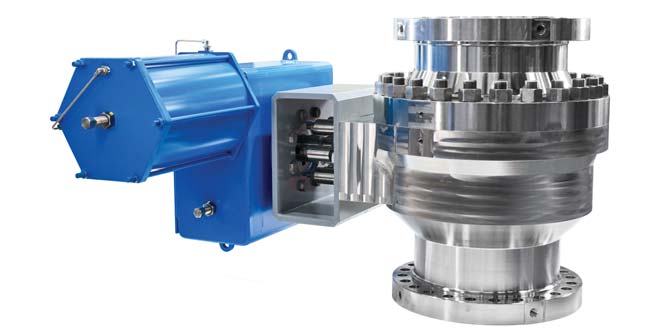
Further discussing the need for correct packaging and storage, Peter notes that a valve made of carbon steel can be stored outside provided that the manufacturer’s procedures are followed. “If not, the body could corrode, forcing the seat to push against moving parts such as the ball, which increases friction. Whilst small increases in friction will not cause issues for well-engineered valves, they can be exacerbated by additional internal damage. On many occasions I have seen items like welding rods, helmets, detritus, etc, removed from pipework during commissioning. If such items pass through the valve during flushing, they can lead to damage on for example coatings or seats. After a few strokes the valve may then stick. Again, that’s another start-up issue which could have been prevented by better advance inspection of the pipework prior to flushing.”
To help ensure valve integrity, some EPCs will open valves to remove trims before flushing and/or will (partially) dismantle valves for inspection prior to start-up. In such cases, Peter advises that spare parts should be ordered well in advance and that the work be carried out by properly trained and qualified personnel. “Take an off-centre split ball valve, where you will definitely need to have replacement soft parts available. Same goes for ball valves fitted with a backsealing arrangement that might need replacing. And if you remove the disk or segment from certain butterfly and segment valves to check behind the seat, then you will also require new pins for reassembly. If you are planning to open the valve, do check with the supplier first to ensure you have all appropriate spare parts to hand, yet without purchasing unnecessary items.”
Smoother start-up
Based on his experience, Peter is adamant that the ideal, most cost-effective scenario would be to have someone inspect the intended storage location, to train the people who will be receiving the goods on how to properly handle the products and also to ensure the entire team responsible for valve installation – including not just the pipe fitters but also the electricians, etc – know which procedures to follow.
And perhaps more importantly, why they should be followed. That should include issues which might seem self-evident, such as pointing out the installation, maintenance, and operation (IMO) manuals, where instructions detailing correct valve installation can be found, etc. He also indicates that a reliable valve manufacturer will happily oversee, inspect during tag check out and also give advance training to those people responsible for installation. Peter’s key message to EPCs and end users is, therefore, that a little advance thinking and a more methodical, common-sense approach to testing and commissioning can assist in pre-empting valve issues. The result will be a smoother start-up. “Which won’t simply make life easier for the managers and engineers, the plant owner can start to generate revenues that much earlier too!”
Capital project commissioning and start-up
Valves, critical for brownfield and greenfield projects, demand careful attention for successful plant start-ups. David Anderson (Director, Flow Control Services, Valmet) kindly offers the following key recommendations:
1. Prioritize safety: ensure teams comprehend risks and good handling practices outlined in Installation, Maintenance, and Operation (IMO) manuals.
2. Communicate effectively: maintain a continuous line of communication with Valmet’s flow control service teams for successful handovers and support.
3. Plan storage adequately: Prevent deterioration with proper storage planning and follow Valmet Flow Controls BL’s detailed recommendations.
4. Prepare for contingencies: have commissioning spares ready, especially for projects in remote locations.
5. Check for signs of contamination or damage: inspect valves before and after installation to detect issues early.
6. Flush the pipeline carefully: Avoid damaging closing elements and seat surfaces during flushing.
7. Ensure correct installation: follow Valmet’s flow controls manuals for correct support, insulation, and expert supervision to guarantee proper installation.
8. Consider expert supervision: evaluate the cost versus the benefits of Valmet’s flow control expert supervision for faster issue resolution.
9. Identify control loop issues early: use Valmet PlantTriage for automated loop tuning and diagnostics.
10. Arrange training for operation and maintenance teams: ensure teams are prepared, especially for critical valves and intelligent devices.
11. Set up systems correctly from day one: ensure correct data and recommendations are in place, and utilize state-of-the-art tools.
12. Leverage data for optimal spares inventory: use data to build a spares inventory that matches operational needs while minimizing capital tied up in spares.
Meet Peter Börjesson
In line with his personal motto – don’t compromise with quality – Peter regularly shares his personal experiences and insights into valves and flow control in order to promote safety and efficiency. Recently for example he provided observations on flange guards for bolted joints for readers of Valve World India & Middle East. Peter Joined Valmet (formerly Neles) in 2018 and is currently Service Sales Project Manager in Valmet’s Flow Control business line.
About this Technical Story
This Technical Story is an article from our Valve World Magazine, March 2024 issue. To read other featured stories and many more articles, subscribe to our print magazine. Available in both print and digital formats. DIGITAL MAGAZINE SUBSCRIPTIONS ARE NOW FREE.
“Every week we share a new Technical Story with our Valve World community. Join us and let’s share your Featured Story on Valve World online and in print.”