Norgren offers a broad variety of smart components.
In this article, we will explore how the introduction of smart components is enabling OEMs to realise significant productivity and efficiency gains across a broad spectrum of sectors and manufacturing applications.
By Francesca Aryee-Dematteis, Product Manager EMEA, Norgren
With much focus on Industry 4.0, OEMs could be forgiven for thinking that the shift towards a connected future is one that requires significant capital expenditure to deliver the levels of flexibility and responsiveness required.
However, there is much to be said for an approach geared to extracting maximum value from existing plant equipment before considering a significant overhaul of the production line. Specified and used wisely, connected devices can monitor in real time the condition of components, recommend timely intervention in the form of predictive maintenance, and enhance overall plant performance and commercial competitiveness.
A number of factors will drive decisions around the integration of connected devices into existing production lines to ensure gains are maximised.
Integration with existing systems
In some applications, such as a system based around a PLC, any additional component installed must be able to run on them same protocols to communicate effectively with the PLC and so provide the required data. However, in other, open-source applications, components are available which are compatible with other existing in situ components, allowing OEMs to select the most appropriate devices for the given application.
Whatever the nature of the application, it is vital that the devices chosen are easy to install, integrate and use, and are able to provide rapid and relevant insight.
Components must also be modular
The key here is for the customer to start with the end goal in mind, being clear from the outset what they are trying to achieve – whether it is simply the monitoring of a specific production parameter, more detailed information on components and performance across an entire system, or somewhere inbetween. This will drive the selection of the correct connected device or devices.
Underspecification will not provide the required level of detail, while over-specification will result in higher financial outlay upfront, and the extraction of vast swathes of data which the customer may not have the time, need, or ability to manage. Specifying modular systems will also allow the customer to add or swap in new devices as and when application and monitoring requirements evolve.
Extracting value
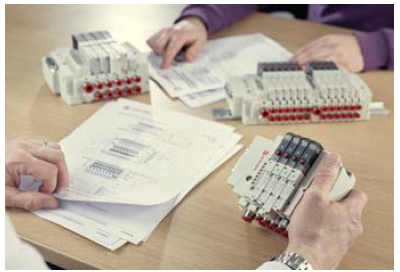
The third factor concerns the value that needs to be delivered by the investment in connected devices. Minimising downtime is almost always a priority, but other requirements may exist around reduced energy usage and carbon footprint, or the monitoring of specific performance parameters.
When it comes to downtime, the aim is that this should be minimised as far as possible. This is especially the case given that profit so often comes from the last few percentage points of production time. While it may be impossible to completely eliminate the risk of downtime, connected devices can help by providing insight into what issue is causing the downtime, as well as why it occurred, the remedial action that is needed, and other information, such as the spare parts needed to affect the repair. And, of course, this insight can help drive decisions around component specification and maintenance to further minimise the risk of downtime in the future.
Another area where connected devices can add significant value is in compressed air usage. There is still a commonly held misconception that because air is readily available all around us, compressed air is a free resource. But, of course, significant energy goes into compressing and processing the air to ready for use in pneumatic applications.
In Europe, it is estimated that around 10% of all industrial electricity consumption goes on producing compressed air. In an era of rapidly rising energy prices, any action to minimise this cost cannot be ignored. Leaks in compressed air systems are hard to avoid completely, even in facilities where systems are regularly checked. They are an inevitable result of the wear and tear to which systems are subjected and are often simply tolerated.
However, connected devices can rapidly identify problem areas where leaks are occurring and impacting on overall system efficiency and performance, allowing appropriate and rapid remedial action to be taken. Leak identification and remediation does not only have an immediate impact on energy usage in compressed air generation; best practice in this area can even allow for a reduction in compressor size, creating long-term financial savings.
The area of connected monitoring devices is one where innovation continues at pace especially when it comes to the visualisation of insights. These can range from simple onboard displays through to the provision of data to PLCs for network access, and even complete cloud based systems accessible via PC, tablet or smartphone, providing a complete overview of system performance – a single version of the truth.
Customers seeking to harness the benefits of connected devices would be well advised to articulate their needs to a systems partner, such as Norgren, who can recommend the best solutions for their requirements. The aim should always be to avoid the generation of data for data’s sake and instead focus on the provision of meaningful insight which can inform operational decision-making.
About the author
With almost a decade’s experience in the engineering sector, Francesca Aryee-Dematteis joined Norgren in 2016. In her role as IIOT and Controls Product Manager across EMEA, Francesca is responsible for the strategic roadmap of the business, together with the development of new product launches across the division. In addition, Francesca leads on several innovation projects, exploring new market opportunities.
About the company
As a company specialised in motion control and fluid technology, Norgren is ideally placed to unearth breakthrough engineering solutions and play an active role in important industry sectors that contribute to the quality and success of everyday life. Norgren offers insight, technical excellence and a collaborative approach to help their customers forge a brighter future.
About this Featured Story
This Featured Story is an article from our Valve World Magazine, September 2023 issue. To read other featured stories and many more articles, subscribe to our print magazine. Available in both print and digital formats. DIGITAL MAGAZINE SUBSCRIPTIONS ARE NOW FREE.
“Every week we share a new Featured Story with our Valve World community. Join us and let’s share your Featured Story on Valve World online and in print.”