The transformative potential of metal additive manufacturing (AM) is now well established. Engineers at IMI Critical Engineering have been exploring the role of 3D-printed valve parts since 2008, and the technology has really gathered pace within the business since the completion of a comprehensive in-house Design for Additive Manufacturing (DFAM) project in 2017, which enabled the deployment of AM technology across a wide range of industries and applications.
By Steve Freitas, IMI Critical Engineering
If AM continues to develop as expected, businesses will have more immediate access to high-performance components that provide a much lower total cost of ownership. Plant operators, for instance, will no longer be beholden to long lead times or need to hold extra inventory because localised industrial printers will eliminate the physical distances between OEMs and their end users. Among other benefits, this will make planned downtime and routine maintenance far more straightforward to complete without the threat of missed deadlines.
Beyond procurement and logistics, AM also allows manufacturers to implement and scale new valve design features for improved performance.¹ This technology can be used to make multi-stage flow control devices, including valve cages or disk stacks, flow distributors or diffusers, and multi-stage high-turndown control ball valves.
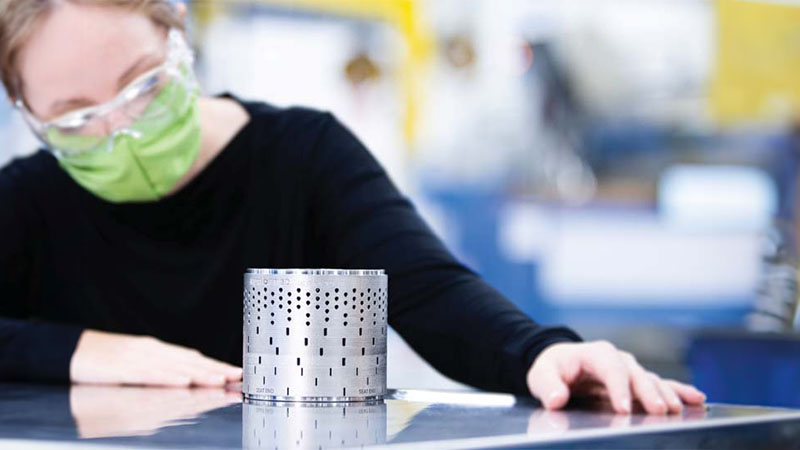
Tools only as good as the hands that wield them
AM must be applied with care, particularly within critical applications across the power, oil and gas, and petrochemical sectors. In theory, anyone with a 3D part scanner and printer can develop components using AM. However, achieving desirable results that improve system reliability and efficiency will very much depend on working with qualified and experienced suppliers. Working this way will ensure the technology is correctly applied for the part’s chosen application.
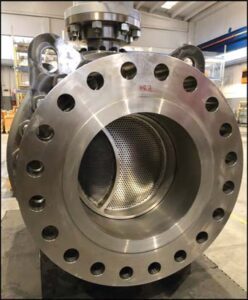
Responsible application of AM is therefore in need of a clear specification process, especially for organisations that are still relatively unfamiliar with its use in severe service. This is an issue IMI Critical Engineering has been working on for several years and, subsequently, we are now seeing more customers ask important questions about valve design options, materials, build qualification and certification.
Effective application of AM will always begin with a clear understanding of the problem. This may seem like a trite point, but it’s essential for creating a solution that fulfils its performance expectations and is compliant with industry standards. This is especially true for an oil and gas or petrochemical plant. The operating conditions and application requirements within each are not only unique but will often evolve over time with changes in plant output and fluid characteristics. The only thing ‘standard’ is that nothing is standard!
The AM part development effort should include a thorough assessment of the valve application. This will typically include a review of the original valve specification but also operating data, turndown requirements, duty cycle, and fluid conditions. It’s also useful to examine service history since frequent repair is a clear indication of severe service and the need for a new solution.
Corrosive service limitations
As it stands, AM parts cannot be certified for applications adhering to NACE MR0175/ISO15156. While there has been extensive research being conducted into the performance of AM materials in corrosive service, the situation is complicated by the metallurgical characteristics of LPBF materials, the variety of post-processing options, and the novelty of AM processes. Because of this, plant operators should always be made aware when the valve supplier intends to offer a part made using AM.
IMI has found some plant operators installing AM parts in corrosive service, but only on a case-by-case basis after completing a risk assessment. For AM to be specified correctly, this assessment should determine the potential consequences of failure both up- and downstream of the valve. Will the AM part be used in pressure containment or safety function, or will it be used for an internal flow control component?
Are there any pipe elements or processes that could be adversely affected by loss of operation? What contingencies exist in the system? Are there parallel or standby valves available? Does the facility require critical spares on site? This isn’t an exhaustive list but gives some idea of the questions posed by the introduction of AM in risk-averse environments.
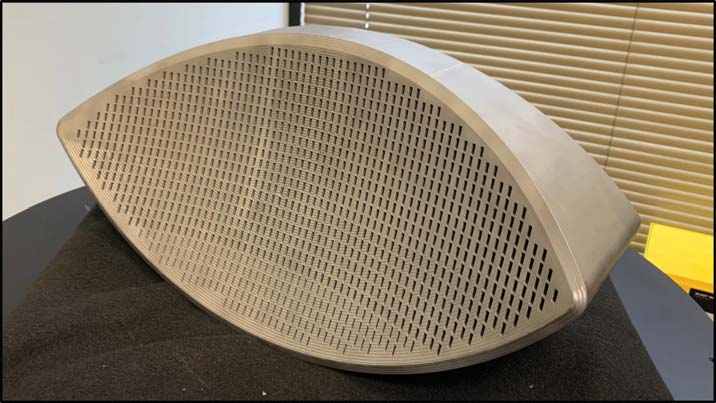
Post-processing and inspection options
Learnings from the assessment will be useful for establishing post-processing and inspection requirements for proposed AM parts. There are several heat treatment options for certain materials, such as UNS N07718. Hot isostatic processing can be used to minimise porosity.
Components with complex geometric features can also be scanned and compared to the original CAD design to determine if the warp has distorted during manufacturing, and flow control components can be flow tested to assess the accuracy of the build features.
There are many options for qualifying the AM build and measuring component properties including mechanical testing, metallurgical inspection, impact and corrosion testing. Each of these processes needs to be reviewed and documented in the build specification, inspection and test plan.
The key to finding the right solution: strong partnership
Unlike traditional manufacturing techniques, such as casting and forging, metal AM is developing rapidly. The build size of commercially available laser powder bed fusion systems (LBPF) has jumped from 300mm to almost 600mm in recent years. Dual- and quad-laser LPBF machines run faster and produce parts at lower cost. Many new materials have become available including cobalt chrome alloys and cemented carbides. There has also been significant progress in the development of industry codes and standards. Gas metal arc additive manufacturing (GMAAM), for example, has been proven in pressure boundary applications and accepted under ASME Section IX Code Case 3020.
The continuous development of AM technology restates the need for close collaboration between the plant owner or operator, the valve supplier and the AM manufacturer. This collaboration should begin with a review of the application by the plant owner and valve supplier, as described above. Consultancy should also extend to review of the design concepts, build constraints, post processing and inspection and test plan with the AM manufacturer.
IMI Critical Engineering has found that collaborative reviews often trigger new ideas which improve AM part quality and valve performance. The issues that can arise during development of AM parts can be complex, and the industry is still working towards something resembling best practice. This is why it’s essential to work with specialists that have a deep knowledge of control valves in severe service, as well as proven experience with the application of AM in these environments.
About the author
Steve Freitas is the R&D Director at IMI CCI. Steve has over 25 years of experience in the design, selection, and application of high pressure and high temperature valves in fossil power plants and oil & gas facilities. Steve also has over 10 years of experience in the development and application of Additively Manufactured flow controls.
References
bit.ly/3Kyp7GA
For more information, please visit: bit.ly/403xSOH