This article discusses the challenges of testing liquefied hydrogen valves, from addressing the unique properties of hydrogen to pioneering cryogenic testing methodologies.
Text and images by PK Valve & Engineering
Hydrogen liquefies at temperatures below -253°C, and liquefied hydrogen has more than 10 times the Boil-Off Gas (BOG) generation compared to LNG on account of its significantly low liquid density.
Additionally, the energy required to liquefy hydrogen is substantial, making the insulation performance of liquefied hydrogen valves and related equipment crucial. Leakage in the seat of liquefied hydrogen valves can lead directly to BOG, increasing the overall BOG generation of the entire process. This can have an adverse effect on the efficiency and performance of the entire process. Therefore, evaluating the reliability of sealing, not only external leakage, of liquefied hydrogen valves is highly important. This prompts the need to explain the testing methods for liquefied hydrogen valves that can assess both external leakage and seating reliability.
Currently, South Korea strictly restricts the production, transportation, storage, and use of hydrogen based on safety standards. Hydrogen can only be produced, transported, stored, and used only designated areas and facilities with special permits, known as regulated free economic zones. Consequently, even if optimal valves for liquefied hydrogen are developed, testing the valve performance in the extreme cryogenic conditions below -253°C (20K), which represent the actual operational environment, poses challenges. Limited facilities and research institutions dealing with liquefied hydrogen mainly use validated foreign valves due to these difficulties. For this reason, evaluating the performance of liquefied hydrogen valves becomes even more challenging.
In the process of developing liquefied hydrogen valves, our company has concurrently developed methods to test valve performance at temperatures below -253°C (20K), which reflect the actual operational environment.
Testing methods
There are various methods to test liquefied hydrogen valves, as follows.
- Traditional performance testing with Liquid Nitrogen (LN2). However, performance evaluation occurs at -196°C (77K), which does not represent the actual operational environment of liquefied hydrogen below – 253°C (20K), making accurate performance assessment impossible.
- While testing with extremely low-temperature fluids like liquefied hydrogen (-253°C), liquid helium (-269°C), and liquid neon (-246°C) is possible, without perfect precooling and insulation in the test facility, temperature and pressure control become impossible. Vaporization of extremely low-temperature fluids leads to increase in pressure, necessitating perfect exhaust facilities to release abnormal pressure in the test equipment. Additionally, the test location can also be problematic. Considering these challenges, our company has determined that testing using such extremely low-temperature fluids is not feasible.
- Attaching the valve to be tested to the process used in liquefied hydrogen production, storage, and transportation facilities for assessment in the real-world environmental assessment is a potential method. However, practical implementation of this approach is difficult, and it is challenging to evaluate the performance of the liquefied hydrogen valve alone using this method.
- Finally, the method developed by our company involves configuring a Cryostat using the G-M cryocooler to cool the valve directly or indirectly within an insulated chamber. This allows testing by cooling the temperature of the valve body itself or the test fluid to the extreme low temperature around -253°C (20K).
Innovative cryogenic testing facility
Our company has developed a testing facility capable of conducting cryogenic tests (-253°C or 20K) for hydrogen valves ranging in size from ∞” to 4”, utilizing G-M Coolers. This testing apparatus consists of two G-M Coolers, a chiller, a vacuum-insulated chamber, vacuum sensors, vacuum rotary pumps and turbo pumps, a vacuum helium detector, seven temperature sensors, and monitoring devices. In this setup, the liquefied hydrogen valve and G-M Cooler are placed within the vacuum-insulated chamber. The cooling generated by the G-M Cooler head is conducted directly to the test valve, cooling the temperature of the valve body to below or around -253°C (20K). Additionally, helium gas, serving as the test fluid, is supplied and pressurized independently through a separate line for the test.
The method employed by our company is designed to ensure safety, as the cooling and high pressure are contained, allowing for inspections and sampling test by customers, entrance. With the supply of electricity to the G-M Cooler, long-term temperature maintenance can be achieved, enabling accurate performance evaluations of the valve. Additionally, the use of a vacuum helium detector allows for precise leak detection, and since the valve is inserted into the vacuum-insulated chamber at the same location where actual vacuum insulation is applied, evaluation of the valve’s performance closely simulates real operational conditions.
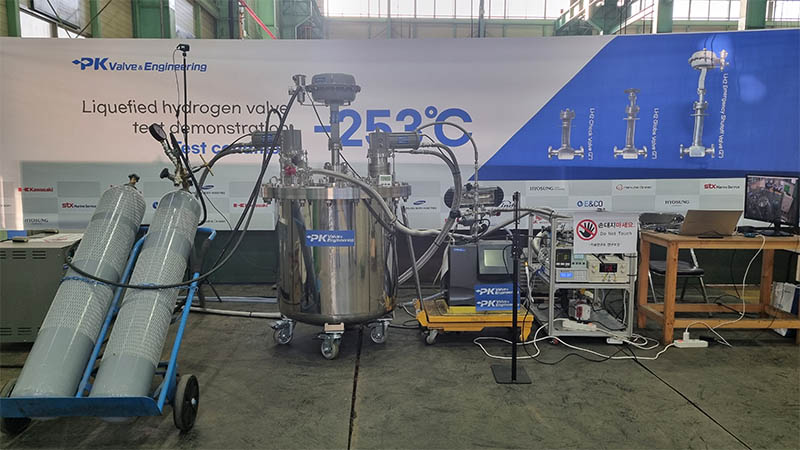
Furthermore, by modifying the cryostat, such as changing the insulation chamber and G-M Cooler cooling transfer method, it is possible to establish a facility for evaluating the performance of other types of liquefied hydrogen valves, such as safety valves.
As for drawbacks, the initial investment cost for the testing facility can be relatively high, and there may be difficulties in setting the vacuum insulation chamber and G-M Cooler cooling capacity based on the size of the test valve. Therefore, there may be limitations on the size of liquefied hydrogen valves that can be tested.
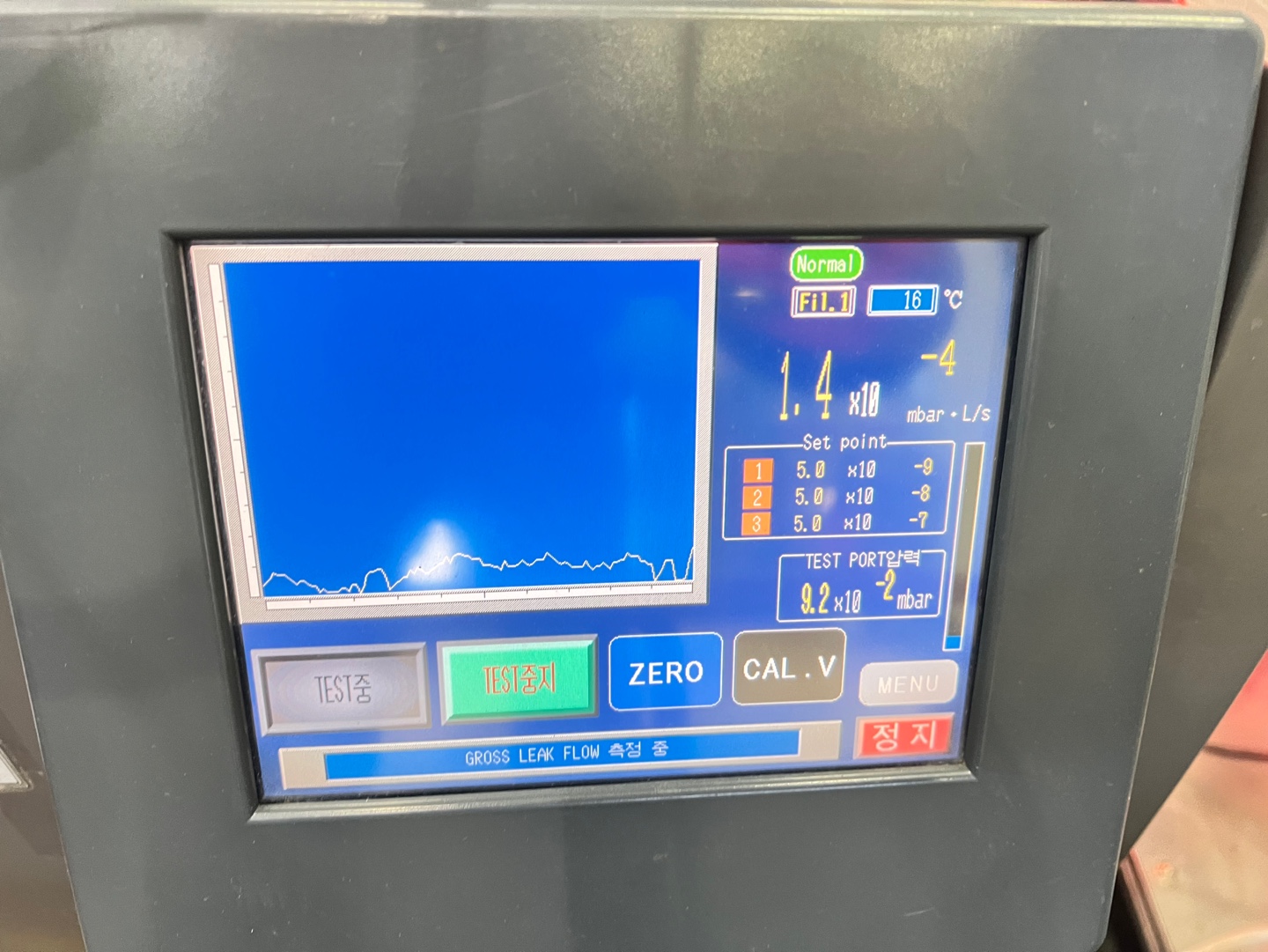
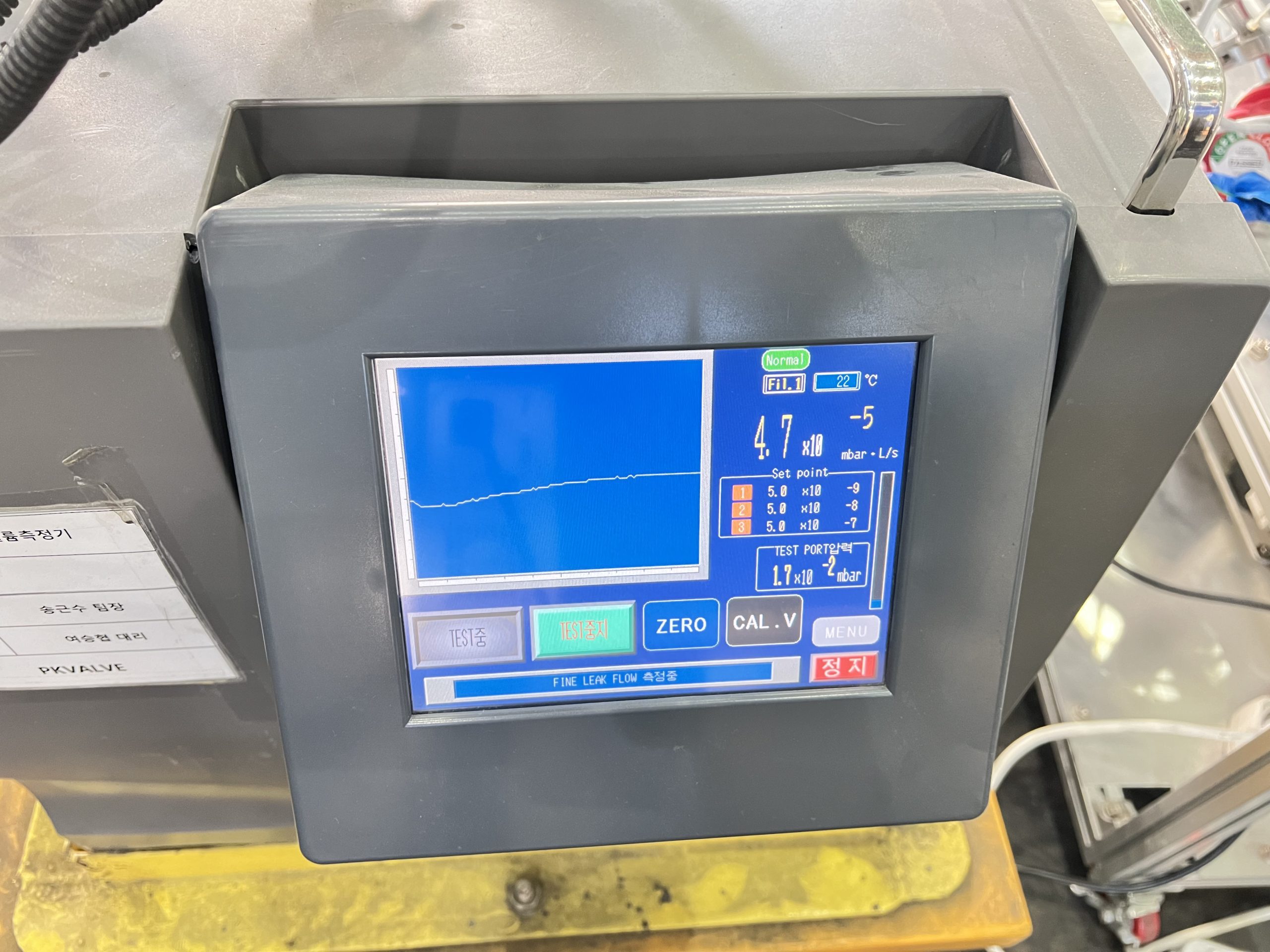
Performance evaluation and future considerations
Our company has successfully completed the performance evaluation of three types of 2-inch liquefied hydrogen valves (Liquefied Hydrogen Globe Valve, ESD – Emergency Shut-Down Valve, Lift Check Valve) under the monitoring of TUV SUD, a third-party certification body. In June and November of 2023, we conducted two demonstration events for liquefied hydrogen valve testing using the established testing facility. The demonstration focused on the 2-inch ESD Valve, with approximately 55 participants from around 20 organizations and companies, including Kawasaki Heavy Industries, Linde, KGS, KOGAS, SAMSUNG Heavy Industries, and Hanwha Ocean.
Based on the experience gained from the two demonstration events of liquefied hydrogen valves and the testing of liquefied hydrogen valves, the testing procedure for liquefied hydrogen valves has been established as follows.
Typical cryogenic tests are conducted using LN2 as a refrigerant in accordance with BS 6364, ISO 28921-1, and MSS SP-134. The stages of the test are structured as follows: ① Initial verification -> ② Cryogenic -> ③ Return to ambient temperature.
The testing procedure established by our company for liquefied hydrogen valves is conducted in the following sequence: ① Initial verification -> ② Cryogenic (-196°C) -> ③ Ambient (within the insulation chamber) & Cryogenic (-253°C) -> ④ Return to ambient temperature. Throughout all stages, helium gas is used as the test fluid, and leakage detection during stage ③ utilizes a Vacuum Helium Detector. When the valve body reaches -253°C or lower, significant vacuum pressure (typically below 0.1 Torr) is formed at the valve outlet (leakage point) due to the cooling process, making it impossible to measure leakage using conventional Mass Cylinder or Flow meters. Therefore, a Vacuum Helium Detector is employed for precise measurement of leakage, enabling accurate measurement of seat leakage.
Even when using helium gas as the test fluid, the test valve is cooled continuously by the G-M Cooler, which helps ensure rapid recooling and maintaining the test temperature.
Currently, in Korea, the leakage acceptance criteria for liquefied hydrogen valves are determined according to ISO 28921-1. However, it is suggested that stricter criteria for evaluating leakage in liquefied hydrogen valves need to be established, as explained earlier, since leakage in liquefied hydrogen processes can have significant impact on the efficiency and performance of the entire liquefied hydrogen process.
About the PK Valve CEO:
Youngchan Chun is the CEO of PK Valve & Engineering Co., Ltd. since 2021
About the author
Changwoo Jung is an engineer of the PK Valve & Engineering R&D Center, Where he has been focusing development of liquefied hydrogen valve process unit using in the transportation, utilization, storage of liquefied hydrogen.
About this Technical Story
This Technical Story is an article from our Valve World Magazine, April 2024 issue. To read other featured stories and many more articles, subscribe to our print magazine. Available in both print and digital formats. DIGITAL MAGAZINE SUBSCRIPTIONS ARE NOW FREE.
“Every week we share a new Technical Story with our Valve World community. Join us and let’s share your Featured Story on Valve World online and in print.”