Since its inception, Bonney Forge has been devoted to surpassing expectations and exceeding industry standards. For over 140 years, the company has achieved manufacturing excellence through detailed attention to customers’ needs and consistently producing some of the highest quality products in the industry.
By Angelica Pajkovic, Valve World
As a leading manufacturer of forged steel fittings and unions, branch connections, forged steel valves, cast steel valves, and bespoke engineered products, Bonney Forge has set a standard for the industry. Valve World recently had the pleasure of speaking with Bonney Forge’s Managing Director of BFE, Antonio Sonzogni; VP Product Engineering, Specialties and China Operations, Paul Heald; Vice President, Valve Products and Business Development – Southwest Region, Steve Thomas; and VP of Sales Engineering and Valve Projects, Tim Harrigan, to learn more about the company’s ongoing dedication to creating speciality solutions that optimize the end user’s experience.
Thinking outside the catalog
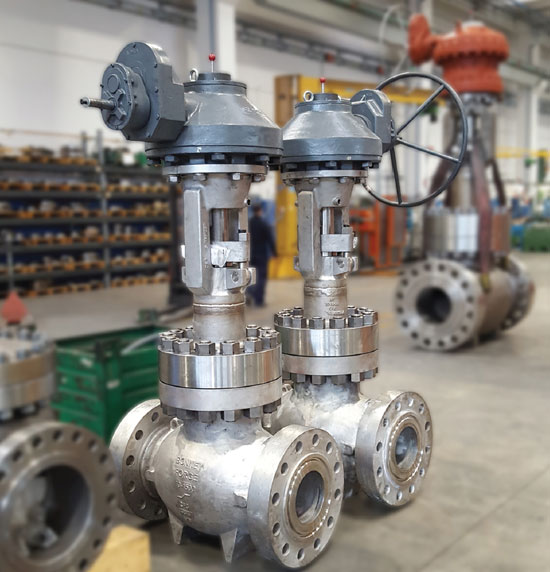
For anyone who works in the valve industry, whether as an Engineer or Project Manager, it is almost a certainty that sitting on the top shelf of their document library (or perhaps even their desk) is a well-worn and much-borrowed Bonney Forge valve catalog. Within the catalog’s 96 pages there is a wide variety of forged steel gate, globe, and check valves. Some of these are offered with special features such as bellows sealed bonnets, cryogenic extensions, and the Valvolet® extended body gate valve.
However, for a company that prides itself on innovation and in-house engineering and design, it is important to know that the catalog is only the beginning of the products they offer.
In addition to these valves, Bonney Forge also manufactures Cast Steel valves, Trunnion-Mounted ball valves, Pressure-Seal valves, Double-Block and Bleed valves, API 6A valves, Modular Valves, Blowdown valves, and Severe Service valves.
Walking through any of its manufacturing facilities this is immediately clear. It is common to see valves like a Class 2500 Y-Pattern Stop Check Pressure Seal with a globe valve by-pass made for an Egyptian Thermal Power Plant or duplex stainless steel trunnion mounted ball valves with stem extensions.
“We make everything from upstream and downstream valves, to valves designed to provide optimal performance in chemical, high-pressure, or high-temperature services. We are very versatile,” Heald stated.
“People see our standard list of products and think that is all we do, but we make a lot of specialty products that are not in our catalog. We work closely with our customers and get them the products they need. Having multiple factories helps us to do this well.”
When a customer comes to the company needing a specialty valve, Bonney Forge’s engineers are prepared to design a solution that will meet all the client’s criteria.
Another example of Bonney Forge specialty valve ingenuity is the API 10K 6A valves they designed and manufactured in collaboration with the customer for an offshore platform in Saudi Arabia. For this project, Bonney Forge was challenged to reduce the weight of the valves by 50% while maintaining the ability to perform in a harsh service and environment.
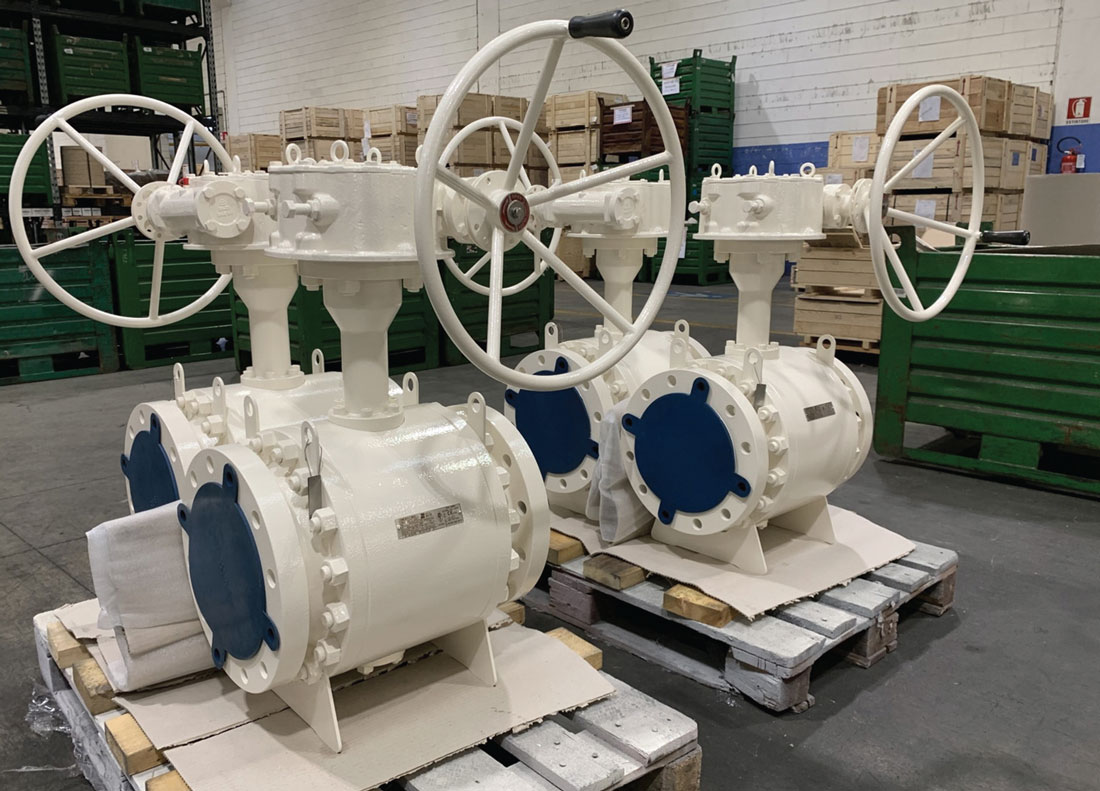
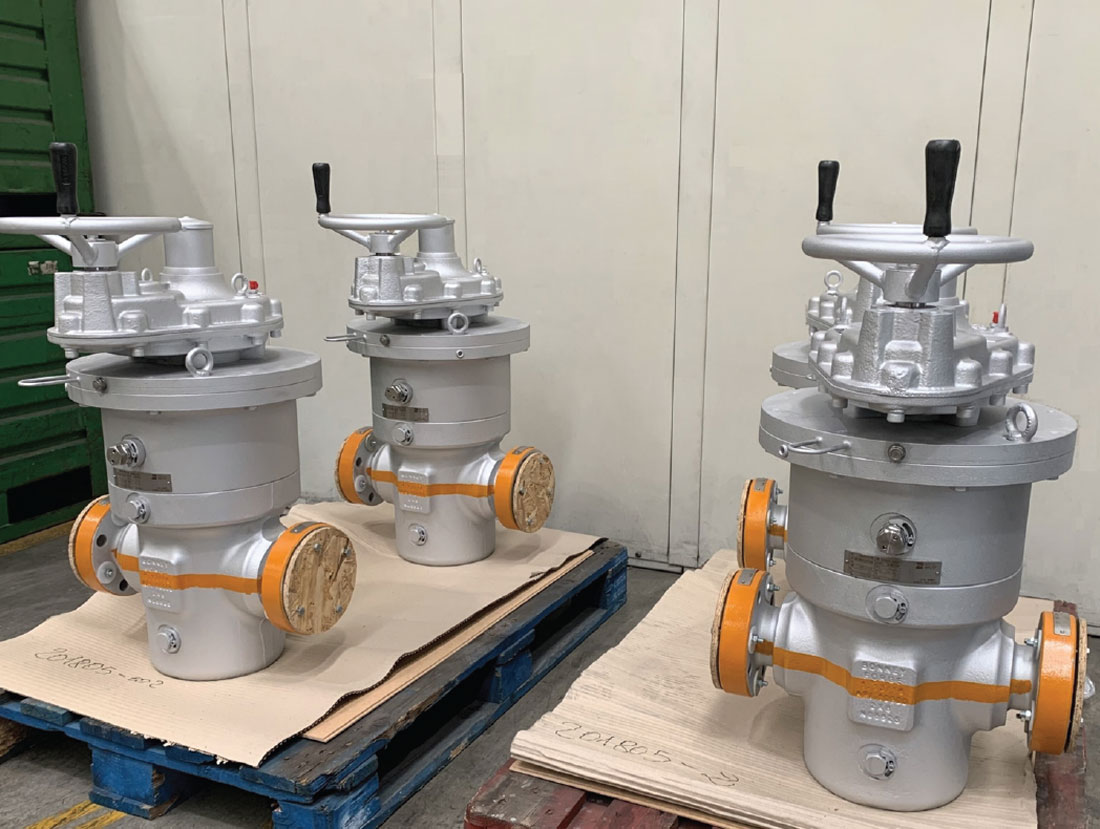
In Houston, we solve problems
Pressure-reducing devices, such as relief valves, can generate high levels of high-frequency acoustical energy downstream of the valve. At the Bonney Forge-owned WFI International facility in Houston, the company offers speciality engineered branch connections that go hand-in-hand with relief valves to mitigate severe service conditions such as acoustic-induced vibration, pressure drop, and temperature fatigue.
One of these products is the Bonney Forge/WFI Safety Relief Valve Vesselet® (SRVV®). Another speciality product engineered specifically for relief valve applications that are designed for both branch connection reinforcement and relief valve operation reaction forces. Additionally, there are flow and vibration analyses performed to fine-tune the performance to eliminate these occurrences to prevent the relief valve seating surfaces from vibrating damage over time.
It is important to know that each application is unique, and there is not a one-size-fits-all solution. Unlike valves and fittings, branch connections, such as the SRVV®, are specialty-engineered products. Therefore the engineers at WFI run full reinforcement calculations,
“We make a lot of
specialty products that
are not in our catalog.”
and in special situations, can also do a comprehensive investigation of their full piping system and validate the design.
Innovating on the Fast Track
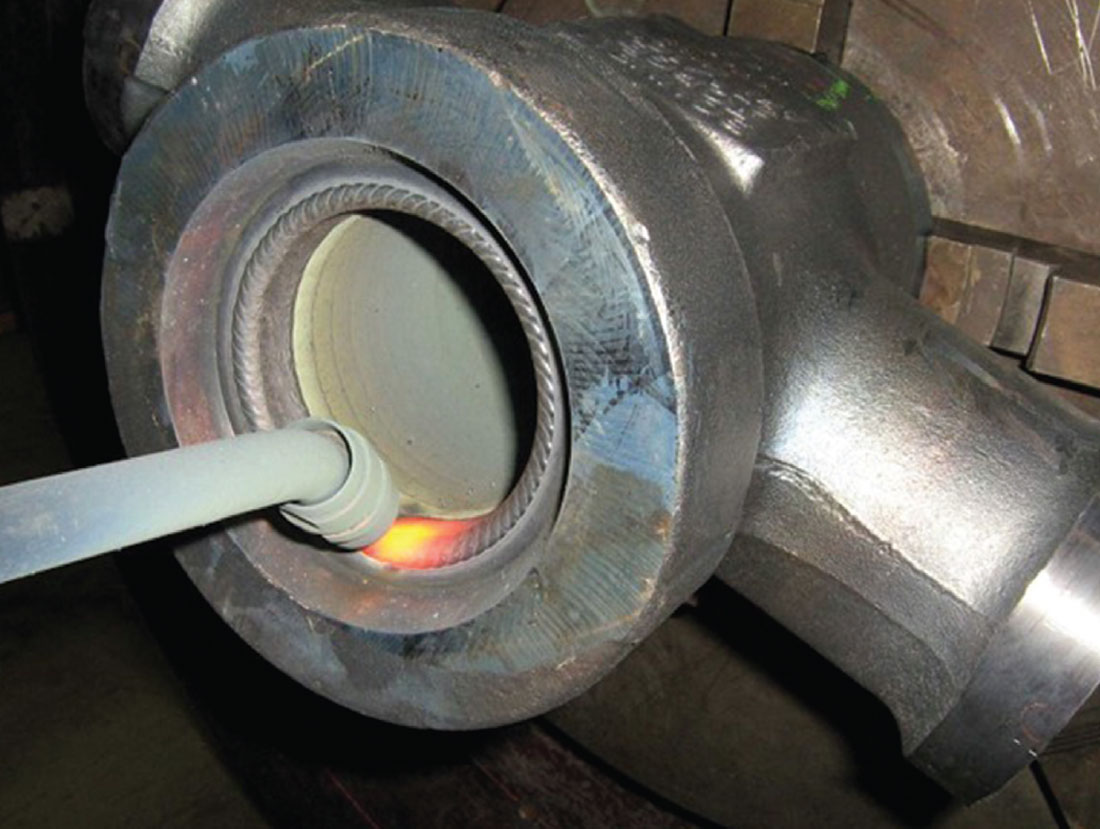
At Bonney Forge, they know that not every project goes according to plan and when the need for speciality valves arises without the luxury to wait on a full factory lead time, they have a solution: the Fast Track program. Designed with customers in mind who require a quick turnaround, from order to delivery, this service is ideal for end users who require a bespoke solution. One such solution is the deceptively simple slab-style gate valve made from a one-piece body featuring a metal-to-metal seal for high temperature and pressure. Recently Bonney Forge manufactured a large run of AISI 4130 API 10K gate valves with Inconel trim in 1/16” size.
“We find that some customers come to us when there are valve shortages on a project, or when they have very special valve specifications,” explained Heald. When a customer needs a valve made with speciality materials, Bonney Forge can do it quickly due to its large inventory. The company runs the program from both its forged facility and its cast facility, which aids with ensuring shorter lead times.
“We do not want to wait around for an order and then order materials to start production. We plan our raw material and finished-product inventory based off our history and the material changes we see in the industry.”
“We are always looking ahead for what could come down the line for us, so when we get an order, we can complete it quickly,” said Thomas.
A logical approach
When Bonney Forge provides products to the market, they approach it as pragmatically as possible, in all facets of the manufacture, proof test, and certification processes. Both inside and outside of the Bonney Forge product catalog, from a pipe fitting to the most complex modular valves, certification by third party is of utmost importance. That its products are tested by accredited, recognized laboratories holds weight with end users, so much so, Bonney Forge has leveraged its quality products for severe service where others may not.
“Each application is
unique and there is not a
one-size-fits-all solution.”
“There are reasons why we do more than the standards require, it is a sense of responsibility to the market, it is a sense of transparency between end user and manufacturer, and it is a sense of ownership. At the end of the day, this is our product with our name on it going out the door and we have the confidence that the product leaving any one of our facilities will out-perform any other product out there,” concluded Harrigan. Transparency is core at Bonney Forge. One way it deliver that is through critical paths – timelines for its customers and, ultimately, end users on product production, testing, and shipping.
“We provide critical paths so our customers’ field engineers, planning personnel, and receiving teams all know when to expect product on-site so that they can plan effectively. On-site work is important, the more upfront understanding we can provide our customers, the smoother the work goes,” said Thomas. Whether the product is complex or simple, critical paths are provided on projects and are available at any time.
Bonney Forge believes in:
• Continuously improving quality, processes and customer service.
• Eliminating delays, errors, and defects in materials and workmanship.
• Providing customers with access to statistical evidence that quality is incorporated in its products and production processes.
• Requiring suppliers to provide statistical evidence of quality in products and process capabilities.
• Sharing with the organization the cost of poor-quality in products and services.
• Driving out fear and bringing problems to light for all to see.
• Working together to address specific problems and establish goals and solutions as a team.
• Controlling manufacturing processes which determine the final cost and quality of its products.
• Removing barriers which stand between employees and their pride of workmanship, and implementing ongoing training, supervision and employee development programs.
• Good housekeeping, which reflects on the company, its operating philosophy, and its people.
• Encouraging a corporate culture which will reinforce the objectives of its mission on a day-to-day basis.
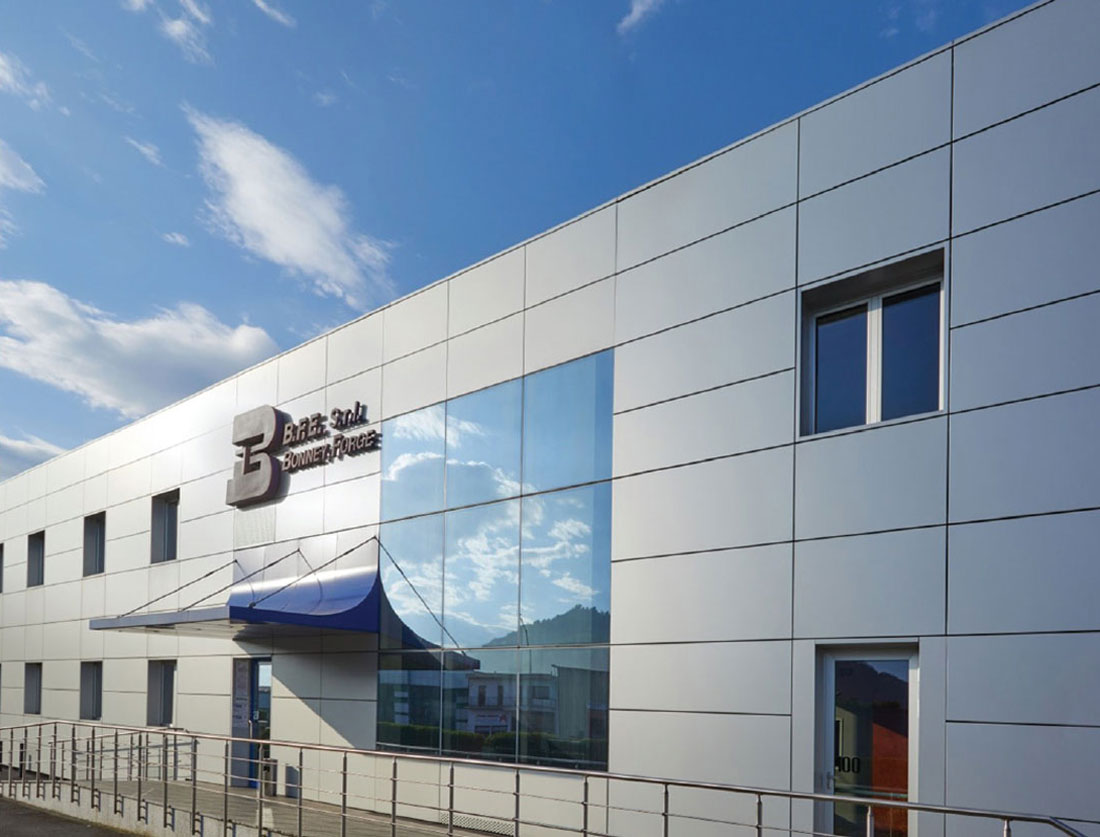
Looking forward
Bonney Forge will continue to grow, invest, and improve the company’s operations in every aspect; this includes capacity, efficiency, productivity,
and quality. “Manufacturing requires continuous improvement, and we invest in our people and facilities every year. That will continue our success throughout the years,” said Heald.
As part of this commitment, the company is always looking forward to the future of the industries they serve and new industries where Bonney Forge can have an impact with its manufacturing innovations.
“We are constantly considering where there may be a gap in the industry, and we are finding ways to fill those gaps,” Sonzogni added.
In the ever-changing world looking to lower emissions, this includes LNG, hydrogen, Carbon Capture facilities, solar, renewable fuels, and nuclear. Bonney Forge will be at the forefront of each of these, ready to provide valves and other products that exceed these industries’ requirements.
“We always felt we were on the front end of many of the major industry changes and have been consistently able to produce the products that are required to address them,” added Thomas.
About this Featured Story
This Featured Story is an article from our Valve World Magazine December 2022 issue. To read other featured stories and many more articles, subscribe to our print magazine. Available in both print and digital formats. DIGITAL MAGAZINE SUBSCRIPTIONS ARE NOW FREE.
“Every week we share a new Featured Story with our Valve World community. Join us and let’s share your Featured Story on Valve World online and in print.”