Batu Valve Türkiye
The adoption of pig ball valve technology in the oil and gas industry represents a significant step forward in pipeline maintenance, offering a more efficient, safe, and environmentally friendly alternative to traditional pigging systems.
By Zahra Farrokhi, Batu Valve Türkiye
The oil and gas industry is seeking innovative pipeline maintenance technologies that balance increasing energy demands with environmental consciousness. Pigging systems, crucial for pipeline integrity and cleanliness, are a key focus area (Energy Sector Innovations, 2020; Sustainable Pipeline Management, 2023).
Traditional pigging systems, while effective, have drawbacks such as extensive infrastructure, complex maintenance, and environmental concerns. Space limitations in offshore platforms and urban areas have further highlighted the need for more adaptable and sustainable alternatives (Spatial Challenges in Urban and Offshore Pipeline Maintenance, 2023).
Pig Ball Valve systems have emerged as a promising solution, consolidating the functions of traditional pigging systems into a compact, efficient unit. These systems enhance operational efficiency and minimize environmental impact (Pipeline Efficiency Reports, 2022). As the industry prioritizes sustainability, the adoption of advanced technologies like Pig Ball Valves is set to reshape pipeline maintenance practices.
Industry adoption examples
- Offshore projects: The adoption of BATU Pig Ball Valves in offshore projects, particularly in the North Sea, represents a significant stride towards modernizing traditional pipeline operations in challenging environments (Regulatory Compliance in Offshore Operations, 2021). The BATU Pig Ball Valve system addresses challenges by offering a compact design that reduces the spatial footprint traditionally required for pigging operations (Technological Advancements in Pipeline Maintenance, 2020).
- Transcontinental pipelines: Operators of transcontinental pipelines prioritize efficiency and reliability (Transcontinental Pipeline Maintenance Innovations, 2022). Adopting the BATU Pig Ball Valve system allows them to reduce the frequency and complexity of maintenance operations (Pipeline Operation Innovations, 2021). This trend reflects an industry-wide move towards technologies that can withstand the demands of managing extensive pipeline networks across diverse geographical terrains.
- Refinery upgrades: Refineries in regions like the United States and the Middle East seek to improve operational safety and efficiency (Case Studies on Refinery Upgrades, 2021). Transitioning to BATU Pig Ball Valves marks a significant upgrade over traditional pigging systems (Pipeline Technology Training and Development, 2021). These newer systems reduce operational downtimes and enhance safety measures, leading to shorter maintenance windows and fewer safety incidents (Safety Improvements in Pipeline Operations, 2021).
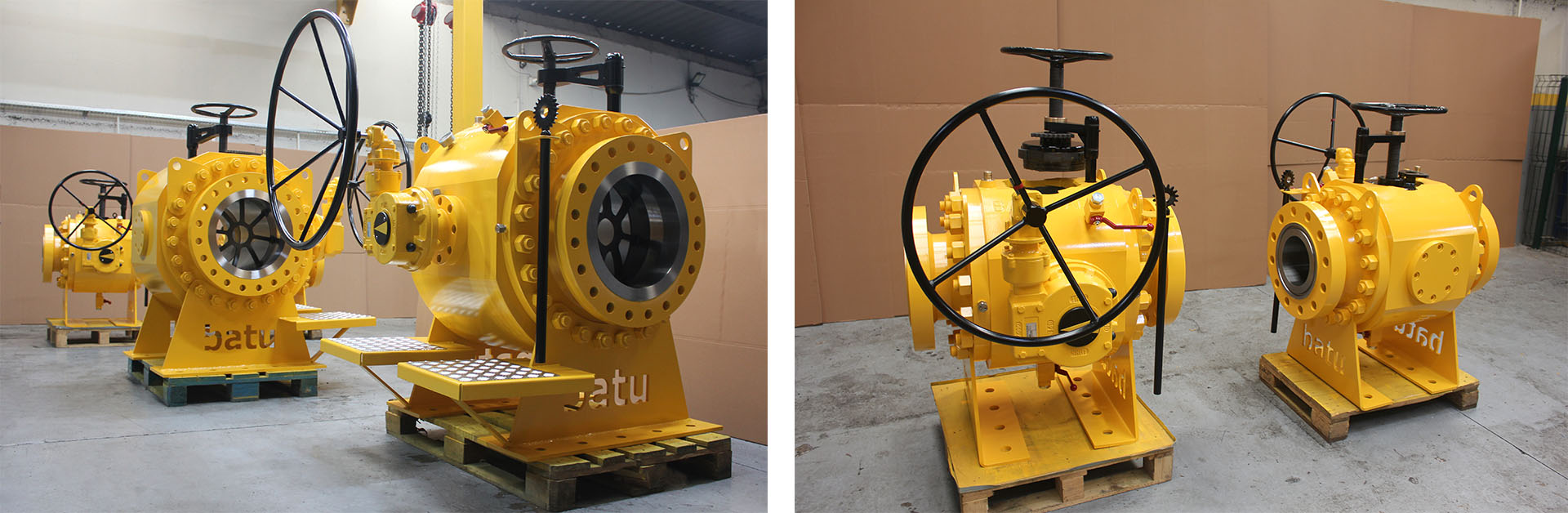
Overview of traditional pig launcher systems
Traditional pigging systems have been a cornerstone of pipeline maintenance for decades, utilizing barrel-style launchers and receivers to propel ‘pigs’ through pipelines (Pipeline Technology Journal, 2021). These systems require significant infrastructure, including large barrels and intricate valving, which can be costly to install and maintain (Operational Economics in Pipelines, 2021).
From an operational perspective, pigs are pressurized within barrels before being inserted into pipelines. This process necessitates extensive infrastructure and space, which can be particularly challenging in offshore or urban environments where space is limited (Spatial Challenges in Urban and Offshore Pipeline Maintenance, 2023). Additionally, manual handling of pigs during insertion and retrieval poses safety risks to operators, who may be exposed to potential injuries or accidents (Pipeline Technology Training and Development, 2021).
Environmental concerns also arise from emissions released during pigging processes, contributing to greenhouse gas emissions and potential regulatory compliance issues (Environmental Impact of Pipeline Technologies, 2023). As urban and offshore settings increasingly demand more efficient use of space and stricter environmental controls, traditional pigging systems face compatibility challenges, driving the need for innovative solutions that can address these concerns (Innovative Pipeline Solutions, 2023).
Introducing pig ball valve technology
Pig Ball Valve technology represents a revolutionary advancement in pipeline maintenance, consolidating the functionalities of launching and receiving pipeline pigs within a single, streamlined ball valve unit. This integrated design eliminates the need for separate and bulky launchers and receivers, significantly reducing the physical footprint and simplifying pipeline system architecture (Pipeline Efficiency Reports, 2022).
The Pig Ball Valve enables the insertion and retrieval of pigs through the same valve that controls the pipeline’s flow, maintaining flow control and pressure integrity without compromising the pipeline’s primary function. This multifunctional capability facilitates a seamless transition between operating modes, enhancing operational flexibility and reducing downtime (Innovative Pipeline Solutions, 2023). Adopting Pig Ball Valve technology yields several operational advantages. Its streamlined design reduces the need for manual handling of equipment, mitigating safety risks associated with conventional pigging methods. Additionally, the closed system design minimizes potential environmental risks, such as leaks or emissions during the pigging process, aligning with increasing environmental regulations and sustainability goals (Environmental Safety in Pipeline Operations, 2022).
The ease of use and reduced infrastructural demands of Pig Ball Valves make them ideal for challenging environments like offshore platforms or urban settings, where space constraints are significant concerns. This adaptability is particularly valuable as the industry prioritizes sustainability and seeks less intrusive methods of pipeline maintenance, enabling more efficient, safer, and environmentally friendly operations (Sustainable Pipeline Management, 2023).
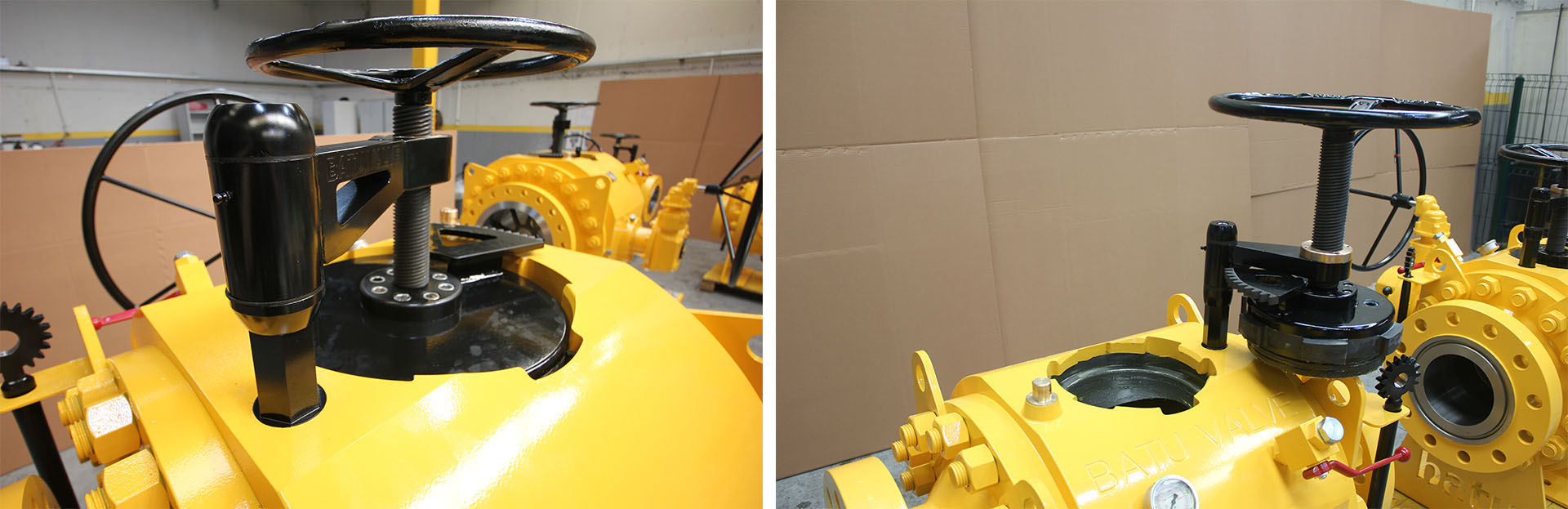
Advantages of pig ball valves
- Compact and efficient design, reducing spatial and infrastructural demands
- Reduced installation and maintenance time, crucial for continuous operations
- Enhanced safety due to fewer parts and decreased accidents
- Environmental benefits from sealed valves that reduce emissions
- Cost savings over the lifecycle due to reduced downtime and operational expenses
- Customizability and versatility to accommodate various pigs
Disadvantages of pig ball valves
- Higher initial investment compared to traditional systems
- Limited track record and reliability data due to being a newer technology
- Need for specialized knowledge and training for installation and management
Comparative analysis
Operational efficiency and time savings: Pig Ball Valve systems reduce maintenance time by up to 40%, minimizing downtime and increasing productivity. (Global Pipeline Efficiency Group, 2023) Cost-effectiveness: Up to 30% reduction in operational costs over five years and a 50% decrease in downtime, leading to significant cost savings. (TechnoOil Energy, 2022) Environmental impact: Sealed design of Pig Ball Valves results in a 25% reduction in emissions compared to traditional pigging systems. (Journal of Sustainable Oil and Gas Engineering, 2024)
The future of pipeline maintenance
Pig ball valve technology offers a paradigm shift in pipeline maintenance, addressing many of the limitations inherent in traditional pigging systems. Its design promotes operational efficiency, safety, cost-effectiveness, and environmental sustainability. These attributes make it a superior choice for contemporary pipeline operations, especially in sectors where space, safety, and environmental regulations are of paramount concern. While the initial investment and need for specialized training could be seen as drawbacks, the long-term benefits in reduced operational costs and enhanced safety and environmental compliance present a compelling case. The widespread adoption of such innovative technologies is crucial as the industry moves towards more sustainable practices and seeks to balance operational demands with environmental stewardship.
For operators and stakeholders considering the transition to pig ball valves, the evidence supports that this technology is not just a viable alternative but a necessary evolution in pipeline maintenance that aligns with future industry standards and regulatory demands. As the oil and gas industry continues to navigate the challenges of meeting energy demands while minimizing environmental impact, the adoption of advanced technologies like pig ball valves will play a critical role in shaping a more sustainable and efficient future.
About the company
BATU Valve is a pioneering force in the oil and gas industry, revolutionizing pipeline maintenance with its innovative Pig Ball Valve technology. Founded by a team of experienced engineers and industry experts, BATU is committed to developing cutting-edge solutions that address the complex challenges faced by modern pipeline operators. To learn more about them visit https://www.batuvalve.com.
About this Featured Story
This Featured Story is an article from our Valve World Magazine, June 2024 issue. To read other featured stories and many more articles, subscribe to our print magazine. Available in both print and digital formats. DIGITAL MAGAZINE SUBSCRIPTIONS ARE NOW FREE.
“Every week we share a new Featured Story with our Valve World community. Join us and let’s share your Featured Story on Valve World online and in print.”