A control valve featuring a unique patented design provides precise flow control using a three-petal mechanism.
By Leire Colomo Zulaika, AMPO POYAM VALVES
The energy industry is at a pivotal juncture where sustainability has taken centre stage. The global reshaping of the oil and gas sector is challenging but essential, not only for the environment but also for energy security. Valve manufacturers now operate in an industry that measures its sustainability through three key pillars: Environmental, Social, and corporate Governance (ESG).
To address the needs of the energy transition, AMPO POYAM VALVES developed the Dilating Disk™ Valve, a control valve featuring a unique patented design that provides precise flow control using a three-petal mechanism. This valve type boasts ultra-low seat and operational torque, resulting in a significant reduction in actuator size and a seamless transition to zero-emission electric automation.
Correct valve sizing essential
Process plant engineers conduct sizing analyses to determine whether a selected control valve has the appropriate flow capacity and operating characteristics to provide the intended process control. Typically, end-user control valve sizing is done in accordance with international standards, such as ISA and IEC. During the sizing process, plant engineers must avoid choosing an undersized valve, as this would result in process inefficiencies and reduced production. Conversely, an oversized valve also presents disadvantages, including poor process control, the need for larger actuators and unnecessary additional weight and cost.
The Dilating Disk™ Valve (DDV) is ideal for control valve applications and is particularly well suited to perform the same functions as globe valves. It also represents a significant advancement in valve design as its unique geometry allows it to deliver a CV equivalent to a much larger globe valve. The centralised flow stream produced by the aperture enables superior process control while providing full port operation with zero pressure drop.
Reduced actuator force
Globe valves, commonly used for process control, typically require significant thrust to operate. This high thrust requirement leads to larger, heavier and more costly actuators.
Reducing the actuator force requirements of control valves is crucial for lowering costs, emissions and complexity. A smaller actuator enhances the efficiency and reliability of control valves. Although butterfly valves and ball valves often cycle from fully closed to fully open on a 90-degree quarter-turn, they still require significant operating torque and produce fluid effects that make them less than ideal for process control applications. The patented design of the DDV addresses the challenge of reducing torque requirements while providing precision control and tight shutoff through the use of a ring gear. This innovation brings to market a quarter-turn motion to cycle from fully closed to fully open.
Additionally, the movement of the three valve petals further minimises torque requirements as the three petals open and close perpendicular to the flow of process fluids, encountering minimal flow-related resistance.
The ring gear is an efficient means of transmitting torque into the functional motion of the valve. Just a quarter-turn of the valve stem is required for a dynamic range of process control, and the valve’s gearing ensures minimal energy loss. These features allow customers using the valve to use much smaller, lighter and more energy-efficient actuators, thereby reducing cost, complexity and energy consumption while increasing reliability and efficiency.
The advantages of the new controlling mechanism have a ripple effect on its environmental footprint. Its lighter and more compact design requires fewer raw materials to produce. In a supply chain-constrained world, reducing raw material consumption is vital.
Reducing emissions
There are numerous potential sources of fugitive emissions within the oil and natural gas sector. Fugitive emissions arise when connection points are improperly fitted or when seals and gaskets begin to deteriorate. Variations in pressure and mechanical stresses can also cause components or equipment to emit fugitive emissions. These emissions do not include devices that vent as part of normal operations, such as gas-driven pneumatic controllers or pumps, provided the natural gas discharged from the device’s vent is not classified as a fugitive emission. According to an OEM Climate Roadmap, methane venting constitutes 12.2% of the total methane emissions from production. Control valves are a significant source of methane venting. Additionally, fugitive emissions account for 10.9% of all methane emissions from production, with control valves again being a major contributor.
In the majority of applications, the natural gas industry employs pneumatic controllers to provide the necessary energy and control signals. Pneumatic controllers are automated instruments used to maintain process conditions such as liquid level, pressure, pressure differential and temperature.
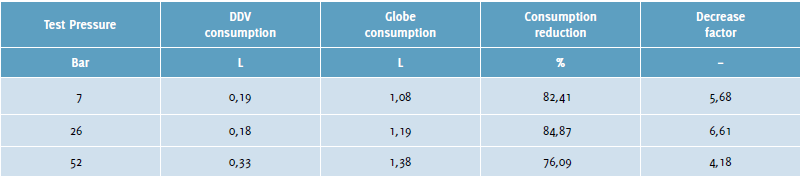
The results indicate that the DDV increases flow rate compared to globe valves on a size-by-size basis, validating the observed performance enhancement. On the same line, the results showed that the valve vents approximately four to six times less air (or methane in the field) than a traditional globe valve.
Reducing ice formation in control valves
The deployment of the DDV in gas lift service commenced in early 2021, focusing on its installation in clean natural gas service across multiple operations. The valves were installed as gas lift injection control valves across various client assets. These installations exposed the valve to multiple operations teams, automation and programming teams and maintenance teams.
Similar to water injection, produced gas from the well may be re-injected to raise the reservoir pressure. This is achieved through low- and high-pressure compression onboard the vessel. Even without the need to maintain well pressure, the overwhelming majority of areas globally now limit the amount of gas flaring that can occur. It is often less costly to re-inject the gas rather than install a pipeline to transport the gas from the vessel. Nearly every FPSO will have gas compression systems used explicitly for gas injection. Those that do not utilise gas injection will still have compression systems for transporting gas off the vessel. Most existing fixed and tension leg platforms, semi-submersibles and spars are used for both oil and gas production, with both components being sent onshore for further processing.
The produced gas can be used to improve product flow up the wellbore to the surface, a process known as gas lift. In these applications, the produced gas is compressed and routed into the outer annulus of the wellbore. It enters the well stream through a series of gas inlets in the inner production conduit. This reduces the density and the hydrostatic head of the well stream fluids, increasing recovery. Gas lift is used where reservoir pressure is relatively low and in deepwater developments where reservoir drive pressure is countered by high hydrostatic head.
A major downside to the reliability of traditional control valves in gas lift applications is hydrate formations, or icing, which can have a negative impact on flow characteristics and in many cases, cause the valve to freeze shut. This phenomenon is caused by the Joule-Thompson Effect, which defines the relationship between a drop in pressure and a corresponding drop in temperature. Since the primary function of a control valve is to produce a pressure drop, the corresponding drop in temperature can cause any water molecules present to crystallise in combination with hydrocarbon molecules, which accumulate within the valve body of a traditional globe valve.
With a DDV, this phenomenon does not cause the valve to freeze shut due to the direct flow path of the fluid and the lack of fluid interactions with the solid structures of the valve body. By directing the fluid down the centreline of the pipe, while still providing the required pressure drop, any hydrates that may form are directed harmlessly downstream until the pressure recovers, and the hydrate molecules return to a liquid phase.
The presence of hydrate or ice formations and total uptime directly determines the revenue generated by each gas lift well. The Dilating Disk™ Valve does not cause ice formations and never freezes the valve shut, providing a significant revenue benefit for gas lift injection applications. By adopting a collaborative approach, AMPO POYAM VALVES is actively working with customers to achieve their net-zero targets, working with the industry and its end-users towards more efficient and effective operational sustainability.
About the author
Leire Colomo Zulaika currently holds the position of Innovation & Technology Development Director at AMPO Valves in the Basque Country, Spain. She holds a double degree engineering in Industrial Engineering and Production and Operations Management from Mondragon University in Spain with an executive master’s in Business Administration. Leire has more than 20 years in the industry, with the last 18 working in the Oil & Gas industry at AMPO POYAM VALVES.
About this Technical Story
This Technical Story is an article from our Valve World Magazine, April 2025 issue. To read other featured stories and many more articles, subscribe to our print magazine. Available in both print and digital formats. DIGITAL MAGAZINE SUBSCRIPTIONS ARE NOW FREE.
“Every week we share a new Technical Story with our Valve World community. Join us and let’s share your Featured Story on Valve World online and in print.”