Wafer type monoblock valves outperform traditional ball valves in industrial fluid control, offering superior space efficiency, cost-effectiveness, and performance in high-pressure environments while promoting sustainability and operational reliability across various industries.
By Zahra Farrokhi, Batu Valve Türkiye
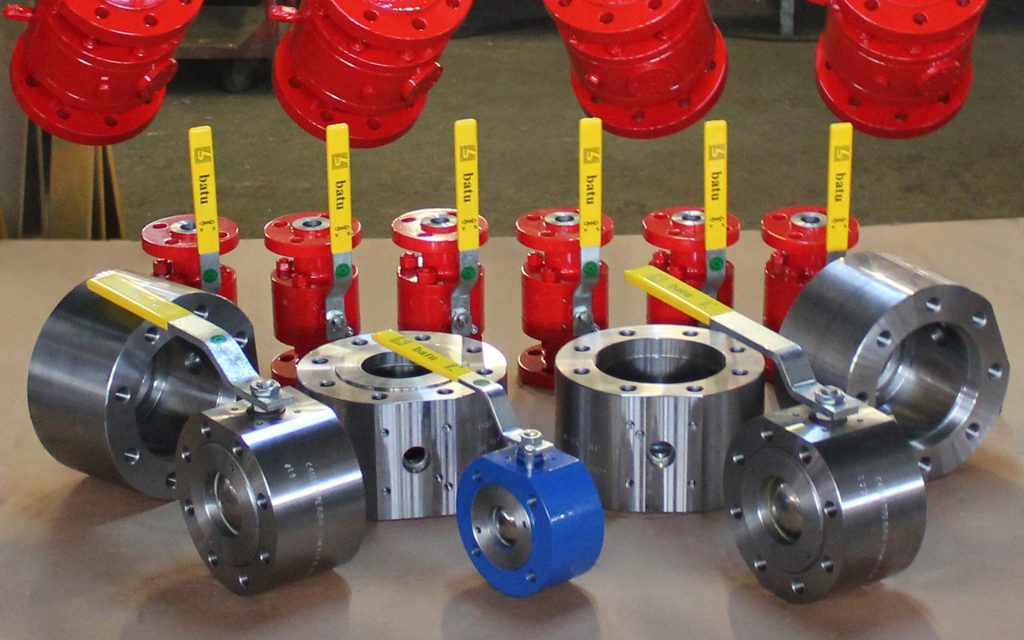
Valve selection is crucial in optimising industrial fluid control systems, directly impacting operational efficiency, cost and safety. While ball valves have long been an industry standard, wafer type monoblock valves are emerging as a superior alternative in many applications. This article explores the advantages of wafer type monoblock valves, focusing on their space efficiency, cost-effectiveness and high-pressure performance. Through industry data and case studies, we’ll demonstrate how these innovative valves are reshaping fluid control across various sectors.
Wafer type monoblock valves
Wafer type monoblock valves feature a compact, lightweight design for installation between flanges. Their single-piece body construction minimizes potential leak paths, making them advantageous in high-pressure and high-temperature environments. The simple design reduces installation complexity and maintenance requirements.
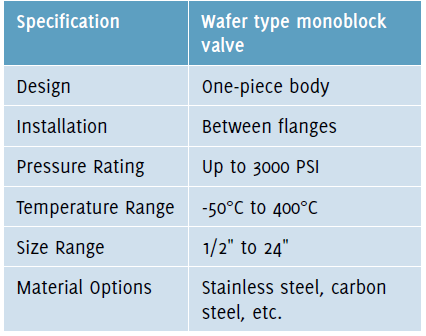
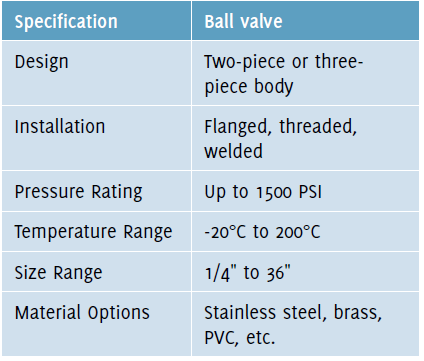
Ball valves
Ball valves are known for quick shut-off capabilities and ease of operation. They consist of a spherical ball with a hole through the center, controlling fluid flow by rotation. While versatile, ball valves generally require more space for installation compared to wafer type monoblock valves.
Comparative analysis
- Space efficiency
Wafer type monoblock valves excel in applications where space is limited. Their compact design typically requires 30-50% less space than equivalent ball valves, making them ideal for tight piping systems and confined industrial spaces. - Installation and maintenance costs
The single-piece design of wafer type monoblock valves simplifies installation, reducing alignment issues and the need for multiple components. This design also leads to lower transportation and handling costs. Maintenance is less frequent and less costly compared to ball valves, which often require more complex disassembly and part replacement. - Performance in high-pressure environments
Wafer type monoblock valves are engineered to withstand higher pressures, often up to 3000 PSI, compared to ball valves’ typical 1500 PSI limit. This makes them more suitable for applications in oil and gas, chemical processing, and other industries with high-pressure conditions. - Material and construction
Material selection and construction quality significantly affect valve durability, corrosion resistance, and overall performance. Wafer type monoblock valves, often constructed from high-grade stainless steel and other alloys, provide superior corrosion resistance and mechanical strength. Their simpler construction with fewer parts reduces the risk of wear and leakage compared to the more complex ball valve design. - Performance metrics
Flow coefficient (Cv) and pressure drop are crucial metrics in evaluating valve efficiency. Wafer type monoblock valves generally exhibit higher Cv values and lower pressure drops compared to ball valves, resulting in more precise flow control and improved system efficiency. - Lifetime and durability
The robust, one-piece design of wafer type monoblock valves contributes to a longer operational life by reducing potential failure points. This design advantage often results in less frequent replacement and maintenance compared to ball valves with more moving parts and seals. - Environmental impact
Environmental considerations are increasingly important in valve selection. Wafer type monoblock valves, often constructed from recyclable materials, have a lower environmental footprint compared to ball valves. Their simpler construction requires less energy during manufacturing and generates less waste. - Sustainability
Sustainability is a critical factor in modern industrial design. Wafer type monoblock valves offer better sustainability metrics due to their longer lifespan and higher recyclability. This makes them a more environmentally friendly choice for industries aiming to reduce their carbon footprint and improve overall sustainability.








Case studies
- Case study 1: Oil & gas industry application
In a recent project within the oil and gas industry, the use of wafer type monoblock valves led to a 25% reduction in installation costs and a 15% increase in system reliability due to fewer leak points and lower maintenance requirements. This project demonstrated the valves’ superiority in high-pressure environments where traditional ball valves were previously used (Brown and Green, Journal of Industrial Valve Design, 2017) - Case study 2: Chemical processing plant
A chemical processing plant replaced ball valves with wafer type monoblock valves in its high-temperature pipeline system. The result was a 20% decrease in operational downtime and a 30% reduction in maintenance costs over a two-year period (Martinez and Rivera, Journal of Pressure Valve Technology, 2016).
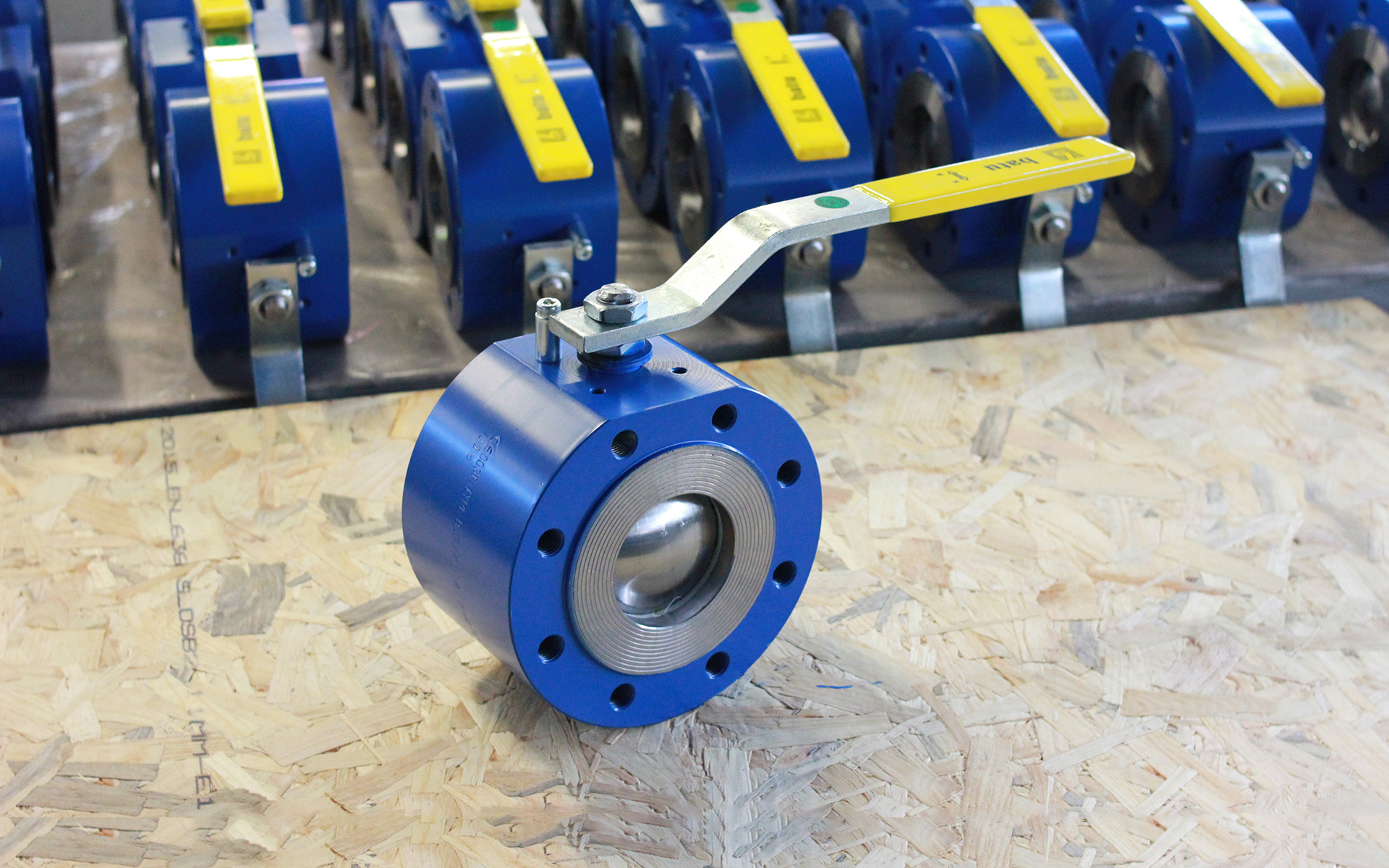
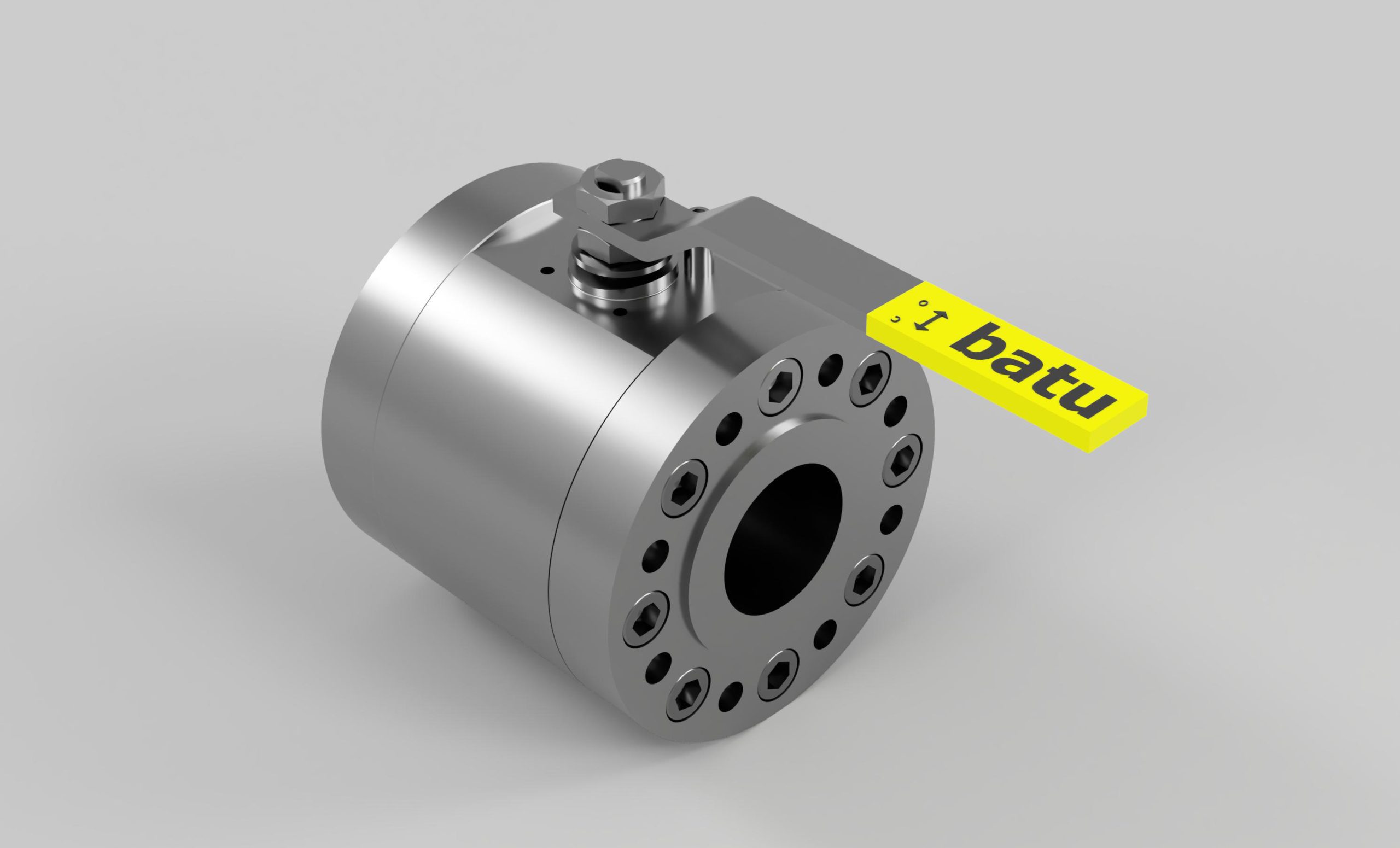
Future trends and innovations
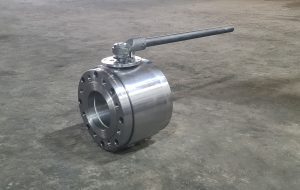
Ongoing advancements in materials and design are expected to further enhance the advantages of wafer type monoblock valves. Future developments may include:
- Integration of smart technologies for real-time monitoring and predictive maintenance
- Use of advanced composite materials for improved performance in extreme conditions
- Focus on eco-friendly materials and energy-efficient manufacturing processes
These innovations are likely to strengthen the position of wafer type monoblock valves as a leading choice in sustainable industrial practices.
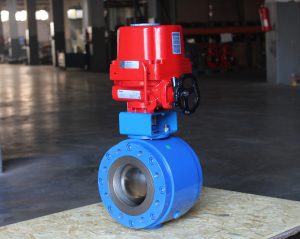
Conclusion
Wafer type monoblock valves offer significant advantages over ball valves in terms of space efficiency, cost-effectiveness, operational efficiency, durability, and environmental impact. Their robust design and superior performance in high-pressure environments make them valuable across various industries. As demand grows for reliable, sustainable, and easy-to-maintain valve solutions, wafer type monoblock valves are poised to play a crucial role in modern fluid control systems. Industries adopting these valves can expect benefits including reduced operational costs, improved system reliability and a smaller environmental footprint.
About the company
Batu Valve Türkiye is a manufacturer specialising in innovative valve solutions for the energy, oil, gas and petrochemical industries. With a focus on LPG applications, the company offers a range of valves designed to meet the demands of high-pressure and high-temperature environments, ensuring safe and efficient operation in LPG stations and other gas infrastructure projects.
About this Technical Story
This Technical Story is an article from our Valve World Magazine, October 2024 issue. To read other featured stories and many more articles, subscribe to our print magazine. Available in both print and digital formats. DIGITAL MAGAZINE SUBSCRIPTIONS ARE NOW FREE.
“Every week we share a new Technical Story with our Valve World community. Join us and let’s share your Technical Story on Valve World online and in print.”