Yara, a global leader in crop nutrition, ammonia and essential industrial solutions, is working hard to decarbonise its activities, optimise throughput and minimise downtime. The integration of third-party software into its digital production platform has helped to improve control valve performance.
Text and images by Perry Jaspers, Yara, and Jules Oudmans, UReason
Unlocking the power of data for operational excellence
In 2019, Yara launched the Digital Production Platform (DPP) initiative based on Amazon Web Services (AWS). The DPP serves as the digital core to securely capture and analyse new and existing data to gain insights. Combined with applications built on top of the DPP, Yara accelerates operational excellence by optimising throughput in a safe and sustainable way, reducing energy consumption, minimising plant downtime and improving safety and quality control across production sites, spanning locations in Europe, Asia Pacific, South America and North America. By integrating data from Distributed Control Systems (DCS) and Condition Monitoring Systems, the DPP enables production optimisation, digital operations and data-driven maintenance strategies across its 23 production sites worldwide.
DPP is Yara AnomaliSense™, a cloud solution developed by Yara to detect rare events and anomalies in process operations. Powered by patent-pending technology, Yara AnomaliSense™ seamlessly scales AI models across a diverse range of assets, prioritising alerts according to risk. The application harnesses generative AI to mine technical drawings, industry standards and internal failure databases, feeding advanced machine and deep learning models that accurately forecast issues and detect anomalies. Built on a robust technology stack, the platform is engineered for peak performance and scalability, and it integrates effortlessly with key third-party diagnostic tools and machine learning (ML) models accelerating the identification of root causes and enabling faster corrective actions. To further enhance efficiency, reduce false positives, and automate root-cause analysis, Yara has integrated UReason’s Control Valve App (CVA) with the DPP.
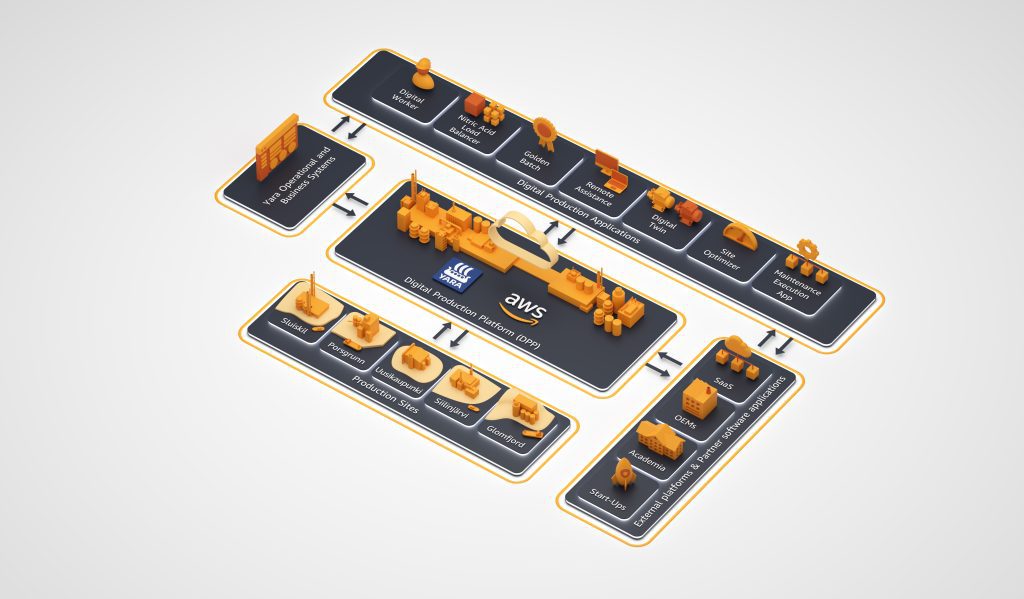
Enhancing predictive maintenance with the Control Valve App
The CVA continuously monitors control valves, positioners and actuators using only setpoint and positioning data, without the need for expensive high-performance positioners. The CVA is vendor agnostic and currently continuously analyses data from control valves of vendors like PARCOL, Emerson/Fisher, Baker Hughes, METSO, AST etcetera. This model – and type – independent approach allows Yara to analyse valve performance across a diverse range of control valves deployed globally using one tool:
Increasing technical reliability and minimising unplanned downtime are key priorities for Yara. Through real-time online condition monitoring by the CVA, asset health awareness of control valves is significantly improved and turnaround scoping for control valves is based on the ‘remaining useful lifetime’ as per CVA-provided information. Besides informing the users on controller performance the CVA identifies issues such as packing/bellow wear, broken spring diaphragm, stiction issues, stuck operation and positioner drift and calibration. The goal is to predict future asset conditions, determine optimal maintenance actions and ultimately achieve zero unplanned downtime.
The digital production platform: a foundation for predictive maintenance
Yara’s DPP is more than just a data lake; it is the backbone of Yara’s digital transformation. By standardising data collection and exchange, the DPP eliminates redundant data flows, ensuring that third-party applications and internal digital tools seamlessly interact with production data. In Yara, predictive maintenance is defined as maintenance triggered automatically by data insights. Whether it is crossing an alarm threshold or adjusting setpoints dynamically, the DPP enables a structured approach to predictive maintenance. This standardised approach ensures scalability and sustainability across all production sites.
Transforming raw data into actionable insights
Simply storing data in a data lake is not enough to drive optimisation. Yara’s approach involves transforming raw data into actionable insights using Yara AnomaliSense™. This proactive deployment of AI signals a broader industrial shift from reactive maintenance to a continuous, data-driven approach that empowers staff at every level. As digital transformation accelerates, innovations like Yara AnomaliSense™ are poised to become critical drivers of operational efficiency and competitive advantage for Yara.
An analogy can be drawn between data processing and chemical production: just as raw materials require refining to maximise their value, raw data must be processed and analysed to unlock actionable insights. Yara AnomaliSense™ serves as a user-friendly interface, offering predictive maintenance alerts, operational insights and integration with existing workflows.
Integrating third-party applications for holistic asset management
Yara’s vision for Yara AnomaliSense™ extends beyond in-house solutions; it integrates with third-party specialised software to provide deeper insights. The integration of the CVA is a testament to this approach, offering in-depth diagnostics on valve health and performance.
In the fertiliser production industry, control valves play a critical role in regulating flow, pressure and temperature across various processes. Any malfunction, such as valve stiction, positioner offsets or excessive wear, can lead to inefficiencies, increased energy consumption and unplanned downtime.
Integrating continuous control valve diagnostics, provided by the CVA, offers a data-driven approach to proactively detect and address valve-related issues, optimising plant performance and reducing operational risks.
A typical rollout of the CVA at Yara sites involves the collection of technical information of the control valves (setup of the CVA Asset Base) followed by the set-up of data collection from the DPP. At the Yara Ferrara site, the first Yara site that adopted the CVA, the rollout started in April 2023 and the site was up and running with the app in a few weeks. Following the successes of the CVA the monitoring scope was increased.
Deploying and validating the Control Valve App
The CVA provides a detailed overview of control valve health, detecting issues such as positioner offsets and valve stiction. By visualising ideal operational patterns, sites can identify and rectify deviations efficiently. The app also provides historical performance tracking, enabling maintenance teams to assess the impact of corrective actions over time.
For example, at Yara’s Ferrara site, the CVA detected stiction issues in July and August. After maintenance interventions, control performance improved significantly, extending the valve’s lifespan and enhancing process efficiency. This process was repeated across the entire monitored set of control valves and was a key validation step during the site’s onboarding and joint valve performance reviews with the UReason team. Post-intervention, the CVA provided feedback on the health of the serviced control valves, confirming the accuracy and value of its predictive models.
The future of valve diagnostics: AI and advanced analytics
The CVA is undergoing continual enhancements. During the roll-out at Yara, for example, language support was added for Italian and Norwegian users to ease the onboarding and bridge language gaps. Functional advancements planned for the next two years include:
- Integration with AVEVA Connect, a cloud-based industrial data management platform that enhances the PI system’s capabilities by integrating PI data
into the cloud and enabling broader accessibility for a large group of industrial customers. - New analytical models, offering deeper insights into valve performance and predictive failure detection, also including data available in Asset Management Systems like Yokogawa PrM, Emerson AMS, Honeywell FDM etcetera.
- Valve benchmarking and anomaly detection, further enhancing predictive maintenance strategies across the growing monitored asset base.
- Large Language Model (LLM) integration, providing users with technical guidance based on their install base and reasoning based on time-series data received and generated by the CVA.
Conclusion
The integration of Yara AnomaliSense™ and the Control Valve App within Yara’s Digital Production Platform showcases the power of data-driven maintenance. By combining advanced anomaly detection with real-time valve diagnostics, Yara and UReason are setting a new standard for predictive maintenance in industrial operations. Continued innovation and collaboration aim to achieve zero unplanned downtime and optimal asset performance in the years ahead. A key takeaway from this deep integration is that technology alone does not guarantee success — the real impact comes from integrating digital solutions into existing workflows and fostering a cultural shift toward data-driven decision-making.
About the authors
Perry Jaspers is a solution-oriented Master of Science in electro- mechanical domain with over 24 years of experience in electrical & automation/instrumentation domain and project management in EPC and end user organisation. Activities ranging from building renovation over data centre engineering & construction to the fertiliser industry for the past 18 years.
Jules Oudmans is one of the co-founders of UReason, a provider of technology products and services enabling companies to quickly create intelligent applications that automate complex reasoning on large quantities of real-time data and events. Jules is a seasoned professional active in the field of operational intelligence and real-time analytics, specialty application areas Fault Management and Predictive Maintenance.
About this Technical Story
This Technical Story is an article from our Valve World Magazine, April 2025 issue. To read other featured stories and many more articles, subscribe to our print magazine. Available in both print and digital formats. DIGITAL MAGAZINE SUBSCRIPTIONS ARE NOW FREE.
“Every week we share a new Technical Story with our Valve World community. Join us and let’s share your Featured Story on Valve World online and in print.”