FR VALVE from Suzhou, China, specialises in ball valves. They are committed to offering high-quality products to their clients and focus on developing and incorporating escape technology into their designs to stay on top of their engineering. Valve World spoke with Mr Guohong Zhang, General Manager, to discover more about their innovative strategies and engineering technology.
By Alexandra Kist, Valve World
As a long-time valve man, Mr Zhang started his career as an engineer at a valve company just fresh out of university. Contrary to most of his fellow engineering students, he dreamed of working in a valve production workshop, instead of spending most of his time in an office. Since then, he has spent upwards of thirty years in the valve industry. In 1999, Mr Zhang left the valve company he was working at and established his own. “Back then, other than the company I left, there was only one other quality ball valve company in China. I realised that we needed to improve the quality of Chinese valves to be able to enter into European and American markets. As I had already worked with ball valves, I chose to specialise in them and so they became the sole focus of this company.”
The company is located in Suzhou, China, in the heart of ‘Valve Valley.’ Nowadays, the city’s map is speckled with valve manufacturers, located approximately 100 kilometres from Shanghai; a stark contrast to the state of the Chinese valve market in 1999. With their mission to become the world’s leading ball valve manufacturer, the company focuses on forged steel-ball valve products and services. FR Valve’s current featured products are trunnion mounted coke valves, cryogenic trunnion mounted ball valves, and ring ball valves.
Their products are manufactured from ASME, ASTM and API-compliant forged steel, and they can meet ball valve requirements of up to 56” and API 20,000 psi.
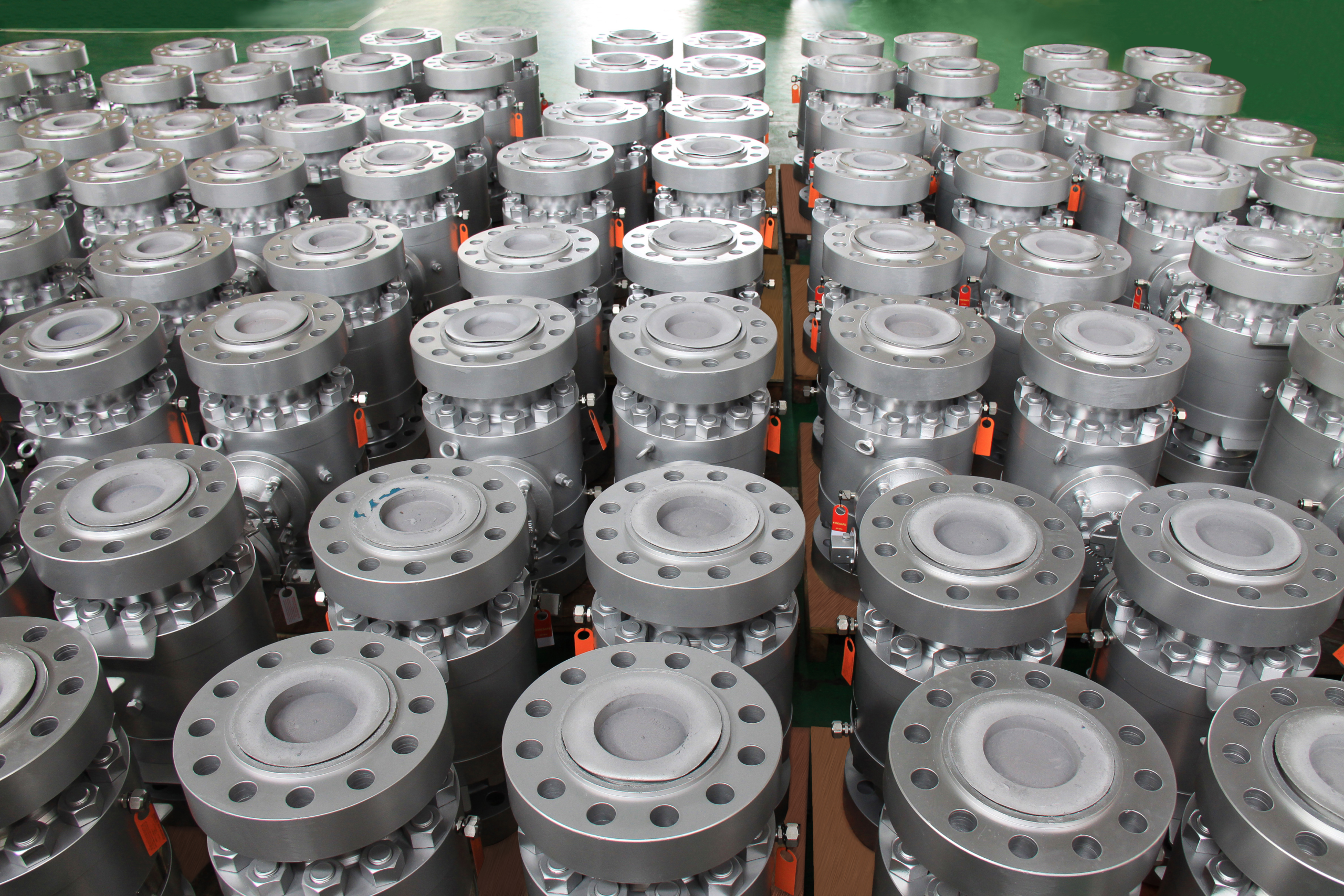
Reliable partnerships
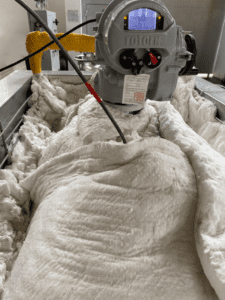
A valve enthusiast at heart, Mr Zhang speaks passionately of his family-owned company FR Valve, which is set to celebrate its 25-year jubilee next year. One of the company’s main priorities is customer satisfaction. They achieve this through designing and manufacturing high-quality and high-performance ball valves. One aspect of their partnership attitude is their determination to offer both pre- and post-sale qualified technical support. Customers value FR Valve’s commitment to support, ensuring opportunity for long-lasting relationships
“We have been working on including escape technology in our valve design. It’s also being used in SpaceX.”
and in-house knowledge bespoke to each project. Loyalty between customer and supplier/manufacturer offers stability and familiarity with a customer’s projects and applications. This, along with their competitive prices, forms a solid base for the company’s success.
Staying ahead of the game
Mr Zhang shares what sets FR Valve apart in today’s competitive market. “Lots of Chinese valve manufacturers, as well as those from other countries, focus on expanding their manufacturing capabilities. Instead, we prioritise technological developments and improving our product quality. We are confident in our manufacturing capabilities and are now able to release lots of new designs and innovative engineering.” Mr Zhang specifically mentions that FR Valve has expanded their range of ball valve products, which they specialise in. They offer a variety of floating and trunnion ball valves, and have developed specially designed valves. The company’s growth is based on the improvement of the staff’s engineering background and their R&D department is continuously on the lookout for the most advanced materials and technology. Because of this, FR Valve has developed specially designed valves, such as cryogenic and low-temperature service ball valves, metal-seated ball valves, double block and bleed assemblies, coke valves, ring valves, and ball valves for subsea application. FR Valve uses forged steel for their products instead of castings.
“As per API standard, floating ball valves usually don’t possess a double block and bleed function, but our floating ball valves do. It is a completely new product. Our valves’ torque are much lower than that of other floating ball valves, which greatly reduces actuator costs for our clients. “We have been working on including escape technology in our valve design. It’s also being used in SpaceX,” Mr. Zhang adds proudly. With this technology, a special compartment is created to catch all possible fugitive emissions. This way, it is easier to collect and dispose of the material, or even test it. This will help us enter the hydrogen market. “We have decided to include this feature on all of our valves,” says Mr Zhang. “Even though our method of testing ensures that our products are of a high quality, there is even less chance of fugitive emissions becoming a problem now.”
“We test all of our valves with high-pressure gas to ensure that our products are of an especially high quality.”
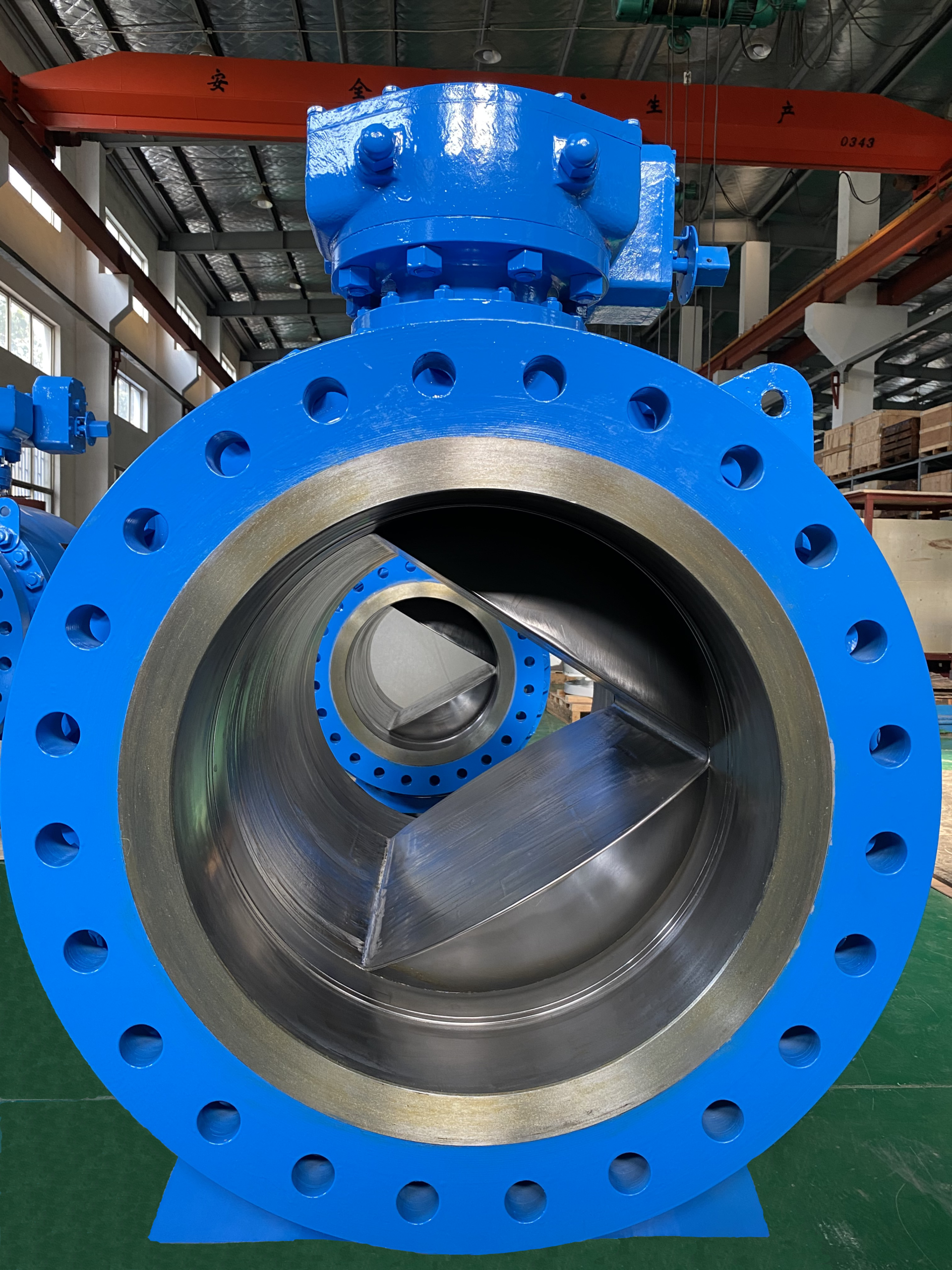
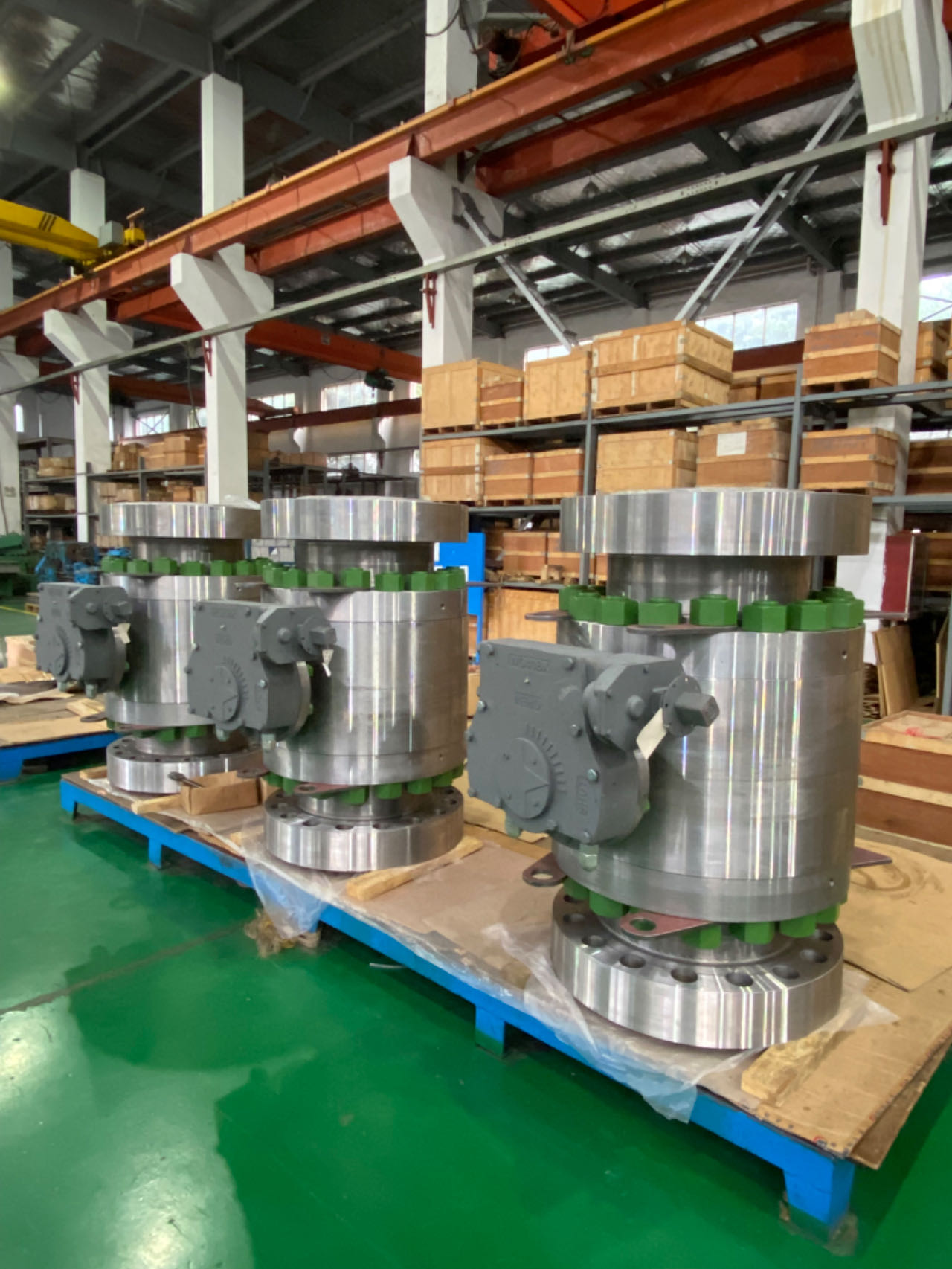
Assessing quality
FR Valve takes special care when it comes to testing their products. “We have improved our tests in a special manner, which means that we use new technology and have redesigned the entire testing process. To guarantee our customers that our products are of the highest quality, we even invite them to witness the testing process by themselves,” Mr Zhang explains.
“As per Shell specification, ISO 15845, API 6A and 6D, valves are required to be tested with water, but we test with high-pressure gas.” By doing this, FR Valve acknowledges that all leakage matters, not matter how little. With gas, it’s easier to find whether there is any leakage at all. In oil and gas refineries, sometimes the end-user may find that their valves are in fact leaking, even though that batch has been tested with water. By testing with high-pressure gas, we ensure that this is not a possibility for our valves. The customer is welcome to verify this for themselves by witnessing the testing procedure. While testing valves with water generally suffices, Mr Zhang explains that for some applications, it’s more important that the valve doesn’t leak. “If we don’t use gas for testing, it usually isn’t a problem for oil and gas refineries and water pipelines, as the emissions are not necessarily dangerous.
However, if the valve is used for liquid hydrogen, for example, the consequences could be much worse. Those absolutely have to be tested with high-pressure gas.” By using this testing method for any and all valves, FR Valve not only saves workshop space, but also assures their clients that their products adhere to higher standards than required.
Mr Zhang explains that this testing strategy is not entirely without risks. “Not all companies dare to test this way. It can be dangerous, because if the product is not of the highest quality, it can explode.” He adds that normally, one out of every one hundred valves should undergo testing, but that clients sometimes have extra requirements for their orders. “This happened to us in 2011, when our client asked us to test 10% of the valves they ordered, and with high-pressure gas, nonetheless,” says Mr Zhang. “This was new to us, but we quickly noticed we had nothing to worry about. Because the desired outcome of this way of testing is more difficult to achieve, we adopted this procedure as our standard way of testing to ensure that our products are of an especially high quality.” An additional benefit of this strategy is that FR Valve’s own standards for their products are often higher than the customer’s. FR Valve encourages their subcontractors to uphold the same product standards as them. “As we improve our engineering, we also help them to improve theirs.”
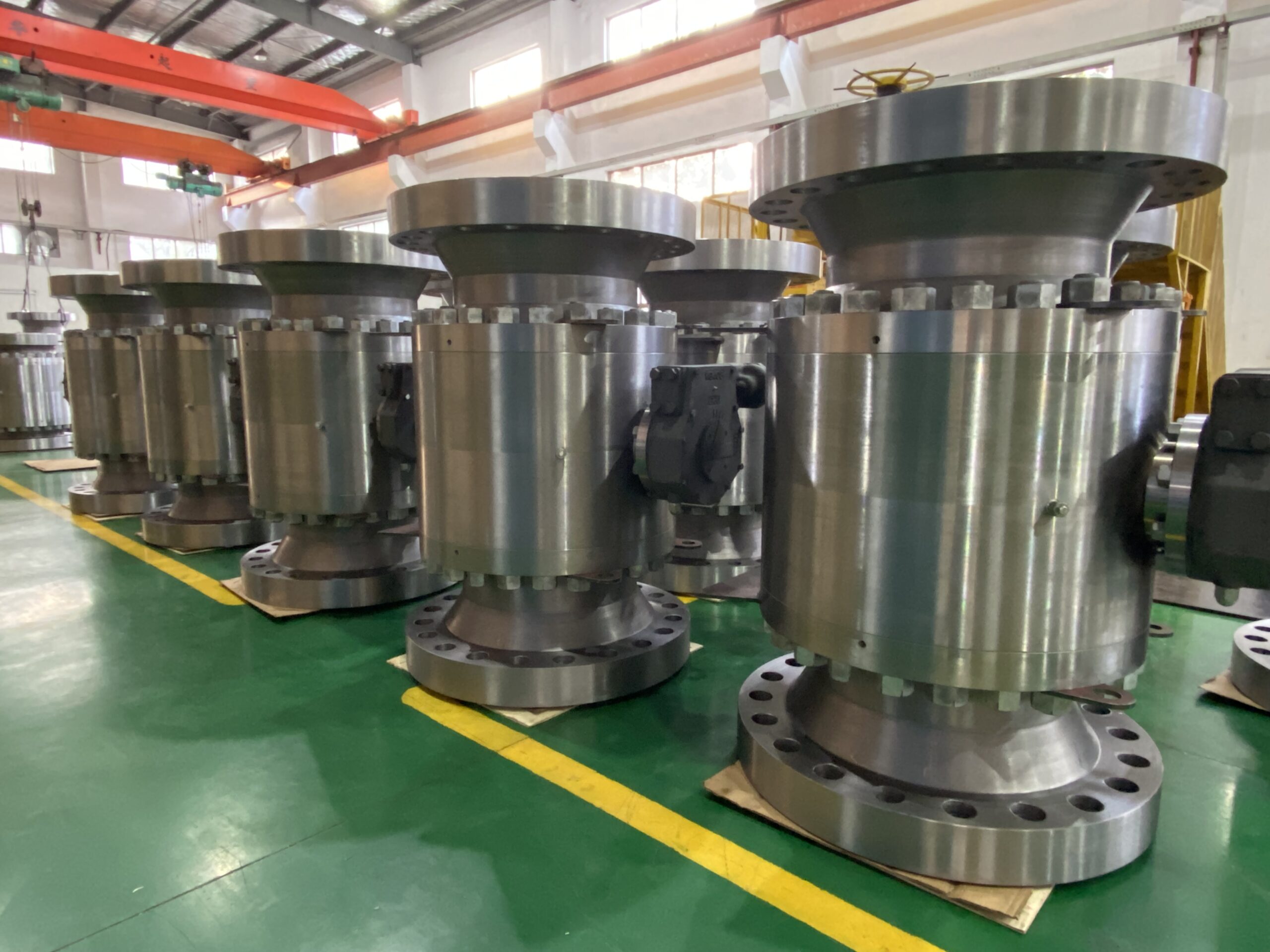
Modernising the workforce by AI
One of the most prominent features that FR Valve continues to invest in is their use of AI technology. They employ the technology to keep track of their testing procedures, manufacturing, and control facility. The testing, for example, takes place without any people present. This way, the company ensures its employees’ safety while simultaneously facilitating accurate testing of their products.“We have a highly skilled workforce trained to monitor several operation facilities, and make sure a large part of the manufacturing process is automated.”
Initially, FR Valve’s main selling point was the low production costs, as labour was much cheaper in China than in Europe and the US. But, over the course of twenty-five years, the Chinese economy has caught up, and to be able to continue offering competitive prices, the company has had to come up with a different strategy.
AI is a gamechanger, Mr Zhang explains, as the competitive market requires him and his fellow valve manufacturers to keep up with the latest technological advancements. “It has not only impacted our monitoring process, but it has forced us to rethink the way we structure our production process as well.” He explains that he initially feared that the costs for implementing AI would be high, but as the Chinese economy is catching up with the European and American economies, the difference in cost of living is even out.
In China especially, companies reluctant to implement AI often find themselves lagging behind. “When we first started, I noticed that our testing, machining, and our process and control facilities weren’t as good as those in Europe, but we’ve managed to keep up,” Mr Zhang says. “I have visited companies and facilities in Europe and the US, and I can even say that we’re more modern than some of them now. And because we’ve been able to successfully implement AI into many of our processes, our output has improved significantly.”
Though AI continues to be one of FR Valve’s greatest investments, Mr Zhang emphasises that engineering will always have to come first. The company’s strategy to stay ahead of the engineering is mostly based on their ability to improve their products and develop new technology.
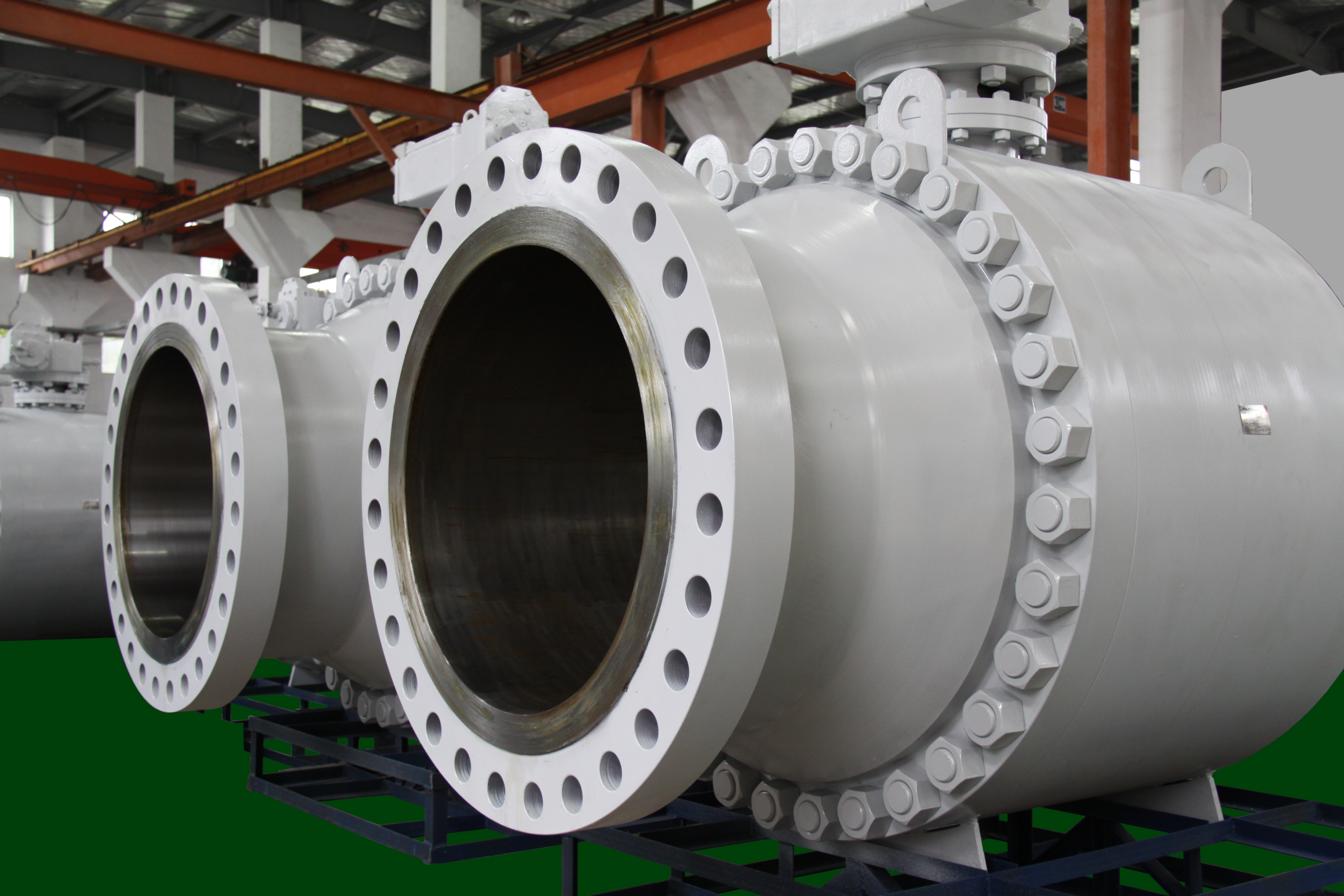
High-pressure gas testing
High-pressure gas testing is essential to verify the reliability and safety of valves under extreme operating conditions. Valves that pass this rigorous testing process provide confidence to manufacturers, suppliers, and end-users that the products are of high quality and can withstand the demands of their respective industries. It helps prevent potential failures that could lead to safety hazards, environmental damage, or costly downtime.
The process involves subjecting the valve to pressures significantly higher than its rated pressure to assess its ability to withstand extreme conditions without failure. The test is conducted using specialised equipment, such as pressure test chambers or hydraulic systems, capable of generating and controlling high pressures.
Valve World Southeast Asia Conference & Expo sponsor
FR Valve is a proud sponsor of the 2023 Valve World Southeast Asia Conference & Expo. The event will be held on 26 and 27 October 2023 and will take place at Singapore Expo Hall 2, Singapore. Conference visitors are welcome to visit them at stand C15 on the expo floor.
Valve World Southeast Asia Conference focuses on hot topics in the development of
the industry, as well as the main challenges faced by players to carry out inter-industry discussions, and forms a professional communication platform to make business communication more accurate and in-depth.
Mr Zhang will speak at the conference, giving a presentation on “Escape technology applied in high pressure gas test innovation,” on day 1 during the Valve Selection & Application session, which is scheduled for 15:30 – 18:00 PM SGT.
About this Featured Story
This Featured Story is an article from our Valve World Magazine, September 2023 issue. To read other featured stories and many more articles, subscribe to our print magazine. Available in both print and digital formats. DIGITAL MAGAZINE SUBSCRIPTIONS ARE NOW FREE.
“Every week we share a new Featured Story with our Valve World community. Join us and let’s share your Featured Story on Valve World online and in print.”