Fluoropolymers such as PTFE, PVDF, FEP and PFA are a group of polymers found within the Per and PolyFluoroAlkyl Substance (PFAS) naming syntax. The goal of industry today is to understand the impact of fluoropolymers, throughout their life cycle, on human health.
By Tim Goedeker, Consultant, and Gobind Khiani, P.Eng., Fellow, Mechanical Engineering – Piping/Pipelines
The term PFAS – Per and PolyFluoroAlkyl Substance (Per is non-polymer and Poly is polymer) – is a broad, non-specific term, which does not inform whether a chemical compound is harmful or not but indicates only that the chemical has a fully fluorinated methyl or methylene carbon group. All PFAS chemical compounds, of which there are 4,700+, are similar in a naming syntax and based on the existence of a carbon-fluorine atom bond. Most PFAS chemicals are not similar in physical properties, in end use, in benefits to society, or in impacts to nature and the environment. To draw any conclusion or inference from another chemical included in the PFAS umbrella is folly. Fluoropolymers such as PTFE, PVDF, FEP and PFA are a group of polymers found within the PFAS naming syntax as shown in Figure 1.
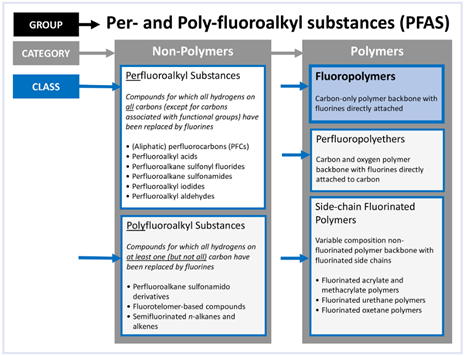
The intent of this article is to bring awareness to some unique properties of fluoropolymers, specifically PTFE. In addition, this article will highlight concerns surrounding certain non-polymer PFAS chemicals (PFOS and PFOA). This article is not intended to conclude or not conclude that fluoropolymers are of “low concern”.
Characteristics of PTFE
PTFE (polytetrafluoroethylene) is a polymer consisting of very long perfluorinated alkyl chains. By naming syntax only, it is termed a “PFAS”, but it has different characteristics. High molecular weight fluoropolymers, like PTFE, are highly stable (chemically and thermally), too large to be bioavailable, non-toxic, and not mobile in the environment. Per the OECD governing body (Organization for Economic Cooperation and Development) many fluoropolymers, like PTFE, meet their criteria of “Polymers of Low Concern” as their properties present low health and environmental concern.
PTFE has been tested many times and proven, for example, in medical products or implants and, unlike perfluorooctanoic acid (PFOA) and perfluorooctanesulfonic acid (PFOS), cannot accumulate in the environment or in living organisms. For these reasons, a general proposal to ban the PTFE substance is irresponsible.
End use benefits of PTFE
PTFE was first used during World War II as a sealing device in equipment used to transport uranium hexafluoride. This super material was critical to the development of nuclear fusion. PTFE is the best performing material in applications where low emissions of volatile organic compounds (VOCs) are required by law.
In finished form PTFE polymers are corrosion resistant, have low frictional characteristics which allow easy movement of machine parts, has thermal stability and effective sealing capability. In sealing products, PTFE prevents leakage from industrial equipment. Seals that utilize PTFE polymers reduce leaks to nearly zero, making them a cornerstone in the efforts to reduce fugitive emissions. The use of PTFE liners and packing has enabled valve manufacturers to significantly reduce the fugitive leaks, including methane, from process valves which has reduced the generation of greenhouse gases.
Precision placement and unyielding redundancy
ESOV placement is critical, ensuring that these sentinels stand guard at key junctures in the process flow. Their strategic placement in units, storage facilities, and both upstream and downstream of vital equipment fortifies the defense against potential calamities. Additionally, redundancy in ESOV systems is essential to ensure a reliable fail-safe operation. Embracing redundancy with dual, or even triple, ESOV configurations foster robust fail-safe operation, adding additional assurance that the facility’s shutdown capabilities persist even if one valve falters.
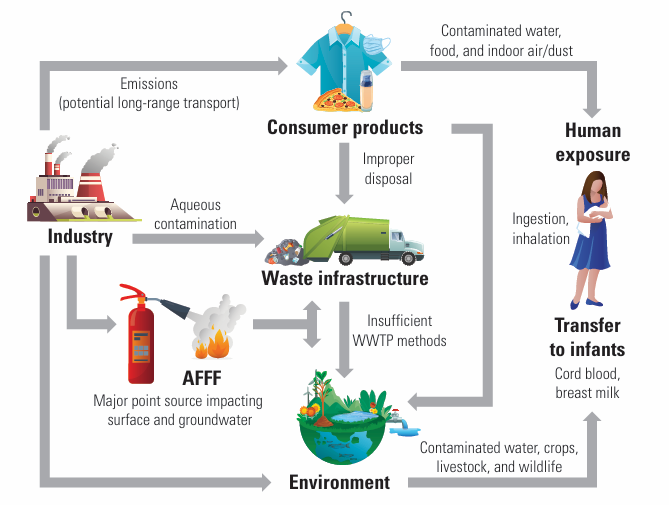
PFOS and PFOA – PFAS chemicals of concern
Certain fluorinated methyl or fluorinated methylene based chemical compounds, specifically, perfluorooctanoic acid (PFOA) and perfluorooctanesulfonic acid (PFOS) chemicals, were found to be potentially harmful and they were used in:
- Household applications – stain & water-resistant products, non-stick cookware coatings.
- Commercial applications – firefighting foam (AFFF) – were found to be possibly harmful.
PFOS was phased out of production and use in 2002 and US manufacturers eliminated PFOA emissions and product content at the end of 2015. As a result, manufacturing processes and products previously relying on PFOA and PFOS were modified to use replacement chemical compounds.
Exposure to PFOA and PFOS
The four major routes of PFOA / PFOS exposure are:
- Fire training/fire response sites using Aqueous Film Forming Foams (AFFF) for fighting fires,
- Industrial sites,
- Landfills,
- Wastewater treatment plants/biosolids (see Figure 2).
The PFOA / PFOS can get into drinking water when products containing them are used or spilled onto the ground or into lakes and rivers. AFFF are synthetic foams containing PFOS or PFOA designed for flammable liquid fires. The PFOS & PFOA serve as surfactants that spread the foam to cool and suppress the fire. Because of their persistence in the environment, they don’t break down and will remain in the environment virtually permanently, and well-documented health effects, these two specific chemicals are largely being phased out in the U.S.
Firefighting foams
The foams primarily used for industrial firefighting (AFFF) have been manufactured with PFOA and PFOS as mentioned above. However, there now are some alternatives which are certified fluorine-free. The Class A/B firefighting foam, PHOS-CHEK® 1% fluorine-free foam concentrate, is one available mixture of water and hydrocarbon surfactants. Developed for use on Class B hydrocarbon fuel fires, the organohalogen-free foam is an environmentally responsible next generation product – does not contain intentionally added PFAS chemicals including PFOA and PFOS.
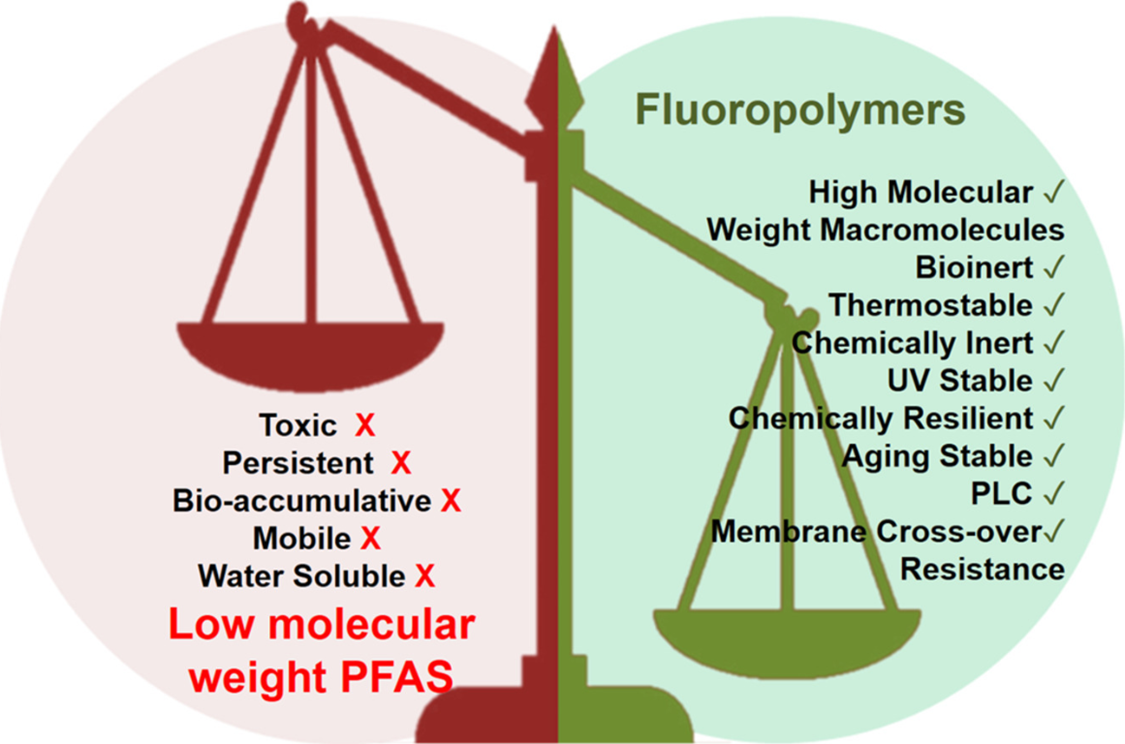
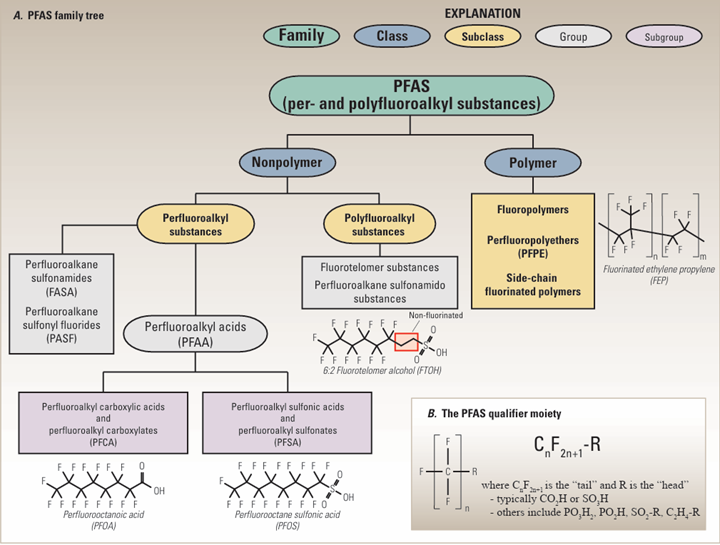
Each PFAS chemical is different
While PFAS chemicals are environmentally persistent, an important distinction among them is they exist in different states — solids, liquids, and gases. The state greatly impacts mobility through air, water and soil. For example, the liquid state of PFAS-containing firefighting foam (AFFF) contributes greatly to its ability to contaminate soil and water.
Additionally, there are physical size differences between PFAS non-polymer substances such as PFOA and PFOS and PFAS polymers such as PTFE. A non-polymer consists of a single molecule; whereas, a polymer can consist of thousands of repeating molecular units. The relatively small size of non-polymers (PFOS, PFOA) makes them more mobile — easy to spread in air and waterways — and more bio-available — with increased potential to build up in blood and body tissues where they might do harm. High molecular weight fluoropolymers, like PTFE, are highly stable, chemically, and thermally, are too large to be bioavailable, are non-toxic and not mobile in the environment.
Much to come for the future
The term PFAS indicates only that a PFAS chemical has a fully fluorinated methyl or methylene carbon group. PFAS are a collection of chemicals used to make many products, ubiquitous to everyday life, including fluoropolymers (see Figure 4).
A number of non-polymer PFAS chemicals – specifically, PFOS, PFOA – have been branded as “forever chemicals” because testing has shown they don’t break down in the environment quickly.
A science-based approach, utilizing standardized testing, is necessary to understand each unique PFAS chemical and determine acceptable levels of use. The science-based approach should also be used to regulate chemicals, such as PFOA and PFOS, and products, such as AFFF, deemed harmful.
References are available upon request.
About the author
Tim Goedeker brings nearly 40 years of leadership in petroleum refining operations, engineering, and environmental compliance. At Phillips 66 until 2022, he focused on enhancing environmental compliance across 15 refineries, negotiating multibillion-dollar consent decrees with the EPA.
Post-retirement, he provided environmental consulting, offering regulatory guidance and fundraising for charitable causes like the Crohn’s & Colitis Foundation.
Gobind N. Khiani is a University of Calgary alumnus, holds a fellowship and serves on the boards of Energy Sustainability Training for Young Engineers and Geoscientists and Canadian Prairie Group of Chartered Engineers since 2019. He chairs the End User Group at API 609 and serves as Vice-Chairman of Standards Council of Canada. With past leadership roles at the CBEC of APEGA, his expertise spans strategy, governance, engineering management, sustainable development, and operations.
About this Technical Story
This Technical Story is an article from our Valve World Magazine, April 2024 issue. To read other featured stories and many more articles, subscribe to our print magazine. Available in both print and digital formats. DIGITAL MAGAZINE SUBSCRIPTIONS ARE NOW FREE.
“Every week we share a new Technical Story with our Valve World community. Join us and let’s share your Technical Story on Valve World online and in print.”