Equinor’s Grane platform in the North Sea. Photo: Elisabeth Sahl / ©Equinor
Duplex stainless steel’s unique combination of properties, including corrosion resistance, strength and durability, has made it increasingly popular for valve manufacturing in demanding environment.
By James Chater
When evaluating materials for valve applications, duplex stainless steels offer a balanced combination of properties, though they may not top every category individually. In terms of corrosion resistance and toughness, duplex grades perform exceptionally well, with heat resistance slightly lower but still impressive. However, it’s important to consider how these properties compare to other materials used in valve manufacturing.
Corrosion resistance is a critical factor for many valve applications. While iridium, a dense and brittle transition metal from the platinum group, holds the title for most corrosion-resistant metal, it’s rarely used in valve construction due to its cost and limited workability. More practically, certain grades of stainless steel, aluminium, copper alloys and nickel alloys are often chosen for their corrosion resistance in valve designs. Heat resistance is another crucial property for valves in high-temperature applications. Although materials like tantalum carbide and hafnium carbonitride (HfCN) boast extremely high melting points (over 4,000°C), they are not typically used in valve manufacturing. For comparison, titanium, which is sometimes used in valve components, melts at 1,668°C. Duplex grade 2205, commonly used in valve applications, has a melting range of 1,385–1,445°C, while super-duplex grades melt at around 1,410–1,460°C, comparable to nickel at 1,455°C.
Strength and toughness, essential for valve integrity under pressure, can be measured in various ways. While graphene holds the record for highest fracture strength (over 125 GPa), it’s not practical for valve construction. Among metals, tungsten is known for its impact resistance, with chromium, iron, titanium, vanadium and lutetium following closely. Duplex stainless steels, however, offer a practical balance of strength and toughness, making them suitable for a wide range of valve applications.
Advantages of duplex in valve applications
When considering materials for valve manufacturing, duplex stainless steel is a versatile choice that combines multiple desirable properties. This unique mix of characteristics makes duplex grades competitive against other stainless steel grades, carbon steel and alternative materials across various industries.
The advantages of duplex stainless steel in valve applications include:
- Corrosion and erosion resistance: Essential for valves in aggressive environments, such as seawater or chemical processing.
- Heat resistance: Allows for use in high-temperature applications, though not as extreme as some specialised alloys.
- Strength: Provides excellent mechanical properties, crucial for maintaining valve integrity under pressure.
- Cost-effectiveness: Offers a balance of performance and affordability, particularly when considering life-cycle costs.
- Formability: Allows for easier manufacturing of complex valve components.
- Recyclability: Contributes to sustainability efforts in valve production and end-of-life management.
These combined properties make duplex stainless steel an attractive option for valve manufacturers seeking to improve performance, durability and cost-effectiveness.
Duplex stainless steel valves across industries
Duplex stainless steel valves have found widespread application across multiple industries due to their unique combination of properties. Let’s examine how these duplex stainless steel valves are utilised in different sectors:
- Deepwater oil & gas
Longitudinally-welded or seamless umbilicals, which bundle together the various lines (flowlines, power, data, water, chemicals, fluids, etc.) between subsea wells and the platform, often need to span long distances in deep water, so a material that can both resist corrosion and withstand high pressures is called for, such as super-duplex type 2507. Flexible pipes or risers, used to convey oil or gas from seabed to surface, also require high grades. Depending on the depth, super-austenitics, duplex in lean (2101), standard (2205) or super-austenitic (2507) grades are applied. Duplex is also finding use in valves that handle monoethylene glycol (MEG). This chemical is used to inhibit hydrate formation in pipelines, which can cause blockages. Recently Oliver Twinsafe supplied double block and bleed valves for the MEG injection pump systems of an offshore project, made of A182 F55 super-duplex stainless steel. - Marine installations
Oil & gas or wind platforms or solar power systems, being exposed to seawater, are environments where duplex grades are often applied. These have three types of environments: atmospheric, splash or submerged zones. Depending on the level of corrosivity, each can require duplex steels of varying strength. The most severe zone of all is the splash zone, where hazards include oxygen-rich seawater (chloride environment), wet-dry cycles and UV radiation. In addition, other challenges include powerful wind or underwater currents, cold and sea spray and sand abrasion. For all these reasons, standard or super-duplex grades are required; for the other two, lean grades can sometimes be enough. - Wastewater and desalination
Desalination is an obvious area in which duplex grades are applied, because of the exposure to saltwater. But wastewater treatment is increasingly turning to duplex because of the need to resist both corrosion and erosion. Type 2205 is used in evaporators, piping systems, heat exchangers, tanks, valves and reactors. Recently Invest-Tech designed a new type of wastewater treatment storage tank built of Forta LDX 2101. This departs from the traditional round form because of the need to expand to accommodate increased capacity. Square or rectangular shapes are bolted together – though the process does require some welding. Therefore, apart from corrosion resistance, high pressure and weldability were important criteria.
Conclusion
Looking ahead, the role of duplex stainless steel in valve applications is set to expand further. As industries push the boundaries of operational environments and seek to optimise their processes, the demand for materials that can withstand extreme conditions while offering long-term reliability will only increase. Valve manufacturers are already exploring new duplex alloy compositions and innovative manufacturing techniques to enhance performance even further. Additionally, the growing focus on sustainability in industrial operations may increase the appeal of duplex stainless steel valves, given their durability and potential for reducing replacement frequency.
A supplier’s view
Rodney Rice, director of Langley Alloys, notes the continuing high demand for duplex and super duplex grades, particularly in the oil & gas sector. He highlights the strong demand not only in upstream applications but also in downstream uses, specifically mentioning valve components. Rice also points out the growing use of duplex in seawater-exposed applications, such as offshore wind power and in desalination plants, where water scarcity drives demand for duplex and super duplex piping. The versatility of duplex stainless steel extends beyond traditional applications.
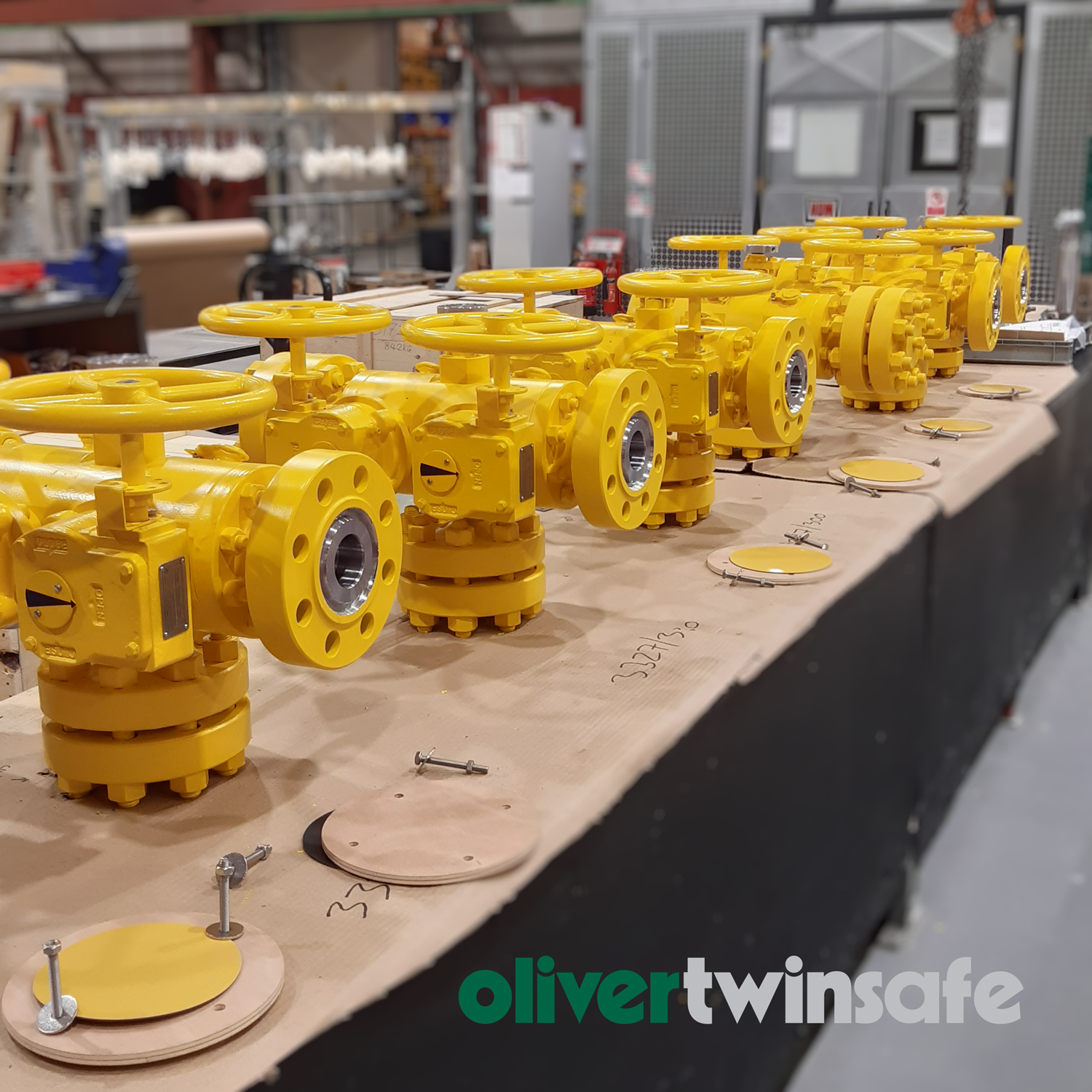
Dive Deeper into Valve World
Enjoyed this featured article? There’s much more to discover! Subscribe to Valve World Magazine and gain access to:
- Advanced industry insights
- Expert analysis and case studies
- Exclusive interviews with valve innovators
Available in print and digital formats.
Breaking news: Digital subscriptions now FREE!
Join our thriving community of valve professionals. Have a story to share? Your expertise could be featured next – online and in print.
“Every week we share a new Featured Story with our Valve World community. Join us and let’s share your Featured Story on Valve World online and in print.”