Proper installation and maintenance to achieve optimum system performance are essential when researching packing behaviour.
By Maria Garcia, MONTERO FYE S.A.
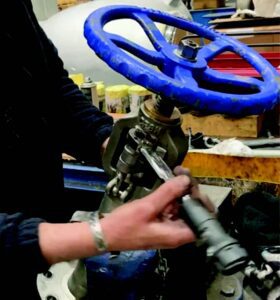
In technical papers, information is available about low emissions and how aiming for the best torque on a valve packing gland is essential to optimise economic resources and environmental impact. The correct balance between sealing force and stem friction must be reached. Inadequate torque methods result in several problems, including increased maintenance, higher leakage and reduced packing life with the consequent waste of money and energy. Reducing energy consumption, being competitive and minimising costs means being efficient. The best results are needed. So, once the correct packing material, geometry and design have been chosen, the right torque choice and its controlled application on the bolts are required to reach an optimised compressive load. This is one of the most important considerations to be taken. Appropriate load and an accurate transmission to the packing must be achieved.
At this point, two questions must be addressed: torque value and tightening method.
Torque value & tightening
Usually, the packing manufacturer will recommend the torque value for their particular packing. The optimum torque value is calculated by considering several parameters: number of bolts, quality, diameter, packing composition and friction factors. Regarding the tightening method, some variation occurs in the information given by manufacturers, but in general best practice will involve the following elements:
- Clean and inspect the housing and counter face
- Use hardened flat washers
- Tighten the gland bolts (often recommended to be done in several stages)
- Use a calibrated torque wrench
- Measure bolts distance
- Readjust gland nuts after a short working period (sometimes it is recommended at least 5 times with the valve in the closed stroke position).
- Proper lubrication
These practices will minimise the changes and losses due to variations in the torquing process. All of them affect the sealing system.
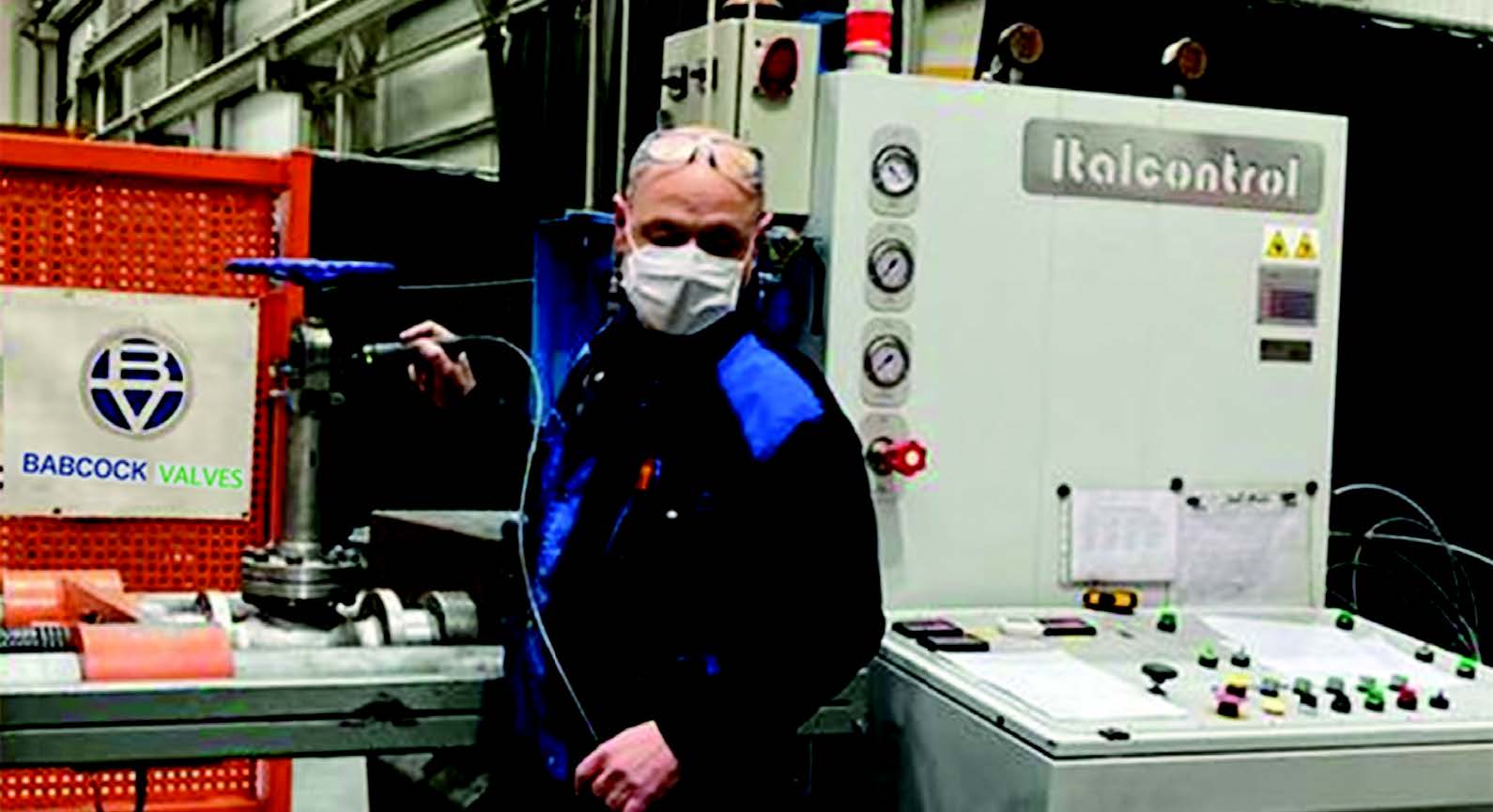
Can we adjust the packing to minimise deviations in the torquing process?
The first contact between the packing and the valve stem is produced by a seating torque value. During assembly, the first torque value required to seat the packing will affect packing behaviour during operation. Plastic deformation in the packing set takes place, and all the gaps between the stem/ housing and packing gradually disappear as the load increases. This is the pre-deformation or seating process, and this is the torque value that needs place the packing set in the best condition to perform its work.
After this, the tightening torque is applied. The aim of pre-deformation is to ensure that the tightening torque value is maintained throughout the life of the packing. Therefore, pre-deformation must optimise the sealing system, which requires us to balance two factors: achieving optimum tightness to ensure low emissions whilst minimising friction.
This seating value determines how the packing will adapt to the sealing system.
If this seating stress is adequate, the behaviour of the whole system will improve with time. A good seating torque value, in addition to an appropriate working torque value, could optimise packing performance. It is logical to think that this first contact will be decisive in getting a reliable packing performance. To corroborate this idea, we have performed a series of tests.
Several types of packings with the same geometry, design and working conditions (torque values, temperature, cycles, internal pressure, etc) but with different seating torque values at the beginning, on assembly, were tested. The tests were conducted at one of our valve manufacturing customers, and we thank them for their cooperation. The tests were performed in a 3” ball valve, pressure class 300. The stuffing box dimensions were 28.3 x 44 x 52 mm. A sniffer performed leakage measurement with a helium mass spectrometer.
Packings
- Six ring set with 28,3x44x8 mm packing dimension, manufactured from three different packing materials:
- Braided PTFE packing with pure PTFE yarns and PTFE impregnation, density 1.5 g/cm3,
- Braided expanded graphite packing made from Inconel wire over knitted expanded graphite yarn (C>99% carbon content), density 1.7 g/cm3,
- Braided carbon fibre packing made from carbon yarn with graphite impregnation, density 1.1 g/cm3.
Seating process
- Anti-Friction component (Molykote) on bolts
- Pre-deformation two times to 20, 30 and 40 Nm
- Working load 30 Nm
- 3 cycles
- 20/10 bar Helium
Conclusions
The pre-deformation or seating torque values of the packing sets impact the final packing sealability when the other conditions are fixed and maintained. In all cases, the packing set sealing behaviour with three different seating torque values is accurately represented by an equation that reaches an optimum sealing value with a particular seating torque value, providing the lowest emissions. With higher torque values, sealability starts to decrease.
In all cases, sealability initially improves with an increase in seating torque value until the optimum value is reached. This is clearly represented in the carbon fibre packing which, due to its composition, has a lower ability to seal, and changes in this ability are clearer.
If the optimum seating torque value is exceeded, the packing set loses some of its sealability. This must be due to over-compression, which lowers the packing set’s ability to adapt to the irregularities in the stuffing box due to increased stiffness. These tests show that, once we know the optimum torque value for the packing set at the working conditions, an initial deformation or an optimal seating torque value before operation could:
- improve the packing set behaviour during operation and,
- minimise some irregularities both in the packing and in the stuffing box, generating more homogeneity and better performance of the packing set.
The author would like to thank Babcock Valves for performing the tests and providing photographs.
About the author
Maria Garcia is the R&D Manager of MONTERO FYE S.A. and a member of the ESA Packings Division. She has a degree in Physical Chemistry (Basque Country University) and a postgraduate qualification as ‘Expert in Plastics and Rubber’.