The oil and gas industries supply global energy needs while confronting environmental and social demands. Extraction, transport and processing of hydrocarbons carries risks that must be managed. Emergency shutdown valves play a critical role in safeguarding personnel, equipment and the environment across the sector’s complex applications.
By David Gaines
Emergency Shutdown Valves (ESOVs) represent the linchpin of crisis management within oil & gas facilities. An ESOV is a critical component that is designed to halt process flow in the event of an emergency or abnormal condition. Its mission is clear: avert catastrophic outcomes by restricting hydrocarbon flow during emergencies, ranging from equipment malfunctions to potential infernos. Nimbly responding to atmospheric conditions and input signals from safety systems or personnel allows ESOVs to reliably mitigate hazards and safeguard lives, property, and the environment.
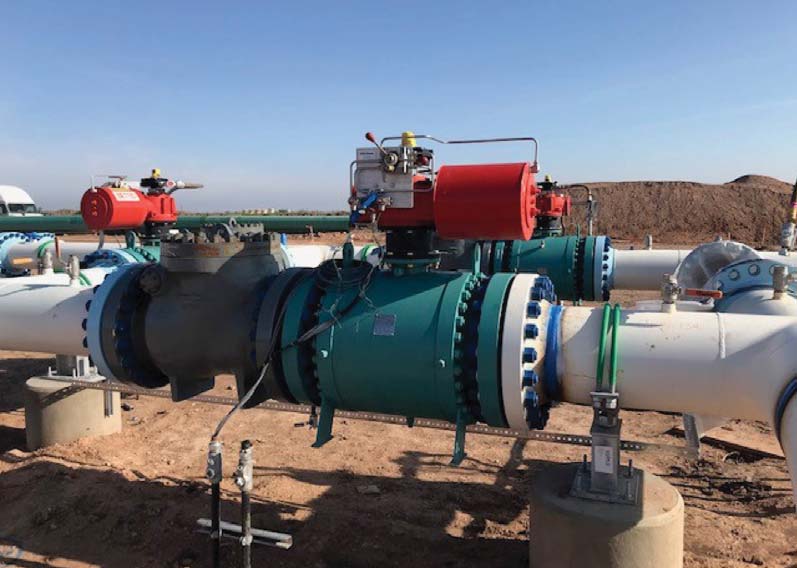
Diverse functionality and integration
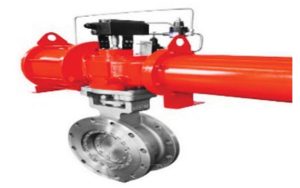
Strategically positioned across production, transportation, and refining processes, ESOVs come in pneumatic, hydraulic, and electric variations, each tailored to specific operational conditions. The working principle of an ESOV is simple. The valve closes rapidly, initiated by a specific increase in atmospheric temperature around the valve itself or in response to a signal from safety systems or operating personnel, immediately interrupting the flow of hydrocarbons. Its harmonious integration into modern safety systems amplifies its impact, as sensors and detectors vigilantly monitor conditions like pressure, temperature, and flow rates. These systems work in conjunction to optimize safety and prevent emergencies from spiraling into disasters.
Types of emergency shutoff valves
There are various types of ESOVs, each designed to address specific operational requirements and scenarios within different industries. Here are some common types of ESOVs:
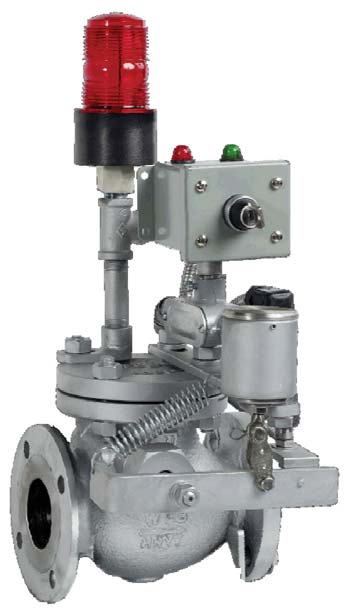
- Pneumatic ESOVs: Commonly used in offshore platforms and remote areas, pneumatic ESOVs rely on compressed air or gas to actuate the valve closure. These valves are well-suited for environments with limited electrical power sources.
- Hydraulic ESOVs: Hydraulic ESOVs utilize hydraulic fluid pressure to close the valve during emergencies. They are often preferred for applications where rapid response times are critical, as hydraulics offer high-speed actuation.
- Electric ESOVs: Electric ESOVs are actuated by electrical signals, making them ideal for integration with modern automation systems. These valves can be operated remotely from central control rooms, enhancing safety and operational efficiency.
- ESOV with Fusible Link: These are commonly check valves with a fusible link designed to disintegrate at a certain temperature, slamming the valve shut in the event of a fire. These can also be paired with a limit switch for feedback and a pneumatic cylinder offering PLC operation. These ESOVs require manual intervention by maintenance personnel to reset the valve after closure.
- Solenoid-Operated Valves: Solenoid-operated ESOVs use electromagnetic principles to actuate valve closure. They are often used for smaller-scale applications and can be operated remotely through electrical signals through the PLC.
Precision placement and unyielding redundancy
ESOV placement is critical, ensuring that these sentinels stand guard at key junctures in the process flow. Their strategic placement in units, storage facilities, and both upstream and downstream of vital equipment fortifies the defense against potential calamities. Additionally, redundancy in ESOV systems is essential to ensure a reliable fail-safe operation. Embracing redundancy with dual, or even triple, ESOV configurations foster robust fail-safe operation, adding additional assurance that the facility’s shutdown capabilities persist even if one valve falters.
Precision placement and unyielding redundancy
Leak Prevention
ESOVs prevent accidental releases of hazardous materials, such as hydrocarbons and chemicals, by rapidly shutting down the flow in emergencies. This significantly reduces the risk of spills and leaks that could harm the environment and surrounding communities.
Emission Reduction
In refineries and petrochemical plants, ESOVs are integral to safety systems that help minimize emissions during operational incidents. By preventing unplanned releases of pollutants, these valves aid in meeting environmental regulations and reducing the facilities’ carbon footprint.
Water Resource Protection
Petrochemical and refining processes often involve large amounts of water. ESOVs ensure that water flow is promptly halted in case of leaks or equipment malfunctions, preventing contamination of water resources and ecosystems. ESOVs embody the harmonious convergence of ESG ideals. At the forefront of the environmental realm, they staunchly prevent leaks, emissions, and contamination, mitigating ecological harm. On the social front, ESOVs champion personnel well-being through accident reduction and enhanced emergency preparedness. Moreover, as governance stalwarts, ESOVs bolster risk management, regulatory compliance, and transparent incident reporting, building trust among stakeholders.
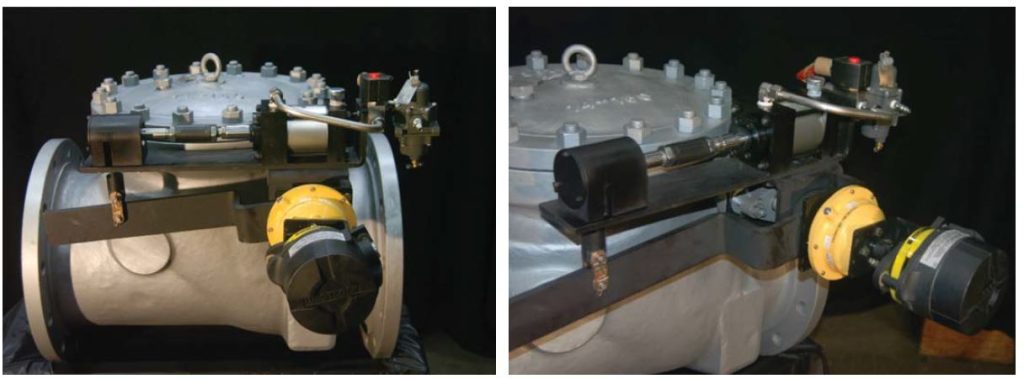
Continuous improvement and people-centric approach
Regular testing, meticulous maintenance, and ongoing training are the cornerstones of ESOV reliability. Assigning a Safety Integrity Level (SIL) rating to an Emergency Shutdown Valve (ESOV) is another pivotal step in ensuring operational safety and risk management within high-hazard industries. SIL ratings provide a quantified measure of a component’s reliability and performance in mitigating potential risks and preventing hazardous events. Through this, ESOVs acquire a tangible language of safety, allowing operators and engineers to make informed decisions about valve selection, placement, and integration within complex safety systems. Thus, ensuring that operators possess the knowledge and skills to execute emergency protocols reflects a people-centric ethos, fostering a culture of safety and shared responsibility.
ESOV standards and resilience
ESOVs stand tall within the framework of industry standards and regulations, guided by institutions like the American Petroleum Institute, ISO, and ASME. Compliant implementation not only underscores governance practices but also acts as a beacon of operational resilience. By fortifying business continuity plans and protecting critical assets, ESOVs imbue petrochemical and refining industries with robustness.
- Continuity Planning: Incorporating ESOVs into business continuity plans enhances the facility’s resilience in the face of emergencies. Rapid response and effective shutdown capabilities minimize the impact of incidents and help the facility recover quickly.
- Protection of Assets: ESOVs safeguard critical assets, such as pipelines, tanks, and equipment, during emergency shutdowns. Protecting these assets aligns with the principles of responsible asset management and stewardship.
- Long-Term Sustainability: By prioritizing safety and environmental protection through ESOV implementation, petrochemical, and refining companies contribute to the long-term sustainability of their operations and the communities they serve.
A future envisioned through ESOVs
Incorporating Emergency Shutdown Valves (ESOVs) into the oil & gas industries is imperative, aligning with the core principles of Environmental, Social, and Governance (ESG) requirements. By swiftly halting hydrocarbon flow, preventing hazards, and fostering a culture of safety, ESOVs ensure responsible corporate practices, sustainable operations, and integrity within these vital sectors. As the sun sets on conventional paradigms, ESOVs illuminate a path forward for the petrochemical and refining sectors. Beyond immediate safety, they enshrine a legacy of environmental stewardship, social well-being, and exemplary governance.
By embracing these guards of security, industries embrace a future that embraces both progress and responsibility, fostering sustainability for generations to come.
About the author
David Gaines, Jr. is a seasoned oil and gas industry professional with over 15 years of oil and gas experience. He currently serves as the Business Development Manager at Williams Valve Corporation and has significant experience specializing in manual valves, control valves, and automated valves across the industry sectors.
About this Technical Story
This Technical Story is an article from our Valve World Magazine, April 2024 issue. To read other featured stories and many more articles, subscribe to our print magazine. Available in both print and digital formats. DIGITAL MAGAZINE SUBSCRIPTIONS ARE NOW FREE.
“Every week we share a new Technical Story with our Valve World community. Join us and let’s share your Featured Story on Valve World online and in print.”