The world is cracking down on methane emissions. As of November 2021, nearly 90 countries have committed to the Global Methane Pledge, an initiative to reduce global methane emissions by at least 30 per cent from 2020 levels by 2030. Demonstrating global leadership at COP26, President Biden committed the US to an ‘aggressive’ target to reduce methane emissions by about 50 per cent below 2005 levels. As the largest source of industrial emissions of methane, all eyes will be on the oil and gas industry to deliver, making it imperative that all operators take urgent steps to eliminate fugitive emissions, effectively, reliably and as soon as possible.
By Dr Chris Kennell, Technical Sales Manager at Oxford Flow
Poorly monitored and controlled fugitive methane emissions represent a significant proportion of greenhouse estimated that 82 Mt methane emissions came from oil and gas operations – equating to nearly a quarter of all anthropogenic sources. Despite its significant global warming potency however, until recently, the driving force behind tackling fugitive methane emissions has been one primarily born out of safety rather than climate action. However, with more legislative control appearing globally, that is set to change. Upstream and downstream facilities operators will be increasingly under the spotlight to tackle fugitive emissions as a means to achieve good climate management in line with stakeholder expectations.
Valves: a major source of leaks
While there are many areas of the production process that result in fugitive emissions including flaring, well integrity and abandonment, the joint integrity of flow control infrastructure (aka valves) is a major source of integrity leaks and fugitive emissions that is often somewhat overlooked. A single major processing plant – be it a crude oil refinery or an FPSO – can have anywhere between eight to ten thousand valves. The culminative potential of these valve populations to be responsible for high volumes of fugitive emissions should not be underestimated.
With the need to minimise the risk of hydrogen sulphide poisoning and explosion risk, operators spend thousands/millions a year on joint integrity inspection and preventative maintenance plans. However, in terms of fugitive emissions, it’s a sticking plaster that has a varied success rate, and one that doesn’t address the root cause of the problem – the valve design itself.
Up until recently, the valve industry has only brought forward iterative engineering design improvements with no major changes to the clas-sic valve blueprint. However, given that the most common failure points of most valves is the stem and actuator, without reimagining the design, operators remain trapped in a cycle of spending millions in maintenance to catch leaks after they’ve already increased safety risk or impacted the environment. This is until a team of aerospace engineers looked at the problem through a different lens and developed a radically new design that could eliminate fugitive emissions altogether while vastly improving valve safety too.
Valve innovation started with a jet engine
Unable to source a pressure regulating valve that could meet the needs of his jet engine research, University of Oxford Professor Thomas Povey was compelled to design his own. Instead of an industry standard flexible diaphragm, Povey designed a valve that uses a hydraulic piston integrated within the valve body for actuation instead. It was exactly what he needed for his research, but coincidentally, the design also achieved vast improvements on the valve industry’s benchmark for performance and reliability. The secret to its success was in its simplicity. By removing the diaphragm and associated elastomers, Povey significantly reduced the issues of fatigue, erosion and embrittlement and tackled the Achilles heel of pressure regulator valves. Recognising the potential benefits of this innovative approach to valve technol-ogy, Oxford Flow was established in 2015 to commercialise the technology for broader use.
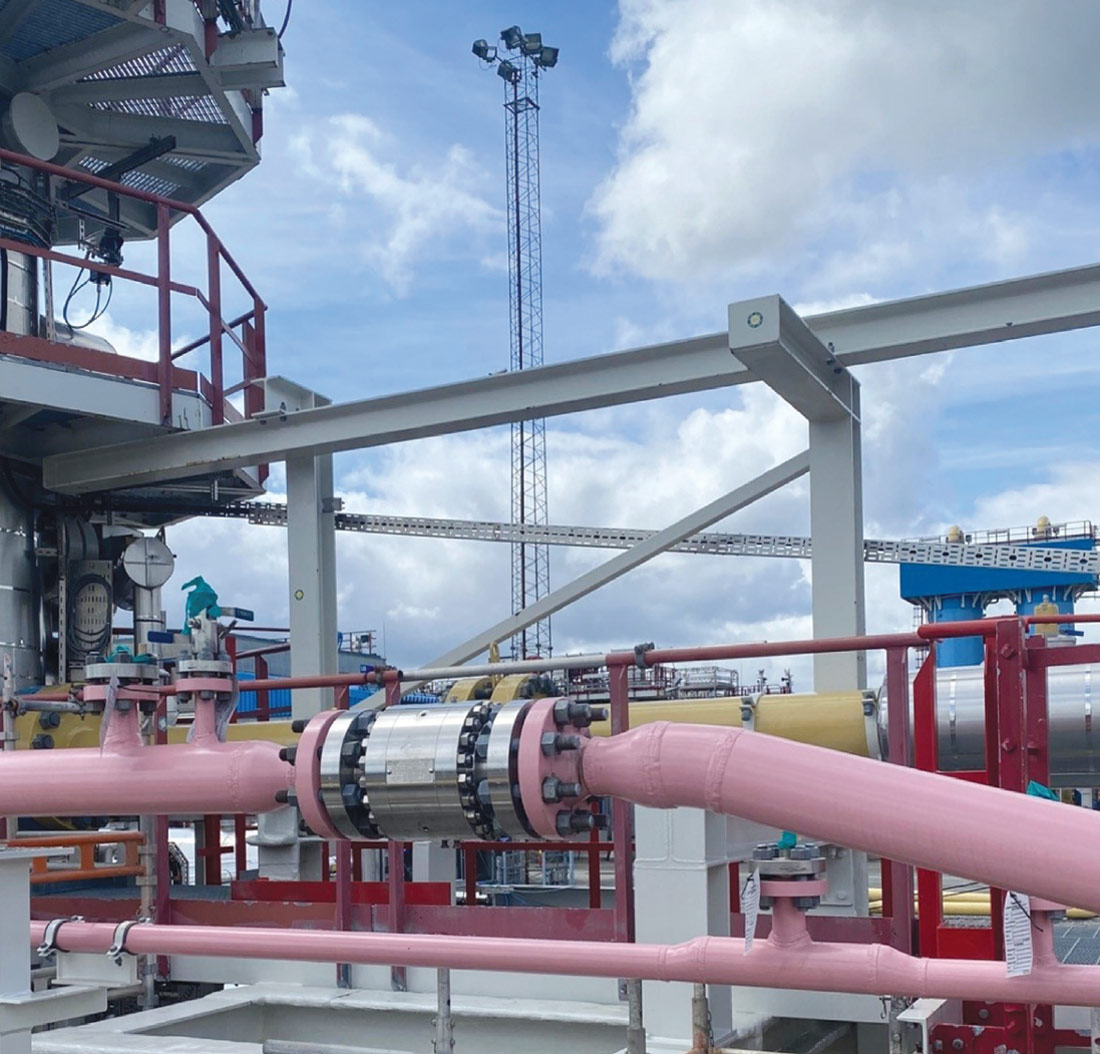
“Operators replacing traditional valves with
the reimagined ES valve will no longer need to allocate precious
resources to seek out fugitive emissions”
Building on Povey’s innovative and simple approach, Oxford Flow developed the ES valve in 2018, which removed the stem – the leading cause of fugitive emissions – the actuator and drivetrain.
The ES valve is certified as meeting the ISO 15848-1 Class A standard and provides remarkable assurances of leak reduction and elimination in comparison to the standard Class B certification which is typically seen across the industry. This means that the innovative valve design has been proven to show substantial improvement over existing products in the market and marks a significant step forward in emissions reduction technology.
The design is a gamechanger for operations and maintenance too, particularly for those operations with a high proportion of critical control valves, or for operators with ageing assets. Those operators that begin to replace traditional valves with the reimagined ES valve will no longer need to allocate precious resources to seek out fugitive emissions on that portion of their valve population. Nor will they need to adhere to the same intensive maintenance regime as drivetrain related failures are eliminated and there is no stem packing to maintain. As a result, operators can expect a 20-30% reduction in cost of ownership as well as doubling the mechanical life of the valve.
Altogether, the list of improvements and cost reductions made possible by the reimagined valve is long. However, in today’s climate, its true value lies in the transformative impact that it can have on eliminating fugitive emissions at a global scale. Hundreds of thousands of valves leak fugitive emissions from oil and gas infrastructure both onshore and offshore every year, creating a substantial burden on operators to continuously identify and mitigate leaks. With the ES valve, this no longer needs to be so – from all angles – cost, weight, size, availability, reliability, performance, maintenance – the case for its specification for retrofitting and new installations alike is compelling, however its ability to eliminate fugitive emissions entirely is what cannot be ignored.
About this Featured Story
This Featured Story is an article from our Valve World Magazine June 2022 issue. To read other featured stories and many more articles, subscribe to our print magazine.
“Every week we share a new Featured Story with our Valve World community. Join us and let’s share your Featured Story on Valve World online and in print.”