The health of control valves and actuators is critical to the ability of process plants to operate without significant unplanned downtime events. This paper discusses the development of an auto-diagnosis algorithm for predicting the Remaining Useful Lifetime of control valves and actuators using operating data.
By Walt Boyes and Nicolas Spiegl, UReason
For operators, maintenance engineers, and asset management experts in process plants, turnarounds are the only chance to repair or replace critical control valves without additional unplanned downtime. Waiting for turnarounds, which are very expensive, increases the chances of surprise failures, which are often even more expensive. Besides that, in a turnaround, time is of the essence, and it is necessary to focus on only necessary and critical tasks.
To know the accurate Remaining Useful Lifetime (RUL) of valves and actuators is therefore a huge advantage in planning the next turnaround. Manufacturers normally provide an indication of the expected lifetime of a valve or actuator. However, these indicators do not consider the actual operating history of the valve, or the operating conditions under which the valves and actuators exist. The information provided by the manufacturers is really of limited use for maintenance and turnaround planning.
The information should be relevant to asset management and reliability engineers. Having the ability to know the accurate RUL is critically relevant for planning a shutdown, turnaround, or any sort of asset replacement strategy. The issue is the same for zero maintenance valves, which simply require replacement, and valves that can be refurbished.
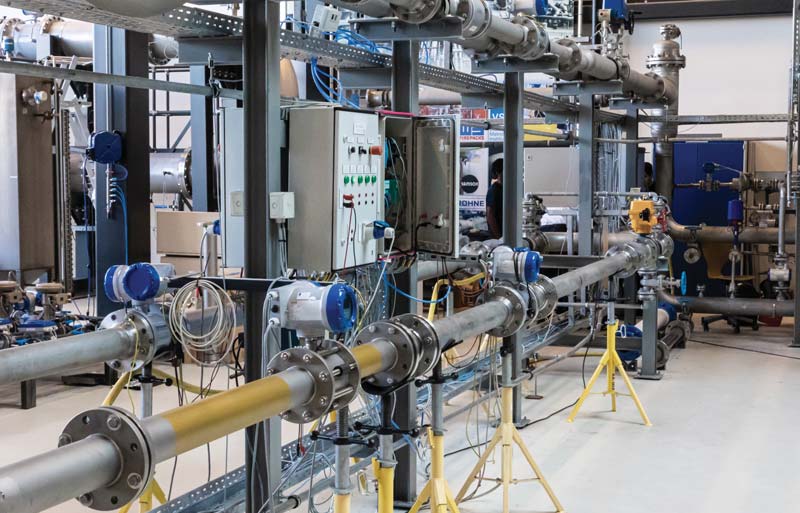
The business issues of unplanned valve failure
The cost of an unplanned shutdown to replace or repair a valve can be much higher than the simple cost of the valve, actuator, and the labor to repair it. If a valve fails, even if it doesn’t fail catastrophically, the cost of the unplanned shutdown includes the maintenance costs, but also the service interruption, and the loss of production. The supply chain issues of a single valve failure can be costly. If the process plant is producing feedstock, the downstream plant that is waiting for the feedstock may also have to shut down. If the plant is producing finished product, deliveries may be missed, and contracts may be breached.
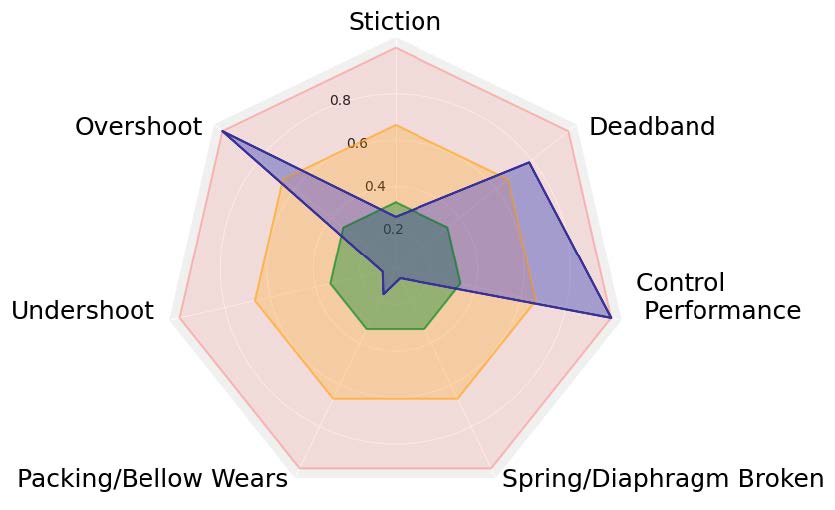
If the valve fails catastrophically, there can be injuries, additional failures of equipment and instruments, and even damage or destruction to vessels, reactors, and piping and systems. For example, allowing a polymer reactor to go cold because of a valve failure could result in having to replace the reactor entirely.
Thus, a single control valve failure could set off a concatenation of failures that can be catastrophic and costly. While the cost of a catastrophic failure dwarfs the cost of replacing valves and actuators that do not need replacement because their condition is not known, the practice of replacing valves and actuators during a turnaround because they might fail before the next turnaround is common and costly.
Carrying the inventory of replacement valves, actuators, and valve trim in stock without knowing when or how many valves will need to be replaced is expensive, and there is never any guarantee that even with a large stock of inventory replacements, the correct parts or valves will actually be in stock when needed. The cost of periodic inspections is lost time and production loss. Basic function inspection (or partial stroke testing) simply confirms that the valve opens and closes. It does not indicate how the valve is actually performing.
Finally, there are costs attached to having to hire and retain experts and consultants who can inspect a valve and replace a valve if required. This is even more problematic when the worldwide shortage of such experts is considered. Many plants outsource the inspection and repair functions to vendors or system integrators who tend to insist on a particular manufacture of valve and actuator, reducing the plant’s ability to use the best possible devices for the service they need. The bottom line is that if the plant operations and maintenance engineers do not know what the actual condition of the valves and actuators on the plant, the costs of that ‘not knowing’ can be enormous.
Developing the algorithm for Remaining Useful Lifetime (RUL)
Understanding the business problem, our team of data scientists saw a challenge and started to explore a better way of estimating the RUL for individual valves and actuators installed in process plants without shutdowns or turnarounds. These efforts were supported by our domain experts, who have worked for years with customers and partners in multiple projects related to valve performance and diagnostics.
The result of this work is an auto diagnosis algorithm combining expert models with machine learning, capable of predicting the accurate Remaining Useful Lifetime of a wide range of control valves and actuators of different models, ages, and manufacture, using only the available operating data.
Our solution continuously analyses the performance of valve and actuator: control performance, failures, typical issues, movement patterns, and other information. All this information is used to periodically update the RUL. Everything that the valve is doing, and everything that is happening to the valve is taken into consideration to update the RUL.
For the development of the algorithm, we used the experience from our test centre. The test centre features a water loop at industrial scale. It allows us to perform hundreds of test cycles for individual valves. In a typical test, a valve and actuator with known dysfunctions are installed and operated for hundreds or even thousands of cycles. The operating data are collected and used to develop algorithm cable of detecting the failure. We were able to show that algorithm developed at the test centre are suitable for harsh industrial environment of an operating plant.
The test centre allows us to rapidly test a large variety of valves and actuators and simulate dysfunction. The flow loop is equipped with advanced sensors and data recording equipment. Other solutions to the problem rely on the diagnostic information from the individual actuators (smart positioners). Our approach only needs the operating data of the valve: the setpoint and actual position, or alternatively, the controlled variable. This approach provides two major advantages.
First, this approach can be used for all types of different valves and actuators: old, new, digital, analogue, electric, pneumatic, and so forth. This is the reality in all existing plants. Many different models and types from various vendors that have been installed over the past thirty years or more and are in significantly different states of repair.
Second, it does not require a smart actuator or positioner. Smart actuators require communications infrastructure to get the smart diagnostic data from the actuator to the operating software and the maintenance system. This requires extra investment. Many valves and actuators use one type of communications, while others use a different system. In many cases, the smartness of the actuator is only used for calibration and initial startup, not for real time reporting of diagnostic data, because the control system itself was not designed to accept that input in real time.
Our solution requires only the existing data that is already available on the DCS/SCADA level for basic process control. Most companies are recording and storing this data for a minimum of three years or more.
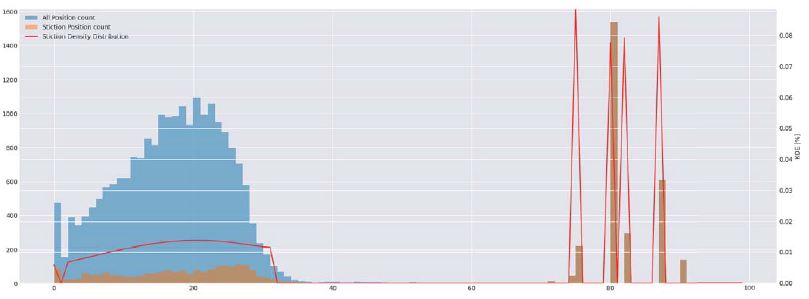
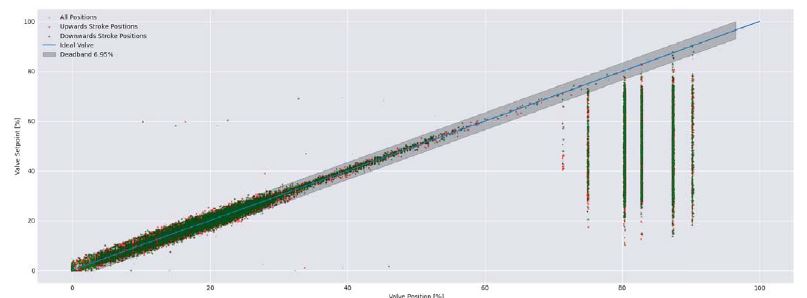
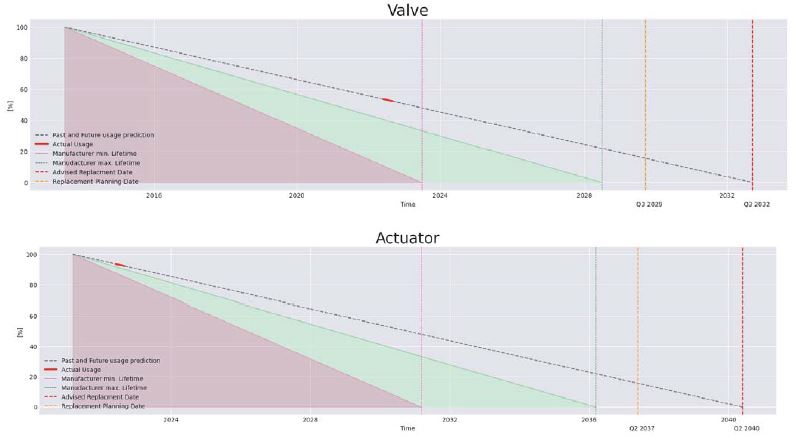
The results of using the algorithm
To validate the algorithm, it was used for over three months to calculate the RUL for 40 valves and actuators in a heat distribution network. The operator of the network uses the OEM’s straight-line estimate of 15 years to plan replacement, stock spare parts, predict investment and maintenance costs. The 40 valves in the system were installed at different times in the last 15 years.
The RUL calculated matched the operator experience that he has normally had to replace the valves anywhere from 2 years to 20 years, which matched very well the actual performance of the valve (failure detected and control performance analysed) and matched the condition of the valve after inspection. The RUL calculated did not agree with the straight-line estimate of performance from the OEM—it was more accurate.
Our conclusions
It is an absolute necessity to be in control of the actual condition of critical assets in a process plant. It is not a nice-to-have gimmick of some Industry 4.0 pilot projects. It is now critical to be in control. There are reasons for it: skyrocketing costs of process failures, supply chain failures, critical shortage of experts, and the need for more automation.
By now, it is well understood that the operating data from production assets like control valves contain critical information about the actual health and condition of those assets. We have shown that it is possible to use the basic operating data of a valve (setpoint and actual position) to evaluate the condition of the valve and the actuator and to use these results to derive the valve’s RUL.
Knowing the RUL of these assets, especially control valves, is very valuable for asset management, reliability engineers, operations, and maintenance teams. It helps the plant operate better. It helps the management to invest smarter. It contributes to increased production and higher profit with lower maintenance expenses. The answer to the question is thus to use the operating data to calculate the RUL.
About the author
Dr Nicolas Spiegl is a chemical engineer who leverages his knowledge of technology and work processes to develop pragmatic digital solutions. He works with partners and clients in the process industry to reduce costs, increase efficiency, and innovate new business models. He can be reached at nspiegl.@ureason.com. For more information, please visit www.ureason.com.