71,000sqm (land space) new-built plant in Vietnam.
Over the past half-century, Kingdom Flow Control (KI) has been keen on improving hardware and upgrading its products and service. The outcome is a continuous outpouring of applications and growth in market share and a powerful brand that has gradually been built for KI.
By Laura Wang, Valve World
Kingdom Flow Control (KI) is a sole investment enterprise established in Taiwan specialising in precision equipment, among others. So far, their products have been sold to more than 50 countries and regions. KI’s total casting capacity is 10,000t/y. Their key equipment includes fifteen high-frequency melting furnaces, 250 CNC Lathes and various types of testing equipment, which enables the company to occupy a leading position in the precision casting business.
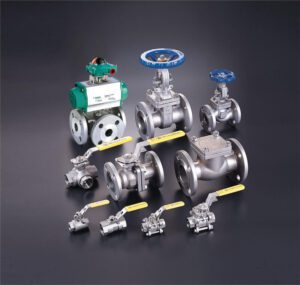
The foundation of the advanced facility is an integrated valve product R&D centre, production line, sales department and service centre. KI excels especially in terms of ball valves with the ‘KI metal-seated ball valve,’ which is widely recognised by the industry and the international market. Currently, the KI ball valve series is particularly utilised in various applications in the chemical industry, including atmospheric, high and low temperature, soft-seated, and wear-resisting applications. More importantly, KI products show great performance in the fields of industrial equipment, new energy (lithium cell, polycrystalline solar panel, etc.), paper, semi-conductors, food, pharmaceutical, power generation, and construction.
For many years, KI has expanded its product spectrum, improving product performance and boosting service capability. With the unified standardisation and integrated information system, KI has further enhanced its quality control, price advantage, mass production and customised service capabilities through standardisation and integrated information by using ERP, MES, HRM, CRM, SCM, BPM, BI and heat number management systems. This enables flexible response to meet diversified needs and provides customers with safe operation of devices around the world.
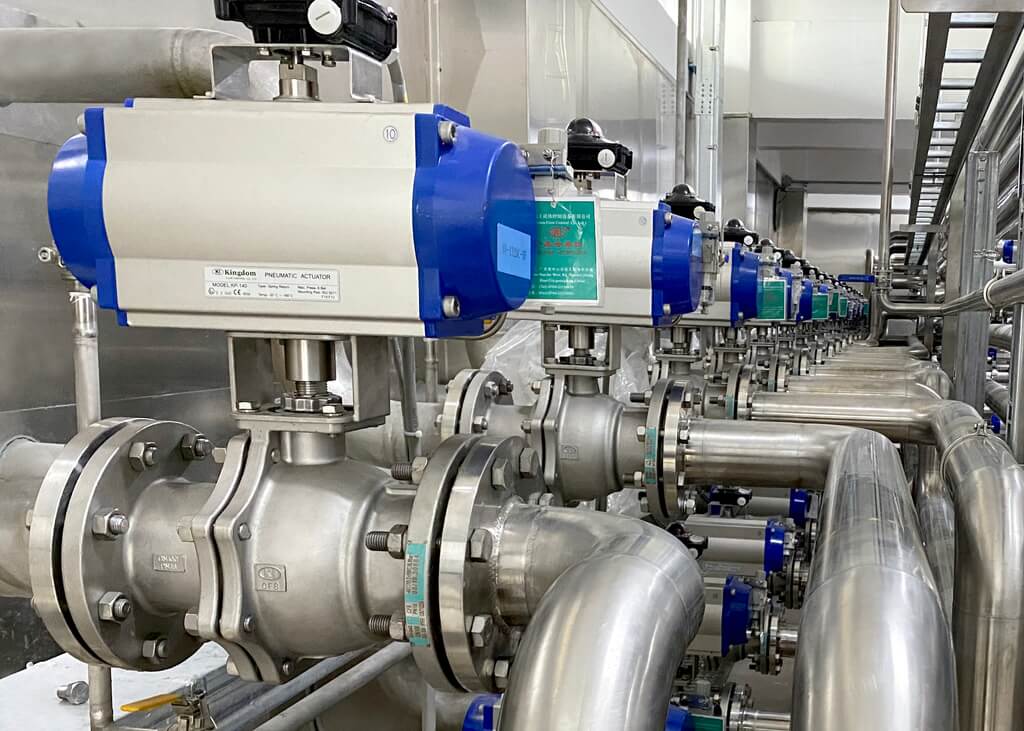
Added value through four plants
It’s been fifty years since the establishment of KI in 1973 in Kaohsiung, Taiwan. The company is currently running four plants, which are located in Guangdong Province, Fujian Province, Jiangsu Province in China, and Binh Duong Province in Vietnam respectively. In its early years, KI focused on mechanical equipment products, thereby accumulating valuable experience in facility construction, operational configuration, and especially in key technology. This constitutes a solid foundation for the establishment and operation of the four plants. Mr Andrew Chen, General Manager reveals: “Each KI plant has a unique purpose and added value. Yet, they share common operating, QC and information systems. Through resource integration, KI aims to provide clients with increased added value in terms of quality, cost and lead time; and to mitigate any potential risks from the supply side.”
Zhongshan Plant (1991) – Valve R&D Centre
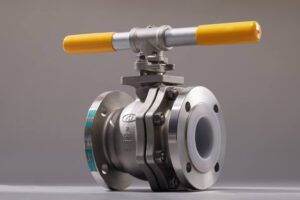
Established in the early 1990s, the Zhongshan Plant is KI’s oldest facility and home to the company’s ball valve R&D centre, as well as being a key production base for its valve products. As the KI brand grew more sophisticated and market recognition increased the original plant became unable to meet customers’ new needs and orders which poured in, nor did it match the company’s R&D requirements and development needs. This is why KI invested in expanding the plant from 40,000m2 to 100,000m2, and increasing capacity by 150%. The added space allowed KI to upgrade its facilities with new automatic equipment and to secure mass production capabilities with elevated reliability. Moreover, it established the Valve Research & Development Centre and the National Testing Centre at the Zhongshan Plant.
Over the years, the Zhongshan Plant has accumulated numerous series of testing equipment. Besides serving KI, the plant is also used to facilitate product testing and enterprise qualification for domestic and overseas fellow manufacturers and clients. Boosted by powerful hardware and rich experience, KI has achieved a series of successes in the field of research & development; especially in terms of high-pressure and large-size products, including, but not limited to, ball valves. According to Mr Chen, the Zhongshan Plant has finished Expansion Phase I and has started mass production. Phase II and III are to be carried out in the future with the aim of upgrading and improving.
Fujian Plant (2001) – focus on production
The establishment of the Fujian Plant is testimony to the emergence of KI products. As its customer base expanded, the rising number of products needed by customers became a challenge for KI’s production capacity. In order to accommodate the increase in demand, a second precision casting plant was built in Fujian, China, in 2001. In early 2010, the management team noticed a decrease in labour cost advantages, and decided that automation, with its outstanding efficiency and performance, would become mainstream. The Fujian Plant was then outfitted with automatic production lines.
Suzhou Plant (2012) – upgrading in automation
With their experience in machinery and vast knowledge of the automation trend, KI built a plant to produce digital control equipment and automation devices in Suzhou, China, in 2012. Besides serving its customers, the plant also serves as a solid foundation for KI. The advanced production plant combines precision processing, assembly, and testing under one roof.
Vietnam Plant (2019) – upgraded casting process
KI always pays close attention to its customer needs. As the industry develops and the international environment changes, KI decided to provide customers with more options for flexible service. In 2019, the Vietnam Plant was established. The 71,000m2 facility was finished and running within one year, with a production capacity of 300t/m, which will later be elevated to 500t/m. The Vietnam Plant is fully equipped with an advanced automatic robot line and shell mould production line. Automated casting and processing have increased product quality and reliability. Automation not only covers the production lines, but plant management and information flow as well. Thus, the production cycle became smarter, and product performance and service capability were further improved. Whereas the Zhongshan Plant is regarded as a valve research & development base, the Vietnam Plant, where resolvable ceramic core technology is developed, can be seen as a research centre for casting techniques. Ceramic core technology can be used to produce specially designed castings, such as impellers.
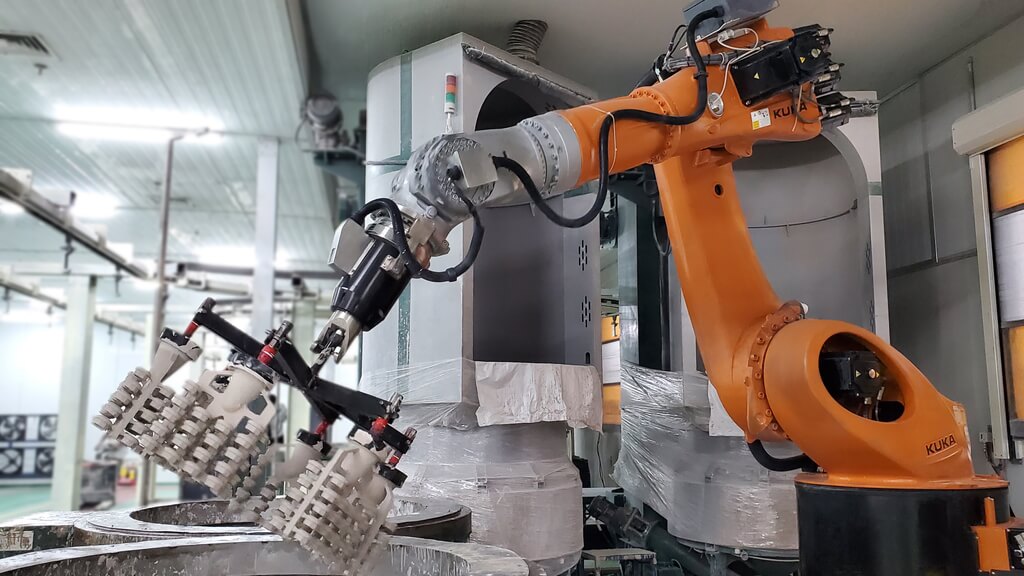
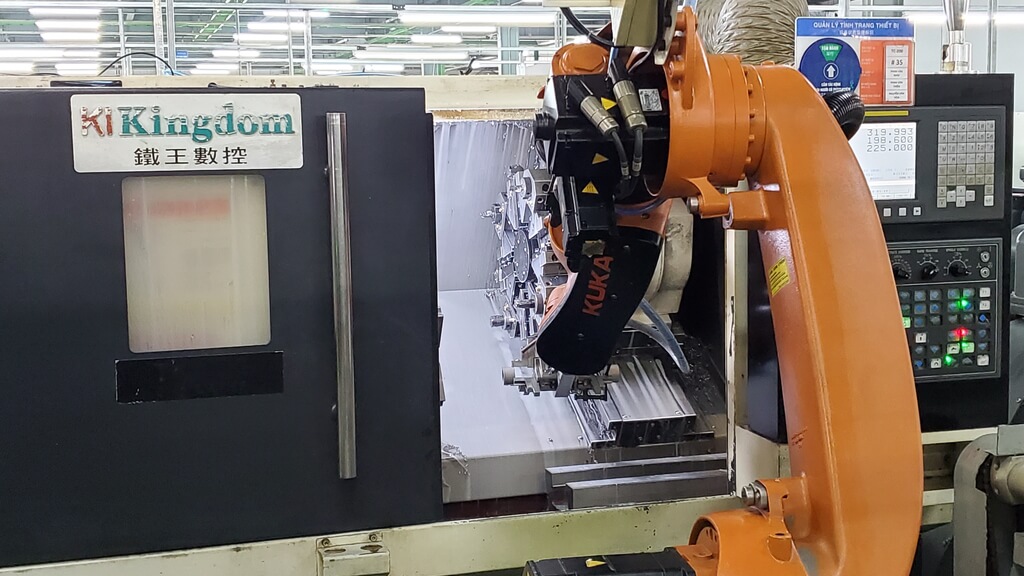
Working around the pandemic
In the following three years, customers were widely impacted by the Covid-19 pandemic. Each of them had the same urgent issues, pertaining to matters
such as cost, technique, material, transportation, and logistics. Despite these circumstances, KI successfully solved its customers’ problems by means of effective coordination between the four KI plants. The Zhongshan Plant acts as the R&D base for the whole company, and as the development centre for the company’s strategy; the Vietnam Plant focuses on developing casting techniques and upgrading research and production capabilities; the Fujian Plant exploits the technical results of the Zhongshan and Vietnam plants with the aim of providing customers with services through smooth and organised mass production with lowered costs; the Suzhou Plant serves as a backup force, which focuses on planning and building automated production lines for internal use. The four plants work under a common standard and strategy in all aspects: production, QC, information flow and testing and inspection criteria. “KI actively pursues standardisation, informatisation and integration. Besides expediting the inquiry-response process,
KI uses these three measures to improve inventory management and raise efficiency. They also help the management team to find out potential risks and promptly work out the best solution. More importantly, informatisation and integration is not simply limited to the plants and headquarters; they are also applicable to our clients. The goal is to make our production ‘visible’ and our service timely by means of mitigating management risk, securing smooth information flow and increased efficiency,” explained Mr Chen.
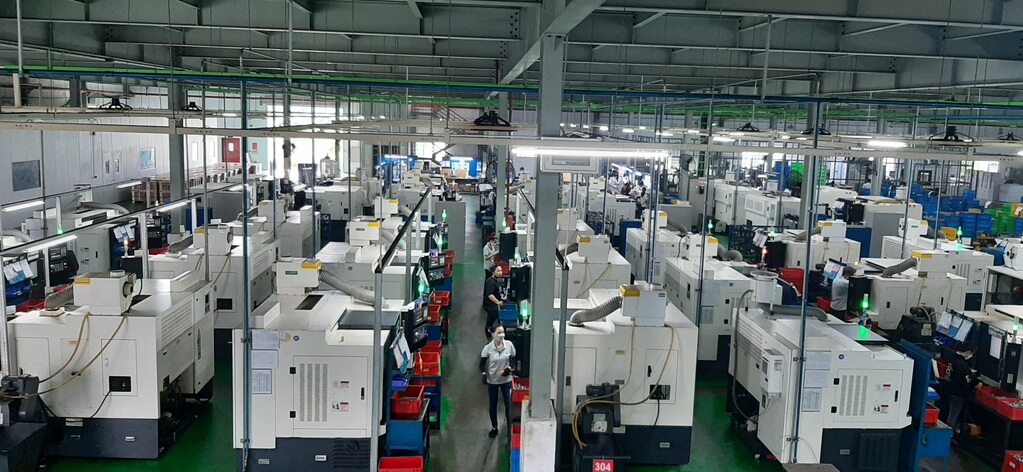
Specialisation and innovation
Innovation is the major driving force behind KI’s development. Although they started with a focus on precision casting and processing, they decided to turn this technique into an advantage and started to produce valve products with added value. Products range from engineered threaded-end ball valves to flange ball valves, gate, globe and control valves, from soft-seated to metal-seated, PFA lined valve, cryogenic ball valve, triple offset butterfly valve,
as well as fire-safe valves and fugitive emission valves.
As each of the industries started upgrading or transforming, KI has foreseen an increasing demand for automation products, and for valve products for the new energy industry as well. Their focus now lies on valve automation and intelligence. Various types of control valves and butterfly valves have been developed and widely applied in petrochemical, chemical, pharmaceutical and polycrystalline silicon, for example. KI’s products are especially increasingly recognised by clients from the polycrystalline silicon and chemical industry. They have established a clean workshop to satisfy the stringent requirements for severe applications. As a forward-thinking company, KI has started investing in the fields of green energy and carbon reduction.
Through its long-term cultivation of the valve industry, KI is becoming increasingly familiar with diversified process conditions and customer needs. As a valve manufacturer, the product is not the only thing that KI provides. Instead, they can work out a complete ‘valve solution’ with their professional knowledge of applications according to specific needs. KI believes that such a solution is not simply a commitment or description. It requires the manufacturer to have a thorough understanding of their customers’ industry and its development trends.
“By continuously upgrading, our advanced facility is able to produce special ball valves to meet customised needs. That’s why several of our products enjoy remarkable market demand. KI is an innovative company that keeps up with the times.”
“Besides effective brand promotion and marketing, the true reason that new orders keep pouring in is customer recognition. In the past half century, KI has grown together with our clients. We keep a close watch on customers’ industrial fields and development trends. We also pay close attention to innovation. It makes us capable of helping customers develop new markets and become more competitive. Many of our customers have established long-term partnerships with us. Some of them have been doing business with us for over 25 years,” Mr Chen added.
Honesty and integrity
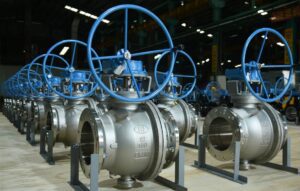
From the very beginning, KI’s products have mainly been sold to the European, American and Japanese markets. For this reason, the company always aims to have updated international standards and thus started planning and investing for this a long time ago. Sound achievement has been made in meeting applicable standards and maintaining relevant certifications.
When asked about KI’s core competence, Mr Chen commented: “As a company, especially a manufacturer, ‘hard power’ such as research and development, and production capability are surely very important. ‘Soft power’ is essential as well. I think KI’s core competence is ‘honesty and integrity’ and it makes our clients and ourselves feel safe. People consider our products and services to be trustworthy and reliable. We have both the initiative and the expertise to safeguard our customers from valve selection to problem shooting. KI is not only a supplier selling products to customers, but also a reliable partner to customers; we can also help our clients explore new markets, which allows us to work with them for the long term. Just like our slogan: ‘All is well with Kingdom.’”
About this Featured Story
This Featured Story is an article from our Valve World Magazine, May 2023 issue. To read other featured stories and many more articles, subscribe to our print magazine. Available in both print and digital formats. DIGITAL MAGAZINE SUBSCRIPTIONS ARE NOW FREE.
“Every week we share a new Featured Story with our Valve World community. Join us and let’s share your Featured Story on Valve World online and in print.”