With their unique compact valves, Combet Valves is ready to take the industry by storm. The young company has surpassed initial expectations, despite only dipping its toes in the vast market. Valve World spoke with Matthieu Smit and Benjie Terrebonne at their facility in Houten, the Netherlands.
By Alexandra Kist, Valve World
Matthieu Smit and Benjie Terrebonne met during an exhibition in the US while working for different companies and decided to team up in 2015. They developed their unique compact valve designs and in 2017, they took their products to the market. Initially, business went well, but then the pandemic hit and business slowed. “But now, we have exploded,” says Matthieu Smit, CEO at Combet Valves.
With an office in the Netherlands and one in the US, the company is effectively establishing its presence in both the European and US markets. The full team currently consists of ten people. The office in the Netherlands serves as the manufacturing headquarters, and the American office is managed by Benjie Terrebonne, Vice President of the US branch, who focuses on business development. The two men meet daily on Skype to ensure everything goes smoothly on both sides of the world.
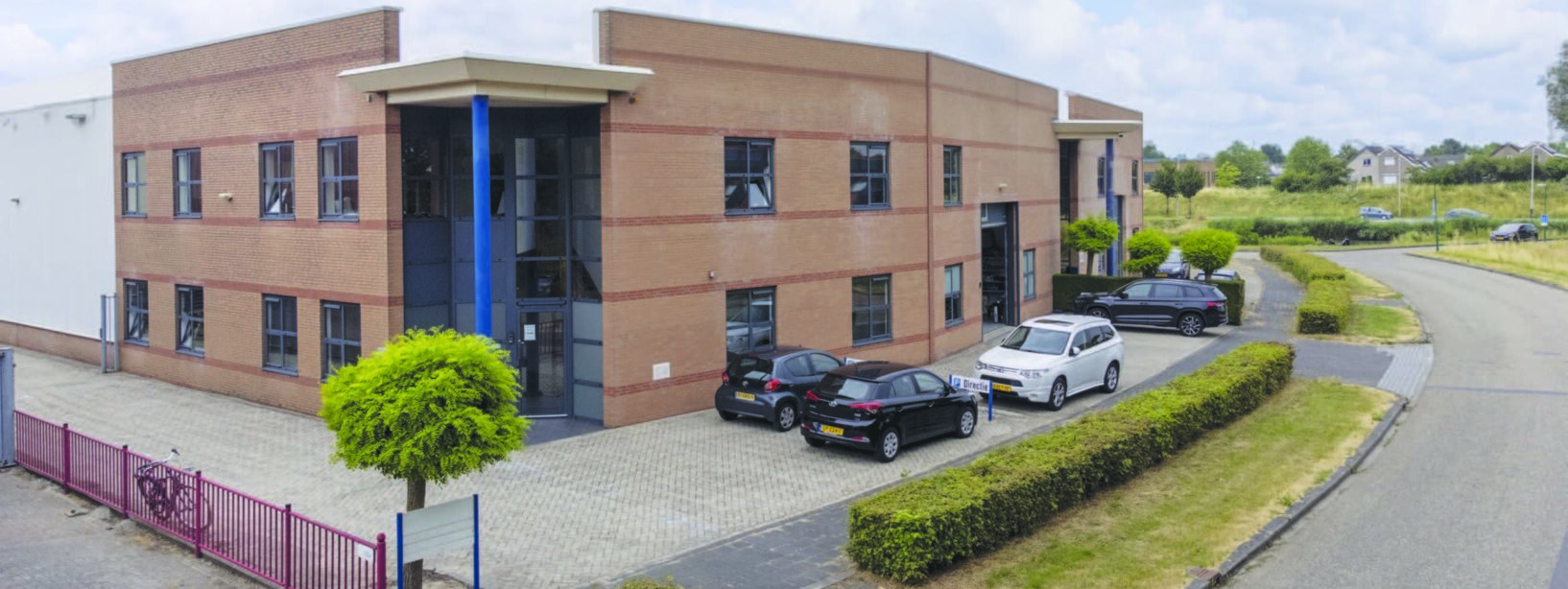
Unique features in a compact design
Compact valves are specifically designed to be small in size and weight while still providing effective control over fluid flow. These valves are typically characterised by their compact and space-saving design, which allows them to be integrated into systems or devices with limited space availability. They offer advantages such as reduced footprint, energy efficiency, fast response times, and reliable performance.
“For our compact valves, we use a modular design,” Benjie says. “They are outfitted with a unique seat carrier design that revolutionises the way floating ball valves are used in high pressure applications. Apart from that, the design code criteria of many popular specifications are incorporated into the compact valve, and the valve is not designed with traditional end-to-end lay lengths. Compared to conventional valves, ours are smaller in size, saving our clients space, weight, and cost.”
The valves have a three-piece design, and of those parts, only the body group is truly proprietary to Combet Valves. Any end connection, such as butt welds, flanges and hammer unions can be fitted onto the valve, depending on the client’s wishes. Weld ends are supplied in the client’s piping material and schedule size, so there is no need for the client to make new welding procedures.
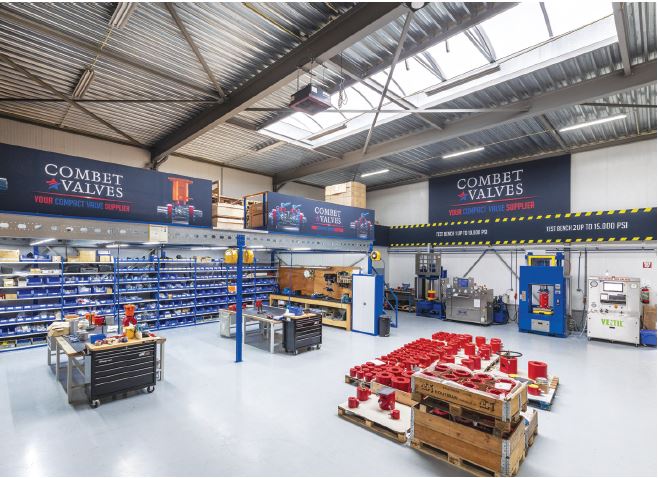
“On top of that, the ends can be welded while unconnected to the valve, so no heat will be transferred into the valve, which could otherwise damage the seats and seals. After welding, the valve can easily be inserted between the end connections of the client’s piping. Just rotate the valve into position, tighten the bolting and you’re done,” Matthieu says.
“With our valves, the clients also face a lower pressure drop, as our ball valves’ ID closely matches the ID of the piping systems clients use,” says Benjie. “We can adjust the valve’s length, materials and end connections. Our compact valves are very flexible. They are small and light, and the torque to open them is similar to that of a traditional trunnion design,” Matthieu explains.
As the dimensional envelope of their compact valves is identical to those of other manufacturers, clients still have the option to switch compact valves after the end connections have been welded to the pipe. Other than that, Benjie adds that they can also meet the dimensional envelope of conventional valves, as they can customise the end connections in such a way that the compact valve takes up the space of a conventional valve envelope. Combet Valves is thus able to serve clients quickly if they need short deliveries for a traditional valve space envelope.
The Combet floating ball valve has a unique seat carrier design that has overcome the challenges of low-pressure positive shut-off and high operating torques where traditional floating ball valves might struggle. The ball moves between the two seats and is bi-directional. When pressure is applied, the ball is pushed into the seat, causing that side to seal. The seat insert and seat carrier work in tandem with the L-seal that only allows pressure to pass in one direction.
In Combet’s design, the seat carrier acts as an internal bypass mechanism that equalises pressure at the moment the valve is opened, which reduces the operating torque. The way their bypass works is that there are small holes in combination with a loose seat, which causes pressure to be equalised when the valve is opened. Usually, floating ball valves have a superior seal, but are harder to open because of frictional forces. Combet Valves’ bypass design circumvents that issue.
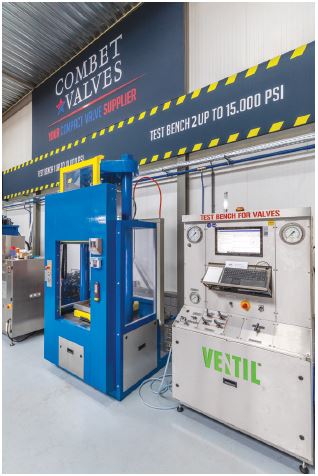
22.500 Psi.
“When looking for a valve solution to deal with high pressure, companies usually select trunnion valves or metal-seated valves. Our floating ball valve can handle those pressures as well. They’re also more cost-efficient. Our valves only consist of seven parts, while trunnion designs usually have fifteen to twenty, making them more expensive,” Matthieu explains.
“The loose seat design makes the valves also easy for field repairs where other designs need to be sent to special valve repair shops or even back to the manufacturer. Our valves can easily be taken out of the pressure line and all internals can be replaced quickly with a simple repair kit, after which the valve can be mounted back in the pressure line to continue operation.”
Another advantage is that this valve has good low-pressure sealing with a much larger seat sealing area, Benjie continues. The seat assembly with the seat carrier is energised like the trunnion valve, but with an elastomeric L- seal. Instead using PTFE, like for traditional floating ball valves, we use an acetal co-polymer or peek with an elastic memory.
The floating compact ball valve seat design will seal in low-pressure applications on the inner diameter of the seat insert, creating a line seal and sealing bubble tight, even in helium gas testing. In a high-pressure differential application, the ball is pushed in the seat. Pushing the ball into the downstream seat will follow the full geometry of the seat insert, creating a very large ball/seat interface.
This large ball/seat cross section is what sets the compact floating ball valve design apart from soft-seated API 6D trunnion ball valves. This design makes it possible to use this valve in unprocessed upstream fluid applications. The compact style floating ball and seat interface is larger than any other seat design, which makes this valve more tolerant of abrasive flow media. This valve is widely used in applications where other ball valves are usually not considered, such as upstream manifolds and fracking service. Even if particles are pushed into the seat, it won’t affect the sealing.
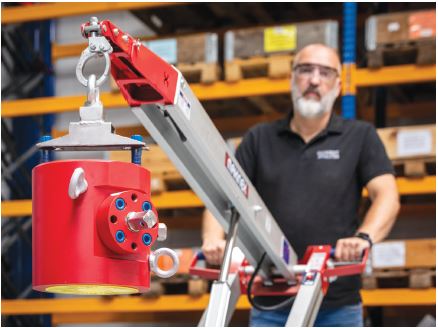
Short delivery times
One of the company’s main selling points is its short delivery times. “What sets us apart is that we’re always available,” Benjie says. “Other designs call for castings, which create long delivery times. Our standard is about four to six weeks, compared to delivery times of up to 24 weeks for conventional valves.”
Matthieu then explains that clients looking to buy conventional valves usually go through a foundry, and the casting will take eight to ten weeks to be delivered. The casting will then have to be machined, the valve assembled, and finally it will be tested. “With our design, we work with stock from locally available suppliers, so we can start machining the parts very quickly.” He also explains the modular design of their compact valves.
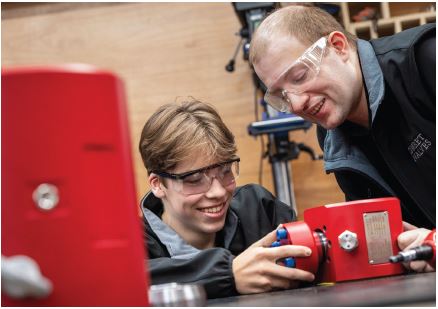
“Our standard compact valves have welded ends and we include flanges with them. This way, the client saves money because there is no need for companion flanges that then need to be welded to the piping. With our products, we already supply the flange and the weld end. The flange is sized according to the client’s wishes to ensure our products can be installed anywhere and everywhere.”
And because Combet Valves always has enough products in stock, the client can replace their traditional valve with a significantly shorter lead time. “We can anticipate longer delivery times because our European facility is closer to the material suppliers than most of our competitors,” Benjie adds. “Any items with long lead times of four to six weeks are kept in stock, so we can control delivery schedules.”
Combet Valves keeps its prices competitive through a solid network of local partner machine shops and by stocking critical materials and parts. “We were able to dodge the volatility in the market when the war broke out because we source our materials from elsewhere,” Matthieu explains.
A worldwide market
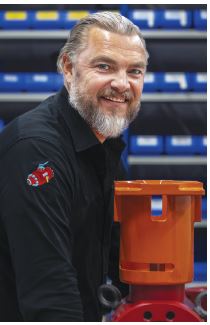
As the only traditional compact valve manufacturer in Europe, Combet Valves’ products find their way to all corners of the world. The company is currently working on jobs for clients in Asia, Australia, Brazil, Mexico, and the US. “About eighty percent of our products are destined for subsea applications,” Matthieu says. “There are also good opportunities for us in the topside and land-based markets.” He adds that they took on a distributor in Houston last year. “At the moment, we are penetrating the US market.”
“In the US, there are several compact valve suppliers,” says Benjie. “What sets us apart is that our products are drop-in replaceable. This means that our end patterns match up to a specific size range, up to six inches. For our FPSO clients, this means that they have a variety of options to source their compact valves. If they were to buy compact valves, they are never limited to one supplier. On top of that, we work with the same end connections as these other suppliers, which means that our valves are interchangeable with any of them.”
Looking towards an even brighter future
Business has been booming for the team, and it seems there is no end in sight. “We’re outgrowing our workshop,” Matthieu says proudly. “Although we haven’t been in this building very long, I’m in discussion with our neighbour about renting half of their workshop. This will allow us to move some of our stock and free up space for more projects.”
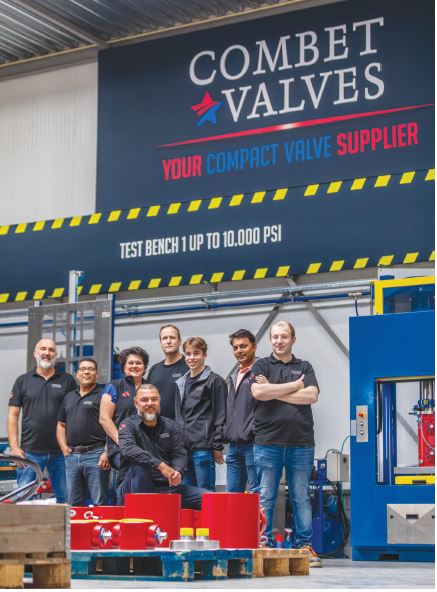
“Our figures are going straight up,” Benjie adds. “Our business has significantly accelerated since the pandemic.” The team plans to stay in the same building for as long as possible to increase their market share but add that they might have to move sooner rather than later.
“Over the last couple of years, we have invested in new test machines and more stock. The war in Ukraine has affected material availability, but we make sure to have everything in stock. This gives us an edge because in the US, our competitors tend to rely on the same resources, while we have access to different resources in Europe,” Matthieu explains.
While the US market is Combet Valves’ biggest competitor, it is also their biggest client. “Most of our material is sourced within Europe, so that’s where we opened up shop,” Benjie chimes in. “We notice material cost increases as soon as they happen, while in the US, they first have to use up six months of stock before they notice the increases as well. By that time, we will already have mitigated that price increase. We believe this puts us a step ahead of the US market.”
“We are young and small in this market and see opportunities to take a larger market share. We want to get the word out about compact valves because they have not yet been adopted on a large scale in Asia and Europe,” Matthieu says.
As the company grows organically, they strive to keep offering the same level of service, both in the office with their quotes and in the workshop with their deliveries. The men look forward to a bright future. “One thing’s for sure,” Benjie adds. “Compact valves haven’t realised their full potential yet.”
About this Featured Story
This Featured Story is an article from our Valve World Magazine, August 2023 issue. To read other featured stories and many more articles, subscribe to our print magazine. Available in both print and digital formats. DIGITAL MAGAZINE SUBSCRIPTIONS ARE NOW FREE.
“Every week we share a new Featured Story with our Valve World community. Join us and let’s share your Featured Story on Valve World online and in print.”