Attemperators have been a key component of combined cycle power plants for many years. Back when the units were base loaded, spray water control was a non-issue.
Text by VMCS
In today’s world, plants are ramping up and down daily, putting a strain on steam temperature control regulation. Attemperators are being cycled more than ever before, introducing unforeseen problems in the Heat Recovery Steam Generator (HRSG) steam system. Service is demanding for this equipment, as hardware can remain at elevated temperatures for extended periods of time, and then be cooled quickly when spray water is required. Located between the primary and secondary superheaters and reheaters, attemperators are the final control element before the HP, IP, and LP turbines. They are responsible for controlling steam temperature in accordance with steam turbine design guidelines. Most plants use an attemperator control logic program for tighter temperatures and to prevent overspray, and subsequent carryover of water into the secondary superheaters. It is critical that proper temperature is maintained during plant start-up and shutdown to prevent thermal damage to superheater and reheater tubes, as well as downstream steam piping.
Key to success
The key to success for precise temperature control at the turbine, is to provide the exact amount of water needed to reach design conditions for optimal efficiency. Even small fluctuations in spray water flow will cause an operator to lower steam temperature set point to the turbine, reducing steam cycle efficiency and electrical output. During low load operation, it is critical for precise control at valve travels 10% or less. Reducing or eliminating spray valve trim erosion, especially in the HRH lines, plays an important role in predictable temperature control.
The problem
Maintaining accurate spray water valve position in a cycling plant can be a challenge. Excessive temperature variability caused by valve instability can ultimately lead to intentional unit trips, or reduced output. Often during start up, shut down or low loads, when trim in a pneumatically operated valve takes a beating, violently slamming closed when cracked open due the compressible nature of air, hysteresis, and excessive dead time. Maintenance frequency can be drastically increased for trim replacement every 6-8 months. If reheat spray valves become damaged to where they cannot control temperature within a specified range, the unit will usually be brought down to 50-60% power where attemperation is not needed, and remain at that level until a rebuild can be performed. Catastrophic tube failure is also a result of leaking valves, adding too much water that carries over into the super-heater and reheater during low loads and ramp scenarios. To get around spray valve inadequacies, operators program the control system to prevent low flow operation, which limits plant flexibility. Sometimes electric actuators with induction A/C Motors can also be found in attemperator applications. These types of actuators are not well suited for continuous duty, as they are limited in starts/stops per hour. In this scenario, the plant must decide to either ‘detune the loop’ for much lower controllability to allow the actuator to survive, or live with the impact of high maintenance requirements due to frequent actuator rebuilds and replacements.
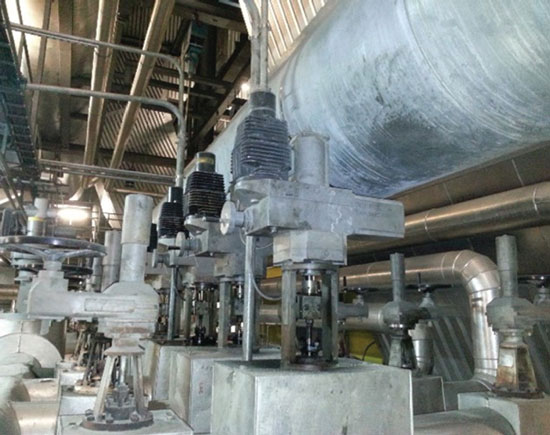
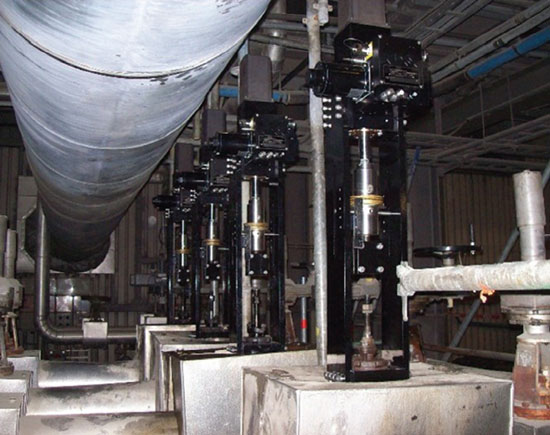
The solution
REXA Electraulic™ Actuation offers a responsive and repeatable control solution for superheat attemperator spray valve applications. Designed for continuous modulating service, the patented self-contained, closed loop, hydraulic circuit provides stiff, stable control in the harshest conditions (-40°C to 121°C). The closed hydraulic system requires no filters, and has no requirement for any oil-based maintenance. A dedicated microprocessor control enclosure operates the drive unit, and is usually located in a convenient area. Set-up and calibration is made simple through a membrane key pad on the enclosure cover. Perfor-mance is unmatched in the industry with adjustable dead-band to 0.05% of stroke, resolution of < 2 seconds) with no hysteresis or overshoot.
The results
The most noticeable improvement that a combined cycle plant operator will immediately see, is precise spray water valve control on the low end of valve travel. This allows the plant to operate at lower loads efficiently, and without the risk of large temperature swings. With high resolution and repeatable positioning, REXA Actuators allow the steam temperature at the HP and LP turbines to be set closer to design than ever before. An increase of 5.5°C equates to approximately a 0.1% increase in turbine efficiency for a standard condensing turbine.
About the company
VMCS specialises in valves and actuators for heavy and/or precision applications. They focus their products on the energy, chemical and petrochemical industry and offshore applications. They also offer various services, such as performing calculations for clients to control valves and actuators, and reparing REXA drives.
About this Featured Story
This Featured Story is an article from our Valve World Magazine November 2022 issue. To read other featured stories and many more articles, subscribe to our print magazine. Available in both print and digital formats. DIGITAL MAGAZINE SUBSCRIPTIONS ARE NOW FREE.
“Every week we share a new Featured Story with our Valve World community. Join us and let’s share your Featured Story on Valve World online and in print.”